This is the second transcript of a three-part series on Automation Trends in Food Processing and Packaging. If you would prefer to watch the video of these discussions, choose link below:
· Robotics video (20 minutes)
· Remote Access video (20 minutes)
· vFAT (Virtual Factory Acceptance Test) video (13 minutes)
David Greenfield:
Another technology area that's seen a lot of increased attention because of COVID is remote access. And here we're talking about the ability to remotely access plant floor equipment, or specific devices and systems, either by in-house engineers, or operators, or even third parties such as OEMs and system integrators. And like cobots, this technology has been developing very quickly over the past several years now, but it's really seen an accelerated level of interest due to COVID in the past year.
Glen, you've been very focused on the trends around remote access between OEMs and food package goods manufacturers. How would you say things have been changing here in the past few years?
Glen Long:
It's near and dear to me because I come from that side of the business. And the technology to add remote access to equipment has been around for years. But the willingness on the two sides to allow that to happen has not really been there. So, all of a sudden enter COVID, and very quickly it becomes a necessity versus, say, whether the capability existed, or whether it was wanted or not. So, tremendous adoption in different types of remote access. And I think when you talk about remote access, you think about three different areas. Certainly, there's a service aspect of it, and I believe that's where a lot of the companies were first thinking to be able to access a machine remotely for the purpose of fault diagnostics, or program fault diagnostics, and so forth. But the other two elements that we see a lot now are training. We went with the OpX Leadership Network and our Industry Relations Committee on sort of a field trip to Emerson last year, and that was certainly something that they were a proponent of. And it's possible now to conduct training in a way that we've never been able to do it before through augmented reality and virtual reality. There are training elements that can be conducted with staff remotely that just were never possible before. So, I think that's a second element of remote access.
To learn more about OpX Remote Access, click here.
And I think the third one is predictive maintenance, and the ability now to get into a piece of equipment remotely to see what's happening with motors, and drives, and temperatures, and loads, and things like that, is just a tremendous leap forward. It's been around in other industries for some time, and there's a trickle-down effect. Certainly, the cost of the equipment has a lot to do with the ability, or the viability, of that kind of predictive technology. But remote access now has become a needed technology, and there are a couple of really interesting things that are going on. First of all, the OpX Leadership Network published a document on best practices for allowing that connectivity between the CPG and the OEM supplier. That's always been a roadblock. Again, that's coming down, but there a number of different ways that you can look to see how that can be done safely. And it's really up to a collaboration between the OEM and the CPG as to how they go about that.
The CPG can turn that on and turn that off as needed, but that's a big element of making it happen. We've also seen instances in the service realm where we're now, out of necessity, there are trained professionals on one side being able to walk less skilled employees of CPGs through very complex tasks. So, that not only saves money in terms of that service element, but there's that training element involved as well. And for the CPG in the time of need, as we've seen over the last nine months or so, that up time. Being able to keep that equipment up and running as necessary. So, there's tremendous benefit that we've seen in the short-term. There's been more progress in the last year with this kind of thing than there has been in the 10 years prior to this point. So, you're seeing an accelerated adoption, and tremendous benefit on both sides. It's beneficial to the OEM to be able to conserve that limited resource, and not spend so much time traveling back and forth between places.And for the CPG, there's cost savings, there's speed involved in fault diagnostics, and remediation. So, just tremendous benefits on both sides. I think all of those things are playing into what you see, and it's, again, trickle-down effect. A lot of the suppliers of this type of equipment are seeing this happen, and they're being pushed to adopt it more rapidly. So, you're seeing not only innovation, but adoption in this technology.
In September of 2020, PMMI's Business Intelligence group published a study on trends in the adoption of remote access. So, that's a great reference document to see some of the different things people are doing, and how it's being deployed because I think it's interesting to see the innovation, and the imagination, in some of the suppliers, and how that technology is being deployed.
To download the PMMI Business Intelligence, Trends in Adoption of Remote Access report, click here.
Bryan Griffen:
I think beyond just the great applications that Glen mentioned, which really justified the need and the cost for doing these technologies, we also have to look at how we do remote access to make sure that it's safe, it's secure, that we avoid cybersecurity issues. And OMAC, the Organization for Machine Automation and Control, is just now releasing a new best practice document on how to implement remote access technologies in factories. There are a few key subjects from the guide that merit some comment here. Perhaps the biggest component to a successful remote access solution is not necessarily the technology, but the people that are involved. One of the biggest things that we have seen over the years as we've tried to implement remote access is the conflict between IT and OT. IT is all about cybersecurity, and maintaining control of those networks, and they do a fantastic job of it. But OT is all about ‘we need to manufacture right now.’ We can't stop for doing a patch, for example, because stopping right now to do that patch means we throw away the batch, which could be hundreds of thousands of dollars of lost product.
So, there needs to be a point where those two factors come together and discuss what are the needs of both sides. Understand what each side of that equation needs in order to successfully implement remote access tools. Then once all of the players are on the right page, and communicating well, then they can turn to the task of developing the remote access solution, which type of remote access they want to use, assessing the current situation within the factory, and what the needs would be from a technology standpoint, and then getting everything to play well together. But it all starts really with that human aspect of the solution, not the technical one.
Tom Egan:
Yeah, and for me I'm going to take off from what Bryan said there for a little bit, still with that OMAC report, which I agree. I thought was very good. Some real success ideas for implementing remote access. I learned a new term there when that IT/OT piece, first time that I saw it in a report anyway, which was CIA and AIC. And Bryan, I hope I have this right. But the CIA element was that the IT group looks at confidentiality, integrity, and then availability, meaning the availability of whatever the resource is. Whereas the OT group looks at availability first. I just thought that that was an easy statement to look at and say, "They're looking at the same problem. They're looking at it through two different facets of the same problem. And so that's why until that discussion takes place, sometimes we have the conflict." So, I think that was a good takeaway on that piece.
For more information on OMAC, click here.
The other overarching part for me on the remote access, Dave, is that I just don't believe that there's an option. Glen alluded to the point that there's a benefit for both groups now. There always has been. Perhaps the pandemic has really pushed that to the fore because of the restrictions on travel, for example. But the benefit is that the cost of downtime is just too high. It's too high for the company that's trying to make a product to get into the marketplace to sell, and it's too high for an OEM that's trying to support the equipment and has to get a human resource to the location. So, if you're able to at least go in, and take a look at whatever the issue might be on a production line, or even to be monitoring that in the ultimate as a way of accessing, and utilizing beneficially that remote access, it's that understanding that just downtime is just too, too expensive now. What can we do to reduce that timeframe? Remote access is one approach that will absolutely work.
Glen Long:
Dave, I think we've always looked at this as the OEM and the CPG being the two sides of the remote access question, and I think for the CPG, in and of themselves, there's tremendous capability for being able to remotely access equipment in different facilities, or for supervisors that are in big plants that have the ability to be notified, even outside the plant, to be notified that something in the line is not functioning correctly, or it's not functioning at its optimum efficiency. I've been with CPG employees outside the plants on visits when they're notified via their cell phone that something in the line is dropping below a certain point. And they literally excuse themselves to be able to go, and get ahold of the plant, and address it. So, there's definitely that OEM and CPG connection. And it's that remote access part, but for the plants that have multiple lines and multiple facilities just within their own organizations there's tremendous capability and promise in the development in the machinery world for that data to be gathered and then output. So, remote access, I think, has two connotations. There's the outside connotation where you're talking about the OEM, and the CPG.
But then the inside connotation where it's being used within a big group. So, you're seeing tremendous appreciation for the ability to do it, and finding ways that it can be done safely, and just beginning to realize the benefit because there's a lot of data that's available there. And the question is now how do you gather it, and how do you use it properly?
David Greenfield:
Yeah, I think to both of your points what we've been talking about here in just the past couple of minutes about is those cultural issues, organizational issues, and bottom-line cost issues. And I can remember when I first started writing about remote access technologies several years ago now, that the big factor was the cost issues, the bottom-line benefits to end users who adopted this. But that didn't seem to be able to overcome the cultural and organizational issues that existed in these companies - and have for years for obvious reasons. But it's interesting that what's happened in the past year has forced industry's hand to rethink how things have to operate. And so, I think at this point they're starting to see those bottom-line benefits that have been talked about forever. They're being able to see - like not having the amount of downtime, or virtually no downtime, the reduced cost of travel, and having to send someone to these sites all the time, or to go physically check out these various facilities, or pieces of equipment that they don't have to travel there to do now.
I think all of that it that falls to the bottom line, and they see that it's kind of coming full circle back around again now that we've gotten over some of those cultural and organizational issues that have always existed. So, that's been an interesting development for sure.
Augmented RealityDavid Greenfield:
So, one other technology area associated with remote access that's seen a big boost in this past year has been augmented reality for preventative maintenance. And much of what I had seen in terms of application examples over the past few years had almost always been in the discreet manufacturing industries, but I've been seeing more and more references to it in food and beverage. For example, through Cisco's project with the dairy farmers of America that we covered recently. Are any of you hearing much about the use of augmented reality for preventative maintenance and/or training, as you mentioned Glen, with food and beverage, and CPG producers?
Read Cisco Aids Dairy Farmers of America’s Digital Transformation, click here.
Glen Long:
Yeah. There was an article in this month's ProFood World magazine about using it for training for sanitation, which is a very specialized thing. And through the use of augmented reality, and virtual reality technology, they were able to walk a lesser skilled worker through the very complex process of sanitizing a particular piece of equipment. So, surely that technology is out there. I think it's also very helpful for operators and maintenance people in food plants to be able to deploy that in terms of maintenance and repair, even without the OEM being involved. There's a tremendous amount of information from OEMs on simple things, like threading film, for example. I've seen it used for that when they have such turnover in the food plants with the operators for the equipment. Even what you would consider relatively simple tasks are difficult because the training isn't there to pass that knowledge from worker to worker. And then with the turnover, this technology allows even a lower skilled worker the ability to walk through a step-by-step process, and get that job, or that task accomplished. So, for sure it's becoming more widely available as the price drops, and the technologies advance.
Tom Egan:
And Dave, the article that you reference about Cisco I was reading for the first time, and I really liked what Cisco was looking at, which is they have a technology, and there is a need. How do they partner with organizations to do that? I thought the use where Cisco said, "We're going to give you, or provide at a very reduced cost, a full suite of tools, so that the workers, the managers, and the corporate can really understand just what's happening with those.” Excellent example. It involved all parts of the organization. The individuals that are down on the plant floor are getting information to help them do their job. The managers are then getting information from what the workforce is doing in terms of handling any issues, or doing a solution, as Glen mentioned, about the sanitation work. They're understanding what can improve that particular project from the workforce. And then on a corporate basis, just being able to manage overall. I thought it was a great example where a whole suite of tools was brought in.
Read Will AR Change the Game for Packaging Operations? Click here.
Bryan Griffen:
I think one of the other interesting things that we're seeing as a use of these sorts of augmented reality and remote access being combined, is where we can take a technician who is the premier technician on a particular piece of equipment, but maybe tied up at somebody else's site. And we can send another technician to the site that's in question, and that technician can connect remotely with the premier technician, and get online, real time assistance for solving whatever the problem is. And so effectively you've turned your standard technicians all into the same level and quality as your premier technicians by having that connectivity.
Looking for reports mentioned in this discussion?
To learn more about OpX Remote Access, click here.
To download the PMMI Business Intelligence, Trends in Adoption of Remote Access report, click here.
For more information on OMAC, click here.
Read Cisco Aids Dairy Farmers of America’s Digital Transformation, click here.
Read Will AR Change the Game for Packaging Operations? Click here.
Want to read the first transcript on robotics? Click here.
Interested in learning more about predictive maintenance? Download this free PMMI Business Intelligence white paper below:
Sponsored Recommendations
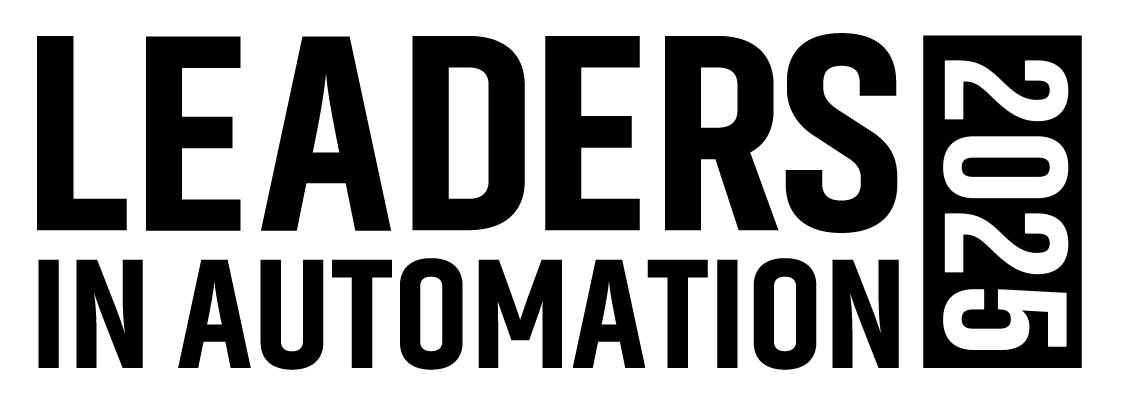
Leaders relevant to this article: