Enhancing Worker Safety with Real-time Personnel Location Systems
In recent years, a number of high-profile accidents in the industrial space have raised public and regulatory concerns, not only over the potential for environmental impact, but also over the safety of workers. Last year’s Upper Big Branch Mine explosion in West Virginia killed 29 miners, for example, while the BP Deepwater Horizon disaster in the Gulf of Mexico—which caused billions of dollars in environmental and economic damage—also took the lives of 11 oil platform workers.
When the unthinkable happens, one key to providing workers with the best chance for survival is knowing where they are. “The most important thing is to have an overview of all personnel as soon as possible, because if we are missing anyone, we need to start looking for them. We need to know who they are and where they’re supposed to be, so we can search in the right area,” says an official at one oil-and-gas company who asks not to be named.
That’s one reason why wireless personnel location awareness systems designed to improve worker safety have been getting a more serious look lately by many multinational industrial companies. “I think the industry has been gradually awakening to the need for this sort of technology for some time,” says Doug Woodbridge, head of sales and marketing at S3 ID Group Ltd., a Rotherham, United Kingdom-based provider of personnel location awareness systems to the offshore oil-and-gas industry. He cities growing regulatory pressures worldwide among the drivers. And Woodbridge reports too that interest in his company’s products “shot up immediately” following the Deepwater Horizon incident.
Where are they?
Sometimes called real-time location systems (RTLS), personnel location awareness technologies typically rely upon active radio frequency identification (RFID) tag transponders worn by workers, contractors and visitors. The locations of these people can then be determined in real time, thanks to RF sensors mounted within a plant or industrial complex that receive signals from the tags. Associated software calculates the locations and manipulates the data for mapping, report generation and other functions.
For use in hazardous, explosive environments, the tags and sensors must be certified intrinsically safe. And while Wi-Fi (for Wireless Fidelity) is sometimes used, systems designed for industrial use often deploy ultra wide band (UWB) transmission technology, because of its ability to work well in dense metallic environments. UWB is also more accurate than competing technologies, and can often pinpoint worker tag locations to within inches, and in three dimensions, proponents say.
For outdoor applications covering large areas beyond preassigned zones, Global Positioning System (GPS) satellite technology can also be used, with typical location accuracies to within 50 feet. The Dow Chemical Co., Midland, Mich., uses GPS technology to help ensure the safety of remote workers along 4,000 miles of Gulf Coast pipeline, for example (see “Dow Employs GPS for Pipeline Worker Safety”).
Some location awareness systems are designed to track people’s movement between zones, with tags being read as employees pass sensor antennas located at doors and other choke points. In case of a safety emergency, these systems can count and locate thousands of people in real time as they assemble at muster points or evacuation areas, enabling timely knowledge of the identity of workers who are accounted for, and of those who may still be missing.
Privacy concerns
Systems can also be set up to blanket a facility with enough sensors to provide continuous monitoring of tag wearers, whose locations can be displayed in real time on computerized maps and satellite photographs of the site. Workers sometimes raise concerns that such tracking technologies represent an invasion of their privacy. But these concerns can typically be allayed, vendors contend, when an organization makes clear that a system is being installed for safety purposes, and not for “Big Brother”-style employee monitoring.
If an emergency occurs, this technology could mean the difference between life and death, proponents say, by providing rescue personnel with the exact locations of missing workers, thus saving valuable search time. The technology can also prevent the need to unnecessarily send rescuers into dangerous areas to search where no workers are present.
The Pohang Iron and Steel Co. (POSCO), a South Korean steel producer, for one, uses a UWB-based system with technology supplied by Ubisense Ltd., Cambridge, United Kingdom. The system monitors more than 500 workers as they move throughout hazardous areas of a steel plant in Pohang. And voestalpine, an Austrian steel manufacturer, has been able to accelerate search-and-rescue time by nearly 100 percent at one of its plants, thanks to a pilot UWB-based RTLS supplied by Zebra Technologies that monitors employees working around dangerous blast furnaces.
Among other things, location awareness systems can also be used for access control, providing automatic notification and alarms when employees, contractors or visitors enter dangerous or restricted areas without proper permits or authorization. Systems can be programmed to automatically lock and unlock doors, for example, and perform other functions such as turning off lights when workers are not present.
Jumping in
As interest in RTLS technology increases, more vendors are jumping into the business. The list includes Lincolnshire, Ill.-based Zebra, which last September introduced its wireless Personnel Safety Solution (PSS) for locating workers in hazardous industrial environments; and Apprion Inc., a Mountain View, Calif., industrial wireless technology supplier, which rolled out its ION Location Application in February for wireless real-time tracking of both assets and personnel.
Likewise, industrial automation supplier Honeywell International Inc. is also planning an entry into the space. Its Honeywell Analytics unit in Lincolnshire, Ill., plans to add real-time location awareness and two-way wireless communication capability to its personal gas detectors worn by workers in the oil-and-gas, chemical, mining and other industries. “We’ve been doing a number of beta trials around the world, in Europe and the USA,” notes Patrick Hogan, a Honeywell Analytics vice president. Initial versions of the product are expected to be commercially available by the end of April, according to Hogan.
As vendors move into the business, most concede that the market for personnel location awareness is still in an early adoption phase. Given the safety advantages of the technology, “you would imagine that health and safety personnel in large organizations would be aware of this possibility,” says Euro Beinat, vice president of location solutions at Zebra. “But that awareness is still not there to the level that you would expect,” he notes, adding that continuing educational efforts are needed. Once companies learn about the technology, “it’s an eye opener,” which is typically “followed up by action,” Beinat contends.
Perhaps the largest penetration of personnel location awareness systems to date is for use on offshore oil-and-gas platforms. S3 ID has systems deployed on about 20 platforms around the globe, according to Woodbridge.
One offshore operator that is using the technology is the Norwegian energy company, Statoil. The company operates three production platforms in the Statfjord field, some 80 miles off the coast of Norway. And in 2006, with the safety of its personnel in mind, Statoil set out to improve its emergency preparedness across its Statfjord A, B and C platforms. One key aspect focused on finding a better way to register personnel in an evacuation situation and keep the company’s Emergency Preparedness Management Team fully updated about an evacuation status in real time.
Statoil performs muster drills regularly on the platforms. At the time, the company was using a manual, paper-based muster system, by which workers notified an individual waiting at each muster site who checked off workers’ names as they entered their assigned lifeboats. This system enabled musters to be achieved within 20 minutes, in line with Norwegian legislation. But it was clear that this approach could become challenging during a crisis. Consequently, Statoil decided to replace the paper-based muster system with an Electronic Personnel Registration System (PRS) supplied by S3 ID.
“In the event of a crisis, we wanted to ensure safety was not compromised through failing to properly account for personnel, so that the search for those missing could take place faster, and at the same time prevent the risk of unnecessarily sending rescue teams into a danger zone to find those incorrectly marked as missing through human error,” observes Svein Thorsen, Statoil principal engineer. “PRS is not subject to human error under stress, which means you can rely on the data and counts you get in real time.”
Here, wear this
The S3 ID PRS system provides an automated way to register personnel during a platform muster. Active RFID transponder tags are issued to all Statfjord personnel at the onshore heliport when they arrive for work, and each transponder’s unique code is logged to the individual receiving it. The transponders, which are certified intrinsically safe, resemble a watch in size and shape, and are worn at all times to ensure that workers arriving at their designated muster stations are detected as they pass near PRS muster station antennas. Currently, about 3,200 tags are in use.
When a muster is initiated on a platform, each person is registered to the PRS database whenever the associated transponder is detected at the muster station. This enables real-time knowledge of the location of workers who have reached muster stations. Several PRS operator workstations are located on each platform and at the heliport. In the event of an incident, individual muster lists are available via PRS operator screens and on hardcopy reports.
The PRS has now been operational across Statfjord for more than three years and has proven highly effective in addressing the risks and reducing the possibility of human error associated with the previous paper-based manual mustering technique, according to Thorsen.
Further, the system has also produced business benefits for Statoil by improving productivity. Compared to the previous manual mustering system, the PRS has significantly reduced the time required to carry out these necessary exercises, allowing personnel to get back to work more quickly. Manual paper-based mustering techniques can also be time-consuming, both to administer and to generate post-muster reports. An electronic PRS does this automatically, providing measurable benefits by storing a full muster history and generating reports at the touch of a button.
“The PRS system is now an important part of our emergency preparedness precautions in Statfjord,” Thorsen concludes. “We at Statoil look forward to many more years of safe operation at Statfjord, and while we hope the PRS system never has to be used in a real crisis, it is reassuring to know it is there.”
Does safety pay?
For industrial end-users, the investment required for a personnel location awareness system can vary widely, depending on the scope of coverage and the technology deployed. Industry sources typically put the cost for a basic, RFID-based starting-level system designed for simple personnel check-in or mustering in the range of $100,000 to $200,000. And for Wi-Fi-based systems, the cost of a starting bundle can be less than $100,000 for companies that already have a Wi-Fi infrastructure in place. But for more capable UWB-based systems designed for full-fledged, comprehensive coverage of large areas with full location awareness of large numbers of people, the price tag can easily run into the millions of dollars, vendors confirm.
Few manufacturers or other industrial companies would admit to not doing all that they can to ensure the safety of their employees. But some vendors point out that one big factor holding back the growth of industrial personnel-focused RTLS involves cost.
“It always seems to be difficult for companies to generate a return-on-investment (ROI) calculation in people safety that satisfies their investment objectives,” observes Terry Phebey, sales vice president at Ubisense, the U.K.-based UWB technology provider. Unfortunately, as a result, many personnel location awareness projects fail to move forward, Phebey says.
Zebra’s Beinat notes that RTLS investments are typically easier to cost-justify when the technology is used for asset-focused applications such as inventory control or component tracking on production lines. “There’s an entire section of our business that supplies the automotive industry, and we’ve got plenty of evidence for ROI using exactly the same kind of [RTLS] technology, but it’s used for asset management and production support instead of safety,” Beinat points out.
Consequently, Beinat suggests that companies considering RTLS investments may want to look at infrastructures that can serve both asset management and worker safety. But at the same time, he says, there is a growing case to be made on the safety side alone.
Recent incidents including the BP Texas City Refinery explosion that killed 15 worker in 2005, as well as others in the oil-and-gas and chemical industries, have raised awareness of safety issues, and have caused more organizations to begin looking for ways to radically improve worker safety in their plants, says Beinat.
Traditional safety approaches—ranging from personal protective equipment to behavioral safety methodologies and various systems to measure and report incidents—have all been effective. But these approaches seem to have “plateaued” recently in moving manufacturers toward their goal of achieving the so-called “zero-incident workplace.” Real-time location awareness systems can produce the radical improvement in safety that many manufacturers are looking for, Beinat believes, and hold potential to be “a game changer for safety.”
Falling prices should also play a role in pushing manufacturers toward wider use of real-time personnel location technologies, says Doug Donzelli, chief executive officer at Apprion. Several vectors have recently come together that are quickly making wireless real-time location tracking a more viable option, he says. These include the development of radio technologies that are both ultra-low power and low cost, along with the ability to support multiple types of location tracking on a single physical unit.
Apprion’s newly introduced ION Location Application includes personnel tags that support both Wi-Fi and RFID transmission technologies, for example, in a form factor that is rated Class 1, Division 2 for use in hazardous environments, all for a price of less than $200 per tag, says Donzelli. Subsequent versions will support other technologies, including UWB and satellite, as well as an ability to track human biometrics such as heart rate and respiration.
Donzelli notes too that other trends also point toward wider use of personnel location technologies. With the Obama administration providing higher levels of funding for the Occupational Health and Safety Administration (OSHA), “there has been an increasing sensitivity to safety compliance that maybe wasn’t there in prior administrations,” Donzelli says. “Plus, when you take into account the nature of accidents that have occurred, people are pretty sensitive to work safety in a way that maybe they weren’t as much in the past.”
These factors, combined with declining costs for RTLS technology, will make it increasingly difficult for companies to resist putting safety-based location-tracking systems in place, Donzelli figures. “As the price comes down,” says Donzelli, “the question becomes not, ‘Should you do it?’ It becomes, ‘Why didn’t you do it?’ ”
March 2010, Related Whitepaper – Guidelines for use of wireless instruments for valve monitoring
To read the feature article, visit http://www.automationworld.com/whitepaper-6785
April 2011, Related Feature – Dow Employs GPS for Pipeline Worker Safety
To read the feature article, visit http://www.automationworld.com/feature-8577
Companies in this Article
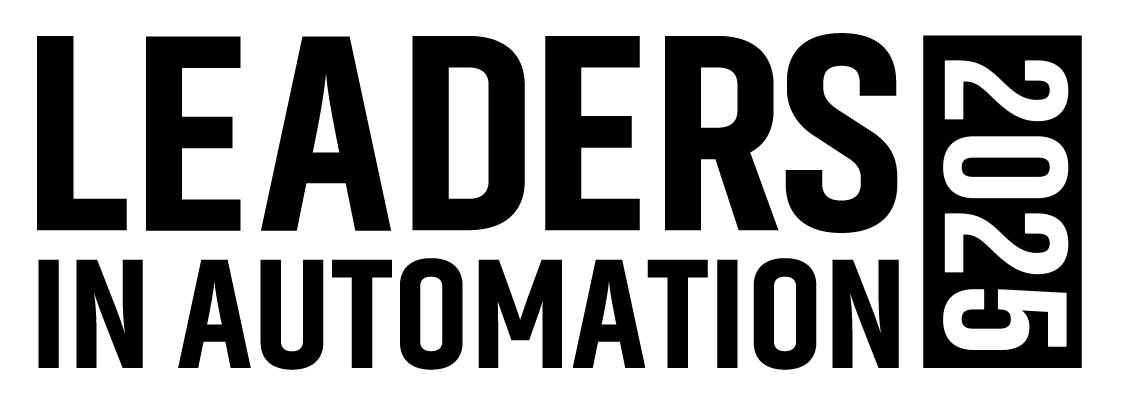
Leaders relevant to this article: