Chris Damsgard, a senior controls and information systems engineer at food maker General Mills Inc., in Golden Valley, Minn., tells a story about a usability study that the company recently conducted with employees on a particular software product. "We were asking the user to change a setting. This UI (user interface) had about 30 different settings on it, and we followed the user's mouse around the screen as we recorded it. The user's mouse circled the entire screen, and the check box they needed to change was sitting right in the middle, and they never even saw it," Damsgard relates. "Something that may be very obvious to the developer, because they built it, may not be obvious to the end-user, especially when they've got 30 different options staring them in the face."This anecdote illustrates an issue that is gathering a growing amount of attention these days in the industrial controls and automation space. Many of today's industrial products, with their ever-growing feature sets, have become too complex and difficult to use, leading to increased training costs and lost time, and in some cases, even robbing manufacturing companies of the very benefits that the features were intended to produce. But more vendors are beginning to take notice. Increasingly, as a way to differentiate their products and help customers become more productive, automation suppliers are stepping up their efforts to reduce complexity in their products and make them easier to use.One of the most visible is Emerson Process Management, Austin, Texas. The company launched its own Human Centered Design Institute last year, and is working to broadly integrate human-centered design (HCD) principles and methodologies throughout its product-design process. Other vendors, including ABB, Invensys Operations Management (IOM) and Rockwell Automation, among others, cite a growing internal focus on usability issues as well.Usability has always been important, says Jerry Cook, a software manager at Rockwell Automation Inc.'s Control and Visualization Business, in Mayfield Heights, Ohio. "But I think the recognition of how important it is has become clearer to the automation world in the last few years," observes Cook, who heads up a user-experience design team that aims to improve usability of Rockwell's RSLogix 5000 product line. Indeed, even manufacturers themselves are getting into the act. "We have projects going on in advanced visualization, and we've done work with some of our very largest customers," says Rob McGreevy, IOM vice president, platforms and applications. "And it's interesting to find that not only are we doing these sorts of user-centered design activities, but a lot of them are doing it as well." A converging set of challenges is driving the trend. Changing workforce demographics is one. As more experienced users retire and workforces are streamlined, fewer workers with less in-depth knowledge are being asked today to do more, and they often don't have time to learn or be trained on highly complex product feature sets. Add to that the fact that in many industries, process units and plants are becoming larger, while smarter instrumentation, sensors and other devices are all producing growing amounts of data. This calls for engineering, controls and maintenance tools that are more advanced, but also more complex. The result is that industrial end-users today may be faced with multiple product interfaces for an array of feature-laden products that often provide layer upon layer of functionality, requiring advanced knowledge for optimum results.Ask grandma: Meanwhile, new generations of highly usable consumer products are also fueling changing user expectations. "With software, we can make these things simpler. The [Apple] iPhone is proof of that," declares Damsgard at General Mills. "My grandma can use an iPhone. But my plant engineer, who's possibly got a master's degree, struggles to figure out how to use a trending tool. That's a big problem."Emerson Process Management's human-centered design initiative got its start about six years ago. At the time, research showed that despite many useful features being built into Emerson products, those features weren't being used as frequently as expected. In many cases, surveys revealed that the products were simply too difficult for time-strapped customers to figure out and use, says Duane Toavs, director of the company's Human Centered Design Institute. The company identified usability as a strategic imperative, and established a relationship with the Human Computer Interaction Institute at Carnegie Mellon University (CMU), in Pittsburgh, a recognized leader in the field of usability research. As an outgrowth of its work with CMU, the company formed its Emerson Human Centered Design Institute, a virtual organization with the goal of instilling a pervasive HCD knowledge throughout the company's design teams. The strategy involved formal HCD training for engineers and designers, as well as hiring a few high-energy HCD professionals, who would subsequently train and mentor others in the HCD discipline, says Toavs. Today, Emerson has a growing network of employees—currently numbering 70 to 80—who have been trained in HCD and who apply their skills in various product areas across some eight Emerson divisions, says Jay Elkerton, Emerson director of Human Centered Design.Some of the first fruits of Emerson's HCD initiative appeared late last year with introduction of redesigned instrument screens for more than 50 field devices, significantly improving their usability. The application of HCD principles also led to development of a new electronic marshalling scheme for Version 11 of the company's DeltaV distributed control system (DCS) that significantly reduces wiring requirements, lowering labor costs and improving start-up times for customers.Name game: Design-for-usability philosophies have been referred to variously over the years, with names including human-computer design, user-centered design and pervasive usability, among others. Rockwell, for its part, has lately settled upon "user-experience design," says Cook, to convey the idea that the field goes beyond just the human-machine interface to incorporate the whole vendor-customer relationship—from phone interactions to how easy a product is to unpack and use when it arrives at a customer location. But whatever name is used, the focus is on better understanding and meeting the needs of users.Emerson defines human-centered design as "an approach to interactive systems development that aims to make systems usable and useful by focusing on the users, their needs and requirements, and by applying human factors/ergonomics and usability knowledge and techniques." This definition is drawn from ISO 9241-210:2010, an international standard promulgated by the International Organization for Standardization (ISO). In HCD, some traditional product design techniques still apply. For example, customers still need to be interviewed about product needs and features. But HCD goes beyond that to encompass a range additional tools that help suppliers get "inside the heads" of users, and to understand how workers actually use a product and interact with other users."Human-centered design isn't just some check box where you've got some idea and you go hold a focus group. It's a whole discipline in which there are dozens of methods that make you much more attuned to your key stakeholders and what their true needs and desires are," observes Chris Pacione, director and chief executive officer of Luma Institute, a Pittsburgh company that provides HCD training and education. Luma has done multiple HCD workshops for Emerson since 2008, says Pacione, and the firm also lists Rockwell and Schneider Electric among clients.Pacione refers to three "meta-competencies" that make up the HCD discipline—looking, understanding and making—each with its own set of methods. Brian Jones, an Emerson product manager who focuses on HCD, calls the three steps research, design and evaluation, and notes that frequent iterations based on user inputs are key all along the way. "Before a product ever gets into that stage where the developers are going to be coding code, the product would have already been in front of users as some sort of prototype, whether it be paper, or an actual working software prototype, so that when we build something, we know it's going to meet the needs of users." As part of Emerson's initial user research, Emerson personnel made visits to 36 customer sites to observe users in their actual work environments, says Elkerton. In HCD terms, these are called "contextual inquiries," and they formed the basis for the creation of multiple user "personnas," which describe the jobs of specific types of users and how they use Emerson technologies. Likewise, "stakeholder maps" were created that show how users interact with each other. These tools can provide insights to functional roles and information needs, helping product designers to create interfaces that meet user needs by providing the right information at the right time, while also improving workflow and communication among people.For many Emerson HCD researchers who made initial visits to live control rooms, "it was a total surprise on the amount of noise that is around an operator in his daily job," notes Toavs. "The phone is ringing constantly, people are coming in that have to sign into the facility, [operators] are responsible for rounds that have to be made, they've got reports to fill out… These are things that were never really thought about before when [a designer] is sitting in a booth trying to build screens on a display for an operator," he says. Now, Emerson designers have the benefit of that added insight. Know thy user: In many cases, seeing customers actually use their interfaces can be a humbling experience for product designers. "A lot of times, usability testing is very insightful for developers who may believe they've got the best solution, but when they sit in a room and see someone trying to use it, struggle for 20 minutes and have no idea how to solve the problem that we put before them, it's really eye-opening," notes Rockwell's Cook. "We've got a button around here that says, ‘Know thy user, for they are not you.' "Other HCD methodologies can range from the highly sophisticated, such as the use of eye-tracking to measure and record the eye movements of users as they interact with a screen, to paper prototyping exercises in which users rely on scissors, paper and tape to show HCD researchers how they would place elements on a display for optimum usability. At Emerson, many of these techniques came together in the redesign of more than 50 Device Dashboards introduced late last year that were developed for the company's AMS Suite: Intelligent Device Manager software. Emerson developers relied on methods including job personnas and stakeholder maps, as well as low-fidelity prototyping sketches by users to come up with simplified information screens that match the way that field personnel do their jobs. Emerson identified the most common tasks performed in the field and designed screens that provide easy access to those tasks. At-a-glance status views and one-button shortcuts are among features designed to speed task completion for users.One of the changes noted by Toavs, for example, involves quick access to information for maintenance technicians. The tools are used for device configuration and commissioning, as well as for routine maintenance, but the original tool design focused on configuration, he says. For a maintenance tech, "when you're starting these things up, all you want to know is whether a device is working right away. So these quick indicators are really important," Toavs notes. "That sounds subtle, but there's 20 years of history of building interfaces for the configuration guy, and then completely ignoring the needs for day-to-day operation."In the end, according to Emerson, the HCD initiative is driving a fundamental shift in the way the company develops technology to meet user needs. Indeed, concludes a recent report from ARC Advisory Group Inc., Dedham, Mass., "Emerson has made a big step forward with the HCD approach and its investment in the Human Centered Design Institute. Now it must continue to build on its positive momentum and drive HCD concepts into its full suite of products."Related Sidebar - Eye Tracking to Measure the ImmeasurableTo read the article accompanying this story, go towww.automationworld.com/feature-7978.Related Sidebar - ABB Product Architecture Supports UsabilityTo read the article accompanying this story, go towww.automationworld.com/feature-7979.
Subscribe to Automation World's RSS Feeds for Feature Articles
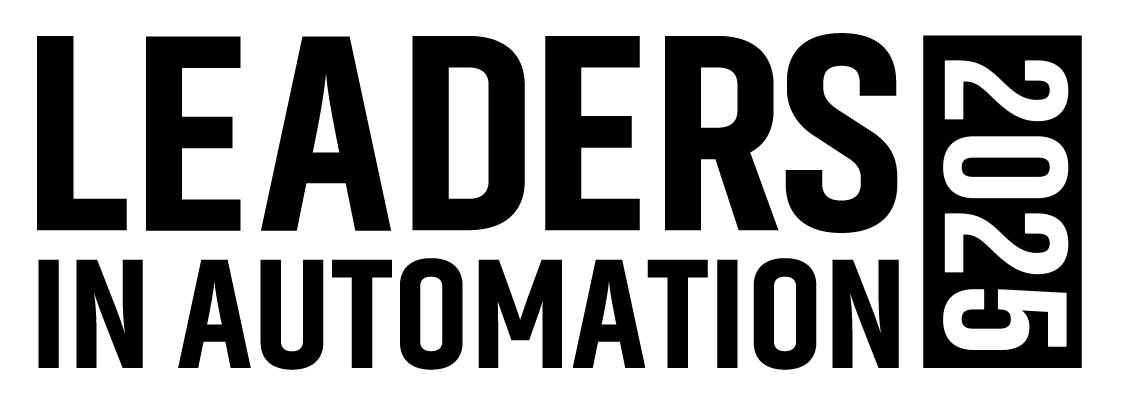
Leaders relevant to this article: