For suppliers of industrial control products and solutions, implementation of the FDT® standard is a forward-looking strategy supporting the new era of automation. The technology will soon offer greater flexibility for developers with an innovative FDT Server solution supporting the Industrial Internet of Things (IIoT), including applications opening the door for standardized sensor-to-cloud and enterprise-wide integration.
New Opportunities on the Horizon
FDT Group is an independent, international, not-for-profit standards association supporting FDT technology (IEC 62453). Its current FDT 2.1 standard provides a powerful combination of features, including faster performance, greater ease of use, and improved investment protection. These developments underscore FDT’s transformation as a complete, standardized IIoT architecture.
Development of the FDT IIoT Server™ (FITS™) platform is the “game-changer” the automation industry has been anticipating. The emerging FITS specification is set to empower the intelligent enterprise with native integration of the OPC Unified Architecture (OPC UA), as well as comprehensive control and Web Services for mobile applications. Additionally, it includes robust security to protect valuable information and operating data. FITS will enable cloud, enterprise, on-premise, and a single user desktop deployment methods meeting the needs of the process, hybrid and discrete sectors.
FITS is multi-faceted, scalable and agile, and can be utilized in a host of diverse operating environments due to its platform independent approach employing .NET Core framework. The technology has diversified to include single-user desktop and multi-user server environments. FITS protects industry investments in FDT through advanced business logic, well-defined interfaces and Common Components, and enables Operating System (OS) agnostic implementation of the technology while supporting today’s integrated automation architecture.
FDT Group members, including many of the largest suppliers of industrial automation technology worldwide, see a wide range of opportunities to better serve customers – and improve their business performance – by adopting the FITS solution.
Indeed, the insights of the FDT Group leadership community may be an “eye-opener” for companies that have not kept a close watch on key developments in the FDT standard.
Expanded Connectivity and Worker Mobility
Automation suppliers have a broad view of how the FITS solution is likely to impact the industrial marketplace, including its role in simplifying the automation ecosystem exchange. Designed to empower the future of IIoT and Industrie 4.0, FITS enables sensor-to-cloud and enterprise-wide connectivity.
Another large control software provider expects FITS to expand mobile access to detailed device diagnostics across equipment vendors and all FDT-supported network architectures, while eliminating the need for advanced coding or programming in the supervisory control system.
At the same time, the company believes OPC UA and mobile remote access will have a significant impact on plant and factory maintenance personnel, who are looking for condition-based maintenance solutions to reduce their cost for periodic, scheduled repair and troubleshooting activities. OPC UA service opens up all possible parameters in an installed device, so end-users can pick specific maintenance-related parameters and observe their trends.
According to a key FDT Group member, the original premise of an FDT/FRAME application – to provide access to key information for asset management and to configure multiple vendor field devices across multiple protocols – is still compelling. However, the addition of FDT Server increases the number and variety of platforms that can be used for accessing this information.
The member stated, “Virtual reality access to field device and asset management information in the plant will be an important driver for implementation of FITS. For the industrial sector, the extremely wide and growing range of protocols for IIoT-based sensors and controlling elements is another positive argument for FITS adoption.”
An additional automation supplier considers OPC UA connectivity with standardized data models for all types of field devices and across all protocols – and with web access via mobile devices – as important capabilities justifying implementation of the FITS solution. The FDT Server’s Web Service features will be useful for monitoring device status remotely, while convenient smart phone usage is an advantage for work in the field.
Enhanced Communications and Cyber Security
With the convergence of Information Technology (IT) and Operational Technology (OT) in industrial manufacturing, there is a need to safeguard data access from the enterprise all the way down to the device level.
A key FDT Group member supplying process control technology has a positive outlook for the adoption of FITSThe FITS solution features robust layered security, leverages vetted industry standards, and utilizes Transport Layer Security (TLS) to establish a hardened shell and encrypt all communications throughout the architecture. Optionally, this solution can authorize devices connected to the FDT Server. User-based security is employed to determine the user’s role and rights within the application.
The addition of security on the wire via CIP to the FDT standard will enable a complete solution for comprehensive, end-to-end, enterprise-wide security.
Greater Interoperability and Information Access
FDT Group technology was ahead of its time in terms of providing secure and reliable interoperability and information access across automation systems, networks and devices. Now, members of the organization anticipate that future platform independence within the FITS architecture will open up new opportunities and business models.
A leading controls developer remarked: “Some people see the ability to use Linux as the holy grail of cost reduction because of the elimination of a Windows license on each server. An FDT Server running on a cloud platform could create a new opportunity for a ‘FITS as a Service’ business model. Both automation and IT service vendors would have a chance to take part in this business.”
A second supplier offered this perspective: “While platform independence would not be an advantage for a single plant where the decision to use an automation platform of a certain brand has already been made, it could benefit customers who operate larger plants with different brands of automation systems. Here, real-time monitoring and predictive maintenance applications requiring uniform access to field devices across platforms would realize significant value from FITS. Platform independence with this solution would enable enterprise control so that a single control room can monitor multiple plants at a time on a remote basis.”
Standardized Device and Network Integration
FDT’s ability to seamlessly nest or tunnel through a myriad of networks to transparently communicate with the end device demonstrates its pivotal position in an intelligent, connected enterprise.
The latest technology developments protect existing investments in the FDT standard while also providing the foundation for a modern, integrated automation architecture. FDT is the bridge to IIoT connectivity for legacy protocols, and at the same time, supports modern solutions using Ethernet and other IIoT networks. In this way, the technology provides complete cross-networking integration for legacy and next generation communications.
As the FDT IIoT Server architecture becomes a technical standard infrastructure throughout the industrial automation field, it will be deployed across different control system platforms becoming the comprehensive standardized solution offering freedom of choice for field device integration.An automation vendor already incorporating FITS in its business strategy commented: “OPC UA server implementation, once it comes with FDT Server Common Components, will make it easy for vendors to include such services in their product line. Interpreter DTMs for FDI Device Packages and some protocol-specific DD files are welcomed by system and device suppliers, since they address most of the devices in a web user interface without the need for device-specific DTMs.”
Improved Plant Operations and Maintenance
A growing number of automation technology firms think FITS will transform the way end-users around the world operate and maintain their facilities. A supplier with global operations said, “With FITS, maintenance becomes much more empowered thanks to better diagnostics and easier access to device information, reducing downtime andThe supplier added, “Remote access with FITS Web Services will enable 24/7 observation of devices. This capability could be enhanced with a device patrol feature, which connects devices and collects diagnostic information using static functions. The FDT Server could issue alerts to maintenance personnel by mobile apps, email or SNS, so they don’t have to stay at the plant all night.”
Web Services will provide a standardized mobile access approach utilizing browsers, apps, standalone applications or anything else capable of interfacing via web sockets. Any mobile device authenticated by the FDT Server will have full access to the topology with tunneling capability to manage assets on any network. These features will spur the development of new apps to optimize asset management, preventive maintenance and other critical functions at modern industrial facilities.
Another automation solution provider indicated FITS could help meet growing customer and legislative demand for storage and access to process parameter and configuration data – including the availability of both live historic view and live instant view information via either desktop or virtual reality applications.
Increased Customer Demand and Implementation
FDT Group members predict that improvements in end-user workflows will spur a rapid transition to FITS products. However, as one member stated, customer benefits will need to be clearly addressed and demonstrated. This will make control system and device vendors more likely to invest in FITS and integrate the technology in their platforms.
A control software supplier active in FDT development work noted that R&D budgets are increasingly restrictive in the automation sector, with product design efforts planned many years in advance. As such, the adoption of new technology is notoriously slow. The supplier stated, “The ability to connect FDT at a level customers are demanding, such as in cyber security, will likely result in increased adoption.”
Due to the “hidden” nature of FDT, some end-users do not realize it is the world’s leading device and network integration standard for industrial automation – implemented by nearly all major controls suppliers. Indeed, the technology might be the industry’s best-kept secret, since there is little direct visibility of FDT/FRAME applications and other parts of the standard. As an embedded technology, FDT is largely undetectable by industrial control engineers who are using it without issue.
Automation solution providers are learning that FDT-based products are not difficult to develop. Suppliers have access to a set of tools saving countless engineering hours in their R&D efforts. FDT developer tools such as Common Components are available to create a library of routines to simplify the development process. Developers can also employ the official test and certification tool for DTMs,dtmINSPECTOR. These tools ensure specification compliance, greatly enhance interoperability, and work together to help developers deliver robust FDT-enabled solutions while accelerating time to market.
Conclusion
Plants and factories employing FDT-enabled systems are already benefiting from open access to the Industrial Internet. In the future, FITS will simplify the move to IIoT, providing OPC UA integration, Web Services, mobility, and control to enhance connectivity and information sharing across platforms. These and other opportunities will transform the outlook for industrial automation stakeholders.
Companies in this Article
Sponsored Recommendations
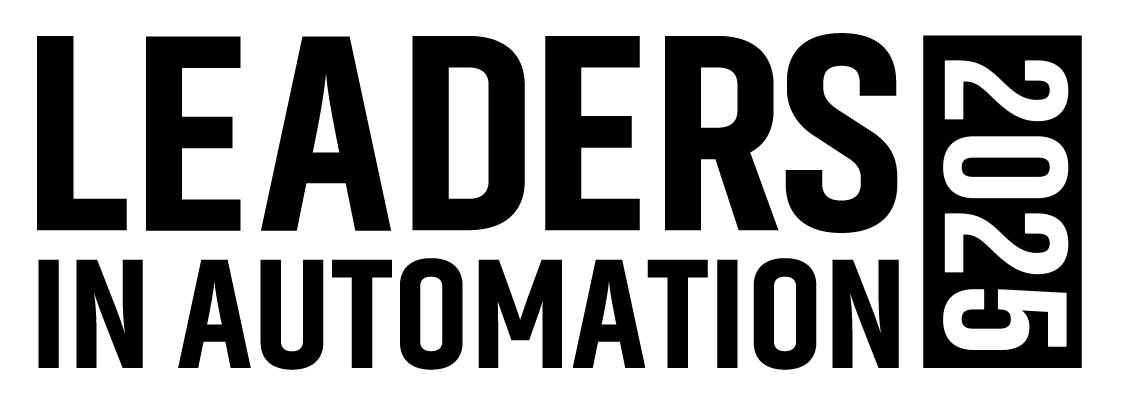
Leaders relevant to this article: