Enhancing DP-Based Flow Measurement with Dynamic Compensation
This article describes how a multivariable pressure transmitter with built-in dynamic compensation can correct for many of the errors and inaccuracies that can occur in differential pressure based flow measurements. It also shows how the built-in computing and communications capabilities of such modern flowmeters ensure ease of integration with FDT Technology based tools in process automation and management systems.
Introduction
Differential pressure transmitters form the core of many field instrumentation systems. They are widely used to measure the flow rate, pressure and density of liquids, gases and steam, as well as the level of liquid in a tank. Over the years, such transmitters have evolved to offer increased accuracy and reliability, as well as enhanced computing and communication facilities to ease their integration into plant-wide monitoring, control and in particular, plant asset management systems. Not only are field devices required being more precise and stable, they have also become much more intelligent due to advances in modern microprocessor technology.
A major step towards meeting these challenges came with the development of the DPharp digital resonance sensor, which eliminated the error-prone A/D convertor required by analogue sensors, and provided ‘quartz watch’ stability with unmatched precision, accuracy, response and repeatability. The combination of a digital sensor with integrated processing circuitry provides sensor diagnostics and high integrity, and allows full digital integration in a fieldbus based control system.
The DPharp sensor is an advanced MEMS (micro-electro-mechanical system) based silicon-resonant sensor featuring superior precision and excellent long-term stability. The technology is also inherently fail-safe. Moreover, the design of the DPharp sensor allows differential pressure and static pressure to be transmitted from one sensor (transmitter), allowing the basic pressure measurements to be used as the basis of flow and level metering.
The result is a multivariable transmitter which acts as an ‘all in one’ instrument, integrating the functions of a differential pressure transmitter, a pressure gauge, a thermometer and a flow computer, while featuring high performance and space-saving design. The transmitter employs an advanced flow-rate calculation method to achieve a mass-flow calculation cycle of 100 ms. By adopting a Reynolds number compensation algorithm, all flow calculation parameters are optimized and a mass flow accuracy rate as good as 1% of actual flow rate is achieved.
The multivariable transmitter is compatible with a wide range of primary devices, including orifice plates, nozzles, averaging pitot and venturi tubes, and can be used with various types of fluid, including general fluids, steam and natural gas. Application information, such as the primary devices and fluid data required for mass flow calculation, is input using a mass flow parameter configuration tool that runs on a PC and is downloaded to the transmitter by means of field communication. In operation, the flowmeter computes standard volumetric or mass flow from measured differential pressure (DP) and flowing density using actual measured pressure and temperature, unlike standard differential pressure transmitters which assume pressure and temperature - and therefore flowing density - to be constant.
Error sources affecting DP flow measurement.
Fig.1 shows the transmitter set-up for flow measurement. The basic mass flow equation performed is:In DP flow measurements, the variation in flowing density is only one of a number of potential sources of error.
One source of error is the primary element. The orifice plate still is the most widely used primary element, and its accuracy is extensively debated. It is known, however, that its accuracy degrades over time as the plate loses its sharpness. A typical accuracy figure might be 1% of rate. Another source of error is the DP transmitter. This accuracy is expressed as a percentage of upper range value (URV), and is magnified by the square-law relationship between flow and differential pressure.
Traditionally, DP-based flowmeters have featured a 3:1 ‘turndown’. This is a figure that expresses the range: over which the accuracy is perceived to be acceptable: 30-100% of flow for a 3:1 turndown. If the accuracy of the DP transmitter is assumed to be ±0.2% URV, at 100% flow the accuracy is ±0.2% plus the error of the plate. At 70% flow (49% DP due to the square-law relationship), the accuracy would be ±0.4%; at 50% flow (25% DP) it would be ±0.8%; and at 25% flow (6.25% DP) it would be ±3.2%. The plate adds ±1% over the full range and, when ±2.5% total accuracy is perceived to be acceptable, that accuracy is reached at around 30% flow - hence the 3:1 turn down. Turndown is often increased to 9:1 by using two DP transmitters over the same plate with different ranges, a switching mechanism and a flow computing function.
Today, of course, DP transmitters are much more accurate than ±0.2%. However, the accuracy is still expressed as a percentage of URV, and the square-law relationship between flow and DP is still applicable. Nevertheless, one could argue that a turndown of better than 5:1 is not normally achieved. The error due to pressure (±0.5 bar) and temperature fluctuations (±10°C) in gas or steam flows can easily be of the order of magnitude of ±2%.
The flow factor k in the basic formula above is a constant compensating for the differences between theory and real life. It is calculated as part of the orifice calculation, and is valid only for one particular set of operating conditions – making it another potential source of error. It is dependent on the discharge coefficient, the gas expansion factor and velocity of approach factor.
The result of an orifice calculation is the diameter of the hole in relation to the pipe diameter: the so-called ß-ratio. When a fluid is flowing through a pipe with an orifice plate, the flowing area reduction is abrupt, causing the smallest flowing area (Vena contracta) to be downstream (behind) of the plate. The discharge coefficient (based upon experimental research) compensates for the difference between theory and real life. However, the discharge coefficient is flow profile (Reynolds) dependant and varies with the flow velocity, pipe internal diameter, flowing density and flowing viscosity. In turn, the latter three parameters are affected by flowing temperature.
When a gas or steam flow passes the orifice plate (Fig.2), it is compressed upstream of the plate due to the obstruction caused by the plate. Downstream of the plate it expands again. The gas expansion factor corrects for density differences between the pressure taps, and it depends on the ß-ratio, the isentropic coefficient (correcting for theoretical versus real-life expansion), differential pressure and static pressure. Again, temperature has an effect as well. Finally, the velocity of approach factor is dependent on the ß-ratio (d/D), which in turn is dependent on temperature. The pipe and orifice plate material expands or contracts as temperature changes, and the velocity of approach factor corrects for changes in ß-ratio due to temperature fluctuation.
Dynamic compensation
The error in flow factor k increases with decreasing flow rate, significantly contributing to the overall flowmeter accuracy. A primary element of a DP based flowmeter is sized for one particular set of operating conditions. When in real life the conditions change - lower pressure, higher temperature, lower flow rate etc. - the user would like to re-calculate the flow-rate/DP relationship for every new set of conditions. This is exactly what the multivariable transmitter does. It corrects for pressure and temperature variations and it can compensate continuously for the effects of changing operating conditions on the flow factor. Using its flow configuration wizard, the transmitter can be set up to act as a flow computing device.
There are two mode options: basic and auto compensation mode. In basic mode, the transmitter only compensates for pressure and temperature fluctuations with a constant flow factor, in much the same way as a standard DP transmitter with a separate flow computer, resulting in a turndown of perhaps 5:1. However, in the auto compensation mode, it dynamically compensates for fluctuating conditions and their effects on the flow factor, reducing the error basically to the uncertainty intrinsic to the primary element. Consequently, the accuracy specification of ±1% of flow rate (assuming the primary element to be ideal) over a 10:1 turndown in flow terms (equivalent to 100:1 turndown in DP terms) is only valid in the auto compensation mode. This multivariable transmitter breathes new life into existing square-law flow measurements and, with its 10:1 turndown, not only eliminates the need for a separate flow computer, but can replace one or two DP transmitters and a pressure transmitter over the same plate, while achieving good performance over a wide flow range.
As indicated above, this transmitter supports a range of primary flow devices including orifice plates, averaging pitot and venturi tubes. The flow computer is configured using a portable software application, FlowNavigator™, based on FDT Technology, which interrogates a DIPRR (AIChE) physical properties database for 126 fluids and gases as well as pipe and plate material property databases. Its compressibility equations meet international standards including the AGA 8 and ISO12213 natural gas equations (either simplified or using the full molecular weight composition method), IAPWS-IF97 formulation for water and steam, or custom compensation based on user-defined density and viscosity data.
Configuration through advanced DTM
An important benefit of these advanced transmitters is provided by their advanced communication capabilities, allowing them to interface with other elements of an integrated plant-wide operation. As a result, it is possible to carry out remote configuration and diagnosis using industry standard tools such as FDT Technology, where FDT stands for Field Device Tool. FDT is an industry wide well established and proven open interface specification. A key component in FDT is the Device Type Manager (DTM), a ‘portable’ device (software) application.
FDT Technology is supported by all leading suppliers of intelligent devices and process automation systems. Through DTMs, it facilitates the management and configuration of sensors, actuators, flowmeters, transmitters and other field devices that are installed at production sites and connected to process automation and plant asset management systems as well as PC-based device configuration and management tools, regardless of the communications protocol used (Fig. 3).
The DTM for the multivariable transmitter being discussed in this article features an add-on flow configuration wizard (Fig.4). This DTM with the add-on module can be integrated in any so-called FDT Frame Application. The add-on module not only features the flow configuration wizard configuring the transmitter for a specific flow application: it also, uses FDT’s unique capabilities to access the fluid and material property databases and features the ‘obtain flow coefficient’ function where the transmitter calculates the flow rate, flowing density, discharge coefficient etc., on the basis of manually entered values for differential pressure, pressure and temperature to verify the correctness of the flow configuration. Consequently, the latter function drastically reduces the commissioning effort for this type of device (Fig 5).
The use of this technology creates an open environment in automation systems and devices such as the multivariable transmitter discussed in this article. FDT Technology frees users from having to learn configuration methods from different manufacturers and eliminates the constraint of having to install devices from the same manufacturer, allowing more efficient plant operations to be realized.
The system shown in Fig.6 is a configuration and maintenance tool that uses FDT Technology to facilitate the configuration and adjustment of field devices in this way, and helps customers to optimize asset availability through improved device control and management. Demand for this kind of configuration software is increasing as field devices become more intelligent and digitalization of field communications moves forward. By supporting the latest open standards, systems of this type allow users to enjoy the best benefits of intelligent field devices and digital field communications.
About FDT Technology
FDT based solutions incorporate “open” or standards-based technology which are protocol, automation system and device supplier independent and tested to be interoperable. FDT Technology is an open IEC 62453, ISA 103 and GB/T 29618 international standard which provides device applications (or drivers) called Device Type Managers (DTMs) and Frame Applications which are embedded in device configuration, maintenance and management software applications. The majority of automation, control and device suppliers offer these valuable protocol, supplier and control system independent solutions that are FDT enabled. And because of the rigorous testing and certification programme, you can be confident that devices from different suppliers will fully interoperate with each other for any application – reducing your risk of problems.
Companies in this Article
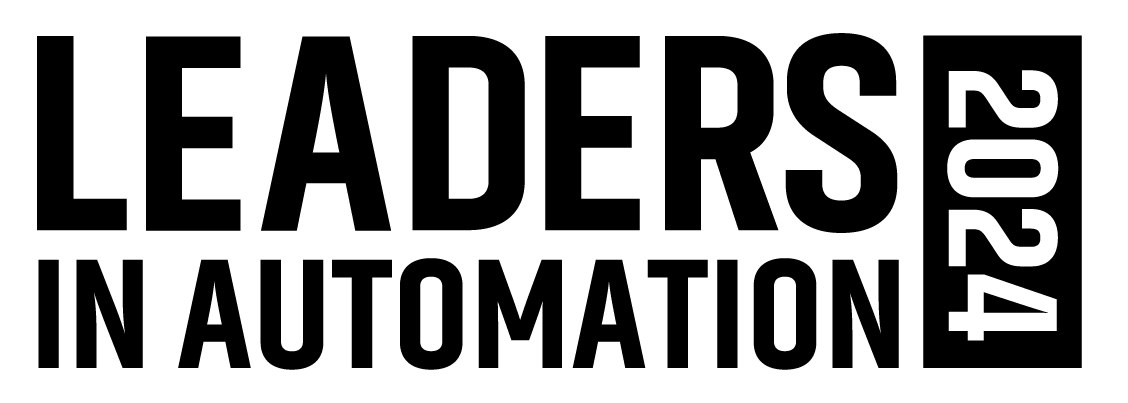
Leaders relevant to this article: