Unlock Smart Manufacturing’s True Potential with Dark Data
Smart control systems and devices that share data with each other through industrial communications protocols have changed how industrial producers understand and improve their operations. But most producers still aren’t close to realizing the true potential of smart manufacturing. That’s because the real work of enabling transformative smart manufacturing won’t happen at the controller level, it will happen at the software level.
When software applications can analyze and act on the vast metadata in production devices that goes unused today—also known as dark data—they change what’s possible in production. You may not realize it, but most of the data generated by your equipment and devices lies deep in the device firmware to optimize local operation and is unseen by the user of the device. This dark data can unleash, among other things, more comprehensive predictive maintenance than is possible now, smarter machines that can self-configure for new production runs, and richer insights into how machines and plants are performing across an enterprise.
These and other opportunities will soon be a reality thanks to the work of industry bodies like the OPC Foundation and ODVA. Their efforts, like ongoing advances in the EtherNet/IP protocol and the OPC UA information modeling framework, will make dark data from multi-vendor production environments available in the form of structured, human-readable models. And it’s from these models that innovative new software applications can be built and deployed.
Breaking down barriers to dark data
Powerful software applications are already being used with control systems today to analyze their dark data, which includes all those details about what control system and device algorithms do that haven’t previously been scrutinized. Readily available AI-powered tools, for instance, can continuously monitor a production asset and notify maintenance teams if it detects deviations from the asset’s normal performance.
Applications like these can help industrial producers combat costly downtime. But they’re just the start of what software can do to optimize production, because the applications that exist today can only be applied to a vendor’s own technologies.
Most production environments are complex ecosystems made up of technologies from several different vendors. And those vendors naturally don’t want to reveal their proprietary secrets by exposing their design documentation. This is where an initiative like OPC UA comes into play. Its goal is to allow those vendors to make their devices become self-describing, communicating not only their data, but also their capabilities and functionalities, controlling the way that proprietary information is exposed.
This will break open the door for data scientists to create software that can finally connect to all of a producer’s control and automation devices. And that software will have drastically larger datasets than anything that maintenance teams have been able to access because it will leverage not only the process data that’s widely used today but also massive volumes of device dark data. This will allow the software to uncover opportunities to optimize production all the way from the machine level to the enterprise level.
The next leap forward
So, what will the next iteration of smart manufacturing look like when software can analyze and act on a producer’s wealth of dark data, which could be as much as 90% of an organization’s data? A few likely outcomes include:
Producers will become even more resilient against downtime. Machine learning applications will ingest more data and gain a more complete picture of the causes of failures and how to get in front of them. If a machine does fail, asset diagnostics and a complete history of the machine’s health and performance will be used to identify what went wrong and prescribe how to fix it. This will help speed up recovery times and reduce companies’ reliance on workers with historical knowledge who will take that knowledge with them when they retire.
Smart machines and plants will evolve into smart enterprises. Data pulled from across a producer’s installed base will provide insights into where performance gains can be made across the enterprise. Operations teams, for example, will be able to evaluate how assets are performing worldwide and identify the top-performing machines or lines as well as the laggards. Those teams could then start analyzing the data to understand why certain machines or lines are underperforming to help push the entire enterprise toward a gold standard for production.
Production operations will become more flexible. Software applications will be able to help employees quickly reconfigure machines or lines for each new production run. This will help make shorter production runs more efficient and personalized products possible or more profitable. Software may even enable machines or lines to be self-optimizing and self-reconfiguring. A beverage company’s sales promotion for six-packs of juice, for instance, could automatically trigger a plant to reconfigure its production lines to adjust for different production rates and speeds based on the volume expected to be sold from the promotion.
The next evolution of smart manufacturing
The controller-to-device loop has largely been solved and addresses the needs of most industrial producers. Today, machines or lines are optimized in real time with industrial communications protocols that facilitate seamless data sharing and analysis within a control system. Extending that data sharing and analysis into innovative software applications will help make individual production assets and entire enterprises more productive and sustainable across their entire lifecycle.
Paul Brooks is senior manager of open architecture management at Rockwell Automation.
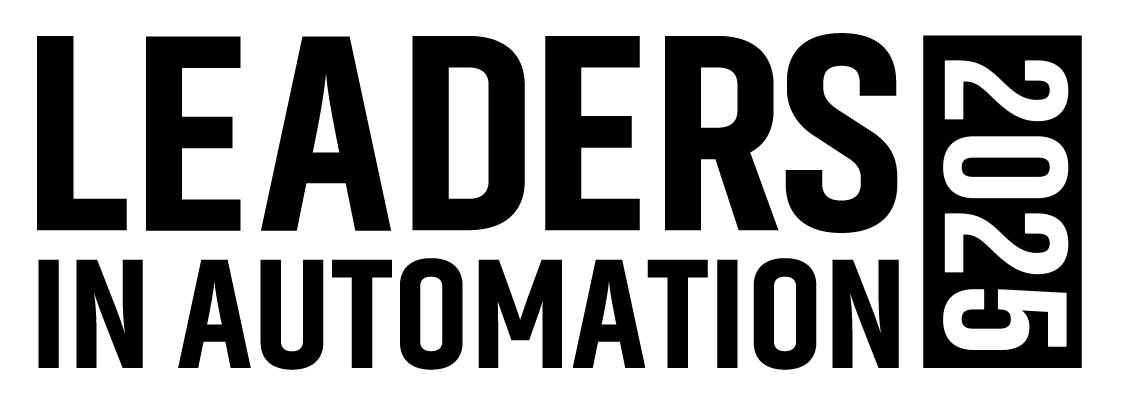
Leaders relevant to this article: