By now, it’s an old story. The integration of logic control and motion control is a mantra that has been touted and discussed in the discrete automation space for more than 20 years. And today, most agree, all of the talk has truly been transformed into reality.
“A couple of decades ago, everything was in its own little black box, and you had to do a lot of design to get everything to talk. There were latency issues with communication update rates and things like that,” observes Jeff Harrow, a project engineer with system integrator Matrix Technologies Inc., in Maumee, Ohio. “But a lot of that has been solved with the more tightly integrated systems they have today where all the control resides in one program.”
Indeed, as noted by Sal Spada, research director at ARC Advisory Group Inc., in Dedham, Mass., “the multi-box problem” has essentially been solved, with “every vendor on the market” now moving their product lines forward to offer even higher levels of integration and capability. Automation and controls suppliers these days are increasingly adding robotics and kinematics integration to the mix, for example, as well as integrated safety functionality.
The benefits of this integration are many, including significantly reduced time and cost to bring new machines to market, along with automation systems and machines that are more reliable and robust, require less maintenance and offer significantly more flexibility for end-users. In he future, Spada expects to see introduction of more engineering tools that provide analytical and modeling capabilities to support even faster deployment by original equipment manufacturers and machine builders.
As the age of integrated logic and motion control continues to mature, Automation World set out here to provide a look at how the technology is being deployed today in the field, along with the benefits to users. Following are four snapshot case studies that help tell that tale.
AEMK Systems
“When it comes to speed, the amount of mass that you have to move becomes very, very important,” observes Amir Khajepour, president of AEMK Systems Inc., of Waterloo, Ontario, Canada.
That’s one reason that the high-speed DeltaBot parallel robot developed by Khajepour at the University of Waterloo relies upon lightweight cables instead of rigid elements to control the movement of end effectors. The cable-actuated design enables speeds of more than 120 pick-and-place cycles per minute, with zero backlash and high accuracy, says Khajepour, who is also a professor of mechanical engineering at the school. Further, the use of cables brings cost advantages compared to conventional designs with arms made from rigid carbon fiber or other materials, he adds.
After filing a patent and forming AEMK in 2006 to commercialize the technology, Khajepour and company turned from the mechanical design to the question of the best way to control the DeltaBot. After trying various platforms, the company settled upon a CX1010 Embedded PC (personal computer) with TwinCat software from Beckhoff Automation LLC, Burnsville, Minn. The design also relies on high-speed EtherCat input/output (I/O) terminals and Beckhoff AX5000 EtherCat servo drives installed above the pick-and-place unit.
“The kinematics of parallel robots is complicated, and the first thing that we were looking for was a control system that is open enough that we could write our own kinematics,” says Khajepour. Further, AEMK wanted a small control footprint, as well as a system that had enough power and flexibility to provide integrated control of auxiliary system components. The CX1010 fit the bill, says Khajepour, because it could not only handle the robot control, but featured integrated logic and motion control for conveyors, cameras and other components needed. One DeltaBot turnkey system developed for an automotive inspection application, for example, uses a half dozen servo motors, with three conveyors, four or five cameras and a complex database for parts tracking, all running under the same controller, he notes.
“The Beckhoff system allows you to have the robot controller, and at the same time, you can run your logic codes—your PLC (programmable logic controller) codes—which is a huge benefit, because of instead of multiple controllers, you can have one,” says Khajepour. “You save money, you save space and it makes things much easier in terms of synchronization and timing.” Compared to alternative multi-controller approaches, the cost savings amounts to at least 40 percent, he estimates, while saving 70 percent to 80 percent in footprint requirements. High-speed EtherCat networking also reduces wiring costs as well as communication jitter, says Khajepour, an important consideration given that the fast-moving DeltaBot must complete most paths in less than 500 milliseconds.
Although AEMK wrote its own kinematics software for the DeltaBot, that’s a step that future robotic system developers may choose to forego when using Beckhoff controllers. That’s because Beckhoff recently released a kinematics software library for its TwinCat NC I software platform, facilitating robotics integration in addition to basic PLC logic and motion functionality.
Specialty Tooling
It was a tall order when a customer came to the engineers at Specialty Tooling Inc., an Evansville, Ind., machine builder. The customer—a major appliance manufacturer—wanted to improve the efficiency of a tube-bending process used to create refrigerator condensers.
The appliance maker’s existing process was based on hard tooling and pneumatics. But Specialty Tooling had a complete makeover in mind, based on intelligent servo drives. The machine builder selected the IndraMotion MLD-M (for Motion Logic in the Drive-Multiple axes) control architecture from Bosch Rexroth Corp., Hoffman Estates, Ill., for the task. The MLD architecture integrates motion logic and PLC control functions directly in the drive, rather than in a separate controller, and also includes SERCOS III (for serial real-time communications system) I/O and built-in Safety on Board with Safe Motion functionality. Programming is based on the International Electrotechnical Commission’s IEC 61131-3 standard.
The drive-based system enabled significant reductions in wiring compared to a traditional control platform using an external PLC, says Ryan Johann, Specialty Tooling automation engineer. The traditional approach would have required wiring the I/O points from the I/O cards in a separate controller to terminal blocks in the panel. Instead, Johann’s design relies on a SERCOS interface on the four-axis machine, with a single wire daisy-chained from drive to drive and out to the I/O blocks.
The approach saved about 25 percent on panel space and about 35 percent on wiring costs, Johann estimates, and resulted in a much cleaner panel layout, which should pay dividends on maintenance down the line. Because of the reduced complexity, he observes, “anybody can look at this and they’re not overwhelmed with communication cables, discrete I/O and everything else.”
The new platform also produced big productivity improvements for the appliance maker, eliminating the 60- to 90-minute hard-tooling changeover times. Machine operators can now change among four part configurations with the push of a button. “With the previous machines, they needed three machines on the line to keep up, but with our machine, [due to the faster changeover times], they actually need only one machine,” Johann says. Further, when part differences occur from one coil of steel tubing to the next, operators can often make minor tweaks using the system’s human-machine interface (HMI) to accommodate the variations, enabling the machine to keep running. “A lot of times in the past, when they would get a bad batch of parts, they would have to reject those parts, and it might have put them in a situation where they didn’t have enough parts for the particular product they were intending to run,” says Johann. “Now, they don’t have to mess around with changing schedules and things like that.”
An added productivity benefit for the customer comes with the Safety on Board safety technology integrated into the drives. Certified to various international safety standards, the drive-based safety platform allows an operator to enter the machine cell to load and unload parts without having to drop the mains voltage, eliminating the need for a complete restart.
“We set the system up so that if an operator enters the light curtain, we put everything into a safe stop. We effectively pause the cycle so it’s completely safe for the operator if they need to tweak something, or if something drops in there and they need to move it out of the way. And as soon as they exit the work cell, the system can resume from where it was,” Johann explains. “We found the afety on Board technology to be very useful.”
Drilling Technical Services
Drilling Technical Services (DTS), a Milford, Ohio-based machine builder, specializes in mechanical, electrical and process engineering for the narrow and mid-width printing industry. During a recent project for one global leader in label and filmic product solutions, DTS was commissioned to develop a mid-width web roll-to-roll die cutter with various unique and challenging substrate manipulation functions.
Every aspect of the work was to be done to the customer’s strict system specifications for equipment criteria, including die-cutting accuracy, line-speed accuracy, tension control and wound-roll precision. The contract offered a notable opportunity for DTS. The first machine was required from DTS on a short time schedule for the customer’s showroom, with a second machine to be provided to the initial end-user. But long-range plans call for the machine to be marketed worldwide by the DTS customer.
DTS uses controls technologies from various suppliers, says founder Joe Drilling. “But if we have the luxury of specifying, we use Siemens.” DTS follows a mechanical design method based on modular construction, and Siemens provides a range of electrical components that are well suited to support that modular approach, Drilling observes.
So it was that DTS selected the Simotion D435 motion controller from Siemens Industry Inc., Alpharetta, Ga., to achieve the accuracies required by the user as part of an “electronic line shafting” design for the machine. The D435 is a compact, drive-based platform that incorporates motion control, logic control and drive control in a single hardware unit. The drive-mounted D435, a mid-range product for up to 16 axes, was to be the control for the entire machine’s functionality. Feeding off this platform would be multi-axis control drives of the Siemens Sinamics family, as well as Simatic I/O components and runtime software, plus related HMI software.
Components for the machine were selected by DTS engineers using the Siemens Converting Toolbox, a suite of product specifications and application software that allows engineers to customize portions of a machine build, then recall or reuse them or make modifications for subsequent builds. The reduction in machine design engineering time was about 80 percent on the second machine, says Drilling, who anticipates similar savings on subsequent units.
That time savings was a hit with the customer, who had previously used another vendor for machine upgrades. That supplier typically took months to research, develop and implement design changes, says Drilling. “Having these [Siemens Converting Toolbox] tools available to us makes us look like heroes in front of our clients, because when they ask us to make changes or improvements, we’re able to make them rather quickly,” he observes.
In the end, the flexibility and precision afforded by the integrated control scheme and electronic line shafting approach enabled DTS to meet customer requirements for machine precision and accuracy. And the end-users of the machines will also profit from a variety of benefits, ranging from reduced machine maintenance to faster product changeovers.
For example, according to Drilling, “the HMI has a feature enabling the users to save the last settings for a particular product that was run through the machine, and the machine is capable of changing itself over, creating the tension zones needed for a particular product change.” On older machine designs that required mechanical adjustments to be made, such product changeovers might have required up to an hour of operator time, Drilling says. With the new design, by contrast, the changeover requires “two to three minutes, at the most.”
Curt G. Joa Inc.
My, how things have changed at Curt G. Joa Inc., a Sheybogan Falls, Wis.-based machine builder. Shortly after Curt G. Joa established an engineering company bearing his name in 1932, he applied for his first patent on an end-fold mechanism for an early sanitary napkin production machine. Today, while mechanical innovation is still important at the company, innovation in electronic machine control also plays a significant role.
The company, which specializes in custom-designed web converting machinery for major manufacturers of baby diapers, feminine sanitary napkins and incontinence pads, routinely builds machines that are up to 150 feet long and incorporate 100 to 150 axes or more of motion, says Kevin Zeinemann, Joa’s electrical engineering manager.
And as the axis count has grown, standardized programming has become key, Zeinemann observes. “Say, you’ve got a machine with 100 or more axes, and you’ve got 30 conveyers that are identical. You don’t want to rewrite that code every time, so what we’re looking for is a way of building up a block and basically dropping it in,” he explains.
It’s an approach that is available from each of Joa’s primary controls suppliers, including Bosch Rexroth, Rockwell Automation and Siemens, Zeinemann says. “I think it’s an industry trend that’s pretty relevant, that they’re all trying to tie all this [code block] functionality into a common programming software. And besides motion control and logic, [the software] also integrates safety, which all of these major suppliers are including in their integrated architecture tool kits.”
The benefits of today’s tools and broader integration can be seen in a job done by Joa for a customer who wanted to upgrade a 15-year-old converting machine that was outdated and becoming increasingly expensive to fix.
Among first steps, Joa upgraded the system’s servo drives to Allen-Bradley Kinetix 6000 multi-axis servo drives supplied by Rockwell Automation Inc., Milwaukee, and also upgraded the machine’s processor with an Allen-Bradley ControlLogix Programmable Automation Controller (PAC). As part of the Rockwell Automation Integrated Architecture, the ControlLogix PAC eliminated the need for a separate motion controller. Integrating high-speed discrete and motion capabilities on the same platform saved space, improved synchronization and reduced programming requirements.
Joa engineers also integrated an Allen-Bradley GuardLogix controller into the machine to perform all of the safety interlock functions. The controller features a two-processor architecture that allows integrated safety and machine control within a single platform. This helped minimize hardware costs because system components can be used by both the standard and safety portions of the application.
Additional changes involved replacing existing ControlNet and DeviceNet communication with Common Industrial Protocol (CIP).Related Feature: What's New in Integrated Logic and Motion Control, Vendors Respond.To Read this feature, visit www.automationworld.com/feature-8199
Subscribe to Automation World's RSS Feeds for Feature Articles
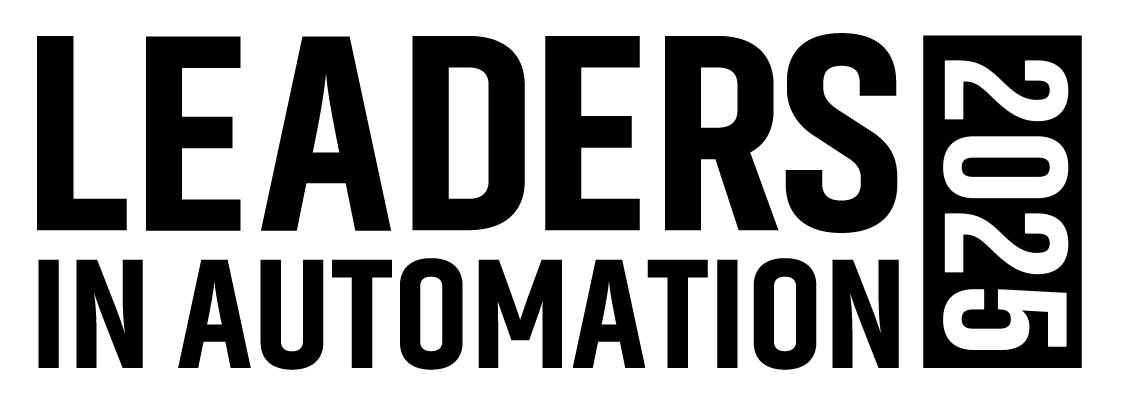
Leaders relevant to this article: