Robots that operate independently, blockaded behind light curtains and other barriers, may soon give way to collaborative robots that work interactively with humans. Design teams that are beginning to employ sensors and software to help robots work closely with people are striving to handle heavy payloads while working in close proximity with people.
These robots have emerged fairly quickly, driven in large part by new standards. The International Organization for Standardization’s committee for Industrial Robot Safety provided guidelines for safe deployment of collaborative robot operations in Specification TS 15066. It leveraged work in ANSI/RIA R15.06-2012, which sparked interest from both manufacturers and users.
“The standards group recently approved wording describing these types of robots,” says Marty Linn, principal engineer, robotics, at General Motors’ ME Vehicle Systems. “We’re very interested in these types of devices. We’re looking at ways they can help in production by improving quality and efficiency.”
Industry groups feel that collaborative robots could open up a large new market as smaller companies use them to improve worker efficiency. That’s partially because these robots don’t require complex programming, since operators can adjust them to meet personal requirements.
Trade groups say the new machine category is getting plenty of attention. “The field of collaborative robots is currently the hottest area of interest within the robotics industry, and with good reason,” says Jeff Burnstein, president of the Association for Advancing Automation (A3). “The notion that humans can now work safely, side by side with a robot employee, is both intriguing and groundbreaking.”
The standards set multiple classifications for these robots, focusing on different ways to sense humans and slow down or stop when danger is sensed. At present, universities and standards groups are working to determine how to differentiate between a harmless nudge and contact that could cause injury. That’s a difficult task, since one person’s harmless tap may be another’s painful collision. That determination also varies depending on the part of the body that’s being hit.
Just as there are many definitions for pain and injury, many interpretations are being used to define collaborative robots. Some companies are already shipping equipment that works closely with humans. ABB unveiled its YuMi line in April, calling it “the world’s first truly collaborative robot.” Autonomous vehicle suppliers contend their mobile units are collaborative. Some suppliers contend that it’s the usage environment, not the robot, that defines the segment.
“There are no collaborative robots; it’s the application that’s collaborative,” says Erik Nieves, technology director at Yaskawa America’s Motoman Robotics Division. “A robot itself can’t be collaborative. Everything is predicated on the use case.”
Technology and demographics both play a role in the emergence of these interactive environments. Advanced electronics make it easier and less costly to develop robots that can better sense their environment and stop when injuries appear imminent. At the same time, the need for technically skilled employees is becoming more acute, so it’s important to improve efficiency of these workers.
“The rapid rise of smart electronics has increased the demand for highly skilled production workers capable of consistent precision,” says Per Vegard Nerseth, global head of the Robotics Business Unit at ABB. “With this shift in skill levels comes an increase in labor concerns: labor pool limitations, the workforce management costs, compensation and retention. In many countries, the Baby Boomer effect is changing the demographic. Several large auto OEMs, for example Mercedes, have said that in 10 years’ time, 50 percent of their staff will be more than 50 years old.”
Power and safety
The easiest way to create a collaborative robot is to ensure that movements are so slow and gentle that they couldn’t hurt a person or damage equipment. Though that might work in medical environments and other fields where heavy payloads are measured in grams, it’s not a viable solution in most industrial applications.
“That approach does not advance the use of automation in industrial, warehouse or construction applications where heavy machinery is required and robotics can create a real economic impact,” says Daniel Theobald, CTO at Vecna. “To enable industrial robots to operate in close proximity and in cooperation with humans, they need several layers of sensing, planning and motion control.”
Robot design teams are employing a range of techniques to ensure that more powerful robots don’t cause problems. Advanced cameras, sensors and algorithms can be combined with old-fashioned cushions to minimize the potential for injuries.
“Its design is based on the integration of motion control software, speed-limited hardware, reduced weight, a compact frame and 14-axis agility,” Nerseth says, speaking of ABB’s YuMi. “The lightweight, padded, magnesium arms can cease operation in milliseconds if necessary, and cameras embedded in the hands monitor the immediate environment.”
University researchers are working to determine what limits should be used to guarantee that robots won’t hurt people. One challenge is that hitting a human in the head is much more dangerous than hitting a person’s legs. While several robot developers are racing to catch the wave of interest in collaborative robots, some product designers note that elements such as end effectors must be considered to ensure safety.
“Regardless of the robot’s capabilities, the application is what matters,” Nieves says. “If the end effector has sharp edges or points, it can be much more dangerous than a robot that has smooth, curved end effector elements.”
Working hand in glove
GM, which estimates that it uses roughly 30,000 robots globally, is keenly interested in adding this type of automation to its operations. It teamed up with NASA to develop a robotic glove that can reduce the fatigue that quickly sets in when workers grip a tool. The Robonaut 2 should reduce repetitive stress injuries like carpal tunnel syndrome. But deployment isn’t imminent.
“It allows operators to reduce their grasp pressure,” Linn says. “We’re doing tests to see if it helps operators build a better quality product. It’s a slow process to do the risk assessment for a new technology.”
Once this analysis is finished, it could still take some time to move the prototype glove into production. The gloves must blend a number of sensors and actuators into a wearable product. GM’s initial exploration hasn’t yielded a manufacturer that’s capable and interested in commercializing the system.
“We’re trying to find somebody who makes both robots and gloves. Oddly enough, no company does both,” Linn says. “The custom part is the glove; people’s hands are many different sizes.”
In more conventional robotic applications, equipment makers are focusing on making cost-effective products. Some vendors contend that collaborative robots can be more cost-effective than their entrenched brethren.
“These kinds of co-bots are poised to bridge the gap between fully manual assembly and fully automated manufacturing lines. Nowhere is that more obvious than in the small-to-medium business sector, that up until now viewed robot automation as too costly and complex to even consider,” says Esben Østergaard, chief technology officer at Universal Robots. “The old rule of thumb is that the robot’s cost is equivalent to one worker’s two-year salary. But collaborative robots are closer to one-fourth of that price.”
Lower costs could help the robot industry—which continually sells most equipment to auto-related and electronic manufacturers—move into new fields. BJ-Gear, a Danish gear and actuator manufacturer, recently made interactive robots a primary focus of its automation strategy.
“Previously, we were reluctant to acquire robots as they were so costly that the payback time would be far too long,” says Bjørn Sommer, BJ-Gear’s plant manager, in a white paper. “Universal Robots’ flexible lightweight robots pay off in no time and are easily implemented. Our calculations show that the cost will be covered in less than one year.”
The low cost could help robotics move into lower-wage countries. Quick payback times, combined with the improved quality and efficiency provided by automation, can make these devices attractive to companies that have relied on inexpensive employees.
“Even in countries with low-priced labor, human-robot collaboration compares favorably to the total cost of an all-human workforce,” Nerseth says. “Collaboration is proving to be instrumental in raising throughput, reducing waste and taking humans out of harm’s way.”
Ease of use could also make these robots accessible for companies that haven’t before delved into robotics. Collaborative machines are inherently easier to manipulate during normal operations.
“Now humans can grab the robot and move the arm while the robot is in the play mode,” Nieves says. “Before the standard, you could only do that in the teach mode.”
This simplified control can mean that experts are no longer needed to set up robotic operations. In an era when highly skilled workers are stretched to their limits, enabling plants to program equipment and alter operations on the fly is a boon to managers and operators alike.
“While larger, traditional robotic systems require trained engineers or technical biologists to operate, collaborative robots are less intimidating,” Burnstein says. “The ability for anyone to walk up and use them is a draw for some end users.Anything that makes programming and installing the robot quicker will help justify end users for installing more of collaborative robots.”
Going mobile
Though robots that hold components or otherwise help people are getting much of the attention in this emerging area, many observers note that autonomous vehicles also work closely with people. They stop when humans or other objects are in their paths, and they carry materials that are often unloaded by people, making them collaborative.
Kiva Systems, a wholly owned subsidiary of Amazon, is one example.“Kiva uses game-changing automation technology for fulfillment centers that helps Amazon simplify operations and reduce costs,” Burnstein notes. “Using hundreds of autonomous mobile robots and sophisticated control software enables extremely fast cycle times with reduced labor requirements, from receiving to picking to shipping.”
The technology used on these mobile carriers could be reconfigured for use on other mobile products such as forklifts. Leveraging existing technologies helps build volumes that drive down prices, which often leads to broader usage. That could substantially reduce injuries each year.
“The sensors that ultimately may give a robot its autonomous capabilities can at first be used for basic safety monitoring features aboard equipment already used by human operators,” Theobald says. “A forklift that is fitted with sensors for safety could perceive a human in its path and come to a full stop before the operator can even react, curbing the 110,000 major forklift accidents that occur every year.”
Companies in this Article
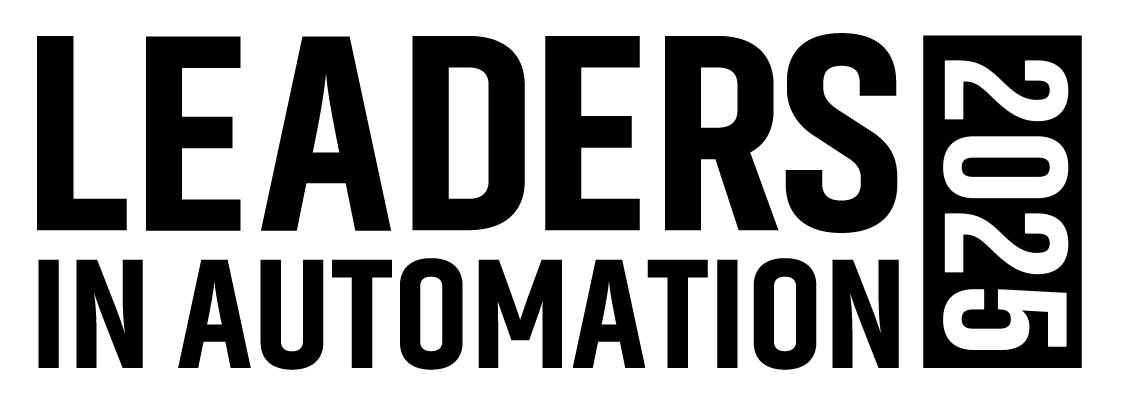
Leaders relevant to this article: