Operating in machines at extremely high speeds and achieving high precision labeling with very little errors place Elmo as a major solution provider in the field of high-end labeling and cupping machines. The challenges involving operating more than 60 integrated motor/drives as a solution on an extremely fast rotating platform, transferring high-power, and high-speed EtherCAT communication via slip rings, is implemented rapidly and efficiently only with Elmo's smart solutions and advanced tools.
Realization of a fast bottle labelling (or cupping ) machine challenges the design and execution of complex and dynamic ECAM movements. These require the tackling of fast manipulators using rapid, sophisticated, and complex control of rotating mechanics, with dozens of motors and drives that operate in an unfavorable, vibrating, humid, and extreme temperature environment. In addition, there is the requirement of transmitting fast, deterministic and “signal integrity” sensitive communication via the slip ring media. This could involve substantial time, many weeks of intensive work, requiring high-level expertise with considerable experience.
The Advance Motion Control offered by Elmo simplifies and dramatically eases the implementation process to the level of an ordinary engineering (no wizards) and shortens the Motion Control design and operation to less than three days.
The Innovative Solution:
-Smart Supporting Software Tools.
Using an innovative Smart Software toolbox that simplifies the process of motion development. It contains two major group of tools; the first group are an integral part of the EASII advanced tools such Servo Tuning, ECAM, Error Mapping, Network Configuration etc..., which are regularly used in the configuration stage of the development. The second group is a set of very rich and sophisticated “motion blocks”, (EMBL, Elmo Advanced Motion Blocks), Libraries and Machine Templates, that simplify the long exhausting programming requirements constructed by the developer/programmer. These are usually used in the process development stage of the machine. The two groups complement each other to achieve the goal of simple implementation in the fastest timing. “Intelligence by Simplicity” not only eliminates the need for multi-disciplinary implementers, but also dramatically improves the motion control performance and significantly Shortens the "Time to Market" while enormously saving engineering resources.
-Integrated Motors.
-Powerful GOLD WHISTLE servo drives, which are ultra-small, highly efficient, and very rugged, are integrated inside the motors. This significantly simplifies the rotating carousel, saves appreciable space and weight, restricts the cabling to only DC bus plus EtherCAT communication cables, and “shrinks” the electrical cabinet. This “no-cabling” reduces the induced EMI and improves the noise immunity.
-GOLD Servo drives.
The Ultra small intelligent G-WHI servo drive is perfectly tuned for widest bandwidth and fastest response by overcoming the non-linearity of the mechanical load. This allow very fast, stable operation, very high throughput, and error free operation.
-The Maestro.
The whole orchestra of 60 servo drives is conducted by the Maestro, controlling and supervising the entire “bottling” process. The Maestro is a World- Class multi axis controller, precisely executing the complex motion scenario. Harmonious Motion is achieved by the Maestro operating in conjunction with the GOLD Servo Drives.
Solution highlights:
60 Axes located on a rotating platform are used for high speed bottle labeling and cupping. Bottles are automatically fed into the machine and transferred to the rotating platform. The rotating platform consists of 60 high power, small footprint Elmo DUETs, an advanced integrated Drive/Motor solution. The DUETs are essential components in this machine due to the limited size of the rotating platform. The DUETS are positioned on the rotating platform, and use direct coupling to ensure high precision of rotation during Camera image capturing.
Only High power and a serial EtherCAT cable is connected between the DUETS. The richness of the EASII tools and functionalities enable tuning of the drives and optimization of their servo operation to provide highest speeds, precision, and accuracy. The EASII Advanced Servo Control incorporates capabilities to maximize the optimization of the servo performance of any motor and any mechanics.
The Compact Motor/High Power Drive solution is optimized for limited machine space. It uses high resolution absolute feedback to achieve high precision and best servo control and performance. The DUETs solution must be rugged to withstand the mechanical vibrations of the rotating platform. The minimum cabling used in the solution results in minimum influences of external noise, low EMI and RFI, therefore provides the best solution for large numbers of axes controlled by EtherCAT serial communication networking.
Four high speed cameras are located at the stationary section of the machine. When bottles pass through a camera, a snapshot is taken and transferred to a host computer. The host computer processes the picture data and calculates the exact label position using an image processing algorithm. The bottle rotation is controlled by the Maestro, Elmo's multi axes controller, which sets the initial target labeling position and waits for the ECAM execute operation to start. The ECAM function running on the Maestro is one of the key functionalities used in the operation of this machine.
Operating the ECAM using the Maestro has huge advantages. All slaves operate in DS-402 standardized cyclic synchronized position mode of operation. The Maestro and EASII allow high interpolation levels for smooth motion trajectories with a minimum number of ECAM points. It enable Fast Dynamic table calculations, execution, table switching, multi-hierarchy topology building, virtual axes synchronization and many related advanced features that simplify and accelerate the implementation process.
The advanced EASII, Elmo Application Studio ECAM tool combined with Elmo's EMBL - Elmo's Motion Block Libraries, enable very simple, fast design and precise testing of the ECAM trajectories to raise the machine level to operational within a matter of days. By just adding several slave positions as a function of the Master position and interpolating between the position in one of the advanced interpolation methods. The EMBLs are complementary to the EASII advanced tools setup. Elmo developed numerous EMBLs that simplify the development process of the machine. For example Homing (all DS-402 methods and more), Output Compare (PEGS), Emulation, ECAM, PVT, Splines, Joystick.... .
Elmo continues to develop and introduce new EMBLs for the users, without any request of payment.
With the right tools Elmo walks you through the whole implementation process in a Simple, fast and intelligent manner, ensuring the shortest “time to market” with minimum engineering resources.
>> For more information please click here.
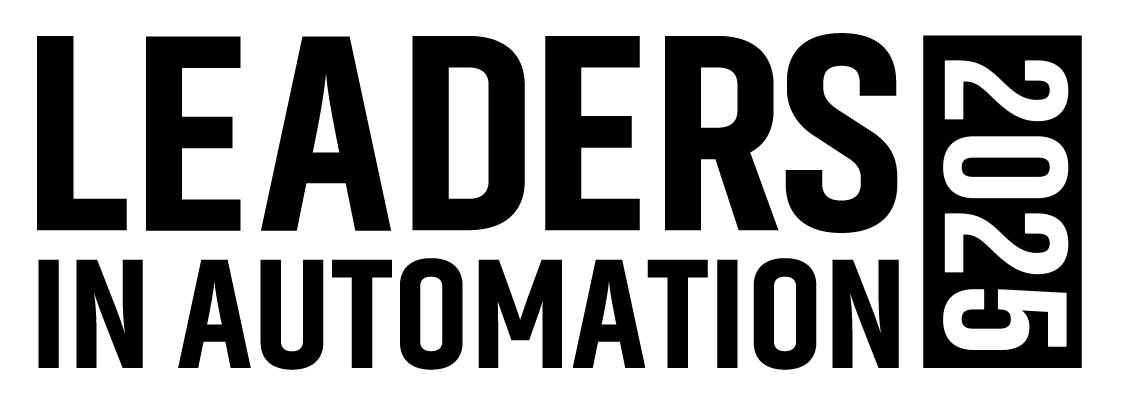
Leaders relevant to this product: