Controls Technology Improvements Increase Efficiencies for Robotic Aseptic Syringe Filler/Capper
It wasn’t that long ago that packaging robots focused on end-of-line functions, such as case packing and palletizing. In December, ESS Technologies introduced its TaskMate® Robotic Syringe Filler and Capper. The system integrates two FANUC clean class LR Mate robots with RABS (Restricted Access Barrier System) from SKAN to meet the stringent requirements for 503B sterile pharmaceutical compounding applications. ESS designed the system to increase production speeds and efficiency, reduce scrap and rework, and reduce overhead while protecting both products and employees from harm. The system can fill and cap up to 15 syringes/min. TaskMate Robotic Systems is ESS’s trademarked brand for a variety of robotic pick-and-place systems. The SF20 syringe filler is a member of that brand.
In operation, empty syringes are manually fed through a sterile rapid transfer port into the ESS-supplied, vibratory hopper, dropping them gently onto a flex feeder with a powered, backlit, vibratory conveyor. A spreading tray/vibrating conveyor moves parts forward to a FANUC 2D guidance vision system where the first LR Mate 200iD robot picks syringes one at a time. When no parts are available, the robot will turn the spreading tray on and signal the vibratory hopper to feed additional parts. Once the camera sees available parts again, the conveyor and vibratory hopper stops. The robot, which uses a custom designed vacuum style end-of-arm tool (EOAT), picks a syringe from the flex picker conveyor and transfers it to the filling station.
The filling system uses a stainless-steel, servo-driven, volumetric pump, which is provided with an input connection to attach the filling nozzle to the product supply bag. A precise amount of liquid is dispensed from the bottom up. Caps are manually fed via a drawer that can be pulled out from the RABS to load and unload trays of caps. The second FANUC LR Mate 200iD robot, which also uses a custom-designed vacuum-style EOAT, picks a cap from the tray and places it into the torque station. A servo-driven pick-and-place unit transfers the syringe from the fill station to the final torque station.
For screw-type Luer-Lok caps the system rotates the cap to apply torque. A precision force sensor detects the correct amount of torque and supplies a pass/fail signal to the system. The capping system handles both press-on and tamper-evident Luer-Lok screw-on caps through the use of change parts. The robotic system discharges the filled and capped syringes via a divided gravity chute to a customer-supplied discharge bin. In the event of a station error, bad syringes get discharged via the opposite side of the chute for customer inspection.
Controls and automation advances
With such complex tasks, it’s understandable that controls and automation are essential to the efficient performance of the TaskMate equipment. Mike Morgan, ESS Electrical Engineering Manager, says, “Controls and automation technologies are constantly improving. The availability of new technology for detecting and acquiring parts opens up new opportunities for handling product and allows our systems to operate more efficiently. For instance, advances in vision technology allow for more precise detection and positioning of products in robotic guidance applications. New technologies and updates in industrial safety standards also allow for collaborative robot design to allow operators to safely work around robotic applications without stopping equipment—in some cases without the use of guarding at all. Advances in robotic technology also allow for greater speed, precision and payload capabilities.”
Kevin Browne, ESS President, points out that the recent addition of hygienically designed components also provides benefits to equipment that wasn’t possible in recent years.
Specific robotic systems
The key controls and automation systems related to the Fanuc robots are within the Fanuc controller that executes the required program and directly controls robotic function. Below is a listing of the key components used for the ESS robotic system:
• The syringe picking robot receives information about the location of syringes to be picked via an integrated Fanuc iR vision system that permits flexible feeding of many different syringe types and sizes because the syringes are presented to the robot and camera via a custom-designed vibratory spreading tray and backlight.
Devan Vest, the company’s R&D Engineer, says ESS used a low particulate-generating feeder with an overhung glass presentation area. ESS then worked with Metaphase Technologies to develop a custom, high-intensity LED back light to illuminate the syringes from beneath the feeder. “ESS expanded upon the development of the custom backlight by encapsulating the backlight in an ultra-compact, stainless-steel enclosure that meets stringent environmental demands,” he says. “Special consideration was taken for proper heat dissipation and environment sealing, which affords our end user with reduced changeover time, improved cleaning ability, stable inspection, and long life for the entire system with varying conditions.”
• The Fanuc controller receives signals from an AB PLC (from Rockwell Automation), regarding when to move based on other signals the PLC receives from elsewhere in the system. That assures the concerted actions of the machine occur at the proper time.
• The status of the machine is displayed on a hygienic multi-touch display provided by Beckhoff Automation, specifically designed for compatibility with industry standard sporicidal agent (a cleaner to kill spores).
Vest says, “We chose Beckhoff to supply this component because it is a unique offering on the market that is capable of withstanding frequent, long-term exposure to the caustic cold sterilants that are commonplace in aseptic processing. This allows our end users to more easily clean and comply with the cGMP guidelines for aseptic processing published by the FDA.”
• Baumer provides many of the hygienic sensors used directly within the aseptic environment that are responsible for monitoring the status of components through the PLC and the Fanuc controllers. ESS chose Baumer sensors, says Morgan, “for use in the aseptic environment because of their easy-to-clean hygienic designs allowing less time spent cleaning, better aseptic technique, and an overall safer environment with a lower risk of entrapped contaminates.”
• Turck Connectivity products are used for connection to electrical components inside the environment because they offer stock and custom connectors where needed that can withstand the sporicidal agents.
• Elobau provides e-stops that feature no external moving parts. A silicone seal encases the switch that improves cleaning and also withstands the sporicidal agents.
• Rittal offers hygienically designed enclosures and control cabinets that meet the aseptic processing machinery requirements. “ESS chose Rittal for their hygienic offerings and ease of customization to existing enclosures,” notes Vest.
• NovoNox makes the hygienic fasteners used on the machine. Says Vest, “Their electro-polished fasteners exceed the surface finish requirements, are passive as a result of the electropolishing process, and are designed around special sealing washers to seal the head against the seating surface of the bolt.”
• ESS notes that another key OEM involved with the development of the SF20 is SKAN. “While not an automation vendor, they provide the Open RABS used on the system,” says Vest. “Working with SKAN to develop the RABS, ESS has developed a user-friendly system that can be more easily managed through the glove ports thanks to their extensive worldwide experience in RABS and the Isolator market.”
Companies in this Article
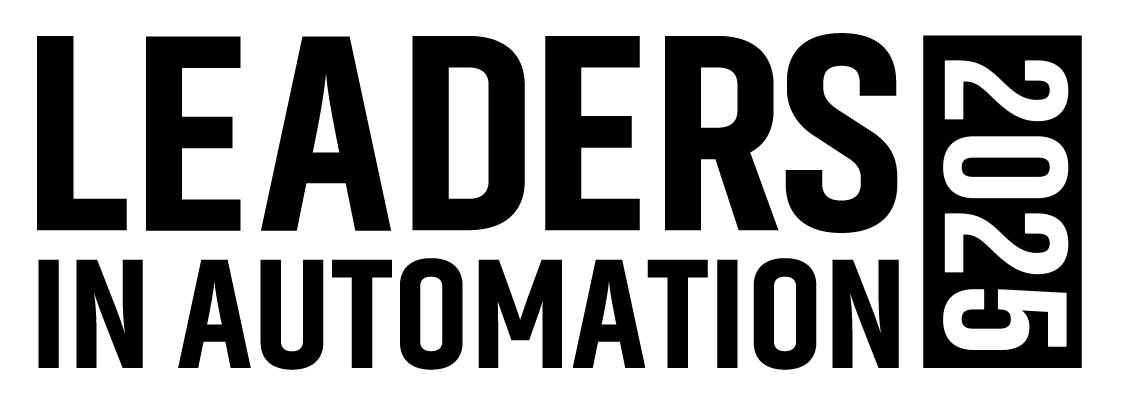
Leaders relevant to this article: