Whether it’s called universal I/O, flexible I/O, intelligent I/O, configurable I/O, electronic marshalling, etc., the use of smart I/O enables more flexibility for I/O changes—an increasingly common occurrence as industry shifts to more customized and manufacturing-on-demand production processes. A major driver behind the push for universal I/O comes from large corporations, like ExxonMobil, looking to ease the commissioning process and enable changes to a control system.
Though the benefits of universal I/O are clear for large companies, smaller companies and OEMs can benefit as well. However, users should be aware that, despite the broad advantages of universal I/O, there are still some use cases where traditional I/O remains effective.
How universal I/O stacks up
Input/output devices handle the bi-directional connection between the controller and the devices or systems being controlled. There are two types of I/O: analog, which is an electrical signal representing things like temperature level or rate of flow; and digital, which uses signals that represent two states, such as on and off or start and stop.With a traditional, analog I/O system, a lot of upfront work is required to specify the right field I/O module, electrical panels, installation, power, distribution, and networking. Because the I/O system is typically associated with a central controller, extensive programming is required to get these systems to communicate effectively with each other.
This is the initial instance where universal I/O can offer benefits. With this kind of I/O, machine builders can drop an I/O module in place and then plug it into a network cable. By removing all the upfront programming requirements, universal I/O simplifies machine design and system building while also delivering data processing and network connectivity options not commonly associated with traditional I/O.
Providing an example of how universal I/O can streamline machine and system building processes, Josh Eastburn, director of technical marketing at Opto 22, says, “If your control systems, process, or manufacturing engineers are still [in the process of] developing the equipment, they may not know how many of a particular type of signal is needed. As a result, they often have to do a bunch of change orders on the backend, revising the I/O design to meet the different signal needs once the design is complete. Or they can drop in flexible or universal I/O, which will allow them to reconfigure it in the field without changing the electrical design, panel, or enclosure. It simplifies a lot of the design process and reduces the project budget. Down the line, universal I/O also translates into easier maintenance.”
Data demand
Behind the demand for universal I/O is a push for more data to help predict machine failure and other critical maintenance timelines.“Beckhoff started offering I/O products in the 1980s, and this [universal I/O] segment has been growing consistently by 10% every year,” says Sree Swarna Gutta, North American I/O product manager at Beckhoff Automation. “That shows you the acceptance within the industry and how happy users are with flexible I/O. One of the things they demand out of flexible I/O is the ability to incorporate more diagnostics and information the OEM and customer could use to improve their designs and performance of the machine.”
Whereas a standard I/O device may only receive process data and signal communication from a sensor within a machine, flexible or universal I/O can provide insight into other information about the environment that the sensor lives in. This capability holds a lot of untapped potential when it comes to predictive maintenance, according to Shishir Rege, technical sales specialist, IIoT (Industrial Internet of Things) at Balluff Inc.
“For example, if something knocked the sensor out of alignment, there is no way for the sensor to tell that to a standard I/O device,” Rege says. “So how does the sensor communicate that information to the machine so that the machine can affirm it? The universal I/O unleashes that sensor or device to provide a lot more diagnostics, not only about itself, but about the environment they live in. So that is much richer communication.”Globalization and retrofitting benefits
As machine builders increasingly develop equipment for use in different countries, they encounter different standards and protocols in every region. According to Belden, universal I/O can work with many different PLC environments and fieldbus protocols, such as Profinet or EtherNet/IP, making it easier to sell equipment into global markets while reducing product variants and the need to replace I/O modules to meet protocol-specific requirements.“When you choose a flexible I/O, machine builders can actually leave that technology as is. They don’t have to re-design anything when they are selling globally,” Gutta says. “While Beckhoff created and specializes in EtherCAT, our I/O supports more than 25 communication protocols. Universal I/O offers the flexibility of being able to connect to any network and it can be used anywhere in the world.”
Aside from allowing machine builders to sell globally with less complexity, universal I/O is also touted as being able to work with both new and legacy equipment. Machine builders can retrofit existing machinery with customizable modules that can include as many inputs and outputs as needed—rather than being confined to the eight inputs and outputs common in traditional I/O devices.
One flexible I/O innovation that has gained a lot of attention over the past decade is IO-Link, a standardized I/O technology for communication with industrial sensors and actuators. Popular in Europe and now making its way to the U.S. and Asia, IO-Link is a unified point-to-point device level communication method that features built-in diagnostics and is reportedly easy to implement. IO-Link is vendor-independent, which is why it is possible to combine IO-Link masters and IO-Link devices from different manufacturers and integrate these products into the same network.
During an interview for an “Automation World Gets Your Questions Answered” podcast episode about IO-Link, Rege described IO-Link as being like a USB for industrial automation in that it is independent of control level networks and protocols. “All you need is a gateway or a bridge module that connects the protocols together. And that’s what we call an IO-Link gateway or IO-Link master, that communicates on the fieldbus level, as well as collects data from the IO-Link devices.”
Belden’s product manager Svenja Litz adds, “Because an Ethernet interface will not fit—regarding size and costs—into the smallest devices like photoelectric sensors, IO-Link is the perfect communication protocol to make simple sensors smart. It enables them to transmit a set of different parameters. This is how a simple sensor can transmit something like temperature information in addition to its standard switching signal by using IO-Link communication.”
The plug-and-play compatibility of universal I/O is equally appealing to end users. As manufacturers combine different machines from a variety of machine builders, there are a variety of interfaces on each of the machines with different cable lengths, which leaves the end user responsible for maintaining inventory of all the different cables in different sizes and with different interfaces. However, if all of the devices and machines are outfitted with universal I/O, only one standard cable is needed to connect to all the devices.
“Whether it’s a digital device, a smart sensor, RFID, or even a valve manifold—it can be brought onto the same standard interface,” Rege says.
Possible drawbacks
Though universal I/O is gaining adherents through its clear connectivity benefits, the technology does come with its own set of tradeoffs.One of these issues is speed. Because universal I/O is a form of data communication, compared to traditional I/O which is signal communication, users and OEMs may run into networking speed issues.
“Signal communication is always going to be faster than data,” Rege says. “If the sensor is communicating in signal, it’s going to reach the controller faster versus if the sensor is communicating data, which is slower because it’s using more bandwidth on the network.”
According to Rege, 95% of industrial automation applications fit well with the universal I/O platform because they can tolerate latencies of 10 to 15 milliseconds. However, if the requirement for latency is less than five milliseconds, Rege says he would not recommend universal I/O.
Opto 22’s Eastburn also doesn’t recommend the universal I/O approach for every application.
“Typically, where we’re seeing adoption [of universal I/O] is in IoT applications where we need to scale a system fast,” Eastburn says. “If you can spend a little bit more on the I/O to save on the front-end design and installation work and then just repeat it over and over for other machines, it can translate into a project savings and make it easier to scale your system. But if you’re wanting to save and get a cheaper I/O, it’s easy to beat out universal I/O in terms of per point/channel price. So, it really depends on what the application is and whether it makes sense from the perspective of total project cost or long-term TCO (total cost of ownership).”
Traditional I/O may also offer a wider range of signal and power options, which would benefit applications that need channel-to-channel isolation or high-frequency counting, for example. That’s why “there’s definitely still a need for traditional I/O,” Eastburn says.
Universal I/O’s role in IoT
The essence of IoT is data, Rege says. And not only does universal I/O provide more opportunities for builders and users to harness the power of data, it also brings more flexibility to machine design and compatibility.“Having this data communication at the sensor level enables a lot more IoT-ready applications to be developed,” Rege says.
One of those applications, according to Rege, is process condition monitoring, which helps users and OEMs enable pattern-based artificial intelligence, allowing for more predictive maintenance.
“All this information and data used to be very expensive to collect,” Rege says. “Now, it’s easily available with universal I/O products like IO-Link. Universal I/O allows integrating different types of interfaces like RFID, barcode reading, or vision, [so that] you can collect and utilize that to create new types of applications, especially in packaging where they run a lot of small batch production.”
And as cybersecurity concerns continue to grow, universal I/O may also be the key to protecting legacy equipment and older control systems, as many universal I/O products have embedded security features, Eastburn says.
“One reason you might need to connect your universal I/O in parallel with an existing control system is because that system doesn’t offer any cybersecurity protection,” Eastburn says. “In that case, it would be a bad idea to take a PLC and connect it directly to your business. But if your universal I/O has security embedded, you can wire those I/O signals and send encrypted data.”
“The real key here is the long-term scalability,” Eastburn says. “By bringing down the cost and making it easier to get connected and maintain the system over time, you don’t have to do a little project every time you bring in a new device or new I/O points. This means that we can scale up systems much larger than we have typically done while having it more tightly integrated with the rest of the organization.”
Companies in this Article
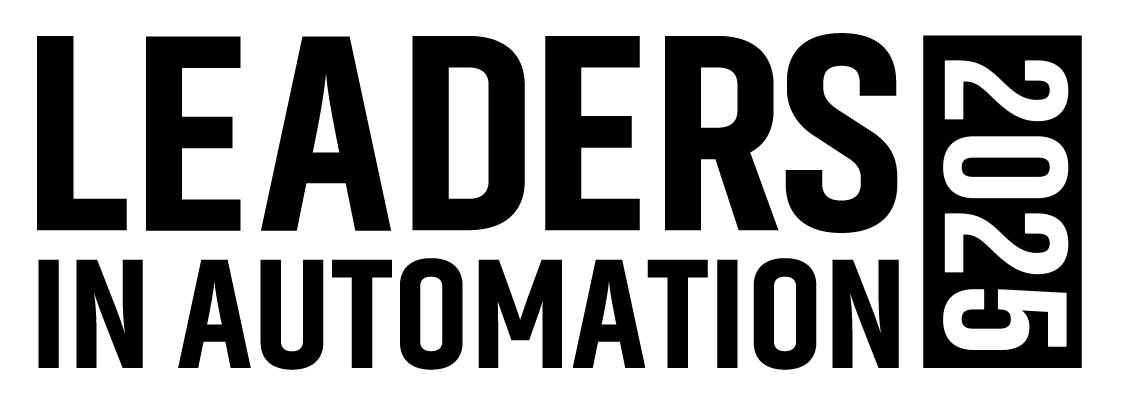
Leaders relevant to this article: