"This is a money digging world of ours; and, as it is said, 'there are more ways than one to skin a cat,' so are there more ways than one of digging for money."
-From "Way down East; or, Portraitures of Yankee Life," by Seba Smith, 1854
{mosimage} Nineteenth-century American humorist and author Seba Smith was certainly not writing about manufacturing software when he penned the words above. Nonetheless, modern practitioners of so-called enterprise manufacturing intelligence, or EMI, software are in many ways “digging for money,” when they use the technology to drill down into their factory or plant data in search of better insights.
EMI solutions are designed to extract and aggregate real-time manufacturing data from many disparate sources on the factory floor. Then, by merging and contextualizing this data together with enterprise transactional data, and presenting information via role-based graphical dashboards and other methods, EMI can enable users to track key performance indicators (KPIs), see relationships that were previously opaque, and drill down to find answers to specific questions. The resulting visibility can help users at all levels—from plant floor operators through plant management to top-level executives—to make smarter decisions that can drive results straight to a company’s bottom line.
In fact, the payoffs from the effective use of EMI software can be handsome indeed. And just as with skinning a cat, there are a multitude of ways in which the digging can be accomplished, and a plethora of vendor tools that can be deployed.
Consider the case of Valero Energy Corp., San Antonio. By using EMI software to provide better real-time visibility into the way that its 15 refineries in the United States, Canada and Aruba are using steam, electricity and fuel gas, Valero expects to significantly improve energy management across all 15 sites. So much so, in fact, that the company projects annual savings of $4 million to $12 million per plant. That’s a minimum of $60 million per year. To achieve these results, Valero selected an EMI product called Manufacturing Integration and Intelligence (MII), from SAP AG, the Walldorf, Germany-based enterprise software supplier.
Or look at Hexion Specialty Chemicals Inc., a Columbus, Ohio-based company that is the world’s largest producer of thermosetting resins and formaldehyde, with more than 100 plants globally. When Hexion began trying out EMI software at individual plants, one of the first plants to use the technology discovered savings totaling about $300,000 in the first year, spurring the company to ramp up deployment of EMI in a series of multi-plant rollouts. The product in use: EMI software from Incuity Software, of Mission Viejo, Calif., now part of automation supplier Rockwell Automation Inc., Milwaukee, which acquired Incuity last May.
{mosimage} Likewise, at Sage Automation Ltd., Australia’s largest system integrator, Team Manager for Manufacturing Intelligence Damian Jolly, in Adelaide, is excited about the benefits that EMI is bringing to one of its customers—a major Australian beverage bottler. Based on earlier experience at the plant level, EMI software will enable a boost of 3 percent to 5 percent in overall equipment effectiveness (OEE) at each of the bottler’s eight plants in Australia and New Zealand during the next two years, saving significant money, Jolly reckons. And by adding another layer atop the plant-level EMI to aggregate and distribute that data at the enterprise level, more benefits will accrue, says Jolly. “We’re certainly looking at payback within the year.”
For the bottler application, Sage is using a Software-as-a-Service (SaaS) solution from myDials, of Lafayette, Colo., to handle the roll-up of data from the individual plants for use at the enterprise level, Jolly says. At the plant level, an EMI product known as Throughput Analyzer, supplied by Activplant Corp., of London, Ontario, Canada, delivers the site level intelligence.
Fantastic info
With a server at every bottling plant, the Activplant software provides “fantastic information and manufacturing KPIs to drive process improvement initiatives at the factory level,” Jolly observes. But due in part to reliability questions surrounding Australia’s wide area network infrastructure, Sage selected the SaaS-based myDials solution to connect the data to the next level, says Jolly. “All of these plants have good Internet access, so it really solved the journey of distance, of moving data between sites,” he explains.
{mosimage} MyDials, which can gather and aggregate data from a large variety of both enterprise and operational data sources, including Activplant, presents information in easy-to-read, interactive dashboards. This enables management at the bottler to make plant-to-plant comparisons on a variety of metrics, using only a Web browser and Internet access. “They’ve got the ability to drill into a region, a site or a line,” Jolly points out.
{mosimage} The myDials and Activplant products play well together to provide effective role-based intelligence, he adds. “The line managers, factory managers, process improvement people and the regional managers on up will be looking at the myDials information,” Jolly says. But for the plant floor operators, “Activplant is the best solution when you want to get down to the granular details.”
As noted on Wikipedia, the free online encyclopedia, the primary goal of Enterprise Manufacturing Intelligence is “to turn large amounts of manufacturing data into real knowledge and drive business results based on that knowledge.” AMR Research Inc., in Boston, has identified five core capabilities that every EMI application should possess. Those capabilities, as summarized on Wikipedia, are as follows:
• Aggregation: Making available data from many sources, most often databases.
• Contextualization: Providing a structure, or model, for the data that will help users find what they need. Usually a folder tree utilizing a hierarchy such as the ISA95 standard.
• Analysis: Enabling users to analyze data across sources and especially across production sites. This often includes the ability for true ad hoc reporting.
• Visualization: Providing tools to create visual summaries of the data to alert decision makers and call attention to the most important information of the moment. The most common visualization tool is the dashboard.
• Propagation: Automating the transfer of data from the plant floor up to enterprise-level systems such as SAP, or vice versa.
AMR has recently added three more capabilities—data mining/discovery, process modeling, and simulation/scenario analysis—that the research firm says are needed for what it calls “next generation operations intelligence,” or OI. And as noted by Alison Smith, a former AMR research director who covered the technology, no single vendor can do it all.
Adding layers
Rather than a single application, EMI/OI actually amounts to an architecture that will ultimately involve various software layers and applications, says Smith, who today is vice president, marketing strategy & research, at Aspen Technology Inc. (AspenTech), a Burlington, Mass., supplier of process optimization software and products. Further, she confirms, there are many possible ways to skin the EMI/OI cat, using different sets of tools and applications depending on a manufacturer’s industry and specific needs.
{mosimage} “For instance, you could take SAP’s MII and layer it over a data historian—or a dozen historians—and in that architecture, you could still have a ShopLogix or Zarpac running on your high-speed packaging lines, along with historians on your blending and mixing processes that were upstream,” Smith relates, referencing EMI suppliers ShopLogix Inc., based in Mississauga, Ontario Canada, and Zarpac Inc., an Oakville, Ontario, Canada-based supplier that specializes in packaging-line performance improvement. Then, as an additional part of this architecture, Smith says, “you’d still need to build a database somewhere, either a historian or a relational database, that would help with your KPIs that you’re going to ship up through MII to your ERP (enterprise resource planning) system.”
Data historians are core components of any EMI architecture in which high speed data acquisition is required, says Smith, who joined AspenTech—a historian supplier—last November. Historians are an EMI necessity in high-speed, highly complex environments such as refineries, for example. But in a pharmaceutical environment, in which a single batch might take weeks to run, a high-speed historian capable of collecting, say, 500,000 data points in a one-second sweep, may not required, Smith says. For this application, “you could probably use different search and analytical tools, and a different kind of database architecture,” she notes.
As a result, as a way to avoid missteps that could cause problems later, manufacturers looking to install EMI applications should consider their needs and their ultimate architectural plan up front, Smith advises.
Isauro Martinez-Cairo, Burlington, Ontario, Canada-based director of EMI for process technology supplier Invensys Process Systems (IPS), agrees on the need for EMI architectural planning. “IPS sees EMI not so much as functionality that is necessarily delivered by a tool of some sort, but as a need that its clients have, a need which it fills through consulting, systems integration and project solutions, sometimes involving third-party partnerships and products,” says Martinez-Cairo.
There is no doubt that as manufacturers examine the EMI/OI space, they have plenty of vendors and applications to choose from. A recent AMR report on the topic mentioned well more than 20 vendors playing at various levels in the EMI/OI market.
In the core EMI space, the AMR list includes vendors of “EMI frameworks,” such as Rockwell Incuity that offer sophisticated EMI development environments, as well suppliers of “production asset-monitoring applications” such as Activplant, ShopLogix and Zarpac. The latter group differs from EMI Framework vendors in that they offer more packaged content such as templated graphics, reports and calculations, and most have a heritage in tactical OEE “focused primarily on performance-monitoring scenarios inside four walls,” AMR says.
What’s new?
Wonderware, an Invensys company based in Lake Forest, Calif., is also called out among the “production asset-monitoring” group of vendors. According to MaryAnne Steidinger, Wonderware MES/EMI marketing program manager, the company currently supplies a variety of both manufacturing- and enterprise-intelligence-based tools and applications that can be used as part of an EMI architecture. But Steidinger tells Automation World that Wonderware also plans “in the near future” to introduce a new product to be called Wonderware Intelligence. “I really can’t say too much about it because it’s still in the throes of development and finalization, but it’s basically going to be our entry into the market with a true enterprise manufacturing intelligence product,” Steidinger says.
Wonderware is not alone in stepping up its EMI and intelligence-based offerings. Other manufacturing execution system (MES) vendors, which have long offered various EMI elements within their product lines, have lately been adding more architectural features such as improved analytics and better multi-site visibility.
The same is true of traditional automation controls suppliers, who have been moving up the MES food chain in recent years and are now adding more EMI capabilities. Rockwell’s 2008 acquisition of Incuity is one clear example. And at automation supplier GE Fanuc Intelligent Platforms, in Charlottesville, Va., Global Markets Development Manager Michael Yost declares that EMI is one of three core pillars of the company’s Proficy operations management software, together with MES execution, and quality and compliance capabilities.
Likewise at Phoenix-based automation vendor Honeywell Process Solutions (HPS), Francois Leclerc, manager of product marketing, notes that Honeywell products such as its Uniformance PHD data historian and Process Studio visualization package; its KPI Manager, which automatically collects and generates KPI results; and its Business Hiway, which provides a link to ERP systems; are among key elements of an extensive Honeywell intelligence capability that is already in place. “We have been winning business with manufacturing intelligence and business intelligence for years,” says Dan O’Brien, HPS MES solutions manager.
Middle fighting
At the same time, traditional enterprise software vendors are also busy adding and enhancing their EMI capabilities. “The big vendors like Oracle and SAP have certainly recognized the need to deal with manufacturing data, and particularly data that is centric to production operations,” observes Dan Miklovic, research vice president who heads up manufacturing research at Gartner Inc., Stamford, Conn.
{mosimage} SAP led the way with its 2005 acquisition of pioneering EMI vendor Lighthammer, whose Illuminator product has since been evolved into the SAP MII product, Miklovic says. And Oracle Corp., Redwood Shores, Calif., recently rolled out an EMI solution known as Manufacturing Operations Center (MOC) that integrates with the company’s Enterprise Business Suite ERP system, he notes.
Even IBM Corp., Armonk, N.Y., is getting into the act with its Cognos business intelligence technology picked up in its 2008 acquisition of Cognos Inc., Ottawa, Ontario, Canada. “They’re not calling it EMI, but if you look at some of the things that IBM is doing, they’re providing Cognos with more capability to talk to plant automation systems,” Miklovic observes.
As noted by Bob Lenich, director of the Syncade Product Platform at process control supplier Emerson Process Management, in Austin, Texas, “The enterprise guys are clearly coming down, the process control guys are clearly coming up, and there’s a little bit of a fight going on here in the middle.”
Emerson, for its part, is pushing toward the middle with its new Syncade Smart Operations Management suite introduced in February this year. Billed as “a new class of real-time production management software to improve plant operations,” the Syncade suite can help improve decision making through the integration of real-time plant floor data and transactional plant business processes, the company says. The software pushes into new territory for Emerson in its extension to the MES layer, or level 3 of the International Society for Automation’s ISA95 standard for enterprise and control systems integration.
“Emerson has always been at levels 1 and 2 with our instrumentation, our control systems and our asset management systems,” says Lenich. “Now, with Syncade, we’re committed to level 3 in terms of pulling together all of that information off the production floor and then looking at how to format it, verify it and then send it on up to the enterprise.”
Quick returns
In today’s difficult economic environment, the time may be right for EMI, say proponents and industry watchers alike. AMR Research Director Simon Jacobson pegs EMI as one of the fastest growing segments in the overall $6 billion market for manufacturing operations software. “Even in a down economy, a lot of companies in this [EMI] space are seeing significant traction,” he observes.
{mosimage} As plants shut down and companies cut back on capital spending, EMI investments can pay off by providing the visibility needed to boost performance of existing plants and assets, Jacobson notes. And the return on investment (ROI) for an EMI project can be rapid, he says, ranging from 1X to 5X per year for a “tactical OEE” investment at a single plant, up to the 10X range for EMI applications in which “you look across a fleet of plants or assets.”
Vendors tell a similar story. Vivek Bapat, an SAP vice president, says that payback typically comes within three to five months for users of his company’s MII product. And Doug Lawson, president at Rockwell Incuity, says that “increasingly, we have good case studies that we can show to customers where the product pays for itself well within a year.”
In some cases, a single discovery that would otherwise have gone unnoticed—such as bottleneck in a production line, a product going out of a specification, or a pipe that was about to burst—can produce near instantaneous EMI payback, various vendors point out. “The ROI can be phenomenal, because you’re making previously undiscovered or invisible information visible,” says Wonderware’s Steidinger.
“The cool thing about EMI is that it’s low risk,” adds Aspentech’s Smith. “You’re not actually changing the process. You’re just watching the process,” she says. “And the payback is great. As much as I love MES systems, these [EMI] things pay off a lot faster than MES does, I’ll tell you that,” Smith concludes.
Related Sidebar - A Room with a View
To read the article accompanying this story, go to www.automationworld.com/feature-5368.
Related Sidebar - EMI Down Under
To read the article accompanying this story, go to www.automationworld.com/feature-5369.
Subscribe to Automation World's RSS Feeds for Feature Articles
Companies in this Article
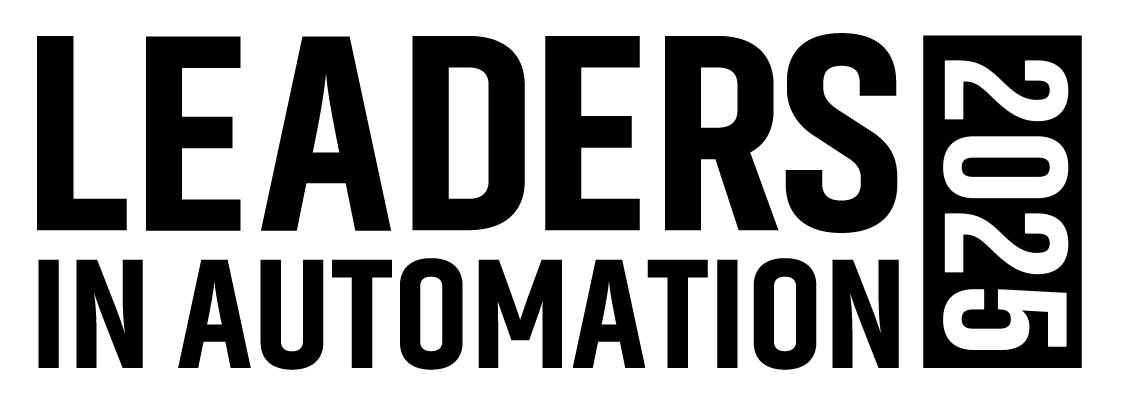
Leaders relevant to this article: