Beckhoff’s PC-based Control Helps Scale Electrochemical Machining
Daniel Herrington was working for the U.S. Department of Energy’s Advanced Research Projects Agency–Energy (ARPA–E) when he realized the importance of manufacturing.
“Manufacturing underpins most major advances in technology, whether it’s in the energy industry, medical device or aerospace,” said Herrington, now the CEO of Voxel Innovations, a supplier of high-volume pulsed electrochemical machining (PECM). “I realized I wanted to work in manufacturing and I saw that electrochemical machining had significant untapped potential, especially in the U.S. So, a vision formed to build a company based around electrochemical machining and an automation platform that would solve the biggest problems faced by our customers.”
By refining the science, developing proprietary IP and building upon a scalable automation platform, Voxel has become a leader in PECM. Founded in 2015 in Raleigh, N.C., the company offers contract manufacturing using machinery developed in-house to support aerospace, medical device, energy and other industries that need highly engineered, metallic components in large quantities.
Voxel’s equipment can be customized to match customers’ needs, such as working with specific metals while providing enhanced traceability. To continue its growth trajectory, Voxel needed to implement a more sophisticated automation platform that could scale. The company selected Beckhoff’s technologies, a decision which led them to Robert Belk, Jr., P.E., owner and automation consultant at Palmetto Mechatronics in Greenville, S.C. Working together, the teams at Voxel, Palmetto and Beckhoff developed an automated production line with robotics and inspection capabilities.
“We had a vision for how the line would work, but Robert helped us understand how all the components could talk together and capture the data we need,” Herrington said. “Before that, our automation systems were built in-house. But going into this next phase of growth, we wanted to build around a single architecture and industrial control platform.”
Engineering ingenuity
One of Herrington’s first hires at Voxel was electrochemist Dr. Omar Yepez, who previously worked to protect offshore equipment against rust. Herrington wanted Yepez to do the opposite for Voxel. After all, that’s what PECM is about—very fast, highly targeted corrosion that shapes intricate, high-quality geometries atom by atom.
“The PECM process is non-contact and non-thermal, so it can create thin-wall geometries with intricate features without deforming the part,” Herrington said. “Our electrochemical machining technologies involve complex fluid dynamics, multi-physics, chemical reactions, heat transfer and a variety of other aspects. But they can produce parts that traditional manufacturing processes can’t handle as economically or, many times, couldn’t make at all.”
The automated line at Voxel moves this rapid corrosion process into high-volume production. First, it sorts parts into a uniform infeed. Then a SCARA robot loads them onto a tray. A gantry moves the tray through pretreatment baths.
Next, an articulated robot grabs multiple workpieces and inserts them into the PECM cell. Inside, the tooling lowers into place, and an electrolyte solution fills the gap between the tool and the part. By applying the correct voltage potential, the system dissolves metal through electrolysis. Simultaneously, the electrolytic fluid acts as a flushing agent that removes waste material and any residual heat.
Afterward, the robot unloads the machined parts onto a separate tray. A second gantry then takes them through post-treatment baths and a drying chamber. Finally, another SCARA unloads the trays, while routing several parts to an inspection station with Micro Epsilon optical gauges.
The operation requires fast cycle times and synchronization between different processes. The process also requires the equipment to interface with databases, connect to other web-based platforms to extract data and be integrated with third-party devices.
Critical software aspects
Belk worked with Voxel controls engineer Kevin Judd to program the machine using TwinCAT 3 automation software, which enables engineers to program in whichever language best suits their skillsets and the needs of the application. This includes the IEC 61131-3 standards with their object-oriented extensions, preloaded or custom function blocks, or computer science standards integrated into Microsoft Visual Studio. Belk relied on Structured Text, along with C# for HMI customization.
Beyond standard PLC functionality and running PID loops for process sensors, several other TwinCAT functions proved crucial for the application, including:
- ADS communication between the machine logic and a custom Windows .Net application for interfacing with the optical measurement device and HMI.
- PTP motion control library to drive ball screw actuators with 13 Beckhoff AM8100 servomotors, which raise and lower the PECM tooling.
- TF6420 database connectivity for high-speed connection to a custom database for work-in-progress control and overall equipment effectiveness statistics.
“This system requires real-time interaction with an MS-SQL database. Each part is assigned a virtual serial number when placed into the first tray and that is updated throughout each step of the process,” Belk said. “The part data is very important for determining machine tool wear or damage and optimizing the machining process. The Beckhoff database client software enables fast execution of stored procedures from within the TwinCAT control software.”
Precision hardware
The automated PECM production line at Voxel uses a CX2042 embedded PC with many-core Intel Xeon processors running TwinCAT as the sole machine controller. A CX2042 with directly connected I/O terminals communicates with the three robots, optical gauges, MS-SQL database and hosts the HMI program.
“One of the things that has driven me toward Beckhoff industrial PCs (IPCs) over the years is the CPUs’ speed and architecture. Plus, you can assign processor cores to specific tasks, whether they’re on the automation side or involve regular PC functionality,” Belk said. “Beyond that, the IPCs offer significant space and cost savings because one piece of hardware can handle everything on the machine.”
On the networking side, the EtherCAT industrial Ethernet system provides real-time communication and a flexible topology. The automated PECM production line uses a range of EL series EtherCAT I/O terminals from Beckhoff to communicate across the system. EL terminals installed on the articulated robot control the end-of-arm tooling with valves and sensors for 24 sets of grippers. Also, EL7211 servomotor terminals provided space-saving 48V dc amplifiers for the AM8100 servomotors.
Along with EtherCAT, Safety over EtherCAT (FSoE) helped streamline implementation. FSoE uses a “black channel” approach to communicate machine safety data over the standard EtherCAT network. Belk leveraged TwinSAFE hardware as well as FSoE capabilities built into the equipment’s KUKA robots, which offer native support for EtherCAT.
“KUKA robots use EtherCAT as a primary communication technology, and TwinCAT simplifies mapping data between the robot and the embedded PC,” explained Belk. “So integration of the three robots into the overall control system and safety network proved to be quick and efficient.”
High-volume PECM
After a year of development time, the automated PECM production line went live in June 2023, and can produce roughly four million parts a year. With this new system, Voxel has hit the performance benchmarks and part-level traceability set in the design phase. The system offers complete visibility into production aspects such as quality control and pH levels while providing traceability to comply with standards like AS9100 in aerospace and ISO 13485 in medical device manufacturing. It can pause production and alert the operator if anything falls out of tolerance.
“Compared to our previous approach, the difference is night and day. The main advantage is we brought all our controls under one roof,” Herrington said. As PECM is capable of processing multiple parts in parallel with a single tooling system, its high-volume capabilities can increase even further with Beckhoff’s automation technology.
Voxel is developing two more production lines, which will include high-end motion control and six-axis robotics. A key strategy in the first implementation was to ensure the company’s engineers learned the technology, working with Belk, to keep that knowledge in-house. Having adequate support was also critical. Herrington appreciated not only Beckhoff’s no-cost technical support, but also assistance from the local applications engineers.
“Whether it’s a part for a jet engine, an implantable medical device or a heat exchanger for an energy application, our vision is to offer customers differentiated technologies that help them optimize performance and cost metrics,” Herrington said. “Then we want to support them all the way through that process and throughout the product life cycle. Our model is to be that trusted engineering development and volume manufacturing partner.”
And the demand is clearly there: The company continues to run production around the clock in three shifts to keep up with orders.
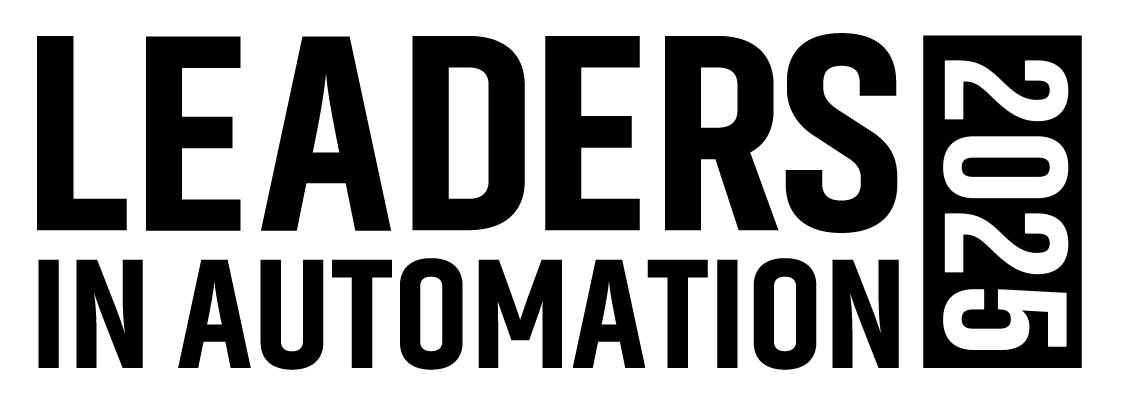
Leaders relevant to this article: