Around the world, major manufacturers and industrial organizations have implemented FDT Technology to help improve plant device interoperability, reliability, and maintenance, while at the same time, preventing unplanned shutdowns, reduce downtime and lower maintenance costs in a wide range of plant automation applications.
The FDT standard makes it easier to access field equipment in the many facilities that use more than one communication network. It simplifies device configuration, commissioning and integration, and brings data from intelligent instruments using different communication protocols together to provide a single point of access for information critical to plant asset management.
With FDT Technology, industrial firms gain the freedom to mix and match field communication protocol; control system platforms; and device suppliers, simplifying device integration for process, factory and hybrid manufacturing environments.
Different needs, integrated solution
In fields like brewing, pharmaceuticals and pulp & paper, many different automation technologies are used throughout a single facility and the enterprise. The challenge is to develop new strategies for maintaining cost-effective, sustainable production capacity, and any such strategy will need to take into account the efficient integration of the network infrastructure. A typical plant might have field devices and systems from 10 different vendors running multiple protocols, each with its own configuration tool.
As an IEC 62453, ISA103 and China GB-T 29618 standard, FDT Technology solves the problem of device integration. It enables interoperability of device information designed to work in facilities that have multiple communication networks to improve plant reliability, lower costs and maximize intelligent assets. The technology was specifically developed to provide an open, standard interface for integrating field devices with automation and asset management systems.
The FDT solution is independent of the communication protocol and the software environment of both the device and the host system—allowing any device to be accessed, from any host, using any protocol. Because it bridges the gap between different communication protocols used in different industries, FDT is suitable for demanding process, hybrid and discrete automation tasks. More importantly, for end users, it also allows them the freedom to choose best-in-class devices from any supplier without worrying about incompatibility.
Since FDT breaks down proprietary barriers in control systems, it opens those systems to smart applications that can utilize all of the advanced features of today’s growing portfolio of intelligent devices.
FDT Technology is well adopted in the global marketplace and known as the most widely accepted integration standard in the industry. Due to its flexible design, the openness of the FDT architecture allows newer technologies such as protocol annexes and other technology standards to be integrated. One example is that the FDI standard is designed to be fully compatible with the FDT standard. FDI addresses integration of process automation networks based on Electronic Device Description Language (EDDL). End users can be assured that their current investment in FDT-enabled tools and devices can be used to incorporate FDI Device Packages (DP’s), as they appear on the market.
Who’s benefitting from FDT?
As demonstrated throughout the industrial sector, FDT Technology can present more meaningful device information to optimize plant operations and, ultimately, economic performance. It is particularly beneficial to the industrial workforce by enabling greater problem and risk awareness, and improved decision support. It also helps empower corrective and collaboration tools, and productivity and workflow solutions.
It is particularly important to consider the advantages of FDT Technology for automation suppliers. The ability to provide customers with a single engineering environment to configure, commission, and manage field assets lowers the total cost of ownership and creates enormous competitive advantages. The supplier is able to progressively lower long-term product maintenance costs by only having to sustain one device engineering software suite to manage the lifecycle of any instrument—from any manufacturer—on any communications protocol.
The list of major end user companies and organizations that have realized significant value from implementation of the FDT standard now reads like a “who’s who” of the industrial sector. From refiners and petrochemical companies, to food processors and power plants, the “face” of FDT in process, factory and hybrid automation is as diverse as the scope of its applications.
For example, Dalum Papir A/S, a leading paper manufacturer based in Odense, Denmark, has enhanced its asset management capabilities using FDT Technology. The company operates two paper machines to produce high-grade office and printing paper. A key initiative is transitioning from time-based to preventive maintenance.
Dalum’s No. 7 machine is controlled and monitored using five different control systems. Several hundred instruments, connected to remote input/output (I/O) devices, support diagnostics and the HART protocol. An FDT-based asset management system communicates via Device Type Managers (DTMs) with all devices—regardless of their make—using various communication protocols. This solution allows diagnostic information to be output at any point within the user network, and real-time data accessed from the devices reflects the current process conditions.
The MOL Group’s Danube Refinery in Százhalombatta, Hungary, has overhauled its plant maintenance systems with a new, unified approach to asset management leveraging the capabilities of FDT. The refinery uses the technology, embedded in device configuration and maintenance systems, to enable fast, simple and safe device configuration and diagnostics as part of its on-line maintenance strategy.Robust information is available to identify the location of an asset problem, for instrument repair, and to remotely access device information and change configurations. The results are enhanced maintenance processes, as well as improved human competencies and skills.
For KUKA, a leading German manufacturer of robotic systems, configuration of industrial robots can be a daunting task. Robotic packages incorporating numerous devices and peripherals must interface to an automation system that issues various coordinating control signals. Multiple fieldbuses are used in a single robotic application.
To cope with the complexity of this application at a manufacturing site in Louisiana, KUKA utilized a common configuration and management tool including an FDT Frame Application. This tool saves all fieldbus-specific information generated during commissioning. DTMs work seamlessly with one another, even though different manufacturers supply them, and complex bus scenarios can be configured across multiple gateways without any difficulty using the nested communications capability in the FDT standard.
Industrial Furnace Company, Inc. (IFCO), a Rochester, New York, firm that designs, constructs and upgrades incinerators, heat treat furnaces, kilns, smelters, boilers and other thermal equipment, also uses FDT Technology to optimize device configuration and commissioning.
IFCO supplied gas-fired, multi-hearth furnaces for a new activated carbon plant in Coushatta, Louisiana—the largest of its kind in the U.S. The company employed an open control platform on the furnaces, whereby networks share a common application layer and have a seamless flow of information between them. This allows engineers to configure furnaces from a single point, as well as access the system’s information remotely to monitor performance and troubleshoot problems. Thanks to FDT Technology and its DTMs, configuration and commissioning of devices and systems utilizing different communication protocols is an efficient process. Additionally, DTMs resident in the plant asset management software work with fieldbus alarm blocks in each instrument to keep track of device health.
In Japan, Mitsubishi Chemical’s Kashima Plant uses smart instrumentation information monitoring to optimize asset lifecycle costs while enhancing maintenance activities, increasing safety, and improving product quality. Key to these improvements is a standardized FDT interface to collect information online from HART- and FOUNDATION Fieldbus-compatible devices and store it in an asset management system. The Kashima facility uses rich device data to ensure the health and performance of field instruments through condition-based maintenance. Equipment is kept in top working order during the entire operational phase of the plant lifecycle.
At Techno-Agrar’s coal wash plant in Germany, electronic motor management (EMM) modules are parameterized and diagnosed via FDT to allow conveyor belts to operate smoothly and efficiently. Reliable production operations require the visualization of all relevant process parameters as well as comprehensive diagnostic options in the control room. With the use of the FDT Technology, combined with the EMM modules, operators can monitor pumps and conveyor belts and, if necessary, adjust the parameters accordingly. Potential failures are therefore detected and prevented in a timely and efficient manner.
Looking to the future
Ongoing development of FDT Technology is enabling end users to realize the true potential of decentralization, transparency, integration, and a unified view of all data and functions within the manufacturing enterprise. Enhancements to the FDT standard enable faster execution for mega installations incorporating thousands of I/O devices, as well as improved control system security.
FDT Group is also committed to maintaining the flexible and scalable nature of its standard. New Frames are compatible with all generations of DTMs, providing full backwards compatibility for the installed base of FDT Technology. This approach eliminates “rip and replace” scenarios in applications utilizing different eras of field equipment, and allows new and existing hardware/software to coexist.
Current FDT developments related to the Industrial Internet of Things (IIoT), Industry 4.0, worker mobility, cloud computing, predictive analytics and cyber security are at the forefront of the automation market. Control system and device suppliers are providing compliant solutions to help plants monitor and manage their intelligent devices with the same level of automation, efficiency and security found in IT infrastructure. Support for both new and existing device technologies and networks will help expand this horizon.
Conclusion
Across the globe, leading companies involved with process, factory and hybrid automation that have realized significant value in engineering, commissioning, operation and asset management by utilizing control solutions with FDT Technology. Open access to robust device intelligence has proven to be the answer to improved overall plant performance. It also allows for a safer work environment by reducing the number of trips to the field and lowering start-up costs.
For more information on FDT Technology, please visit: www.fdtgroup.org
Companies in this Article
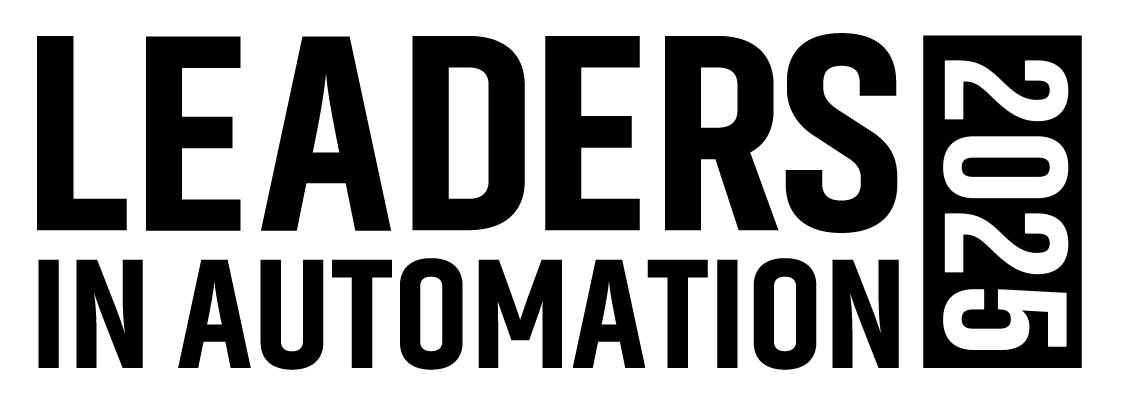
Leaders relevant to this article: