When manufacturing companies attempt to raise profits by doing more with less in the areas of human resources and capital spending, they might find they are inadvertently distancing themselves further from their goal. Reducing headcount in manufacturing automation support places substantial burden on the remaining technicians to effectively respond to production’s calls for help. Reductions in capital spending allocations force procurement departments to routinely award contracts to the low-dollar bidder while assuming all the bids are equal in content and deliverables.
In both instances, the manufacturing companies can incur much higher costs as time goes on that can quickly offset the initial savings of cutting headcount or going with the lowest price. Having automation standards in place can help a manufacturing company reap the intended initial cost savings while mitigating the risk of incurring unintended higher total cost of ownership.
Automation standards are a set of guidelines and specifications created by a company’s automation group or created with the assistance of a qualified integrator/supplier. These standards cover a wide variety of topics, including—but not necessarily limited to—instrumentation; controls and HMI (standalone, thick client or thin client) hardware; programming software, including version levels; visualization/historian/reporting software platforms, including such specs as number of screens and number of tags; server and virtual machine (VM) platforms; network standards (physical and logical); configuration and programming methods (open sourced as contrasted to proprietary); documentation standards (drawings, requirement specs, functional specs, review specs, checkout and commissioning specs, training verification); project execution, including design reviews, FATs, SATs, punch lists and project closeout; use of specific productivity tools, including cloud-based, such as Google G Suite and Microsoft Office 365 SharePoint, Teams and Planner. Automation standards can also include the best practices of suppliers like Rockwell, Panduit, Cisco, Stratus or VMware along with industry associations such as ISA, IEEE, IEC, ANSI and OMAC. The company might have to spend some money to create these comprehensive standards, but remember—sometimes you have to spend money to make money.
Let’s review real cases where not having automation standards resulted in unintended and unanticipated cost incurrences.
In one case, a large food manufacturer added a new production line to one of its existing plants; the new line included a sizeable batch process. The integration was competitively bid with minimal specifications. The contract went to the lowest bidder, which used its own proprietary software batch engine on the project, forcing the unwitting client to go back to that integrator for all support and modifications. The client is very unhappy, to say the least, and feels handcuffed moving forward.
Use of a proprietary automation platform can become even more burdensome to a client when the OEM or supplier is located on a different continent and possibly six or more time zones ahead or behind the plant needing quick response to issues shutting down an entire line. An equal amount of burden and lost production time might also be experienced even when automation systems within a plant are open-sourced, but each system has its own personality and technique because each programmer did it their own way—not following any standards and forcing the technical support resources to learn multiple approaches and ways of thinking.
In another case, a recently acquired pharmaceutical manufacturer added a production line and also wanted to make various enhancements to several of its existing processes. The only specification given: Low price gets the order. The incumbent integrator spent many years helping the manufacturer create and deploy standard automation platforms, meeting industry best practices as well as FDA regulatory compliance. But the new parent company decided it was more beneficial to engage the services of the lowest-cost automation supplier.
The successful bidders did come in at the lowest cost, won the contracts and brought to the jobsite programmers and engineers with little or no experience on the established platforms. Additionally, each integrator resource at the plant programmed the systems using their own technique and approach; not following a common programming/configuration standard as in the past. The projects are not going well and are costing delays in the implementation schedules. In addition, many of the traditional change control procedures to meet regulatory compliance are routinely circumvented. Additional costs will be incurred to correct much of the damage.
In another example, a Midwest U.S. utility company had been increasing its use of connected automation-based power monitoring, controls, visualization, historians and reporting systems without having a comprehensive networking specification. Its operations were experiencing annoying and growing latency issues in controls, screen updates and operator commands. The technicians were pointing their fingers at the OEM equipment and software, saying they were unreliable and not robust. Examination of the plant’s OT network revealed the source of the latency issues was the network itself—unmanaged switches in many locations as well as poor practices in network topology. Much remediation work—and cost—in the network is needed to solve their issues.
Manufacturing plants and utilities should continue to find ways to increase output, increase yield and decrease scrap while reducing operating costs and missed production opportunities. Automation standards can noticeably facilitate reaching those goals. Recruit the services of a qualified system integrator to assist with creating the automation standards useful and effective for your manufacturing environment.
Steve Malyszko, P.E., is president and CEO of Malisko Engineering Inc., a certified member of the Control System Integrators Association (CSIA). See Malisko Engineering’s profile on the Industrial Automation Exchange.
Companies in this Article
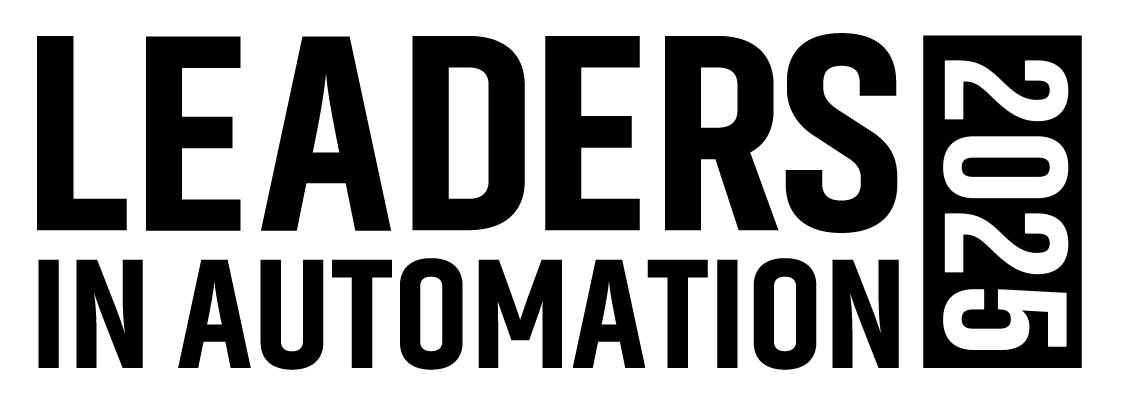
Leaders relevant to this article: