The Case for Frameless Motors in High-Performance Applications
Sept. 25, 2024
A frameless motor is essentially the active torque and speed-producing element of a conventional motor, but without the shaft, bearings, housing, feedback or endbells. It consists of two main parts: the rotor and the stator.
The rotor, typically the inner component, is a rotating steel donut assembly equipped with permanent magnets that mount directly onto the machine shaft. The stator is the outer component containing toothed steel laminations wrapped with copper windings. These windings create the electromagnetic forces necessary for motion. The compact nature of the stator allows it to fit neatly within the machine housing, making frameless motors an excellent choice for space-constrained applications.
Frameless motors, like all servo motors, work as part of a complete servo system. This integration involves one or more feedback devices, such as incremental or absolute encoders, as well as Hall effect sensors or resolvers. These devices provide essential information about rotor position to a drive amplifier, which continuously fine-tunes rotor position and speed to meet application requirements. This process is governed by a series of embedded control loops, ensuring precision and reliability in various operational conditions.
Design considerations
When deciding between a housed motor and a frameless motor, engineers should consider several issues:
- Does the machine need to be smaller?
- Do unreliable mechanical components need to be removed?
- Should the machine operate at a higher throughput rate?
- Does the machine operate in a rigorous environment with elevated temperatures or caustic conditions?
If the answer to any of these questions is yes, a frameless motor approach may be the optimal solution. Following are three primary design considerations that suggest the need for a frameless motor:
Reducing machine footprint. Machine size is often a crucial factor, especially when floor space is limited. Integrating a frameless motor into the machine structure can significantly improve space utilization. By minimizing the space required for the motor, and eliminating gearboxes or belts and pulleys, engineers can save additional space. Frameless designs are particularly advantageous in direct drive applications, where the motor drives the load without the need for intermediary components.
Enhancing Machine Performance. Frameless motors can enhance machine performance by eliminating compliant mechanical elements, such as gearboxes, couplings or belts. Direct drive solutions provided by frameless motors offer more robust performance due to the reduced compliance or backlash in the system. Every linkage in a mechanical system introduces compliance elements that decrease system bandwidth, leading to longer move and settle times and, consequently, reduced productivity. Integrating motors also improves dynamic response and system efficiency. Additionally, the ability to incorporate liquid cooling can substantially increase the available continuous torque.
Rigorous Environmental Conditions. For machines operating in harsh environments, an integrated motor design with frameless components can be highly beneficial. The machine’s existing housings and enclosures, already designed to withstand these conditions, can be utilized to incorporate a frameless motor without significant cost implications. Frameless motors offer the flexibility to integrate motor components directly within the machine elements, protecting them from adverse environmental effects. Rigorous conditions may include high-pressure washdowns with caustic chemicals, elevated ambient temperatures, or even radiation or vacuum environments. For example, food processing machinery that requires stringent washdowns, or gas turbine actuators that operate at high ambient temperatures, can greatly benefit from the robustness and adaptability of frameless motors.
Key advantages
Frameless motors provide several advantages that make them a compelling choice for engineers:
- Compact, lightweight form factor: By eliminating redundant components, engineers can directly integrate the housing, bearings, shaft, couplings and other elements into an exceptionally compact application design.
- Precise performance: Frameless motors can drive the load directly without the need for transmission components. If gear reduction is required, these motors can be seamlessly integrated with compact, low- or zero-backlash planetary, harmonic or cycloidal gearing, offering instant response to changing speed and position demands.
- Environmental resilience: When embedded directly into the application, frameless motors can be thoroughly protected from caustic washdown fluids, submersion, weather exposure and other environmental hazards. Moreover, high temperatures can be managed effectively through the machine structure, ensuring efficient operation even under challenging conditions.
- Design freedom: Frameless motors are available in both torque motor (short axial length relative to diameter) and servo (longer axial length) form factors, as well as in a wide range of diameters, stack lengths and winding variations. This versatility allows engineers to tailor the motor design to the specific needs of the application.
Applications
Frameless, brushless DC motors have become indispensable in various advanced applications due to their compact size, power efficiency and adaptability to demanding environments. These motors are particularly valuable in robotics where they power the most compact and powerful robotic joints. This capability enhances the dexterity, versatility and efficiency of systems like surgical robots, humanoid robots, exoskeletons and industrial collaborative robots (cobots).
In control actuator systems, frameless motors provide optimal torque and speed within extremely confined installation spaces. Their reliability in the face of shocks, vibrations and temperature variations makes them ideal for aerospace applications where durability and performance are critical. This reliability extends to compact rotary actuators, where frameless motors enable tight motion integration, driving loads directly or through compact gear sets like harmonic, planetary or cycloidal gears.
The food and beverage production and packaging industries also benefit from frameless motors, particularly in hygienic applications. These motors can be embedded in machinery in a way that ensures that washdown fluids do not come into contact with the motor, maintaining sanitation standards without compromising performance.
Tom S. Wood has been a motor product specialist at Kollmorgen for more than 40 years.
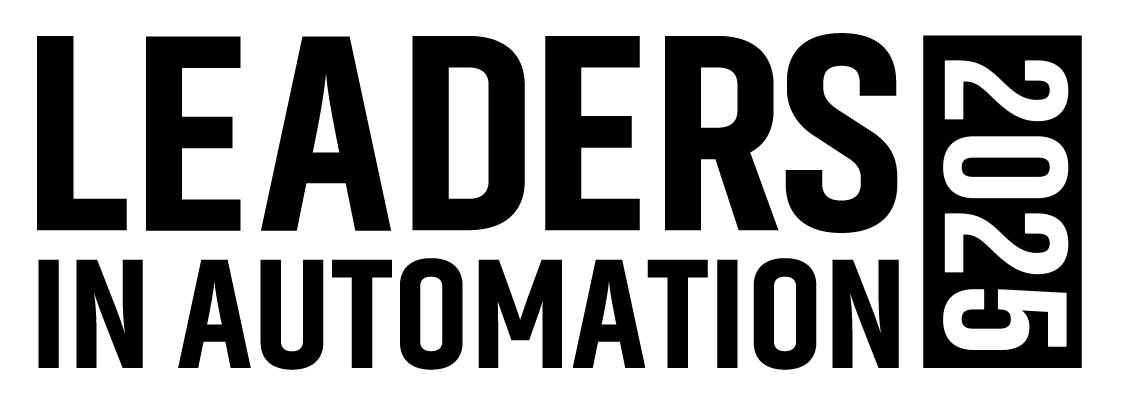
Leaders relevant to this article: