Just over a year ago, in October 2022, Universal Robots introduced the UR20, which, in addition to being the company’s highest payload and longest reach robot at the time, also introduced new design features. Anders Billesø Beck, vice president of strategy and innovation at Universal Robots, characterized the new design as a “complete mechanical reengineering of the whole UR system concept. We hardened the design concept and shifted generations on a lot of technologies to deliver way more torque into the same package to reduce weight.”
Now Universal Robots has announced the UR30, which features the same small footprint as the UR20 but a heavier payload capacity of up to 30 kg. According to Universal Robots, the UR30’s “superior motion control…makes it ideal for several applications, including machine tending and material handling. For machine tending, the high payload allows the cobot to use multiple grippers at the same time to remove finished parts and load more material in a single pass, shortening changeover times and maximizing productivity.”
Beck said that users of Universal Robots’ cobots “often need to handle multiple products in and out of the machines, that’s why the UR30 is designed to handle fairly heavy parts and hold multiple parts at the same time. Moving in and out of machines is done in a tight, confined space, with the UR30’s compact form factor, it can fit into much more compact workspaces.”
Because heavier parts in palletizing applications tend to be around 50 pounds, Beck said the higher payload capability of the UR30 allows it to “comfortably stack parts” in that weight range.
The UR30 also supports high torque screw driving and can handle larger and higher-output torque tools using its “steady mode” feature for straight and consistent screw driving. Beck said steady mode allows the UR30 to drive bolts and screws at a high torque rate without creating safety risks to humans in the work area. Beck explained that cobots will “go into protective mode when meeting resistance. Consequently, many cobots on the market require the user to disable certain safety settings when used for high-torque screw driving. But not the UR30. It can measure the force given and deliver straight, consistent screw driving without activating the protective stop and still maintain safety.”
This steady mode feature is implemented in UR’s other cobots, but Beck noted that is especially useful with the UR30—Universal Robots’ first cobot dedicated to high-torque screw driving.
Speaking of the cobots’ safety aspects, Beck noted that the UR20 and UR30 feature the same certified safety system and built-in safety functions as Universal Robots’ other cobots. “This allows you to limit the robot in a lot of different ways to be in close interaction with humans. But obviously, it still requires a risk assessment on the application to assess overall safety.”
The UR30 also introduces a new end-of-arm tool flange which is Universal Robots’ new standard for its high-payload cobots (UR20 and UR30). This new tool flange is essentially a more robust collar to handle the additional stresses put on the connected robot joint when larger payloads are attached.
To highlight the similarities and differences between the UR20 and UR30, following is a comparison of the key features:
- Payload capacity: UR20 = 20 kg (44 lbs.); UR30 = 30 kg (66.13 lbs.)
- Reach: UR20 = 1750 mm (68.9 in.); UR30 = 1300 mm (51.2 in.)
- Weight: UR20 = 64 kg (141.1 lbs.); UR30 = 63.5 kg (139.9 lbs)
- The footprint of the UR20 and UR30 are the same: 245 mm (9.65 in).
Beck clarified that Universal Robots does not expect the UR30 to impinge on the UR20 in the market, noting that both cobots are designed to address specific end user applications across payload and reach.
The UR20, for example, with its combination of long reach and heavy payload serves many applications— including the ability to stack pallets up to full truck loading height, said Beck. “It’s also well suited to welding applications where you need to carry weld guns around a large work area,” he added. “These factors still make the UR20 a very strong cobot in the market with its significant difference in reach.”
The UR30 is available to order now with delivery planned for Q1 2024.
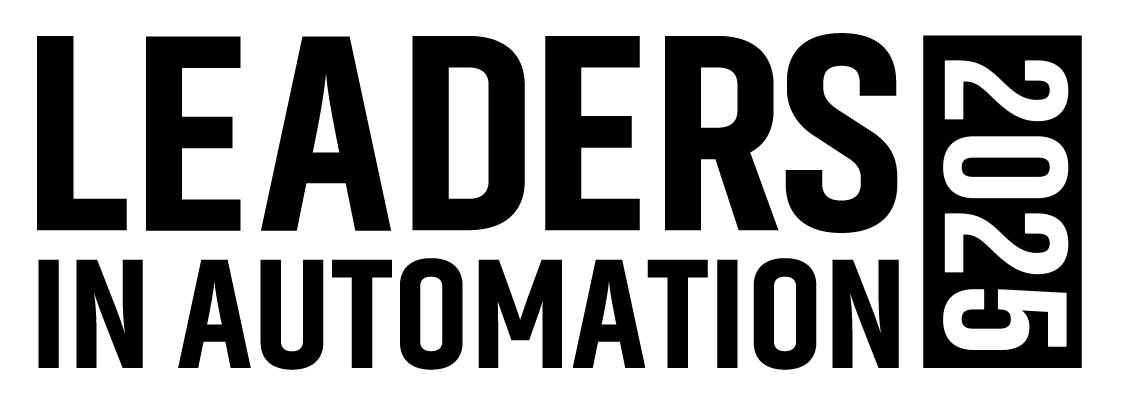
Leaders relevant to this article: