Ethernet continues to expand its role in the factory, but it’s facing some stiff competitors as it stretches down to the input/output (I/O) level. When engineers need to connect sensors and other simple components, they’ve got a number of alternatives that are often more cost-effective than Ethernet.
A range of architectures provide the low cost and performance needed for I/O connections. At the same time, wireless technologies are addressing ease of use, eliminating the difficulty of routing wires every time equipment is moved or new gear is added. Though skeptics scorn the reliability of sending signals through the air of a noisy factory, there’s little doubt that wireless is going to play a solid role in the factory of the future.
Ethernet will also hold a significant role in data gathering. It’s dominating as a central network when production facilities are upgraded, bringing compatibility with the front office. A number of companies are now eyeing the large number of I/O nodes that fill today’s factories, hoping to displace the fieldbuses often used to link these nodes to Ethernet or other factory-wide backbones. Speed is a key weapon in their arsenals.
“We’re betting the farm that Ethernet to remote I/O is the way to go. With today’s switched networks, speed is not an issue. It takes less than a millisecond to send a message,” says Tom Edwards, senior technical advisor at Opto 22, a Temecula, Calif.-based vendor.
Pick your flavor
Other companies and technology groups are promoting various flavors of Ethernet, using different approaches to keep performance high without pushing costs up. For example, the EtherCat architecture keeps costs down by using an application-specific integrated circuit, or ASIC, to handle network communications, making it possible to use less powerful, less expensive central processing units (CPUs) in equipment. “Our ASICs or FPGA (field programmable gate array) implementations are typically cheaper than what competitors use for the underlying fieldbus applications,” argues Joey Stubbs, North American representative for the EtherCat Technology Group, based in Nuremberg, Germany.
Without that capability, Ethernet may not be effective for I/O. “Cost prohibits going down to the [sensor] level. Implementing Ethernet still requires a small computer with a software stack and maybe some extra code to handle standard communications,” Stubbs says.
Others eschew extra hardware, instead using software techniques to give Ethernet the speed that’s needed in applications with strict timing requirements. “Ethernet Powerlink can run on any Ethernet board, because it’s only software. We add the Powerlink stack to assure that messages arrive on time,” says Markus Sandhoefner, sales manager at automation vendor B&R Industrial Automation Corp., of Roswell, Ga.
“At very high speeds on equipment for jobs like carpet making, each I/O node has to operate at 300 to 400 microseconds. If you did that with Modbus, you’d have latency, and with IEEE 1588 (a standard of the Institute of Electrical and Electronics Engineers) you couldn’t rely on an action occurring, though you would know how much a knot might be off,” Sandhoefner says.
Though variations of Ethernet bring real-time capabilities, others note that Ethernet’s speed continues to increase, making the basic network suitable for I/O jobs in which speed is critical. “Fieldbuses have always been deterministic. Ethernet has gotten so refined that that’s usually not a problem now,” says Jeff Blyther, systems engineer at Lantronix Inc., an Irvine, Calif.-based vendor.
Proponents of basic Ethernet also note that pricing premiums over alternative buses are fading as volumes continue upward. “As Ethernet’s usage becomes bigger and bigger, cost issues are disappearing, though for sensors, you still need an alternative,” says Sylain Olier, distributed I/O marketing manager at automation supplier Schneider Electric, in North Andover, Mass.
Product developers also note that Ethernet is addressing ease-of-use by simplifying cabling. With Power-over-Ethernet, engineers don’t have to route power to I/O nodes. “Power-over-Ethernet will help drive application to these types of jobs,” says Bill Black, controllers product manager at GE Fanuc Intelligent Platforms, another automation supplier based in Charlottesville, Va.
But here again, the additional cost of delivering power takes Ethernet away from its high-volume niche. Connectors and cables will be a bit more expensive than those for conventional network products. “It boils down to cost. If you have modular I/O and want to use only Ethernet, you may need to go to Power-over-Ethernet, which raises the price,” Olier says.
Expansion blockers
Ethernet is very cost effective for equipment that has a fair amount of computing power, which earned it the role of standard backbone technology throughout most factories and front offices. The communication scheme is often built into these processors, so it’s effectively free. But competing technologies at the I/O level are not giving way as easily. Sensors and other fairly inexpensive products often don’t have this integrated technology.
“When you get down to something like a photo eye that costs $30 to $50, we haven’t seen Ethernet because of the cost issues. People generally use I/O blocks to get data in a cost effective manner,” Black says.
Those blocks are used widely, and observers don’t expect that to change. “Quite a few PTO members use I/O blocks, connecting eight sensors at an I/O block. It’s hard to imagine Ethernet getting below that level,” says Carl Henning, deputy director at the Profibus Trade Organization, based in Scottsdale, Ariz.
I/O blocks are far from the only alternative for linking low-level gear to the network. Many vendors support a number of fieldbus architectures for these applications. For example, Bosch Rexroth Corp. recently augmented its motion control systems with device-level networking.
“We released a full set of Ethernet I/O protocols this summer, including SERCOS III (for Serial Real-time Communication System), Profinet and EtherNet/IP. It’s better to have a motion control network you can hang I/O onto than to have one network for motion and one for I/O,” says Ted Thayer, PLC product manager at Bosch, based in Hoffman Estates, Ill.
Many options
Those aren’t the only networks being used in the diverse manufacturing world. Many companies take the approach of integrating alternative technologies into their solutions, picking networks that are more cost-effective for lower-level devices. “Within distributed I/O, we use CANopen (for Controller Area Network), though most of the users don’t know it’s CANopen. It’s used downstream for distributed I/O on small machines. All data gathered by CANopen is communicated to Ethernet,” Olier says.
Another option is CC-Link (for Control & Communications Link), which has seen widespread use in Japan. It’s expanding globally, with about half of the 900 members of the CC-Link Partner Association (CLPA) now based outside Japan. It’s designed for fairly simple devices. “CC-Link goes down to the I/O level. You can even put two-bit devices on it. It uses memory mapped I/O so you get more usage of your memory space than with the object-oriented approach of most other architectures,” says John Wozniak, network specialist for the CLPA, in Vernon Hills, Ill.
However, he adds that the technology is not limited to simple applications. Like many networks, it’s got a hierarchy of technologies, with a safety bus and CC-L Industrial Ethernet for higher level communications. However, the simplicity of the I/O level version is a key attraction.
“The master-slave system broadcasts transmissions, providing response times of 4 milliseconds for a 64-device network. Along with speed, ease-of-use is a big attraction. All I/O points look like I/O words on a PLC,” Wozniak says. He adds that CC-Link networks can have thousands of nodes.
European designers also came up with a low-level solution, the Actuator Sensor Interface. The AS-Interface also boasts international usage. The PTO has focused some of its compatibility efforts on the network.
“AS-Interface complements fieldbuses, tying in well to Profibus and Profinet. We’ve got a series of proxies that are part of the standard, so mapping between the two buses is part of the spec.,” Henning says. That eliminates incompatibility, he says.
While AS-Interface focuses on simplicity, it also offers some versatility. “You can intermix safety and standard I/O on the same network. That takes a tremendous amount of cost out, eliminating the need for a safety network,” says Helge Hornis, intelligent systems manager at automation components vendor Pepperl+Fuchs Inc., of Twinsburg, Ohio.
Though many are building solid businesses around these low-level buses, others don’t predict a strong future for them. For example, AS-Interface has its detractors. “With AS-Interface, you need a dedicated master and dedicated cable, which adds expense,” Stubbs says. Bosch’s Thayer predicts that some of these buses won’t have long lifetimes. “We don’t see a whole lot of future for AS-Interface or Modbus,” he says.
Whither wireless?
One of the hottest growth areas in networking technology these days is wireless. It’s seeing more use in areas that change often and those where routing wiring would be difficult. That often describes I/O nodes. Eliminating wires greatly simplifies installation in applications that meet the performance specifications of various wireless architectures. That translates to a metric that resonates in office suites as well as on the plant floor. “Wireless can really reduce costs,” Black says.
Those costs aren’t trivial. When plants or lines are being redesigned, it’s common to add sensors to existing equipment and install new machines. When all these nodes must be wired, costs can rise quickly.
“If IT (information technology) departments drop an Ethernet line on the shop floor, it can cost $300 to $700. For simple implementations, that’s not cost-effective. A lot of companies are looking at wireless,” says Lantronix’s Blyther.
For many communications companies, wireless is a double-edged sword. For example, Opto 22 is rolling out a link to wireless sensors, but it also sees wireless as a threat. The company’s wireless strategy was planned during a fluid stage for wireless standards, but the company decided the technology is now settling down. The success of IEEE 802.11n provides enough speed and market acceptance to let the company settle on this version of the wireless fidelity, or Wi-Fi, specification. Generally, speed rises as the alphabetic notation progresses.
While wireless technologies can complement Ethernet, they will also provide some competition. “Technologies like ZigBee provide a true alternative for systems with relatively small numbers of parts that are widely distributed,” Opto’s Edwards says. Beyond ZigBee, he adds that “there’s room for a lot of wireless technologies.”
Though wireless technologies are seeing rapid growth, they aren’t yet applicable in all areas. In motion control, for example, there’s little interest at this point. “Wireless is eventually going to give us the capability to extend distance and reduce cost, but it’s not something we’re pursuing yet,” says Bosch Rexroth’s Thayer.
Wires forever
Though there’s a lot of interest in wireless technologies, there’s also a fair amount of caution. Skeptics note that speeds aren’t high and that bits can be lost when they’re sent through the air in noisy factory environments. “Wireless has some reliability problems. Some manufacturers are going with dual wireless to eliminate them,” B&R’s Sandhoefner says.
There are also applications within the I/O world that have demanding requirements that still can’t be addressed with wireless communications. “If you need high speed or synchronization, you probably need to use a medium. Wireless doesn’t have high speed or great predictability,” says Stubbs, at the EtherCat Technology Group.
Others note that wireless is an emerging area where several technologies are vying for success. As can be expected in a rising application, some wireless approaches have higher reliability levels than others. “I prefer 802.11a because there’s more noise immunity, particularly at the I/O level where 10 to 50 millisecond response times are usually fine,” Blyther says.
Most observers feel that the concerns over trustworthiness will dissipate as successful wireless protocols undergo more real-world testing and technology advances. That has already occurred with other networks. “The fears people have with wireless today are basically the same concerns they had with Ethernet a few years ago,” Black says.
Some product developers note that wireless is often discussed as a single technology, but in reality, there are many different flavors of wireless. The standards and proprietary communication schemes each have their own positives and negatives.
Some groups are working to provide suggested good practice for implementing wireless. For example, the PTO, Hart Foundation and the Fieldbus Foundation are working together to provide consistency for wireless sensor networks.
Although wireless is treated as a new technology, some groups have longstanding efforts that work without wires. “There’s been a lot of fuss lately about wireless sensor networks. We’ve done wireless Ethernet for a long time, picking up 802.11,” Henning says.
To view the accompanying article, "Software Tools Manage Data Flow", go to www.automationworld.com/view-4204.
Companies in this Article
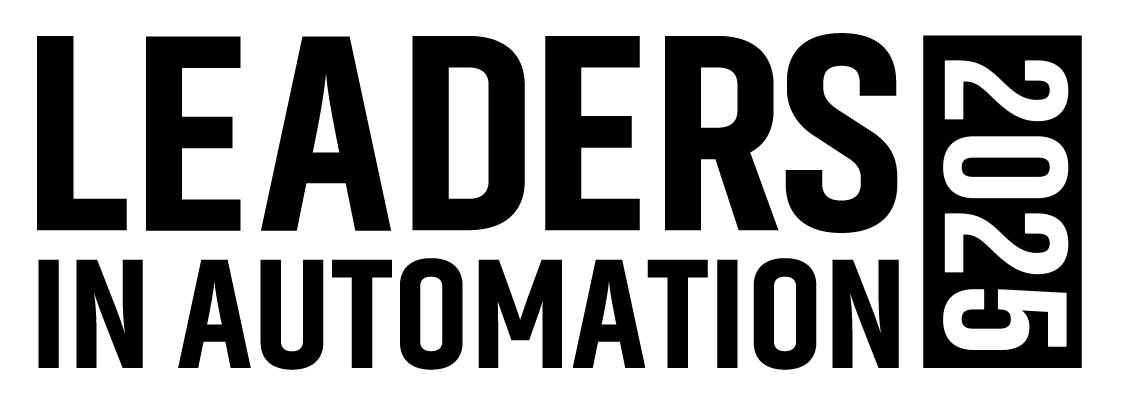
Leaders relevant to this article: