This is the first transcript of a three-part series on Automation Trends in Food Processing and Packaging. If you would prefer to watch the video of these discussions, choose a link below:
· Robotics video (20 minutes)
· Remote Access video (20 minutes)
· vFAT (Virtual Factory Acceptance Test) video (13 minutes)
PACK EXPO Connects Highlights
David Greenfield:
Hello, and thanks for joining us for this discussion about the use of robotics, remote access, and virtual factory acceptance testing in the food and beverage, and consumer package goods industries, and how those trends affect OEMs supplying these industry segments. I'm David Greenfield, Director of Content at Automation World, a part of the PMMI Media Group. And joining me today are Glen Long, Senior Vice President of PMMI, Tom Egan, Vice President of Industry Services at PMMI, and Bryan Griffen, Director of Industry Services at PMMI.
Let's start this discussion by focusing on robotics. New robot advances were all over the place at the Virtual PACK EXPO Connects event, which launched back in November, and runs through March of 2021. Some of the more interesting robot introductions that I saw at Pack Expo Connects were Omron’s HD-1500 autonomous intelligent mobile robot that handles payloads up to 1,500 kilograms, uses lasers to provide 360 degrees of safety. It's also got an onboard sensor for more precise pickup and drop off of materials. What I find interesting about these automation mobile robots is how quickly they're being adopted by industry.
When I visited plants each year, before COVID of course, I would typically only see these kinds of robots in the largest of plants. But by 2018 or 2019, I was seeing them more and more, regardless of plant size. I can't help but think that with COVID and its social distancing requirements, that these kinds of robots are becoming even more widely adopted now.
Omron also debuted its new FH-3D vision sensor with its 3M collaborative robot, which enables the robot to pick up objects in random, overlapping positions, out of a bin. This is something that's historically been really difficult to automate because of the varying weights, shapes, and orientations of objects that require 3D location as well as different forces for the robot to pick up the objects.
Epson Robots introduced its new C12XL 6-Axis robot that has a 12-kilogram payload, a 1,400-millimeter reach, and it can be used as a standalone robot as part of a line in end-of-line applications, such as packaging, kitting, material handling, or palletizing. Now, there's a lot of six-axis robots out there for these kinds of applications.
What I found interesting about the C12XL is its use of quartz micro electromechanical technology referred to as QMEMs. And robots with arms of this length and payload capacities tend to have a good bit of mass added to their base to dampen the vibrations, firm the robot arm to make the robot more stable, and better control the movement of the robot arm. Epson's QMEMS, however, eliminates the need for all this mass at the base to reduce vibration, and deliver a smoother end-of-arm motion, which also makes for a lighter robot overall. This robot weighs less than 140 pounds. So, it can pretty easily be moved around the plant floor as needed. These are just a few robot highlights from Pack Expo Connects.
Tom, I know you've been tracking how the use of robotics has been advancing in the food and beverage industry in particular, both as part of your job as VP of industry services, and through specific PMMI research. So, what's your take on the state of robotics for OEMs in the processing industries they serve?
Gripper Technologies & Object RecognitionTom Egan:
Thanks, Dave, for the introduction and opportunity. I'm going to actually start with a presentation that was done at the PMMI Executive Leadership Conference in 2018. Ken Goldberg, a professor at UC Berkeley gave a really good presentation about what some of the needs were in order to improve robots for doing things like bin picking, which is what you mentioned. And one of his ideas in addition to vision was the idea that some of the modeling of parts in a bin could actually be taken from known images in the Cloud. Now, that's an interesting idea. His approach was to train a robot, instead of doing the training and having to store all of that information in the robot, the robot could begin to take images when it first got an image acquisition from the bin, and say, "What does this look like," because then it helps with making a quicker determination on the best way to pick it up, where it's stable, how it is you're going to be able to take it out of the bin.
So, this goes all the way back to three years ago. I thought it was a great point as you were mentioning about some of what you saw at Pack Expo Connects. But you also mentioned about our business intelligence reports, and PMMI does a number of them throughout the year. I'm going to refer to a couple of them. One was the Robotics Report from April of 2019. We had a Trends and Advances in Food Packaging and Processing in November of 2019, and an Automation Timeline in July 2020. Now, I'm bringing up those three because they are three of probably six, seven, eight different reports that we had. Each of those showing what was happening in robotics including in food and beverage. And I'm happy to say that there is progress. There is a sense from that April 2019 report going all the way up through the Automation Timeline in July 2020, that we're making progress in the implementation of robots, especially in food and beverage. Packaging World had a great study in their Robotics Playbook that talked about filling croissants.
They talked about the case study where there were multiple robots that were added to a production line in order to pick a croissant - a flaky, warm, croissant, that then also had to be filled, whether it be with a jelly, or with chocolate, a cheese, something else. The net result was that the project was successful indicating that progress that I'm mentioning. In addition to that, it used multiple robots, and it used vision, and they ended up using it with some fixed automation too - traditional, more fixed automation, to achieve an output of 160 a minute. One other point that I would like to make is that large CPGs, not necessarily surprising, are ahead of small and medium enterprises in the use and integration of robots to their production operation. But it is not such a delta difference that you say it's all large CPGs, and only one or two small ones. There are islands of automation even in small and medium consumer package goods groups because they want to get the benefits of that. There was also a note that the output in the secondary packaging area is ahead of primary packaging, and both types of packaging use robots more often than processing.
David Greenfield:
That's interesting. A couple of things you mentioned there from the gripper technologies working with soft food items has been amazing, the advances being made there, and even the objects in the Cloud, being able to train on that. That goes in line with a lot of artificial intelligence advances we're seeing about how easy it's becoming to train these various automated systems of all types, which used to take days, weeks, and months to really program these things right. Now you can show them a handful of images, and it learns on its own. It's been really amazing.
Before we move on, Glen, or Bryan, anything to add to some of the comments that Tom's had here?
Glen Long:
I think one of the things that is evident when we look at robot technology itself, and it got to a certain point, and certainly it's evolving, but the basic robot technology's been around for some years. I think the real advances right now are coming in object recognition. It's based in that vision area that Tom mentioned. And the other one that has seen tremendous advances is in the gripper technology. Dave, you mentioned that, and clearly there's some fabulous things going on with 3D printing, and the ability to form very, very complex manipulators at the end of the robot arm. And that's allowing them to be deployed into areas that before they weren't able to be deployed into. And it's the same everywhere else. As that technology becomes more affordable, you're seeing more and more manufacturers put them into places where the cost, the payback, may not have been there before. So, you couple that with the accelerant that we've had with COVID, and the social distancing, and the availability of labor is another real driver. So, now you're seeing all of those things converge to push that technology to the fore. But I really think that that vision recognition, and the gripper technology is what's making this possible, specifically in the food industry.
Driving a new revolution of changeBryan Griffen:
I think we're pushing beyond robots just becoming more usable, and more utilized within the industry. We're really seeing they're driving a new revolution of change within the industry. It's no longer the robot is a last thought that you come to. Now it's the first thing that you come to. Can we use a robot here? Is there something we can do, whether it's a fixed robot, or a cobot? And I think that comes down to three things that are pointed out in the report that Tom referred to. One is the fact that robots are becoming much more adaptive and versatile than they ever were before. To Glen's point, the picking up of fruits, and vegetables, and things with grippers that can pick up soft items that they couldn't do before, the different types of grippers that are available now. All these things make them so much more versatile, and more easily adaptable to what the specific needs are for production at that time. And it can change throughout the day as you go from product to product. You don't need to change out the entire robot.
You can change out the end effectors, and a little bit of programming, and now you've got something that can work with a different product. The second pillar is the fact that they're becoming much smaller, more compact, and therefore more affordable. Robots, when we first thought about them, were these big heavy duty things that did painting, or welding, or that type of work within the automotive industry. And now they're very small, lightweight, weighing even less that 200 pounds that you can pick up, and move around to different places on the line. And then the last piece would be the fact that they are becoming much easier to program, to train, to teach, and then to integrate into existing systems, or other pieces of the line. It no longer requires that you call the manufacturer to come in and make changes. You can make those changes very easily in the factory with factory personnel. So, I think those things have really caused robots to really drive now where automation, and where factory manufacturing is going versus being a last thought of what else can we do.
ObstaclesTom Egan:
Dave, I think we'd be wrong to say it's all good because we're pointing out some really great advances here, right? And you are seeing more implementation. The report that I reference did talk consistently about the need for a cost justification, and that's the number one obstacle to doing more implementation. There is the thought that, "Boy, this is an expensive undertaking. We need to get it right." So, one idea is to start small, to get a win, so that you can work with the production teams at the factory, and say, "Here's something that this program, or this robot can do. Here's the way that we're going to implement it. Let's see how it goes but starting small." That cost justification is the number one obstacle. I took away one more, which I don't know that everybody thinks about so much, and its the rush to say we're making advances. “We've got to install one. Let's put one in.” I think it's still very important to point out a timeline. That there needs to be a good timeline that's in place even to set a baseline within a production floor.
I remember during an automation conference that we had a couple years ago, that there was a food manufacturer that gave a really outstanding presentation. And when he was talking to his corporate management he said, "Well, I think we're ready to go." And they're like, "Okay, when can we have two or three of them in in the next two or three months?" He said, "Whoa, whoa, whoa. In the next two or three months, I have to visit the factory to understand where the baseline is for the technology. Forget the robot. What's their technology in terms of a workforce skillset? What's their technology in terms of bringing in electronics, or bringing in any type of ethernet capability? What's their technology for understanding the output that we're trying to get for this?" That stayed with me. We want so much, and so many times, to say, "We have an idea. Two or three months. Come on. Go get it done. Here's the money." When really the understanding is there's a definite timeline, and it has to start with establishing that baseline at any given plant. And the baseline may be different from one plant to another even within the same company.
CobotsDavid Greenfield:
That's true because so many of these new collaborative robots - I'm seeing more and more of them come out where you can plug them into a standard electrical socket. You don't need a higher end industrial level of electricity to power these robots. They can just plug into a wall in your home. But just because you can do that, doesn't mean you should. To your point, you need to - like any technology - whether it's hardware automation, or software, you really need to look at where you're at, what you need, and what your issues are, and what is capable of being done in the facility before you just start buying things, and implementing them, trying to solve a problem before you figured out specific issues. That goes for robots as well as any other automation technology, absolutely. You know, I think it's important to add to these points that we've talked about, some information that we've collected at Automation World during a recent survey on planned robotic purchases across industry. Now, according to that research, of those planning to purchase robots in the next year, more than 56% plan to purchase a collaborative robot.
As we're all aware, and have been talking about, the social distancing requirements of COVID really increased industry's interest in robots even above the high level they were already at pre-pandemic. And I should note here that this interest in cobots is not just driving the development of cobots specifically, and related tooling, but also the ‘cobotization’ for lack of a better word, of industrial robots. And by that, I mean a number of companies are developing intelligent systems that can enable industrial robots to interact with humans like cobots do. And I think this is an important area to watch because it enables companies to use industrial robots in a human robot collaborative environment, and this is going to greatly expand the concept of what cobots can do, because industrial robots tend to provide higher precision, higher speed, longer reach, the ability to handle heavier payloads, etc. And in automation - where we've seen that - two of the most prominent examples of this in a past couple of years are at Mitsubishi through their partnership with Realtime Robotics.
Using the technology developed by these two companies, industrial robots can dynamically avoid collisions with each other, and with humans in the work cell. Robots using this technology react to each other's presence by recognizing when collisions are possible based on the positioning of the objects to be picked up by the robots. Another company to watch here is Veo Robotics, which has developed what it calls ‘free move technology’ for industrial robots, that uses computer vision to do a 3D analysis of the entire workspace to determine placement of fixed machinery, robots, and people in the work cell, and then it projects all the robot's potential positions over time, to create a safe operational framework for the robot. Veo uses the ISO 10218 robot work cell safety standard to ensure that robots are never a hazard to a person. And the company says that this approach with free move doesn't just apply to robotic work cell safety, but it can be extended throughout a line, or an entire factory. So, basically there's a lot going on here that's going to expand how we think about cobots very, very soon.
StandardsTom Egan:
I think your point about standards is very important. PMMI is involved in standards activity. We are a standards development organization, an ANSI standards development organization, and we do have a safety standard out that's used on packaging and processing equipment called B155.1. that can be used when you are integrating a robot as part of your packaging line, and I encourage everyone to take a look at that.
David Greenfield:
Thanks for adding that. Any other comments, Glen or Bryan, before we move on?
Glen Long:
The only other thing that pops to mind that's worthy of a mention, is that we talked about robots in food and beverage, and this is actually going even farther upstream: We've seen some tremendous applications of robot technology in farming, and in actually producing, or picking, and supplying, the food products into the plants. So, we're seeing it both up and downstream of where we traditionally are. And sometimes those advancements are coming farther, or faster than we see them in packaging just because there's a greater need for that. So, it's interesting to see the deployment of these in all the different areas where we touch.
Looking for reports mentioned in this discussion?
PACK EXPO Connects Robotics Exhibitors, click here.
Download Free PMMI Business Intelligence Report: Trends & Advances in Food Packaging & Processing, click here.
Download Free PMMI Business Intelligence Report: Automation Timeline, click here.
Download Free PMMI Business Intelligence Report: Robotics Innovation 2 Implementation, click here.
Download Free PMMI Business Intelligence Report: Industrial Robot Opportunities in Food and Beverage Processing, click here.
Packaging World Robotics Playbook, click here.
Free Download: 6 Key Robotics Trends in Packaging and Operations, click here.
Sponsored Recommendations
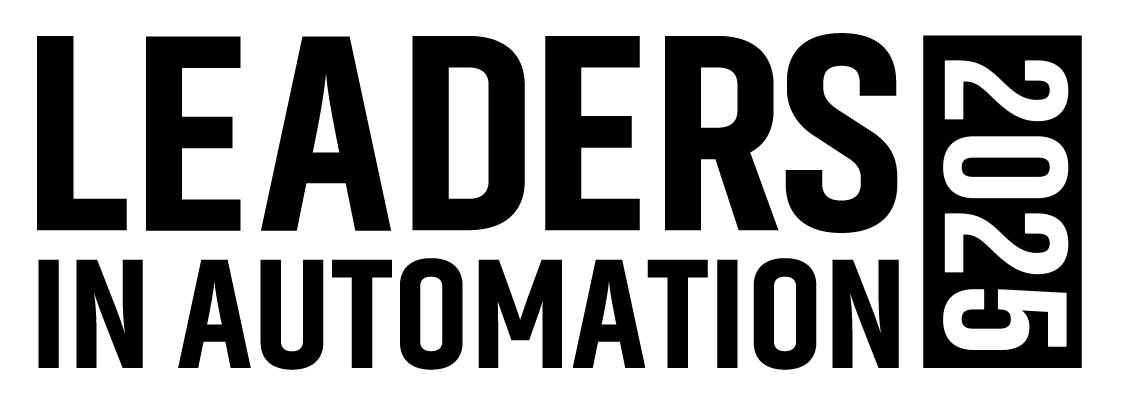
Leaders relevant to this article: