Sustainable has become a coveted buzzword in business and manufacturing circles, even though an exact definition is elusive. There are elements taken from the “green” movement of doing things that are friendly to the environment. It can be seen as one of the principles of the Lean Manufacturing movement—the elimination of waste. It’s a phrase often found in corporate annual reports. But, what is it?
In practical application in manufacturing, its effect manifests itself in activities such as reducing the amount of energy or utilities—electricity, oil, water—consumed in production, seeking alternative energy sources such as re-using waste heat, using power from solar or wind sources, recycling or otherwise reducing material use.
Bentley Prince Street Inc. is a sustainable commercial carpet manufacturer based in City of Industry, Calif. It has been implementing sustainable strategies since 1994 in an effort to reach its Mission Zero goal, which is to eliminate any negative impact that the company has on the environment by the year 2020. It is part of the Interface Group that was profiled in the 2009 Automation World article on sustainability, which can be found at www.automationworld.com/feature-6671.
The company posted on its blog a recap of its sustainable journey, just to show the seriousness of the commitment. “Today, 16 years after we began our climb up Mt. Sustainability, we are only a decade away from reaching the top. Since beginning our journey towards sustainability in 1994, we have undoubtedly made significant progress towards achieving our sustainability goals. We have reached numerous milestones in our progress, and it is important to realize, reflect upon, and celebrate each of these as we look forward to the path that lies ahead. The milestones we have achieved together provide us with encouragement, lessons learned, and a sense of accomplishment as we stand right on target to meet our Mission Zero promise in 2020.”
Kim Matsoukas, sustainability manager at the firm’s City of Industry, Calif., plant is a relative newcomer in a company that prides itself on keeping people for the long term. “I’ve just been here five years,” she notes, “and from the beginning, I’ve heard stories about the successful projects and top management commitment to sustainability. I think it takes that real commitment from the top. Sustainability can’t be the next ‘flavor of the month’ fad. And the commitment here has never wavered, not even during this recession. They have done a lot to integrate sustainability into the culture.”
Matsoukas is one of two full-time program managers for sustainability. They manage all the programs, provide reporting of progress and provide education. “We conduct quarterly education sessions, external education programs and events for associates,” she adds. “Some programs are ingrained. For example, one full-time person is employed on the factory floor to handle the recycling program. That person hauls scrap to bins, empties the bins, calls the recycler when needed and so on.”
Plant personnel conduct monthly waste audits. In the half-hour it takes, they pull out of trash bins everything that should have been recycled. The items are counted and weighed. “This helps maintain momentum and it educates new people,” Matsoukas says.
Some people talk about bottom-line managing, but Paul Nowak, general manager at Proteus Packaging in Franklin, Wis., says that his company uses the “triple bottom-line.” The company not only evaluates profits, it also uses people and planet metrics when evaluating success. “We’re not here to talk politics, we’re here to talk business” is the mantra at Proteus.
Proteus offers paperboard packaging solutions for clients in the pharmaceutical, food, nutritional, health and beauty, and automotive industries. Its management team has taken sustainability to a high level, from recycling virtually all of its inks and paper waste to retrofitting its plant with ultra-energy-efficient heating and cooling systems. Earlier this month, it received “chain of custody” certifications, which link the paper fibers used in Proteus’ packaging to responsibly managed forests.
Nowak also heads up the sustainability program. “Early on, we saw some environmental problems and questioned how our material was handled. Then, some customers working with the Wal-Marts and Targets of the world began pushing us. That’s when we realized a ton of opportunities for us as a company for global presence,” Nowak says. “We focus on workable pieces or buckets. The initial focus was on recycling and how to sort raw material to prove to third parties that it came from a sustainable source.”
Management began working on new buckets. “Now we also focus on energy,” Nowak says. “There are lots of cross functional teams—one on electrical includes the main electrician, maintenance manager, myself and even pulls in Wisconsin Energy. We look at how to drill down to help the environment and the business. We look at off-peak starting, set-backs for thermostats, sensors on lights, and we’re looking at cutting peak times.”
Top-down support
Nowak went to the owners early on believing that if the program was not supported at the top, it would never succeed. “Once we realized they had bought in to the program, then it became easier. The first team was all procurement. Then the program evolved organically. As customers asked how we were getting raw materials, we already had something in place to show them. You need to pick teams wisely. Members must have time to devote.”
Are these companies unique, or are they representative of U.S. manufacturing as a whole? Allen Avery, an analyst with ARC Advisory Group Inc., in Dedham, Mass., reports on a survey conducted by the analyst firm recently.
“We had 125 executives respond to our survey on energy management, and came away with a number of interesting insights into the topic,” Avery says. “Energy management in these corporations was well integrated with automation and operations. On the other hand, we heard much more talk about energy management during the recession and less now that the recession is ending. Regarding the survey, only a quarter of the companies either have not implemented energy management initiatives or don’t know.”
The survey revealed that most companies have someone responsible for the energy management program. Automation and controls personnel are usually part of the energy management team. Most companies are gathering information, although most only do so periodically (52 percent) while only a quarter are set up for continuous monitoring of energy usage.
“About a third of the respondents report tying energy to each product, so there’s room for improvement there,” Avery adds. Also, few give operators energy-related key performance indicators (KPIs). “A culture needs to be established from the top down,” concludes Avery, “with a holistic approach to assure that people and processes are in place where needed, with technology to back it up.”
Boilers are a huge energy user and now are a prime target for automation used to reduce consumption and improve efficiency. The following story is an example of this.
Sasol Solvents Germany GmbH awarded a contract to Honeywell Process Solutions, the Phoenix-based automation supplier, to upgrade the distributed control system (DCS) and programmable logic control (PLC) systems at Sasol’s gas-fired power plant in Moers, Germany, with installation of Honeywell’s Experion Process Knowledge System (PKS) and Safety Manager. The upgrades are part of an ongoing project that will see Honeywell’s process solutions become standard throughout the site, a move that Sasol hopes will significantly boost energy efficiency and reduce ongoing maintenance costs.
Situated near Germany’s industrial region of Ruhr, Sasol’s Moers power plant generates steam for the adjoining solvents manufacturing plant. The new operating environment will run off a universal network and interface, improving management by allowing operators to access the same system from any operator station on the Moers site.
“A large proportion of the Moers site is already controlled by Honeywell technology, so when the time came to upgrade the remaining systems, Honeywell was the natural choice,” says Christian Kramer, D. Eng., manager, Technical Service Electro, Instrumentation and Process Control, for Sasol Solvents. “With the new system in place, we will be able to streamline production and greatly improve the site’s energy efficiency.”
*****************************************************************Case Application: Gear Manufacturer Finds Savings
Energy Management: Tips for Packaging Machinery OEMs
*******************************************************************
Kramer continues, “Some projects started years ago, and we expect to do more next year. This project is at the power plant where we incorporate the new DCS for boiler efficiency calculations and utilization. At start-up of steam generation, it’s aware of efficiency of the boiler to produce steam. Another aspect of the project is to identify the cost of steam. It’s also important to have control functions like more complex logic to monitor the production situation and be able to detect if steam from the chemical plant is missing. Then we can automatically fire up boilers in order to keep steam on a constant pressure.
“The power plant DCS can collect all energy data, steam, nitrogen, electricity and water, and transfer to the process data management system. This will generate lots of ideas in the future for more ways to reduce energy use and cost. Our system can also be used for heating private households in the city via a connection to the district heating grid because it’s more efficient to use steam from our gas-fired boilers for peak loads than the city’s that uses biomass or coal-fired boilers.”
Sasol was faced with its old DCS being phased out, so it had to upgrade. But it discovered that there were many benefits to a newer system. It improved steam balance from its boilers—it has two large and two smaller ones. In fact, managers discovered that they could shut down the smaller boiler and run the remaining three at a more efficient level, reducing maintenance and energy costs due to steam utilization from the chemical plants. The new technology including a Profibus interface enabled a better interface to existing turbogenerators, thereby the plant is a net producer of electricity.
Furnaces, like boilers, are huge energy consumers. Manufacturing glass requires high temperatures, with much of the generated heat lost after it has served its purpose in the process. But Siemens AG, the Munich, Germany-based automation giant, has developed a process for recovering heat from the exhaust from glass furnaces that would otherwise escape through the stack unused.
Siemens’ Reinhold Selz, in Berlin, says that gas furnaces normally have flue gas at around 500 degrees Celsius to 600 degrees Celsius exiting the furnace. The system can use gas from 400 C to 600 C at between 10,000 cubic meters per hour to 100,000 cubic meters per hour, flowing into a boiler system to produce steam, which in turn generates from 1 megawatt (MW) to 3 MW of electricity.
“I’m responsible for the glass industry as a whole,” adds Selz. “We don’t want to just see a waste heat recovery solution, but to have an integrated solution that solves larger system problems.” Siemens supplies turnkey solutions, taking entire responsibility not only for electrical, but for the whole system. In that way, it can integrate its PCS7 control system across the plant in order to gain efficiencies.
As far as financial benefits, Selz says that a 3-MW plant can have savings of about 2 million Euros in the glass industry when the system can generate about half of the electric power required for production.
Sometimes, you need to go back to the product design stage to begin a sustainable manufacturing analysis. The Fred Sparks Design firm in St. Louis, works with clients for a thorough analysis of the product. Kent Ritzel, chief operating officer at Fred Sparks, says, “We worked with our client, Schutt Sports, initially to redesign the packaging for its collectable mini-football helmet products. We wound up getting involved with everything from manufacturing to supply-chain issues.”
Using Sustainable Minds software from Sustainable Minds Inc., in Cambridge, Mass., Fred Sparks designers evaluated the entire bill of materials. “We took a complete and thorough look at the bill of materials,” says Ritzel, “and then dug down to understand the process and material of each item. It was expressed in terms of end points and carbon footprint impacts, looking all the way back to the source. We looked at how the materials were manufactured and shipped all the way up the chain.”
Fred Sparks was able to quantify the impact on material elimination and innovative changes, and demonstrate that within the details of the Sustainable Minds assessment, they could actually provide a “win-win,” a better product for the consumer and a better product for the retailer—and at lower costs.
Dave Petroni, vice president of operations at Lehigh Technologies Inc., in Tucker, Ga., discusses yet another sustainable manufacturing approach—cutting out a large percentage of water used in production. Lehigh manufactures sustainable, micronized powders—varying from 400 microns to 50 microns in size—and sells them under the PolyDyne and MicroDyne brands. Raw materials used for production are post-industrial natural and synthetic scrap rubber. Think grinding up huge amounts of old tires—in itself, a sustainable practice.
“We have a next-generation technology featuring a patented cryogenic process that uses no water in the manufacturing process,” Petroni explains. “What sets us apart from competition is that instead of using grinders or milling machines, our process uses turbo mills that are much like a jet engine, sucking material in and spitting granules out the back. We use a lot of liquid nitrogen, up to six to seven tank wagons per day. The -320 degree Fahrenheit liquid nitrogen brings the rubber to embrittlement to a stage where it acts like glass before grinding. In order to be efficient, we use nested PID (proportional-integral-derivative) loops for temperature and efficiency in our Allen-Bradley ControlLogix [programmable automation controller]. Feedback comes using wireless sensors. This year, our plan is to make the process much more visual so that everyone can see what is going on in each area.”
Finally, electric motors in industry remain a leading consumer of the nation’s electrical power. Here is an example of how a company tackled reducing the cost of electrical consumption in its injection-stretch-blowing-molding process.
Engineering services provider Proplas International Ltd, fitted 13 of the packaging specialist’s Polyethylene-Terephthalate (PET) bottle and jar molding machines with Milwaukee-based supplier Rockwell Automation Inc.’s Allen-Bradley PowerFlex700 variable speed drives, helping to reduce energy consumption by more than 27 percent. From its base in Burnley, United Kingdom, Proplas International has built a reputation for helping industries—especially injection molding—to become more efficient.
The power usage on each machine before the modification was 40 kilowatts (kW), but with the drives retrofit, this has been reduced by 11 kW. The result is an estimated reduction in energy costs of more than £70,000 per year, with a payback period of less than 14 months.
The machines produce a range of bottles and wide-mouth jars in PET for the food and beverage industry. The injection-stretch-blow-molding process is used because of its capability to produce high quality containers. In the process, molten polymer first flows into the injection cavity to produce the desired preform shape. A period of conditioning at a set temperature follows, after which the preform is ready for stretching and blowing into the finished shape. The preform is transferred to the blowmold area, and the mold closes. A stretch rod is introduced to stretch the preform lengthways, whilst differential air pressure is used to blow the preform out to the shape of the mold. Finally, after a set cooling time, the mold opens and the finished container is removed. In practice, the four stages are carried out concurrently with a revolving carousel of molds.
Reduce inefficiency
Proplas director Stephen Anderson comments: “The machines were being driven by hydraulic pumps, with their motors set at a constant speed that would cater for the maximum hydraulic demand—the periods in the process where the molds are opening and closing. But this was an inefficient process, since the energy usage remains constant (and high) while the actual power demand varies.”
The Proplas solution was to fit variable speed drives to the pump motors, operating at two pre-set speeds—a higher speed during the maximum hydraulic demand when the molds are opening and closing, and a lower speed during the periods of reduced demand.
Manufacturers are developing many innovative methods for achieving sustainable manufacturing—from the design to the process to the supply chain. In the process, they are discovering untapped areas for efficiency and cost reduction.
March 2010, Automation Controls Energy Consumption
To read the feature article, visit www.automationworld.com/feature-6669
March 2010, Sustainability Leads To Next-generation Manufacturing
To read the feature article, visit www.automationworld.com/feature-6671
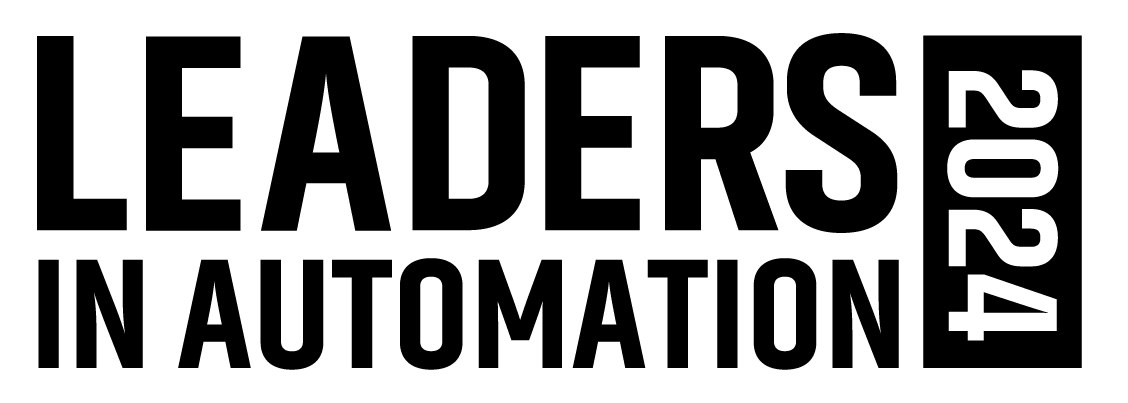
Leaders relevant to this article: