Virtually There: Digital Manufacturing Simulates Survival in a Bear Market
April 1, 2009
Dick Slansky is the first person to admit that he was a little “optimistic” when making his predictions about the adoption rate that digital manufacturing, and virtual commissioning in particular, would see over the past year. “It hasn’t grown as quickly as I thought it would,” concedes Slansky, senior PLM and Discrete Manufacturing analyst at ARC Advisory Group Inc., in Dedham, Mass.{mosimage} A little over a year ago, he predicted the overall product lifecycle management (PLM) market would grow at a compounded annual growth rate of 14.5 percent and swell from $7.5 billion in 2006 to more than $14.6 billion by 2011. While he is still putting together his updated estimates to include 2007 and 2008 numbers, it is already clear that those numbers are too ambitious. And Slansky wasn’t alone in his optimism. Industry analyst firm CIMdata, which specializes in PLM, was even more bullish, predicting that the digital manufacturing tools market would more than double between 2006 and 2011, growing from an estimated $436 million to more than $1 billion.“Several factors have constrained the growth, not the least of which are the economy and the relatively high cost of the solution,” says Slansky. Nevertheless, interest is there, and growth has been steady, despite the fact that a full deployment can often cost more than $100,000 per seat. More to the point, Slansky insists that rather than being an albatross dragging a company down, digital manufacturing and virtual commissioning can make a real impact on a company’s survival prospects in the current economic climate.“The inclination is to hunker down, cut R&D, cut spending. Innovation is going to be the difference between surviving or not as we come out of the downturn. And engineering reform is still going to be a key difference maker.”Traditionally, mechanical engineers and control engineers didn’t work together. The mechanical engineer would get the model of the finished product, design the manufacturing line to produce it and then call in the control engineer to create the code that would run the line. As the old military cliché goes, no plan survives contact with the enemy—or in this case, the production floor—and finding the design did not work as advertised was commonplace. Dozens of different factors such as collisions between robots, bad ergonomics or having the wrong machines altogether, could rise up to snafu the plan, which then had to be reworked or otherwise fixed. Since this was done in the real world, it inevitably meant metal had been bent, which had to be unbent, which in turn is time consuming and expensive. Digital manufacturing and virtual commissioning promised to do away with all that, and, according to Slansky and a host of others, it’s starting to keep that promise.Slansky defines digital manufacturing as the integration of digital models of product designs with manufacturing processes. The manufacturing engineer uses powerful 3D simulation tools to create a virtual model of all the production processes. Once complete, the virtual environment can be used to validate, synchronize and optimize the production process—to make sure it works as advertised.Virtual commissioning is that element of digital manufacturing whereby all elements of a production line are computer-simulated prior to physical set-up. Using detailed mechanical CAD models that include the conveyor systems, robotic work cells, packaging equipment and the control systems, programmable logic controllers (PLCs), motors, sensors and drives, the entire production line, or even the entire factory, can be modeled and run to see if it will work in real life the way it’s supposed to.“They can then use advanced simulation tools to validate that all of these components are synchronized, controlled, and will function in harmony to operate as intended and physically produce the product,” wrote Slansky in his January 2009 report: “The Real Story on Virtual Commissioning: Is the Technology Ready to Speed New Product Introduction?”Additionally, “Engineers can use similar tools to design and program the control logic and pre-validate the connections, logic, and dynamics of the planned physical installation. Virtual commissioning eliminates many of the time- and resource-consuming tasks that engineers must otherwise perform on real physical equipment prior to its use.”The promised benefits can be eye opening. According to CIMdata, organizations using digital manufacturing can expect to see lead time to market reduced by an average of 30 percent, the number of design changes reduced by 65 percent and time spent in the manufacturing planning process reduced by 40 percent. On the other side of the equation, production throughput can be increased by an average of 15 percent and overall production costs can be cut by as much as 13 percent.Writes Slansky, “Not only does this significantly reduce the product launch lifecycle, it also allows engineers to optimize these processes before they are physically installed. By integrating the digital product design with a virtually designed manufacturing environment, it is possible to modify either the product or the production process/equipment without incurring prohibitive costs or delays...virtual commissioning provides real and tangible benefits and addresses one of manufacturing’s fundamental issues: getting product to market in a timely and competitive manner.”Virtual commissioningBy its nature, a lot of the conversations surrounding virtual commissioning deal with the setting up of new production lines/facilities. Considering the economy, there may not be a lot of “new” set-ups taking place, but Slansky says that virtual commissioning pays off any time a company needs to reengineer a line, and is arguably even more important in such circumstances.Given the dour economy, he says, you may have situations in which you are doing limited production runs and need to reconfigure the product lines more frequently, or you may have to consolidate production from three plants into two, without abandoning products. Virtual commissioning shines in such cases, helping you be more flexible and reducing downtime.Stefan Linner, head of marketing for Siemens PLM Software’s Tecnomatix product line, agrees. “Even when companies close down factories and lines, they still need to manufacture product, just in different quantities. If they condense into one location, they may have to switch over existing capacity. If you reduce the number of plants, you may create bottlenecks in existing plants. Digital manufacturing helps avoid that.“From a high level, some people may think if the manufacturing/production goes down, the planning goes down too, but I think the exact opposite is the case,” Linner adds. “You have to be even more rigorous in planning to eliminate any inefficiencies in your process.”Siemens PLM Software (formerly UGS Corp.), a Plano, Texas-based division of Siemens’ Automation and Drives Group, is one of only two vendors offering a comprehensive factory simulation and modeling solution to the market today: the other is the French-based PLM supplier Dassault Systèmes, with its Delmia product line. Dassault has announced a series of relationships with plant floor automation vendors, including Rockwell Automation Inc., Milwaukee, to integrate Delmia directly with their PLC’s to smooth rollouts and enhance collaboration at an earlier stage in the production process. While at this time last year, both vendors were busily integrating their partnerships and acquisitions and promising future solutions, now they are rolling those solutions out to the market.“The savings are tremendous. We are talking millions of dollars,” says Jordan Merhib, sales manager at Applied Manufacturing Technologies Inc. (AMT), an Orion, Mich.-based engineering services company. “For example, one of the big three auto manufacturers had gone out to their usual line builders to automate the end of a press line. They wanted to automate the unloading of that line, and the speed and volume made it very complicated. The bids that came in were all over the map in terms of price and time. They came to us and asked us to look at these five proposals and figure out why they were so different. We simulated each one and saw that none of them would work. We modeled one that would work and they took that and included it in an updated RFP (request for proposals). They figured that we saved them more than $3 million on that one line.”AMT provides project resources, project engineering, project management, consulting and engineering outsourcing to clients. Like virtual commissioning, which took off in the automotive sector first and is expanding to other vertical industries, AMT started in automotive and has seen its client list expand to include aerospace, consumer packaged goods, industrial machinery and alternative energy.“When someone wants to put in a factory or configure a line, the best approach is to do it in the virtual world first and figure out the answers to any questions before you start cutting metal,” says Merhib, adding that the simulation group has become a “huge” part of AMT’s business. “Back in the day, people had to do things the hard way: on a drafting table, and with real-world trial and error. Now, for the most part, for anyone who comes to us to help them figure out how to do something, we will use some kind of simulation software before embarking on the work.“Despite the state of the economy, this continues to be an important and thriving part of our business,” Merhib continues. “People may not be buying a lot of new equipment, but they are trying to get more efficiency out of the equipment they have and consolidating production to conserve costs.”AMT, which uses Siemens PLM’s Technomatix for its simulation work, isn’t the only engineering services company to see the area as important. Fulda, Germany-based EDAG GmbH & Co. is implementing a Delmia automation solution from Dassault Systèmes.“The ability to virtually optimize and validate control behavior in a production cell is particularly advantageous for us as an engineering partner with our own associated line builder,” says Karina Schäfer, head of the digital factory at EDAG. “It lets us move from the construction site into the office, which in turn, creates better working conditions.”More to the point, the way engineering services firms are getting involved makes it more likely that some of the smaller manufacturers and integrators in the market may get involved in what is still a pricy area. Says AMT’s Merhib, “For us, the costs get amortized, while our customers get the full benefits today.”Subdued enthusiasmWhile somewhat subdued in his predictions, Slansky hasn’t lost any of his enthusiasm for the potential impact that digital manufacturing and virtual commissioning can have on businesses, despite the up-front investment. “Manufacturers are going to need technology like this. They may have to make some tech investments up front, but it will pay off for them in the long term.”“Given the intense competition for market share and the absolute necessity to get products to market in time to hit the market window for consumer acceptance, companies are looking for any competitive edge,” Slansky concluded in his January report. “Streamlining the design, validation, and commissioning of production systems will be a key factor for manufacturers in meeting requirements for cost-effective and efficient product launches and hitting market windows. Virtual commissioning and other digital manufacturing tools have emerged at precisely the right time in a global manufacturing climate where accelerating time to market and implementing manufacturing process optimization will be critical to a company’s success.”
Subscribe to Automation World's RSS Feeds for Feature Articles
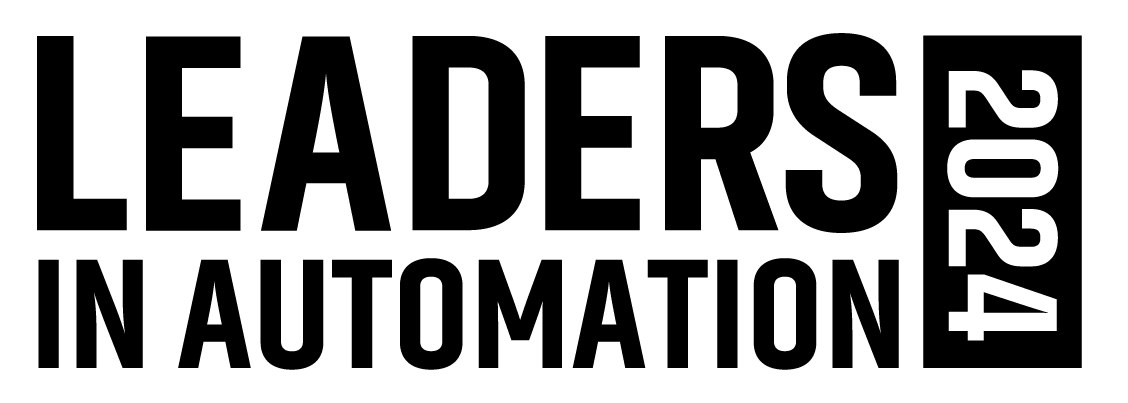
Leaders relevant to this article: