MES (manufacturing execution system) is a critical component of the operations technology stack. This technology provides the ability to optimize the manufacturing process through applications such as OEE (overall equipment effectiveness), SPC (statistical process control) and track-and-trace to leverage real time data from the factory floor and put it into context for the business of running a plant. Accurate and consistent plant floor data is the key to make it all hum. That’s where “MES enablement” comes in.
MES enablement is essentially the middleman for data translation. All factory floor data is scooped up, standardized, processed and structured in a concise format through the MES enablement layer before it is sent to the MES applications. The purpose is to maintain a consistent look and feel for all gathered information from every piece of equipment in each line that has MES functionality.
Computer babble
As mentioned above, there are countless devices on the plant floor that perform various functions in the manufacturing process. For example:
- Photo eyes and vison systems are prime data sources for MES to mine.
- KPI (key performance indicators) are gathered from weigh scales that measure each ingredient that goes into a product and captures it for a batch record.
- The control system compares the weight to the needed setpoint to distinguish when there’s been an error in weighing.
With so many functions, it’s no wonder that all this disparate plant information must be standardized so that an MES application can easily interpret it. After translation and organization of the data, MES applications provide the operators and supervisors information to optimize operations.
Without a structured MES enablement approach, however, the process of collecting valid data is onerous. The information gathered for presentation to the MES applications is not limited to a single line or even plant—most MES programs are intended for implementation at numerous facilities. If the data isn’t standardized, funneled and consistent from each line and piece of equipment, the potential for inconsistency and errors expand.
A major challenge to MES enablement is obsolete PLCs. Obsolete PLCs are often unable to meet the Ethernet communication requirements of a new MES system. In many cases, the unit itself is too aged and cannot be modified to provide the necessary data. In such cases, it is necessary to upgrade or replace the antiquated controller to allow reliable connection to the system.
A plan for enablement
The most important step to standardize and enable plant floor data for the MES application is developing a plan for the collection of the data that includes all the facilities that will access the MES applications. The plan must address the physical connections, the software concentration strategy, the rules for measurement of KPIs and a process for addressing outliers.
This plan can be challenging and, therefore, can benefit from insights provided by a partner integration firm. If you choose to work with a partner for the plan and eventual implementation, your partner should have a deep understanding of all the data devices and process equipment found on your plant floor and know how to extract the data from each. Additionally, the partner should have the scale to address the project as it rolls out to the multiple facilities.
Matt Ruth is President and CEO at Avanceon, a certified member of the Control System Integrators Association (CSIA). For more information about Avanceon, visit its profile on the CSIA Industrial Automation Exchange.
Companies in this Article
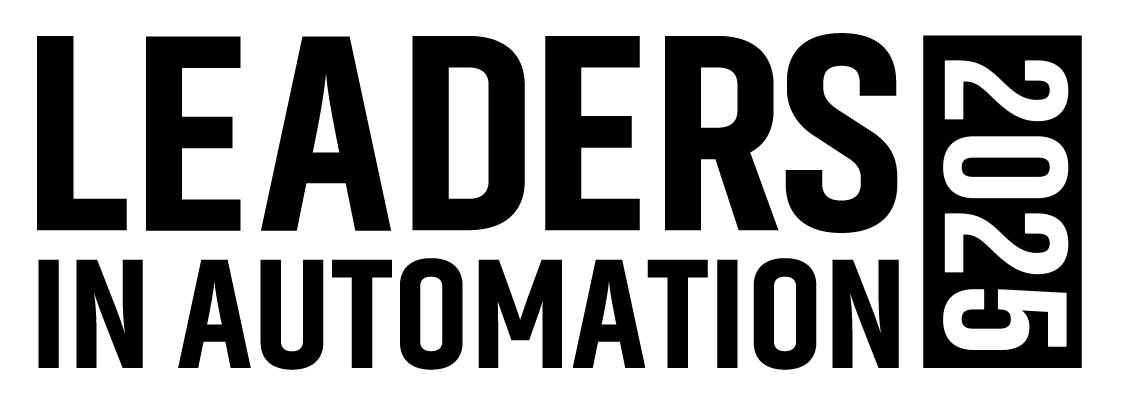
Leaders relevant to this article: