How Does a Digital Twin Work in Practice?
Read the full transcript below
David Greenfield: Welcome to the Automation World Gets Your Questions Answered podcast, where we connect with industry experts to get the answers you need about industrial automation technologies. And you can find even more answers by subscribing to automation world at Subscribe AutomationWorld.com
I'm David Greenfield, Director of Content for Automation World. And the question we'll be answering in this episode is how does a digital twin work in practice? And joining me to answer this question is Dan Riley of Interstates an industrial automation system integrator. So thanks for joining me today, Dan.
Dan Riley: Yeah, pleasure to be here. Thank you.
David Greenfield: So to get right into it, the digital twin concept can be applied to a wide range of industrial technologies from specific devices and pieces of equipment to entire plant floor operations. So can you explain the digital twin concept in general and how it can be so widely applied?
Dan Riley: Yeah. So, you know, really generally speaking, a digital twin is a digital representation of a physical object or process. That's a pretty widely used definition. And in that definition, there are a lot of forms it can take and your question and was right to phrase so widely applied. So you know, its most basic level, a digital twin can be a pretty comprehensive operational dashboard. But there are also a lot of use cases and unique applications that digital twin can take. Something that most manufacturers have in their plants, an HMI is a digital twin, it is the digital representation of their process. That would be considered more of a performance ops use case. Some more specialty ones can include r&d, physics, conditions, testing, that's a more engineering minded digital twin that could be you know, OEMs use that or process engineering firms to test you know, physics, you know, temperature controls, flow rates, things like that. Other applications are AR VR remote operations, AR VR employee training, building information modeling, like BIM that would be a construction based digital twin control system simulation. And then process like I said, process and an asset dashboards. Those can include OEE, alarms, process trends, your maintenance logs, and PID performance. And anything else in there that is critical to the top two, to monitoring the operational performance of your plant or asset.
David Greenfield: Okay, thanks for explaining that. And it sounds like from the way you in your description there that is, much as the digital twin has mostly focused on manufacturing applications. It's even moving into applications outside of that, like in building infrastructure management, is that correct? That it's even moving beyond the industrial manufacturing realm?
Dan Riley: Yeah, yeah, absolutely. So interstates has a couple of different business units within it. And we have an engineering side. It's really ideological engineering, power engineering, but also construction, electrical construction, and we do employ BIM modeling in our designs when we're doing design work for customers. So we can build digital representations of those plants or the areas of the plant so the power distribution areas that make it easier to model and design. We also in our in our controls area, when we're doing user acceptance training or testing or other things, we do have control system simulation. So we have the the plant up and running the simulated plant so we can see what you know batches of processes are going to be impacted. And so when our clients are going through acceptance testing, they can they can see the physical layout as it would be an HMI.
David Greenfield: Okay, so given its broad applicability in the detail that it provides, how difficult is it would you say to apply digital twin technology at both the equipment specific level and at a plant wide, broader level?
Dan Riley: Sure, well, you're going to hear this from me a lot in this conversation, but it depends on the use case and depends where you're starting from, but from deployment say, you know, you're ready to execute a project of a digital twin. You're going to need to have your basics mastered before you can really start that and that means you need to really have a solid plant network, your brain process data on all your assets that you want to have digitized, digitized, alarming events, tables, your mes database men and your maintenance databases all accessible. So you really need to have a pretty mature model of your data ready, and as clean as possible. And then depending on the complexity, depending on the use case, you'll want to have plant Wi Fi, that is if you want to deploy headsets, to operators or maintenance personnel. You know, if you want your digital twin to adjust control parameters, then you're going to need to have some right back capabilities to your PLC, which means you need to have some access in your your network and platform that allows right back. So it's not an entry level digitization use case it is on the you know industry 4.0 or digitization spectrum, it is an advanced use case, you need to have a plan in place really, in data champions at key layers organization to get the most value out of a digital twin. So there are a lot of things you need to have ready and accessible to execute.
David Greenfield: Okay, understood, it sounds like from your answer. They're like the probably the biggest hurdle and it would make most sense for this is having your data ready for use in a digital twin application? Are they given that are there any specific steps or processes that manufacturers should be looking to take first to make sure that data, he was ready for that if they're looking to adopt digital twin sometime in the near term about things they could be doing with their data today to process they could be instantiating, etc, to get things ready for that eventual use of a digital twin?
Dan Riley: Yeah, so most analytics use cases are gonna fall between befall before a digital twin on the spectrum of complexity. So there are, you know, low hanging fruit use cases that you can deploy in your site that will, you know, make you ready step by step for digital twins. And they're in no particular order, you know, they can be, you know, deploying process historian across your facility where you're, you know, trending, all your process variables are the ones that are most important to you, oh, he on your key assets, making sure that your digital or your maintenance system is digitized and is accessible, you know, through some sort of relational database, and alarms and events in the same way. So there are little things that you can do in between zero in digital twin to get you ready. And so as long as you're making those little steps and improvements, then you will eventually work your way, you know, to that readiness for digital twins.
David Greenfield: Okay, thanks for clarifying that, then. So yeah, you mentioned that the the digital twin is clearly not an entry level of technology of you know, it's definitely a more advanced application of industry 4.0. What about the cost related to digital twin technology that's out there? You know, how does the cost of this range from, you know, for applications on specific pieces of equipment or for plant wide applications? Or is it a fixed cost? Can you explain a little more about that?
Dan Riley: Yeah, you're gonna have likely two groups of cost, you're going to have the platform cost that's going to enable you to do the digital twin and again, depends on what level of digital twin you want to do, if you want to have AR VR capabilities, likely that platform is going to be more expensive than those who are going to provide you comprehensive dashboarding. So there's quite a spectrum of costs, that need to be considered based on the type of use case you want to solve for. Also, you know, to factors that lead into the deployment costs would be the experience of the integrator or team deploying that in the race and readiness of your systems. You can save by making that investment that you know, previously in getting your data ready and, and having it well understood across your your facility or your your company. I think that more or less covers it I know I didn't give you like you can expect between, you know, this number and this number. But there were a variety of providers in the space, you know, GE, Rockwell, Yokogawa and others have established digital twin platforms. And again, if you want a comprehensive operational dashboard, then there are even more players in that space that can you know, visualize and trend that data out in those costs, range wildly.
David Greenfield: So given that there's such a wide range of costs on this, looking at it, you know, depending on the application looking at it in general, would you say the digital twin? is more of a tool more for larger manufacturers because of the cost ramifications? Or is it something that can be within the reach of mid tier or smaller manufacturers as well?
Dan Riley: Yeah, so we work with some larger manufacturers, and then plenty of mid tier manufacturers as well. And we see the readiness on both sides, both players, probably the larger manufacturers are going to be able to absorb the I don't know if it's capital costs, or operational costs, depending how they pay for the licensing, but invest more into some of the more advanced digital twin use cases, for example, setting up AR VR capabilities to train employees. That's, that's an emerging use case right now. That takes a lot of time, effort and dedication. And I think you're likely to see that more in your larger manufacturers. Whereas your more mid tier manufacturers, that comprehensive dashboard, maybe a remote operations, if they have a couple of plants would be a good use case.
David Greenfield: So getting to the reader question about how does the digital twin actually work in practice? What kind of information and specific value does the digital twin provide to a user in the manufacturing or processing industries? And how can it be applied then to improve production operations in those different verticals.
Dan Riley: So information, that type of information requires really all the ones I've listed before, so it'd be OEE, alarms and events, process trends, your maintenance logs, and any other special performance measures you want to do in your control system, like PID loop performance is, is an interesting one that we pay attention to. So those are the types of data you want to have accessible. And those will largely give you a variety of use cases. We primarily deal with batch and processing industries. So I'll can speak a little bit more to those then discrete manufacturing, but the value or the direct applicability it can provide. I mentioned remote monitoring of live assets. So right now we're experiencing in the industry, this thing called the talent war, or, you know, a severe lack of experience operational talent, that may mean that your plant will need to centralize some of its more experienced users. And having that process data, your alarms and events and your maintenance information available will allow maybe you to have a central operation center where your experience people can sit and guide your maybe more junior or your process engineers to go out perform or diagnose issues. So that's one example of how a digital twin can enable, you know, value in the processing industry.
David Greenfield: That's interesting that you mentioned the workforce issues around that that's something that I haven't heard yet and all the various discussions of digital twin, of course, I've heard it in training instances, as you've referenced earlier in the conversation, but not quite so specifically, as you know, a workforce management or you know, process tool around that it's mostly been, you know, giving specific information from, you know, pieces of equipment or segments of equipment across the plant floor. Are you seeing that more in terms of the digital twin being the looked at is a possible solution or way to better handle the workforce management issues that are facing industry?
Dan Riley: Yeah, we are we are seeing a lot of interesting companies preparing and scaling industry 4.0 use cases digital twin being an example of that, for instance, a couple of our clients are there, one of the main goals and some of the larger projects are lights out or paperless facilities. So, you know, some of these process facilities are in rural areas where hiring is difficult. And they the goal is to run their facilities off of an iPad or some sort of tablet. And that might mean that the majority of their eyes on glass is sitting somewhere that's not in the facility. And so getting that real time data Available to operations digitizing digitizing the manual collected data, migrating data from on prem to cloud. You know, predictive maintenance, enhance automation is all really important. And digital twins are certainly a way for us to get that digitized and get that in the hands of those who need it. We're, we're doing, we've done some pilots on, you know, AR VR capabilities and testing different headsets for those lights out or paperless facilities.
David Greenfield: Okay, so looking beyond that specific type of application, you know, based on your work as a system integrator with numerous different types of production companies, as you mentioned, mostly in the processing industry verticals, are you seeing much interest among your clients for the digital twin technology in general?
Dan Riley: We're seeing interest in some of its functions, I wouldn't say we're getting called out specifically for digital twins. But you know, industry 4.0 is a sea of acronyms and the sea of different terms. So we are seeing clients really have interest in some of the advanced capabilities, that industry 4.0 is promising. And, you know, either we're helping them run pilots or their internal r&d teams are working on those capabilities. So certainly, to be competitive in the next five years, having a plan in place to digitize your, your operations to have that supervisory layer of not control, necessarily, but observation is going to be important.
David Greenfield: And when again, based on your experience working with end users and industry, are there certain segments of industries that you work with that seem to be had more interest in using the digital twin? And if so how are they using it?
Dan Riley: I would say really, right now, the leaders in the space, are your larger companies who have the teams in place that are driving that innovation internally, and then also looking for partners externally. So there are the brands that you know, most everyone would expect to to do that. Yeah, we are not yet seeing that dripped down into maybe the mid tier manufacturers in terms of the level of complexity, but the mid tier manufacturers are looking at their own ways to digitize.
David Greenfield: Can you explain that? And how some of the mid tier ones are looking to digitize? Is it? Would that involve the digital twin? Or is it other aspects that are not quite so associated with that?
Dan Riley: Yeah, not quite associated with that yet. It's really just getting their data collection and network in order to support digitization in the future. They may be looking to do install base evaluations, electrical obsolescence, observations, especially in the supply chain issue is the understanding their control platform and their electrical obsolescence risk. They are also looking at condition monitoring, maybe some of your predictive maintenance. Use cases. And in a way those can those can start to look like digital twins, really just your digital representations of an asset. Understanding when failure might occur, what current condition is that in real time?
David Greenfield: Okay, so we've covered a lot of ground here in our discussion, Dan, and I appreciate all of your insights. So to wrap up, you know, are there any final thoughts or things we didn't discuss about digital twin technology that our listeners across industry should be aware of?
Dan Riley: Yeah, there are a lot of new technology players entering the manufacturing analytics industry 4.0 space, I would encourage your listeners to do the due diligence on all of them or as much of them as you can before you make a purchase decision. That's not to say any one is better or worse than the next. But each have a unique set of features that may or may not be the best work best work for you or the client. So reviewing those sources like automation, world gardener, ERC are a good way to get to know the players in the space and understand their capabilities.
David Greenfield: All right, well, thank you for joining me for this podcast Dan. And thanks of course to all our listeners and please keep watching this space for more installments of Automation World Gets Your Questions Answered. And remember that you can find us online at AutomationWorld.com. And subscribe to our print magazine at SubscribeAW.com to stay on top of the latest industrial automation technology insights, trends, and news.
Companies in this Article
Latest In IIoT
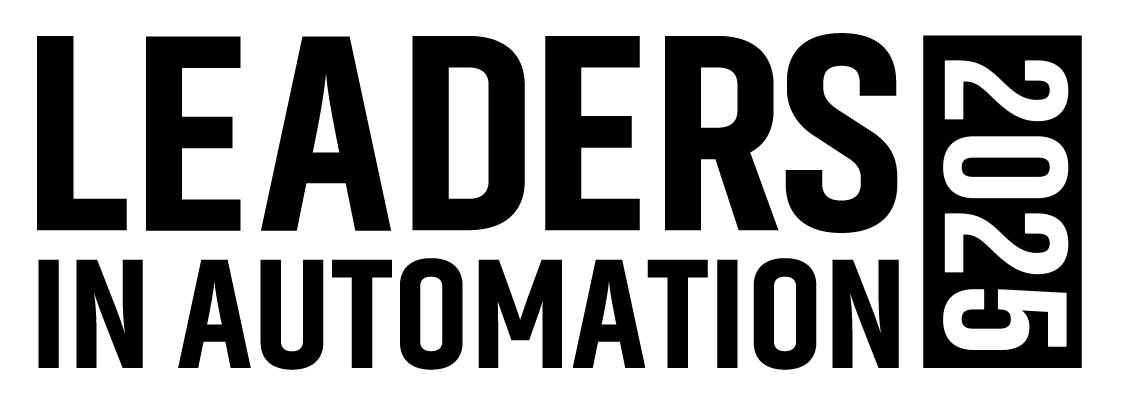
Leaders relevant to this content: