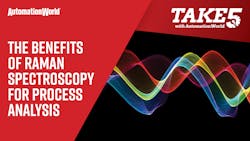
Quick hits:
- Raman spectroscopy is a process that allows the chemical composition of material samples to be determined by exposing them to electromagnetic radiation.
- Raman spectroscopy can measure multiple variables at once with high accuracy, allowing results to be delivered in real-time for continuous, on-the-fly optimization.
- Currently, Raman spectroscopy is largely limited to laboratory use, and has yet to be commonly applied to in-line applications.
Hello and welcome to Take Five with Automation. I’m David Miller, Senior Technical Writer for Automation World. The topic of today’s video is going to be something called Raman Spectroscopy. Now, what is Raman Spectroscopy? Contrary to what you might initially think, it is not related to the popular noodle dish that you may have eaten in college – rather, it takes its name from C.V. Raman who is the physicist that pioneered it. And what it is, more specifically, is a non-invasive technique for determining the chemical composition of material samples by exposing them to electromagnetic radiation.
Now, I am not a physicist, nor a chemist, but I can give our viewers a high-level overview of how this works. In essence, what occurs when Raman spectroscopy is used is that photons – or electromagnetic radiation – basically just light of some sort – is fired at a substance. And depending on the molecular make-up of that substance, and the way its molecules are vibrating, the light that is reflected back will undergo certain minute variations in its wavelength, which a raman spectrometer can detect and analyze. From there, the device can make assessments of all kinds of variables such as temperature, level, flow, or pressure.
Neat toy, right? But the important thing to ask is why is it relevant to industry? Well, in a word, it has several advantages over other methods when used either to monitor process variables for control purposes in in-line process industry applications, or for quality control procedures in process industries such as chemical or pharmaceutical production where an output product needs to be tested and verified for regulatory purposes or something of this nature.
Now, you know, I’m sure you guessed it, but I do want to talk in a little more detail about these aforementioned advantages. But, just first, before we do that, viewers know the drill at this point in time, we’re going to take a quick break to hear a message from PMMI.
Welcome back. So, what are the advantages of using Raman spectroscopy for monitoring process variables and conducting quality control tests in process industry environments?
There are a few.
First of all, when you use conventional field instruments to gather measurements and analysis parameters such as the previously mentioned level, flow, pressure, and temperature, these variables are recorded individually and fed into a regression model, which is basically just a statistical tool for measuring the relationship between multiple variables. And so that allows you to see how these parameters are changing over time in the form of a visual slope or curve.
The issue is that when you do this, you have two drains on you, both of which Raman Spectroscopy can eliminate. The first is that you have to use many different sensors to ascertain each different parameter. The second is that you would have to program a new regression model for each new application you’re looking to measure. So basically it’s very asset intensive, lots of sensors, and time intensive in terms of the need for reconfiguration.
By contrast, with Raman spectroscopy, the promise at least is that you can measure multiple variables simultaneously, and have results delivered in real-time, so that you don’t have run a process, check the data, reconfigure and run again, but instead can engage in an on-the-fly optimization. The idea being that this would help you speed cycle times, increase yields, if there’s a problem with a batch of something, you can figure it out before the batch is finished, and so on.
So, for in-line usage, this is a relatively new technology. Currently, industrial applications for Raman spectroscopy are mostly limited to a laboratory context. And so basically, when set up in a lab instead of integrated directly into a process control system, you have to draw samples and transport them. This means they can change during transport, and then of course, there is the issue of the delay in obtaining a result, meaning that, as I said earlier, you cannot engage in corrective measures while the process is still running. This would lead, obviously to waste.
But again, this is something that is developing – we are beginning to see Raman process analyzers for in-line applications hit the market. So, if you’re interested in reading more about that, feel free to click on the link below.
In any case, that’s about all I have for you today.
Companies in this Article
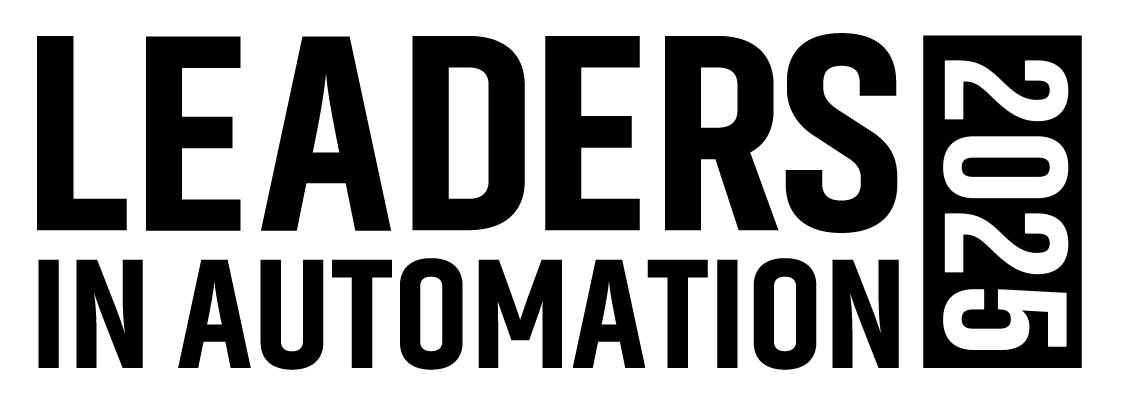
Leaders relevant to this content: