Combining MES and AI for Industrial Sustainability
The demand for greater levels of sustainability and adoption of circular economy principles across industry are not just trends, but clear responses to evolving market demands and societal shifts.
Consumers today are increasingly conscious of their environmental footprint, favoring brands and businesses prioritizing eco-friendly practices. Businesses in the food and beverage sector are realizing that sustainability is no longer optional — it’s a fundamental expectation. Integrating these principles into operations is both a competitive advantage and a responsibility shaped by the collective call for ethical and environmentally sound practices.
For manufacturers, this shift signals a powerful alignment between consumer values, cultural change and business innovation, setting the stage for a more conscious and sustainable economy.
Sustainability through digitalization
Multinational companies are stepping forward as champions of sustainability, redefining corporate priorities to align with environmental stewardship and social responsibility. These organizations are leveraging the immense potential of digitalization to drive meaningful change and achieve their sustainability goals at scale.
More specifically, by integrating manufacturing execution system (MES) and artificial intelligence (AI) technologies, companies create a seamless foundation for more thoughtful, more efficient decision-making.
Here's how that works: MES allows monitoring, controlling and optimizing complex production processes in real time, reducing waste and enhancing resource efficiency. Combined with AI-driven analytics, businesses can unlock powerful insights into operational trends, predict maintenance needs and minimize energy consumption — all while elevating the overall transparency of their supply chains.
This symbiotic relationship between MES and AI elevates efficiency and ensures that these digital tools contribute directly to overarching sustainability objectives. Together, they act as pillars for a future-oriented production vision, where innovation and responsibility intersect to create a lasting, positive environmental impact.
Food and beverage manufacturers who succeed in embedding sustainability and circular economy initiatives into their operations share one commonality — they integrate MES and AI as foundational enablers.
How MES and AI support industrial sustainability
MES software serves as a sustainability engine because it bridges the gaps between shop floor operations and overarching business objectives. MES provides unmatched transparency and control for food and beverage companies aiming to meet sustainability goals by enabling:
- Real-time monitoring of energy consumption: MES software uses data from embedded sensors to provide detailed tracking of energy use correlated with production data. With MES’s identification of inefficiencies, such as spikes during equipment start-up or shutdown, as well as anomalies in energy consumption during the production process, manufacturers can act quickly to improve their energy efficiency.
- Waste minimization: With live data insights, MES can identify production inefficiencies, such as ingredient overuse or processing errors, that contribute to unnecessary waste. For instance, businesses in the food and beverage sector have achieved up to 15% waste reduction with MES analytics.
- Optimized resource usage: MES helps streamline production processes by maintaining detailed digital records, enabling more efficient use of environmental resources and supporting sustainability efforts such as achieving ISO 14001 certifications.
While MES provides the real-time production tracking insights to drive sustainability initiatives, AI works as a predictive force for sustainability. By deploying AI in combination with MES in food and beverage facilities, manufacturers can accelerate the strategic adoption of circular economy practices through:
- AI-driven insights: By analyzing real-time data and identifying patterns, AI technology can forecast equipment issues before they occur. This proactive approach helps minimize unscheduled downtime, reduce maintenance costs and prevent unnecessary waste, ensuring smoother operations and higher efficiency.
- Demand forecasting: AI helps businesses minimize overproduction and waste by accurately predicting future demand. Using advanced algorithms, it analyzes historical sales data, market trends, seasonality and external factors like economic conditions to provide precise forecasts, enabling better inventory and production planning.
- Process optimization: AI can help prioritize sustainable resource allocation, minimizing consumption while maximizing throughput. With data-driven insights into variables like ingredient quality and equipment performance, manufacturers can optimize production processes without sacrificing product quality or efficiency.
Circular economy enablement
The principles of circularity — designing out waste, keeping products in use and regenerating systems — gain momentum when digital technologies enable traceable, transparent and efficient operations. Examples of this include:
- End-to-end traceability: MES systems establish robust traceability capabilities, from tracking raw materials to recycling packaging materials. This ensures resource accountability and facilitates reuse initiatives.
- Closed-loop resource management: Digital platforms streamline the reallocation of waste materials. One production site’s by-products can become critical inputs elsewhere in the value chain, reducing the need for virgin materials.
- AI-powered collaboration platforms: Tools that allow seamless resource sharing between partners can identify innovative ways to repurpose by-products to bolster shared value creation across ecosystems.
The role of system integrators in sustainability
Transforming sustainability objectives into reality requires more than innovative technology tools; it demands expert orchestration, which is where system integrators become indispensable. Following is a list of three key areas in which system integrators can help food and beverage manufacturers apply MES and AI for sustainability initiatives:
- Seamless MES and AI implementation: System integrators possess the expertise to customize MES and AI solutions to the specific needs of food and beverage production environments, ensuring smooth integration across diverse equipment and processes.
- Bridging technical and strategic gaps: Integrators act as a conduit between strategic sustainability goals and the technical roadmap, guiding organizations through aligning business objectives with technical capabilities.
- Ensuring workforce enablement: Effective integration includes training teams to leverage MES and AI systems to their fullest potential, empowering employees to drive operational excellence daily.
Food and beverage manufacturers who succeed in embedding sustainability and circular economy initiatives into their operations share one commonality — they integrate MES and AI as foundational enablers. However, leading this transformation is a collaborative effort. System integrators, technology suppliers and internal teams must unite to redefine sustainability, not as a distinct project but as an intrinsic property of every process.
Luigi De Bernardini is CEO at Autoware a certified member of the Control System Integrators Association (CSIA). For more information about Autoware, visit its profile on the Industrial Automation Exchange.
More insights from Luigi De Bernardini on Automation World:
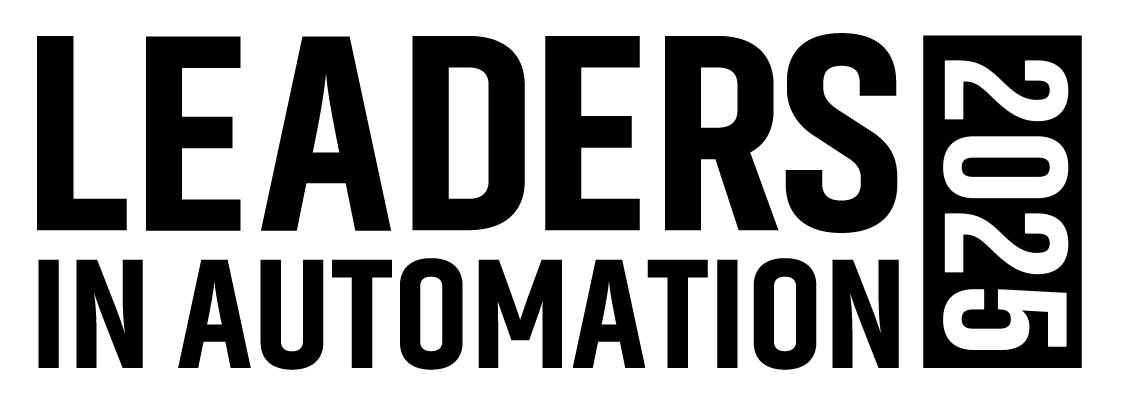
Leaders relevant to this article: