TRANSCRIPT
Welcome to this Industry Update episode of the Automation World Gets Your Questions
Answered podcast. I’m David Greenfield, editor in chief at Automation World. These
Industry Updates are a new addition to this podcast series as a way to help keep our
listeners updated on the latest goings on in the automation industry.
For this Industry Update, we’re focusing on industrial data ops – what it is and what you
need to know about it.
So, while the phrase about data being the new oil has definitely been a bit worn out by now,
it still remains true. After all, everything about Industry 4.0, digital transformation, the
Industrial Internet of Things, digital twins and artificial intelligence—they all come down to
data aggregation, contextualization, transmission and visualization. While this sounds
simple enough since all the devices and equipment on the factory floor generate tons of
data, the catch lies in making sense out of all this disparate data and compiling it in a way
that it can be used for a company’s benefit.
That’s why you’re hearing more and more about data ops and industrial data ops more
specifically.
Daniel Malyszko of system integrator Malisko Engineering explains that industrial data ops
is about bringing together system architectures, data access methods and cultural
approaches as well in the way industries manage and use their data. He says it's about
creating synergies by adding context and governance to data, and ensuring that various
data sources across the enterprise merge fluidly to drive optimized results with shortened
data analytics cycles.
Now, of course, to deliver on this grand concept, industrial data ops require a common data
platform that allows for data modeling, contextualization and data consumption across
multiple applications, and to be able to do this at scale.
According to Daniel, industry’s realm of focus has historically consisted of integrating PLCs
and HMIs to deliver immediate access to process data for analysis by site maintenance,
engineering, production, quality and continuous improvement personnel. But as industries
are becoming more digitally interconnected, simply storing and trending historical data
isn't enough.
As others in the company want access to this data for their own decision making purposes,
we face more intricate questions, such as:
* Where and how is the data directed post-historization?
* Who is leveraging this data and for what purpose?
* What other data sources can add valuable context to the existing data?
* How do various applications use the data?
* How is the data secured and governed?
Analysts at the enterprise level are increasingly advocating for a cloud-first approach to
data management because of its scalability, flexibility and its compatibility with an array of
big data toolsets. For many corporate users of plant floor data, it's not just about
understanding what happened in the past, Daniel says, it’s also about predicting future
trends to optimize supply chains and derive strategic business insights.
To provide an example of how this is playing out in industry today, Daniel referenced a
recent project Malisko Engineering was involved in that would seamlessly bring together
data from production, quality analysis, research and development, and engineering. On
paper, he says this project seemed pretty straightforward, but it involved straddling
multiple data worlds, each with their own intricacies.
In this project, Daniel said they noticed that production used a cloud-based MES system,
they combined spreadsheets from quality and R&D, and they used a homegrown laboratory
information management system and historian data. Meanwhile, the engineering
department used historian data with HMI trending tools, but they also wanted to overlay
lab data, specifically manual data entries from the laboratory information system.
To harmonize these disparate data sources, Malisko Engineering crafted a common data
model independent of the data’s origins. Daniel said one of the most valuable aspects to this
deployment was introducing event data, such as production stages, steps and alarms and
adding context to time-series data. By doing this, each department can maintain their own
distinct tools, but the enterprise benefits from a unified and contextualized data landscape
for more efficient analysis and decision making.
Looking back on this project and at how industrial data ops is transforming industry,
Daniel said it's no longer just about the controls engineering department’s choreography of
data but orchestrating what he calls a grand symphony of data across the company.
Looking at this from a higher level point of view to understand how industrial data ops is
being applied across industry, John Harrington of HighByte, a supplier of industrial data
ops software, says that standardizing device-level data into structures is key to industrial
data ops, but it’s really only just the beginning. And he highlights four key reasons why
manufacturers need an industrial data ops system as part of their information architecture.
His four reasons are these:
Number 1, You’re dealing with machine and vendor variability. John says that because
standards bodies are made up of vendors and users, as the standard is being defined,
variances are allowed for vendor systems with unique capabilities and limitations as well
as for specific use cases. While the intent of this is flexibility, of course, the result is often
ambiguity because it’s typical for vendors to implement the same standard slightly
differently. Also, vendors tend to refine their systems and change data models over time to
suit their needs. This means that even minor variations in datasets require human
interaction to link these machines to other systems in the network to automate dashboards
or analytics. Industrial data ops technology helps users connect to a range of sources
without having to write or maintain code. That allows for non-standardized input to then
be modeled and transformed to the governed data standard for any use case.
Number 2, without industrial data ops, John says you’re viewing individual data without
any relationship context. When analyzing operational metrics, bottlenecks or quality root
causes for a production line, specific information from each machine, test stand and sensor
should ideally be assembled into a single payload for that line. Industrial data ops makes
this possible he says by merging and modeling data from multiple machines and then
correlating those data by logical use case.
Number 3, John says you’re looking at more than just device data. You can’t make strategic
decisions if you’re not linking your machine data to other systems across your
organization. This includes enterprise applications, such as your ERP system, and your
manufacturing databases, such as SCADA, MES, Historians, and maintenance management
systems. Industrial data ops should be able to connect to virtually any system in your
organization and combine information from these systems with machine data to bridge the
gap between operations technology and the rest of the business.
And number 4 involves not getting the data you need when you need it. As well all know by
now, information overload is a real problem in the Industry 4.0 world. So, understanding
what’s needed—and when its needed—is critical. Sometimes data is needed at a cyclic rate,
say, once per second. Other times, you may need an event-based feed to identify cell
production completion, defects or machine performance issues. John says industrial data
ops technology can define the desired data payload and its event or frequency to create a
more efficient decision-making process and minimize your cloud costs because, in this way,
you’re only storing and processing the data you need.
If you’re interested in learning more about industrial data ops and the data hub and spoke
model, be sure to visit this podcast on the Automation World site. There, just above the
transcript, I’ve included links to several recent articles on these topics.
So thanks for checking out this Industry Update episode of the Automation World Gets Your
Questions Answered podcast series. And remember to keep watching this space to stay on
top of the latest news, trends and insights on the world of industrial automation.
Latest In Analytics
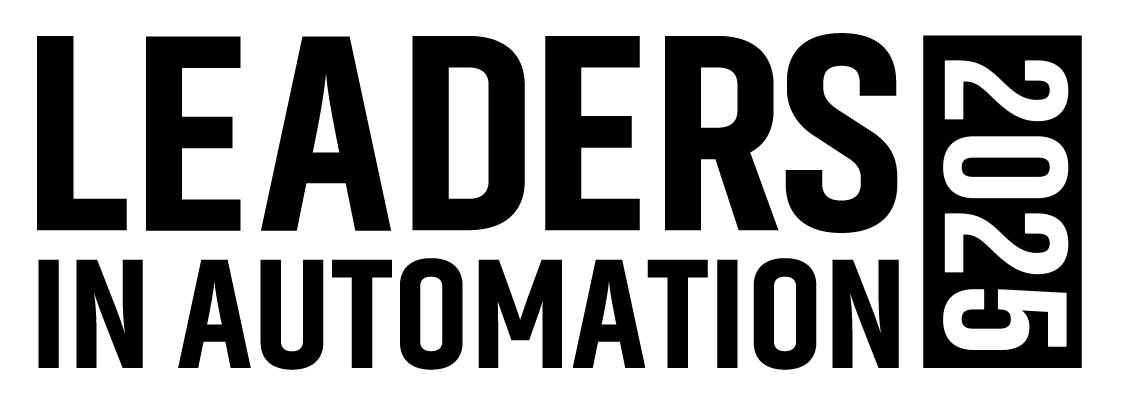
Leaders relevant to this content: