It’s the rare company that admits it made a mistake. All too often, corporate America relies on cover-ups, half-truths and even outright lies to prop up stock prices and protect “shareholder value.”
The media paints a bleak picture of the lack of corporate values in modern culture. A recent front-page story in the Chicago Tribune trumpets, “Corporate culture led to fraud case.” A top sales executive, in a sworn statement, quotes the former CEO of a wiring and cable distributor as saying, “Ship it to your grandmother. Ship it to your garage. Make your frickin’ numbers.” The now-defunct business is under investigation by the Securities and Exchange Commission for financial fraud.
Need more examples? Consider a few run-amok executives at Arthur Anderson, Enron, Tyco and WorldCom and the impact their illegal actions had on tens of thousands of innocent employees.
But the whistleblowers in the financial fraud cases aren’t the only ones wearing the superhero capes. Sometimes, it’s just the regular guy at the manufacturing plant, doing his or her best to make conditions safer, better and more profitable.
This issue of Automation World highlights those individuals, companies and standards organizations that are working together to create a safer and more secure industry for employees, customers and the environment. Some of industry’s finest manufacturers are risking potential embarrassment in “fessing up” to past mistakes, in order to promote this common goal.
The Abnormal Situation Management Consortium is one such group of companies that have banded together to develop creative solutions to some of manufacturing’s most vexing problems—abnormal plant incidents. A plant incident, caused when an event or combination of events deviates from normal behavior, can range from a minimal disruption to a catastrophe.
Kevin Harris, a marketing and technology director for Honeywell Industry Solutions, is the director of the ASM Consortium. “One of the difficulties in getting manufacturers to talk about abnormal situation management is it’s a very sensitive area,” says Harris. “Companies don’t like talking about having plant incidents and they don’t like talking about improvements because that implies they had a bad situation before.”
Yet the Consortium, which was started in 1994 by Honeywell, leading oil and chemical companies and other organizations with specialty expertise, has made significant inroads in the research and development of systems to manage abnormal situations. Harris notes that by collaborating, Consortium members can benchmark across different companies to determine best practices and root causes for incidents.
At first, says Harris, it was a bit awkward for companies who were traditional competitors to share information, until they became comfortable that what they were sharing was for the common good. “We have an understanding in the Consortium about what can be shared and what should remain proprietary.”
Best practices are also shared at industry user group meetings across the various divisions of London-based Invensys. Typically, Invensys will help coordinate these meetings, says Peter Martin, vice president and general manager, Performance Management, but the user group itself takes the lead in getting members to exchange information.
Sharing best practices, even among different operating teams within a given facility, can pay dividends, says Martin. “We did some work with a pharmaceutical company where sharing best practices for startups and shutdowns saved million to .5 million per year in one small section of a plant.”
In another example, cited by Martin, a petrochemical company was venting unused steam rather than shutting it off. By doing an energy analysis and stopping “bad behaviors,” the company saved millions.
So don’t be afraid to uncover bad behaviors, mistakes swept under the carpet, lost opportunities—even if you’re partially responsible. The price for doing nothing is too high. Work to develop an honest, open corporate culture in your company. You could look like a real superhero.
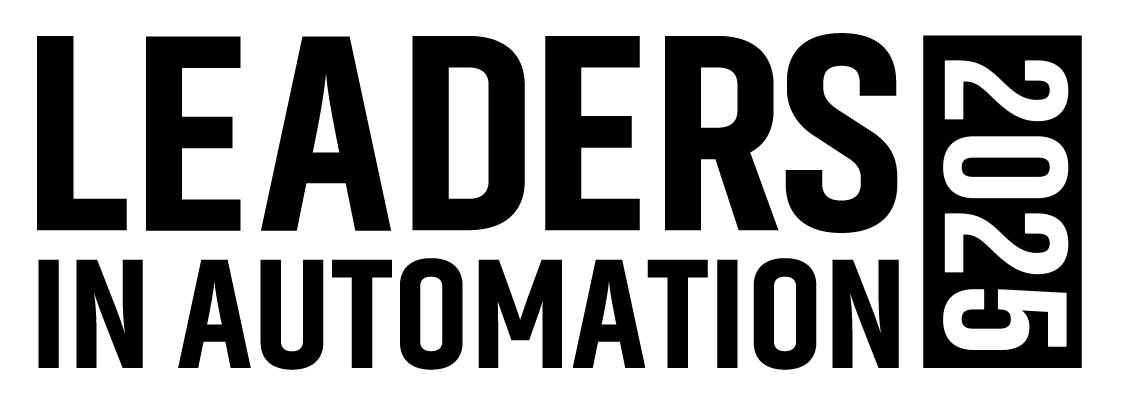
Leaders relevant to this article: