Finding talent is a huge pain point for manufacturers, in the US and around the world. More than 90% of CEOs globally believe talent scarcity and a lack of relevant skills are standing in their way to success. This sentiment was echoed at The National Association of Manufacturers’ (NAM) fall board of directors meeting. There, I had the opportunity to speak with corporate executives and industry leaders from North American manufacturing companies.
What keeps them up at night? The fact that an aging workforce and the ongoing reshoring of production capabilities is driving the competition for talent to new heights. Apart from the issue at hand, leaders were also discussing possible quick fixes, mid-term tactics and long-term solutions.
In my view, for these discussions about talent to lead to meaningful outcomes, they must account for the deep changes manufacturing jobs will undergo. I am, of course, talking about the consequences of industrial automation and advanced artificial intelligence (AI) in the workplace.
Among leaders and workers, the topic spurs excitement and fear alike. Since AI’s big bang moment—the introduction of generative AI to the general public—not a day goes by without news and analyses on how it will break new ground. Accenture research found that the effects could indeed be huge, with 40% of working hours across industries potentially being impacted.
Emerging roles
But it’s not (just) this latest technology advancement that is changing manufacturing jobs. Traditional AI, in concert with more established digital technologies, have as much impact, if not more, on the skill sets required on the factory floor. Future work will require more creative thinking in problem solving and decision-making, empowered by tech.
Here are five examples of future manufacturing roles:
Digital manufacturing technician. Assembly and maintenance technicians, who used to do mostly manual work like assembling products and maintaining machines, will now learn new skills and become digital manufacturing technicians. In their new roles, they will use technologies like digital twins and AI to anticipate and prevent the breakdown of equipment, digital platforms to connect with experts in real-time and analytics dashboards to share real-time updates of production schedule and work order details.
Smart scheduler. Production coordinators and schedulers will be elevated to smart schedulers. Their roles will change from leveraging historical data with traditional forecasting algorithms and tools to manually maintain production schedules to using advanced market and supply chain analytics to set current and future schedules in real-time. They will also use connected technologies to analyze large data sets and generate reports to optimize scheduling.
Smart safety supervisor.Site leaders will become smart safety supervisors who use advanced tech and insights from analytics to see all safety indicators on one integrated platform. Using real-time, predictive data, they will be able to anticipate and prevent workplace accidents. Connected technologies will help them conduct inspections remotely.
Digital twin engineer. The current production engineer will move on to use new methods that involve making 3D designs and simulations to innovate and virtually test production processes. They will also use data from sensors to test how things perform in real-time. It will be easier for them to make decisions about managing equipment to drive uptime and extend equipment life.
Robotics coordinator. Process managers and change managers will become robotics coordinators who combine human skills with machine power in manufacturing. They handle administrative tasks with the help of automation and robotics, use real-time analytics and data insights for supervision and decision-making, and enhance autonomous robots to work faster and with higher quality.
Autonomous teams
Various technologies, with AI first among them, are likely to change manufacturing even more deeply. We see clients considering the notion of autonomous teams.
The idea behind autonomous teams is: Rather than having line or shop operators and departments for planning, scheduling, quality control, maintenance, etc., an autonomous team operates, maintains, schedules and quality manages the line or shop independently. These teams are supported by a digital twin-based, real-time hypervisor that provides information in context to anticipate and adapt to process deviations. Virtual or physical centers of excellence that exist cross-plant can be relied on at any time to support in the resolution of technical issues.
Think of autonomous teams like agile project management, where teams get assembled in pods and/or scrums. They are assembled based on competencies required to define, build, test and deliver assignments of value to their customers. Responsibilities and directive powers are temporarily assigned to the individuals with the best-suited skills for accomplishing a management assignment, plus they need to be dynamic in collaboration with other teams to deliver solutions and contribute to the vision and roadmap.
Develop a talent ecosystem
Organizations can also build the future manufacturing workforce through partnerships that invest in untapped talent sources. Accenture partnered with Purdue University to fund the creation of the Accenture Smart Factory on the university's campus. The program will include a Women in Manufacturing scholarship designed to attract more women to manufacturing fields and drive inclusion and diversity in the industry. We have a similar initiative in Canada, where we are investing in the students of Conestoga College’s Skilled Trades and Engineering programs. Hiring diverse talent would also help an organization contribute to a stronger, more equitable economy and more equitably shared prosperity for all.
Redesign the future workforce
No doubt the role of AI will be huge in enterprise transformation, but it’s important to maintain worker know-how and ensure that decision-making remains in the hands of the workforce. As business leaders solve the talent puzzle, they will have to perform a balancing act. Their quest to address cost pressures and talent shortages should be underscored by their responsibility to bring their employees along on the journey. AI can, no doubt, help them uncover opportunities to transform roles across their organization—STEM or non-STEM. Manufacturing leaders will need the skills and capabilities to deconstruct work, codify talent pools, identify opportunities for automation and create the conditions for collaborative and agile work environments.
It’s important to realize that innovative technology is only one piece of the puzzle. The most successful companies prioritize people and place them at the core of any transformative process. After all, without people, nothing can truly change.
Companies in this Article
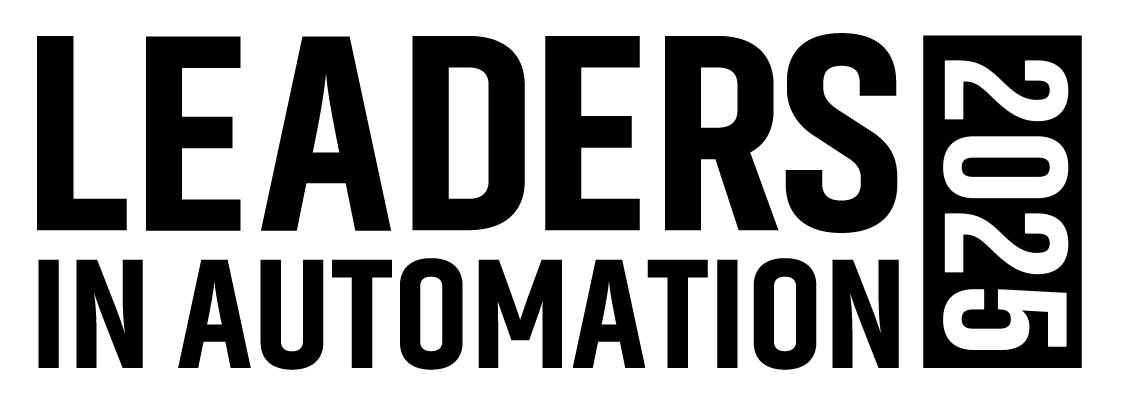
Leaders relevant to this article: