Building Machines Humans Can Work With
Editor’s note: The term Industry 5.0 is easy to dismiss considering manufacturers have only just begun implementing Industry 4.0 to a large degree. But it’s important to realize that Industry 5.0 is not the next step after Industry 4.0. Instead, it’s a concept centered on human-machine collaboration. As such, the term Industry 5.0 could be considered a misnomer. However, the term has caught on to a large degree and is being used widely by the European Commission; therefore, it’s a term industry should get more accustomed to and realize that, despite its name, it’s more a part of Industry 4.0 than a next step beyond it.
The first industrial revolution began with the introduction of steam power and the second involved electrification. Computers characterized the third industrial revolution, and we are well into the fourth. Industry 4.0 is concerned with increasing the efficiency and productivity of manufacturing systems by networking entire factories and applying sophisticated controls.
There are limitations inherent in Industry 4.0 that have some manufacturing companies already embarking on Industry 5.0, however. The keys to overcoming those limitations are likely to be human attributes that global industry just spent several hundred years engineering out of manufacturing.
Each successive stage in industrialization thus far has represented a step away from custom creation and a move toward standardization, increasing scale, greater precision, and improved productivity—toward mass production. Each industrial leap has also been marked by industrial processes becoming more highly automated while human effort in those processes decreases.
Many have come to believe those two trends are at the point where further pursuit will render diminishing returns. With the advent of artificial intelligence (AI) and machine learning (ML), precision robotics and advanced sensors, the machines we have created can achieve amazing things, and it is hard to imagine after all those innovations how mass production can progress beyond incremental improvements in scale, precision and productivity. But there is still one great leap in industry imaginable. It would be to bring the whole thing full circle instead—to take mass production capabilities and apply them to custom manufacturing.
This would require creativity and adaptability, two qualities that rely not only on flexibility but on the ability to be flexible on short notice and with relatively little input. These are traits that machines lack and are unlikely to gain any time soon (if ever). Machines cannot reliably make predictions on outcomes based on minimal data. They are not capable of rapidly adapting in response to new data or to situations never encountered before. They cannot be creative.
Industry 5.0
A key characteristic of Industry 5.0 is collaboration between humans and machines. Proponents of Industry 5.0 expect that humans working in tandem with machines can achieve what neither could accomplish without the other. That said, part of the motivation to develop this new industrial model is dissatisfaction with the dehumanization that has accompanied industrialization thus far.
Europe has led the conceptualization of Industry 5.0. According to the European Commission (EC), Industry 5.0 “places the wellbeing of the worker at the center of the production process and uses new technologies to provide prosperity beyond jobs and growth while respecting the production limits of the planet.”
Industry 5.0 is not expected to supplant Industry 4.0 in the way that electrification replaced steam power, for example. According to the EC, Industry 5.0 “complements the existing Industry 4.0 approach by specifically putting research and innovation at the service of the transition to a sustainable, human-centric and resilient European industry.”
Cyborgs and centaurs
The concept that a collaboration between humans and machines can achieve more than either alone was popularized long ago in fiction about cyborgs. More recently there have been real-world examples that have encouraged proponents of Industry 5.0.
For example, in 1996, world chess champion Gary Kasparov defeated an IBM computer called Deep Blue in a tournament. In a rematch the following year, Deep Blue won. It was the first time a computer had ever defeated a human champion.
Kasparov began training with a chess computer himself and started referring to human players who augment their chess skills with computers as “centaurs.” Where the centaurs of myth were half human and half horse, modern centaurs are half-human and half computer.
Kasparov pointed out that a chess centaur consistently beats both human chess masters playing without computers as well as computers playing on their own. The combination of human creativity and computer processing proves superior.
Engineers already rely on electronic design automation (EDA) tools to perform some of the rote work of designing integrated circuits, printed circuit boards and systems. This has encouraged the expectation that engineers working with even more capable EDA tools built to support richer human-computer interaction might be able to achieve extraordinary designs as yet unimaginable.
It is entirely possible that improving such interactions will lead to unique results, but that might not be necessary to make Industry 5.0 a success. For starters, just the ability to quickly alter a factory’s output in response to any kind of market condition (including ongoing technological innovation) would be a boon.
A shift in values
Industry 5.0 is not just about new manufacturing modes, such as semi-custom mass production, or enriching the ability of humans and machines to collaborate to create the potential for new levels of achievement.
Per the EC, it not only brings humans back to the center of the manufacturing process by emphasizing human-machine interaction, it explicitly brings the well-being of workers back to the center of the process. Workers would become investments rather than costs.
This represents a fundamental shift not just in industrial processes but in societal values as well. In fact, the EC explicitly links Industry 5.0 to Society 5.0, a relatively new concept that proposes to “balance economic development with the resolution of societal and environmental problems.”
The process of industrialization has always been criticized for being dehumanizing. That can be mitigated and perhaps even reversed by restoring the value of uniquely human characteristics and qualities in the manufacturing process.
There is a growing desire worldwide to mitigate climate change and even industries that haven’t fully embraced that goal understand that going “green” involves becoming more operationally efficient, which can translate into potentially significant cost savings. Industry 4.0 does not address environmentalism at all. Environmental concerns will be fundamental to Industry 5.0.
The core values in practice
The EC’s definition of Industry 5.0 says it will be sustainable, human-centric and resilient. What does that mean?
The EC states that a business that is purely profit-driven is “untenable,” failing to take into account environmental and societal costs and benefits. With every new innovation, the question shouldn’t be how much money can we make on it, but what are its advantages and drawbacks? How does it serve us?
Sustainability is fairly well-defined. It means designing products for reuse, repurposing and recycling. It means managing consumption and reducing waste. These are all principles embedded in the concept of the circular economy, which the EC also refers to in its definition of Industry 5.0. Resilience means making sure that production is robust in the face of market setbacks, interruptions and disasters. It also means being able to adopt and adapt to innovations.
Technological and human progress
Industry 5.0 is a concept still in development. Like other conceptual proposals, it is apt to be debated and evolved as manufacturers around the world collaborate on its principles and goals.
Brian Santo has been writing about advanced electronics and emerging technologies for more than 30 years at several publications including Electronic News, IEEE Spectrum and CED, later serving as editor in chief of EE Times.
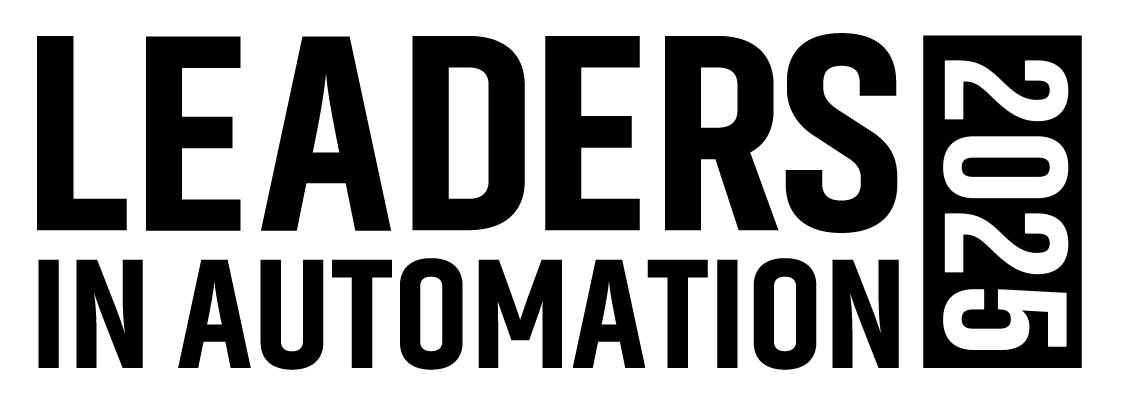
Leaders relevant to this article: