Though some argue that robots are putting Americans out of work, the flipside of that argument is that manufacturing wouldn’t be here at all without the robots. According to Jim Lawton, fleets of robots working alongside people will reduce costs, allow manufacturers to respond more quickly to customers, and “iterate design more rapidly”—all of which will enable “lower costs and being able to operate in parts of the world that [manufacturers] might not otherwise be able to operate in because tariffs are too high and local labor is too high.”
It might not come as a surprise that the chief product and marketing officer of Rethink Robotics is bullish on robots, but he has support for his optimism. A Boston Consulting Group survey released in December showed that 31 percent of executives at companies with annual revenues of $1 billion and above planned to increase U.S.-based manufacturing over the next five years for goods to be sold in the U.S. Only 20 percent said they planned to ramp up production in China for such products. And automation, the survey found, is a key driver of the shift back to the U.S. from China. Fully 75 percent of respondents said their companies planned to increase investments in automation or advanced manufacturing technologies over the coming five years.
“Automation will always beat labor if it can be designed to replicate and deliver good quality product,” says John Gattorna, author of “Dynamic Supply Chains” and an Australia-based logistics consultant. Along with the promise of lower manufacturing costs enabled by automation, an increasing need to innovate quickly is also driving manufacturing closer to the place of consumption, he says. “This is what I call the agile supply chain, and it has to be fast, therefore reshoring is vital.”
Gary LaPoint, professor of supply chain practice at Syracuse University’s Whitman School of Management, agrees. “Some products are becoming obsolete almost as fast as they come to market,” he notes. “This means the time period to recoup R&D, design and setup costs is greatly diminishing.” That means the quicker a company can get from concept to product, the better the bottom line, he explains. Automation, advanced manufacturing and reshoring point the way.
Key technologies
There are four major technologies making it all possible, according to Bobby Bono, U.S. industrial manufacturing leader at PwC: the Internet of Things (IoT), robotics, augmented reality (AR) and 3D printing.
The value created by the IoT could constitute 11 percent of the total global economy by 2025, according to McKinsey & Company. McKinsey expects a third of that value to come from IoT’s use in manufacturing.
As just one example of the increased efficiencies that are already being realized through IoT, a PwC report co-authored by Bono titled “2016 Industrial Manufacturing Trends” cites a Black & Decker factory in Mexico that was able to use the IoT to boost equipment effectiveness by 24 percent, labor efficiency by 10 percent, and production by 10 percent.
With regard to robotics in manufacturing, the West and China are taking two different paths, according to the PwC report. Chinese firms aim to replace workers wholesale in manufacturing, even going so far as to launch the world’s first fully automated factory, a Changying Precision Technology plant in Dongguan that produces mobile phone components.
In the U.S., however, the trend is more toward collaborative robotics, with the understanding that robots can enhance human abilities but can’t entirely replace them. In other words, the thinking goes, humans and robots do their best work together, so there will always be a place for people in factories.
Rethink Robotics is among the robot makers embracing this philosophy. The company’s Baxter and Sawyer robots communicate with workers around them through animated images of eyes and by moving their heads. “Those things, along with the facial expressions, they play a real role,” Lawton explains. “They're not there to make the robot look cute. They're there to help people get comfortable and confident in the way in which the robot's going to operate.” Putting people at ease is just as important to the design of Rethink’s robots as their ability to assemble parts and perform other tasks in a factory.
On the AR front, Ford Motor Co. is among the manufacturers increasingly deploying wearable displays to workers that overlay information on top of the workers’ real-world view to help them manage production and boost productivity. Describing such AR applications in its report, PwC says, “Users simply follow the text, graphics, audio and other virtual enhancements superimposed onto goggles or real assemblies as they perform complex tasks on the factory floor. These tools can simultaneously assess the accuracy and timing of these tasks, and notify the operator of quality risks.”
Adoption of AR is accelerating, and investors are betting big on the technology. In February, Florida-based AR startup Magic Leap announced that it had raised $793.5 million in series C financing, bringing the total invested in the company to $4.5 billion.
The computer-controlled layering of materials to build up parts made of plastics, metals and other materials in the process known as 3D printing, or additive manufacturing, is already in wide use as a prototyping tool. But it is gaining traction in production environments as well. The PwC report cites BAE Systems as an example of a major manufacturer that put 3D printing to work reducing costs. The company cut the cost to manufacture an aircraft part by more than 60 percent, eliminated tooling costs, and shortened the lead time for producing the part by two months with 3D printing.
The jobs question
Advanced technologies are not only spurring companies to bring manufacturing back to the U.S.; they are also changing the face of manufacturing, starting with the workers. “The industry is seeing a shift to a more tech-savvy worker, who possesses capabilities in coding and software development,” Bono says. In other words, new skills will be required for new and retooled manufacturing plants.
“Today’s and tomorrow’s factory workers need computer skills to operate and program the machines. They will need skills in how to repair these machines,” LaPoint says. “I see more support jobs coming.” He also anticipates a rising demand for design and 3D printing services to meet the need for more 3D-printed parts.
The necessary new skillsets will extend to management as well as workers, says Maxime St-Denis at CAI Global, a corporate investment consulting firm. “Managing a robot vs. a human being are two completely different tasks.”
All of this means that while reshoring will indeed bring manufacturing jobs back to the U.S., they won’t be the same jobs that were here before. “Reshoring will create more jobs in the U.S., but not at a one-to-one ratio, as compared to offshore locations prior to the reshoring,” Bono says.
Gattorna is a little more direct in his assessment. “Ultimately,” he says, “there will be fewer jobs required.” After all, automation is, by definition, the outsourcing of tasks formerly done by people to machines.
Even so, experts say that one of the biggest challenges to successful reshoring is actually a shortage of workers with the right skills. “I think one of the biggest threats to reshoring is talent acquisition,” LaPoint says. “We do not have an adequate supply of the right trained people.”
A report from The Manufacturing Institute and Deloitte called “The Skills Gap in U.S. Manufacturing 2015 and Beyond” backs him up. It predicts that there will be 3.4 million manufacturing jobs in the U.S. by 2025—and only 1.4 million skilled workers to fill them.
It’s going to be up to a new generation of workers to fill those jobs. “With the traditional manufacturing model coming to an end and the rise of the technological era, this will result in the retirement of the aging working population in conjunction with the rise of the younger generation entering the workforce, thus replenishing and modernizing the ever-evolving industry,” St-Denis says.
Even collaborative robotics booster Lawton acknowledges the impact on employment that automation has brought and will continue to bring. “There is always going to be some element of what I call ‘the jobs question,’” he says, noting that managing the reactions of workers to increased automation is an important factor in deploying it effectively.
“Automation is designed to eliminate my job, right? So why would I be interested in deploying this stuff?” That’s a typical reaction, Lawton says, adding, “How the organization has thought that through will have a big impact on how much this kind of technology is either embraced by the organization or how much reluctance there is to consider things like this.”
Looking toward the future
Despite the inevitable impact of automation on the workforce, Lawton is confident that, in the coming era of advanced manufacturing, workers and robots will peacefully coexist. “Every factory worker, the first thing they’re going to get is a robot; and the robot is going to be an extension of them,” he says. “It’s going to be a tool they can use to help them do their job better, and they will control the robot and what it does.” That control, he says, is key to fostering the acceptance of robots by workers in the shared workspace.
The result of these and other technological developments will be the factory of the near future “almost living and breathing...just growing and getting better over time through its own operation,” Lawton says.
The goal is production that moves in harmony with demand, Gattorna says, “so that as one product is purchased, a replacement is immediately produced.”
But the future is still being defined, Lawton says. “As much as you and I and other people will speculate on what that future’s going to look like, it’s so open-ended in terms of the range of possibilities. There’s a certain amount of wonder associated with that that frankly hasn’t really been part of automation as much over the last 20 years or so. I think it’s going to be very exciting from that point of view.”
Companies in this Article
Continued Reading
Sponsored Recommendations
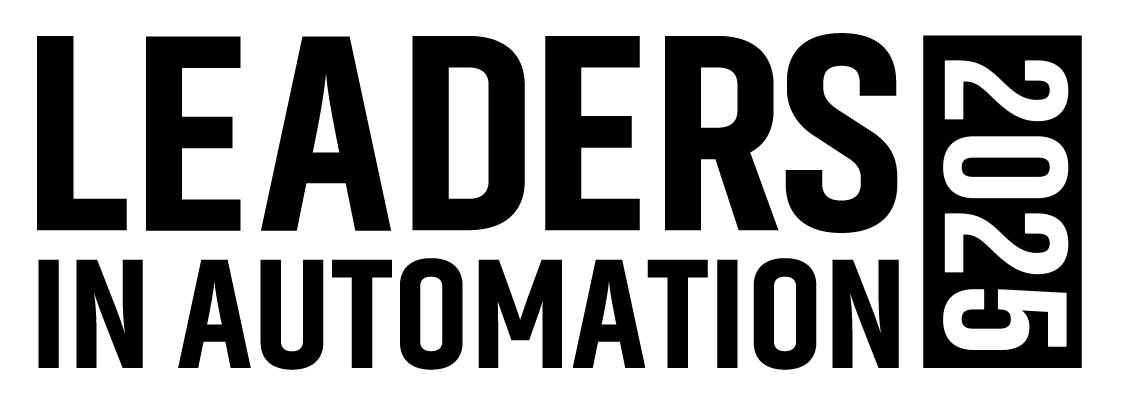
Leaders relevant to this article: