Manufacturers must have real-time access to information from their processes. Such information can assist users throughout the organization in analyzing, troubleshooting, and suggesting enhancements to improve operations. Following are three frequently overlooked integration aspects that, when implemented, will ensure you have access to the information you need:
- Enterprise historians collect time series data from sensors and processes throughout the entire operation, facilitating day-to-day troubleshooting and compliance maintenance in regulated industries. By leveraging artificial intelligence (AI) or machine learning (ML) platforms, this data can yield deeper insights, predict future outcomes and recommend adjustments to enhance future outcomes.
- Equipment manufacturers often offer recipe systems that enable efficient and precise setup of equipment. Granting access to the recipe parameters empowers end users to manage all their equipment recipes through a unified interface, eliminating the need to handle each asset independently.
- Overall equipment effectiveness (OEE) is a widely used metric to identify capacity and quality improvement opportunities. By exposing machine state and production counters, integrating equipment into a plant wide OEE system becomes straightforward.
To enable these integration types, key process and operational data should be exposed through an open industry standard, allowing end users to integrate OEM equipment into an Industrial Internet of Things platform. There are two prevailing communication methods for equipment integration into enterprise communications: OPC UA and MQTT. While there is an industry debate as to the best architecture, it is simple for original equipment manufacturers (OEMs) to offer options for both protocols.
Enabling enterprise integration
None of the integrations suggested above are overwhelming technical feats. Given that, why is it so difficult to complete these integrations once the equipment lands in an end user’s facility? Some of the most common obstacles are:
- Providing an open system may sacrifice the OEM’s intellectual property (IP).
- Perceived high costs associated with developing the interfaces.
- OEMs may not have the staff on hand to architect these interfaces.
- Customers aren’t asking for the integrations upfront.
Embracing these strategies provides tremendous advantages to OEMs by:
- Generating additional revenue by selling the interfaces as add-on features.
- Protecting IP by providing programming interfaces that enable customers to integrate OEM equipment without accessing valuable IP at the code level.
- Boosting market share and competitive advantage by simplifying integration processes and allowing customers to introduce products to the market sooner.
For OEMs looking to deliver an effective equipment integration offering, consider:
- Developing a digital integration strategy and offering open programming interfaces.
- Basing interfaces on standard open communication methods such as OPC UA and MQTT.
- Creating clear and comprehensive documentation to aid customers in the integration process. Well-documented integration procedures help ensure successful execution and minimize the need for expensive support calls.
- Partnering with a system integrator who has expertise in machine-to-enterprise integrations. The costs can often be written off as an R&D reduction and are more cost effective than hiring in-house resources.
Integrating OEM equipment into a facility can be a challenging yet crucial task for optimizing operations in modern manufacturing. Collaboration between end-users and OEMs is vital for successful integration. Starting with developing a digital strategy and finding a partner with the necessary expertise, end-users should insist that OEMs offer open, well-documented interfaces for machine-to-enterprise integrations. OEMs who embrace these challenges will gain market share and increase revenue per transaction.
Peter Larochelle is vice president of sales & marketing at NeoMatrix Inc., an integrator member of the Control System Integrators Association (CSIA). For more information about NeoMatrix, Inc., visit its profile on the Industrial Automation Exchange.
Companies in this Article
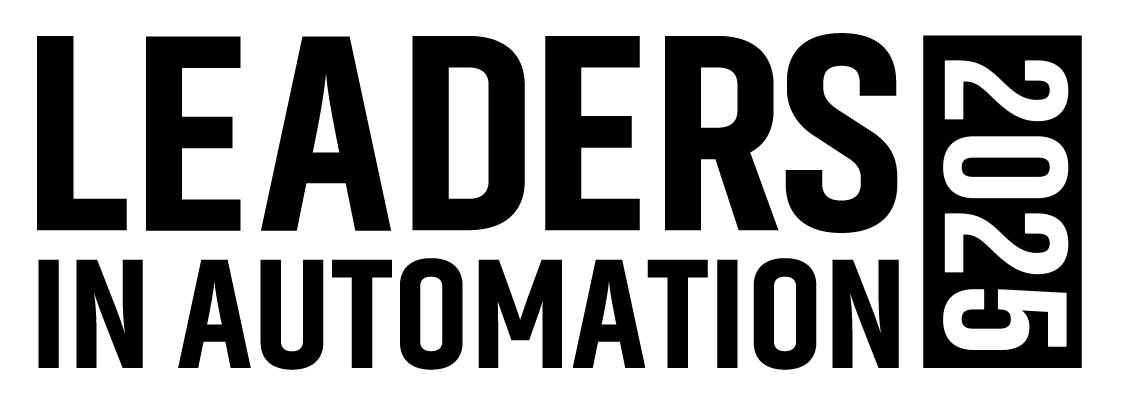
Leaders relevant to this article: