Read the full transcript below
David Greenfield: Welcome to the Automation World Gets Your Questions Answered podcast, where we connect with industry experts to get the answers you need about industrial automation technologies. And you can find even more answers by subscribing to automation world at Subscribe AutomationWorld.com
I'm David Greenfield, Director of Content for Automation World. And the question we'll be answering in this episode is how to select the right valve for an application. And joining me to answer this question is Ross Turbiville, Senior Director of global industry sales of flow control products at Emerson Automation Solutions. So thanks for joining me today, Ross.
Ross Turbiville: Thanks for having me.
David Greenfield: Alright, so let's get into it. You know, let's start the discussion by you know, just explaining the different types of commonly available automated valves based on the function and the effect the media to be controlled by the valve impacts a user's selection decision.
Ross Turbiville: Yeah, so as we look at this and different types of automated valves, there's, there's two big distinctions, you can have automated on off valves. And then you can have control valves that are automated. And even if you look at the automated on off valve space, there's what I would deem a general automated on off valve. And then there's also automated on off valves that go into Safety Instrumented Systems. So those are a couple of distinctions people need to consider, as they're looking at, what is the valve and what's the function they wanted to do? And then, you know, if we look specifically at the control valve side of it, right, it's really looking at what kind of control resolution do you need? What does your system look like? And ultimately, with a control valve, you're trying to, to size and select a valve that has a characteristic that allows the system to be linear with an installed gain of point five to two.
David Greenfield: Okay, thanks, Ross. So what about valve sizing and performance based on flow pressure and temperature characteristics of the media that will be moved through the piping system?
Ross Turbiville: Yeah, so first and foremost, you need to be looking at it from a safety perspective. And when I talk about that, from a safety perspective, what I'm looking at is what's material capability from a corrosion erosion perspective with the media that you're flowing. And then the second piece of the safety perspective is the pressure temperature limitations of a given material and making sure that the material and the pressure kradic class rating, you select for the valve meets meets code requirements, to ensure that there's not a safety event that happens there. The second piece that that you need to take a look at there is obviously the flow of the valve. So you've got pressure and temperature to that also will play into the valve size, depending on your pressure drop. But the flow also takes a big impact on what the capacity of the valve needs to be. So first, make sure that you select the valve that has material that can meet the media from a safety perspective with corrosion, erosion, pressure and temperature limitations. And then from there, you got to work to size your valve to make sure it has the capacity to handle the flow that you're looking at with that media.
David Greenfield: So how does the type of piping system use impact ended users valve choice?
Ross Turbiville: Yes, so the piping system use can impact the type of valve or what you want the valve to do in any given piping system. On the control valve side, when you look at the capacity of the valve, it's dictated by IEC standard 60534 dash two dash three. And what this does, it defines the number of straight runs of pipe upstream and downstream of the valves as well as sensor locations to allow measuring the capacity of the valve when you're in a lab environment. Anytime you get into a potential piping system that is compressed, there is also a risk of capacity of the valve could be different than the published values. It's also good to note that with the public values, the standards also allow a margin of air and the capacity dictated by the industry codes right. And when looking at a piping system, understand what the piping system looks like, and then consult with your valve vendor, if you have a very tight piping system to understand the impacts of that piping system. One great example, we have learned at our Emerson Innovation Center, Marshalltown, Iowa was related to the emergency cooling valve for the AP 1000 nuclear reactor, we put together the actual system for the AP 1000 reactor cooling valve. And the intent of this valve is to allow gravity flow of water in case of an emergency. So it's very important to the cooling. And what we found when when we did this is this compressed piping system had a head of large impact on actual capacity of valve in the system, versus the theoretical capacity of the valve. And the impact that was there was a much reduced capacity of that valve inside the piping system.
David Greenfield: Okay, thanks for explaining that. Ross. So, you know, so far in our discussion, you know, we've talked about, you know, the effects of the media being moved through the piping, how that affects valve choice, you know, you just explained how the type of piping system used impacts valve choices. But, you know, how about when it comes to assessing the materials used to construct the valve itself? You know, in that case, you know, when you're looking at those materials, how does the media being controlled the operating environment, and maintenance issues influence valve selection choices based on what the valve is made of?
Ross Turbiville: Yeah, so the biggest thing there, you know, beyond obviously, material compatibility from a corrosion erosion perspective, is understanding what type of media are you flowing? Is it a compressible media? Is it a non compressible media? Is it clean service, or what I guess I would call a dirty service where there may be debris in it. And then, you know, looking at, what's the pressure drop in that service, and what the valve design is, if you have a dirty or service with debris, obviously, you'll want to stay away from any valve designs that have small Jerald hold trends. Because at that point, you'll end up with more of a strainer in your line versus a controlling, modulating control device or or an on off device that can that where you can control the on off. And then you've also got to look at from a pressure drop perspective, and an E S and H perspective of what are the requirements are around it? Does? Do you have a noise restriction? You need to meet right? Are there? Are there other things going on in the piping system? Or or the area around it? Where special considerations need to be met? What what fluid are you flowing? And what does it mean from an admissions perspective? And then at that point, it'll allow you to select the appropriate valve design, whether that's a butterfly valve, a ball valve, or a globe valve, when it comes to the control side? And then, you know, on the on off side of things, can there be a pressure drop or not? Does a butterfly valve make sense? Does a triple offset valve make sense? Do you need a full bore ball valve. And once you understand these things, then you can get into what what valve is needed. Work the details to make sure that you comply with all of the requirements that you may have in a given system.
David Greenfield: So since this is an automation world podcast and we're speaking with you from Emerson automation solutions, we're obviously talking about automated valves here today. So can you help explain the choice of electric pneumatic or hydraulic actuators for a valve? And how will use a user can determine which is the best fit for their operation?
Ross Turbiville: Yeah, so there's, there's there's a couple different ways to look at this. And first and foremost, I would look at it from a performance perspective, and how quickly a valve needs to respond to process changes. Whether that's on the control side, or on the on offside, to make sure that the process is taken care of and the way it's intended with the design. And if we look at that anything where you need quicker response to a given process change or command, you're going to need to be looking at a pneumatic, or hydraulic operating valve. If response time is less critical, and it can take longer than at that point, you would you could potentially start looking at electric actuation. Now, the the second piece that's really important with that is also what's the cost of the valve? What is maintenance look like? And what environmental safety and health considerations need to be taken into effect, right? If we look at the cost perspective, typically, we're looking at hydraulic actuators as being the most expensive, then electric actuators. And the most economical actuators are the pneumatic actuators, right. And you also need to look at other things is, depending on what media you could be using to drive your actuator, what the emissions look like, you know, in the upstream oil and gas world, if you're using gas to drive a pneumatic actuator, you know, and especially with changing regulations, that may make less sense, and you should go electric, at the same time hydraulics, right can provide extremely high resolution control, they can move very quickly. But they also have an oil reservoir that needs to be taken into account. What is the maintenance of that look like? What are potential environmental impacts? And what are other safety hazards or considerations that should be taken in place when you're selecting the actuator type.
David Greenfield: Okay, so I you know, I noticed in your in your response area, you mentioned environmental health and safety issues, emissions regulations and such. So, given that, you know, I guess one last question here is, you know, what codes, standards or regulations should users pay attention to is they're going about selecting vowels?
Ross Turbiville: So one, one piece, that's, that's been written by n tech to help look at what type of valve there is to select on the control side is there they've written a specification called control valve, dynamic performance specifications. And it walks you through a series of things to consider to determine what is the right type of valve and what type what what is the right type of actuation system to select the best control valve for your process. So that's an important piece in terms of control and what you're looking at. But then also if we just look at general industry standards, and the important industry standards to consider as you're sizing and selecting control, control valves, or automated on off valves is one ASME B 1634. That encompasses both control valves and on off valves. And early as the design basis for what you need to consider or what a manufacturer needs to do. When it comes to pressure boundary parts and making sure you have the correct wall thickness for each for each material type. And the pressures and temperatures of that they can withstand the second code that that needs to be considered from an overall piping system is there's ASME B 31 dash one which covers power piping code, and B 31.3. That covers process piping codes. These will help make sure that the valves you're selecting meet code and ensures you have the best potential valve in place to for safe operations. Then, you know, there's there's two other there's a couple of other codes where there's differentiation between control valves, and on off valves. And those are shut off leakage class codes. So control valve shut off is is dictated by the standard that's FCI 70 dash two while on off, shut off requirements code is API 598. And those are two very important distinctions based on what you want your valve to do and whether you want it to control or you want it to be an isolation automated on off valve. There are also other standards out there, most of them driven by IEC II that also relate to noise calculations and understanding the mitigation of noise within control valves.
David Greenfield: Well, thank you for joining me for this podcast Ross and thanks of course to all of our listeners and Please keep watching this space for more installments of Automation World Gets Your Questions Answered. And remember that you can find us online at AutomationWorld.com. And subscribe to our print magazine at SubscribeAW.com to stay on top of the latest industrial automation technology insights, trends, and news.
Companies in this Article
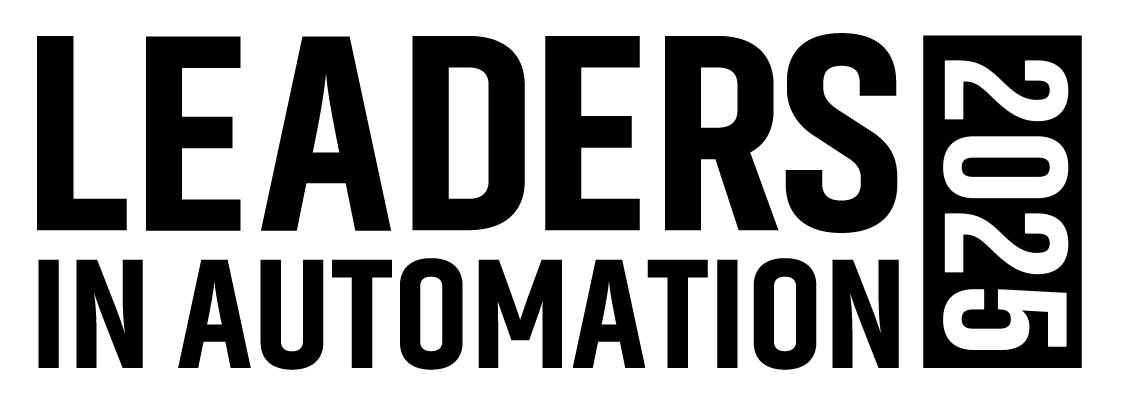
Leaders relevant to this content: