“I told everybody, ‘Run but stay low.’ Stuff was falling,” said Gwendolyn Sanders, one of 71 people hospitalized by an explosion that killed four people at ConAgra Foods’ Slim Jim meat processing plant in Garner, N.C., in June 2009. Cut seriously on the hand and arm, she had returned to the place where she worked for 10 years to look over the wreckage. The explosion brought down a large section of the building and led to the release of about 18,000 pounds of ammonia from the plant’s refrigeration system. A few days earlier, workers had been installing a new, natural gas-powered industrial water heater in an interior utility room, and one of them purged a new gas line before commissioning the heater. The purged gasses vented directly into the utility room where they gradually grew concentrated enough to combust, which they did, bringing part of the building down.Early in the morning of Oct. 23, 2009, a tanker ship in San Juan Harbor, Puerto Rico, was filling a tank at the Caribbean Petroleum tank farm with gasoline. There was a leak or overflow, leading to the formation of a large vapor cloud that duly exploded, leading to a chain reaction that quickly spread throughout the facility, which stored gasoline, diesel fuel, jet fuel and fuel oil in about 30 above-ground storage tanks. Property was damaged more than a mile away and it took authorities more than two days to put the fire out.Then, just weeks ago on April 2, six workers were killed and one injured in an explosion at the Tesoro Refinery in Anacortes, Wash., about 70 miles north of Seattle, following what the San Antonio-based company described as “routine maintenance.”Many investigations
These are not isolated incidents. As we mark the fifth anniversary of the BP Texas City explosion that killed 15 people and injured 180 more in March 2005, the accident reports continue to pile up. The U.S. Chemical Safety Board (CSB)—an independent government agency that investigates serious accidents and makes recommendations regarding safety legislation much like the U.S. Federal Aviation Agency (FAA) does for the aviation industry—has no fewer than 18 ongoing investigations (including a flash fire at a second Tesoro facility in Utah in the fall).This litany of disaster may leave one wondering if we have made any progress at all in terms of improving safety since the Texas City explosion, the worst refinery accident in the United States in 10 years, which cost BP $50 million in fines and $1.6 billion in compensation (so far). The refining industry, in particular, is in the hot seat, with almost half of those aforementioned CSB investigations centered on incidents at refineries.According to John Bresland, chairman and chief executive of the CSB, refinery accidents continue to occur throughout the industry “with dismaying frequency.” These accidents take lives, disrupt communities and threaten the nation’s flow of gasoline and other refined oil products.“This is a significant and disturbing trend that the refining industry needs to address immediately,” says Bresland. “These accidents will only stop when every refinery has made the financial and human commitment to sound process-safety management.” But is the process safety situation actually getting worse, or do we just have a heightened visibility into these incidents? “It’s hard to say if process safety is improving or if it’s getting worse,” says Mike Boudreaux, DeltaV SIS Product Manager for Austin, Texas-based controls vendor Emerson Process Management. “There is increased visibility because [organizations such as] the CSB have been doing a lot of work to investigate things [and are publicizing their findings].”For example, the CSB maintains a rolling ticker of ongoing investigations on its Web site, has a dedicated YouTube channel and sends regular updates via Twitter. This is a good thing because it facilitates a greater level of information sharing. For example, the CSB posted a one-hour video called “Anatomy of a Disaster”—which provides a detailed breakdown of events leading up to the Texas City accident. Bresland urges people to spend a lunch hour watching it with colleagues and ask themselves, ‘Are any of these things happening at my plant?’ ”If nothing else, news cycle level visibility of these accidents and the detailed reports of organizations such as the CSB combined with increased demands of legislation of the type the CSB recommends, along with evolving safety standards, has led to a sharp increase in demand for Safety Instrumented Systems (SIS)—i.e., process systems that are safety-rated, or pure safety and security systems. ARC Advisory Group Inc., Dedham, Mass., predicts that the market will grow at a compound annual growth rate of about 12 percent to reach $2.5 billion in 2012, despite the recent economic downturn. “From a vendor perspective, I know that our customers are spending heavily on process safety,” says Boudreaux. “And they are adopting the latest standards.”Start with reading“I’m less and less pleased with what I’m seeing,” says Paul Gruhn, a training manager at ICS Triplex, a safety systems supplier, in Houston. Gruhn is also member of the SP84 Committee of the International Society of Automation (ISA) that wrote the safety systems standard, an ISA Fellow and developer of the world’s first safety software modeler system. He also developed and instructs ISA safety courses and is the primary author on the ISA book on the topic. “A lot of the places I go, I am seeing an extreme lack of knowledge. Unfortunately, I see things getting worse before they get better.”One of the primary problems, says Gruhn, is the lack of safety-related knowledge at end-user companies. If end-users haven’t read the standards and don’t know how they apply to their particular operations, then they can’t possibly know what they are going to need, and they can’t write complete and knowledgeable specifications.The obvious and easy solution to this problem is training, and many organizations—including both vendors and industry groups such as the ISA—offer quality training options. For example, the Board of Certified Safety Professionals, in Savoy, Ill., offers certification in 16 different safety practices, ranging from ergonomics to fire prevention. There are about 200 independent safety certifications available in the United States alone.Charlie Fialkowski, a safety expert at Alpharetta, Ga.-based supplier Siemens Industry Inc., has seen a significant push throughout the process industry to improve the general level of competency with regard to safety. “The standards tell you that decisions should be made by ‘competent’ individuals, but that term is used loosely. So education programs have come up to help qualify people to do the work.”Fialkowski refers to the CFSE (certified functional safety expert) program—a non-profit organization that is geared to certifying people, the FSE (functional safety expert/engineer) program, and the ISA itself, for which, like Gruhn, Fialkowski is a trainer. “I also know some of the safety programmable logic controller (PLC) manufacturers out there offer free workshops on how to apply best practices techniques on applying the standards. So there is a lot of education available. When I got my CFSE five years ago, there were a few dozen of us. Now, there are more than 500, so you can see the trend.”“Our major customers all have dedicated safety engineers. They all know the standards and know what they are looking for. The others, many of them, especially the smaller businesses, have less knowledge and therefore, it’s very difficult for them to pick a system that meets their needs,” says Erik de Groot, global marketing manager for Safety Management at Phoenix-based supplier Honeywell Process Solutions.Safety coursesThus, Honeywell uses numerous means, ranging from detailed surveys and questionnaires to in-depth, vendor-neutral safety courses covering topics such as standards, to try to work with customers on safety issues.Adds de Groot, “Customers are often wading through the confusion about what these standards mean, and that can hold them back. It’s about making sure the customer is educated. This is the cost of doing business. It’s the job of companies like Honeywell to help customers understand what they need.”After training comes the systems themselves. Almost all of the process automation vendors offer some kind of SIS. These systems are universally standards-compliant, and when combined with “competent” staff, can help a manufacturer meet safety requirements. The latest research and development (R&D) advances apply an evolution that has been gradually permeating the automation industry as a whole: the continued introduction of intelligence to all levels of the operation, and then the use of that intelligence for greater control and more informed decision-making. Siemens calls this Totally Integrated Automation, but Siemens isn’t alone. For example: Emerson has PlantWeb and other vendors are doing the same thing. In keeping with this approach, Emerson’s DeltaV SIS is an extension of PlantWeb, covering the safety system, the field devices and control valves, plus integrating with the process automation system, plant asset management system and other elements of plant automation.Whatever system you install, Art Pietrzyk, segment manager for critical control and process safety for vendor Rockwell Automation Inc., Milwaukee, stresses that this is just the first step. “Technology alone can not make things safe. In fact, it gives us a false sense of safety.” Pietrzyk gives the example of a car’s emergency brake. You don’t know how the emergency brake is going to work until you use it, unless you test it on a regular basis. Safety integrated systems are the same. “It’s not enough to merely have a system. In the process world, the safety system is a low demand system. You can go for years without that systems being activated. You have to go back periodically and do a proof test, make sure the system works, the sensors are sensing and valves are working.”This is where intelligence comes into play. “Newer technologies provide more than a mere connection to the device but include intelligence in the device itself. This makes it an instrument rather than merely a device, and allows us to do things like predictive maintenance.”This intelligence is an important building block in the safety process lifecycle. “People are starting to realize that when the standard calls for a safety lifecycle, there’s more to compliance than just using a certified safety system,” says Luis Duran, business development manager for safety systems, Americas, for supplier ABB Inc., in Houston.Critical stepsDuran identifies four critical steps in the life of a safety process: 1. Analysis. What are the risks and how can they be mitigated?2. Safety System/Process Design. With the assessment complete, you can design the best system for you and ascertain how it will be used and maintained, and what other risk mitigation processes that may be required. Says Duran, “This is where people are realizing that it is more than just buying and installing a system. How often does the system need to be maintained? How will you proof test it?”3. How do we actually run the system? There is a lot more emphasis on the operational maintenance today than in the past. 4. End of life and replacement. Adds Duran, “Some of the incidents that have happened in the process industry are a result of failures to properly proof test and maintain the system. For example, if you look at Texas City, you can’t point to one failure. Numerous things went wrong.” In the intervening years, BP has accepted that human error was a factor in the explosion. Additionally, several level indicators failed, leading to overfilling of a knock-out drum, and light hydrocarbons concentrated at ground level throughout the area which were, in turn, ignited by a truck that was left running nearby. But will lessons learned at the cost of lives lead to improvements? The systems are better, the standard of related education has improved and manufacturers are spending money on the issue, so one has to be positive. However, some managers persist in the belief that increased safety systems will slow down production and cost money—a position that Gruhn of ICS Triplex says is patently ridiculous. Production efficiency actually improves when you do safety properly because you have more control and intelligence about how your operation is set up and running, says Gruhn. By way of example, he points to the Occupational Safety and Health Administration’s (OSHA) introduction of the PSM Process Safety Management of Highly Hazardous Chemicals standard (29 CFR 1910.119) regulation. In the years since, reports indicate that the number of accidents has gone down by more than 20 percent, and companies are reporting that their productivity has gone up.And that’s before the cost of an incident is factored into the equation. Texas City has cost BP more than $2 billion so far. When all is said and done, the 2005 Buncefield Depot explosion in Hertfordshire, United Kingdom, will cost operating companies Total UK Limited and Hertfordshire Oil Storage Ltd around £700 million. The first impact of the most recent Tesoro incident was felt as quickly as the following trading day, as Tesoro’s stock price fell 6 percent. Says Bresland, “When will we know whether the tragedy of 2005 has resulted in greater safety at BP and other companies’ refineries? Only when we can look back over a significant number of years without major accidents, deaths or injuries.”For additional safety organizations and links, go to www.automationworld.com/feature-6994.
These are not isolated incidents. As we mark the fifth anniversary of the BP Texas City explosion that killed 15 people and injured 180 more in March 2005, the accident reports continue to pile up. The U.S. Chemical Safety Board (CSB)—an independent government agency that investigates serious accidents and makes recommendations regarding safety legislation much like the U.S. Federal Aviation Agency (FAA) does for the aviation industry—has no fewer than 18 ongoing investigations (including a flash fire at a second Tesoro facility in Utah in the fall).This litany of disaster may leave one wondering if we have made any progress at all in terms of improving safety since the Texas City explosion, the worst refinery accident in the United States in 10 years, which cost BP $50 million in fines and $1.6 billion in compensation (so far). The refining industry, in particular, is in the hot seat, with almost half of those aforementioned CSB investigations centered on incidents at refineries.According to John Bresland, chairman and chief executive of the CSB, refinery accidents continue to occur throughout the industry “with dismaying frequency.” These accidents take lives, disrupt communities and threaten the nation’s flow of gasoline and other refined oil products.“This is a significant and disturbing trend that the refining industry needs to address immediately,” says Bresland. “These accidents will only stop when every refinery has made the financial and human commitment to sound process-safety management.” But is the process safety situation actually getting worse, or do we just have a heightened visibility into these incidents? “It’s hard to say if process safety is improving or if it’s getting worse,” says Mike Boudreaux, DeltaV SIS Product Manager for Austin, Texas-based controls vendor Emerson Process Management. “There is increased visibility because [organizations such as] the CSB have been doing a lot of work to investigate things [and are publicizing their findings].”For example, the CSB maintains a rolling ticker of ongoing investigations on its Web site, has a dedicated YouTube channel and sends regular updates via Twitter. This is a good thing because it facilitates a greater level of information sharing. For example, the CSB posted a one-hour video called “Anatomy of a Disaster”—which provides a detailed breakdown of events leading up to the Texas City accident. Bresland urges people to spend a lunch hour watching it with colleagues and ask themselves, ‘Are any of these things happening at my plant?’ ”If nothing else, news cycle level visibility of these accidents and the detailed reports of organizations such as the CSB combined with increased demands of legislation of the type the CSB recommends, along with evolving safety standards, has led to a sharp increase in demand for Safety Instrumented Systems (SIS)—i.e., process systems that are safety-rated, or pure safety and security systems. ARC Advisory Group Inc., Dedham, Mass., predicts that the market will grow at a compound annual growth rate of about 12 percent to reach $2.5 billion in 2012, despite the recent economic downturn. “From a vendor perspective, I know that our customers are spending heavily on process safety,” says Boudreaux. “And they are adopting the latest standards.”Start with reading“I’m less and less pleased with what I’m seeing,” says Paul Gruhn, a training manager at ICS Triplex, a safety systems supplier, in Houston. Gruhn is also member of the SP84 Committee of the International Society of Automation (ISA) that wrote the safety systems standard, an ISA Fellow and developer of the world’s first safety software modeler system. He also developed and instructs ISA safety courses and is the primary author on the ISA book on the topic. “A lot of the places I go, I am seeing an extreme lack of knowledge. Unfortunately, I see things getting worse before they get better.”One of the primary problems, says Gruhn, is the lack of safety-related knowledge at end-user companies. If end-users haven’t read the standards and don’t know how they apply to their particular operations, then they can’t possibly know what they are going to need, and they can’t write complete and knowledgeable specifications.The obvious and easy solution to this problem is training, and many organizations—including both vendors and industry groups such as the ISA—offer quality training options. For example, the Board of Certified Safety Professionals, in Savoy, Ill., offers certification in 16 different safety practices, ranging from ergonomics to fire prevention. There are about 200 independent safety certifications available in the United States alone.Charlie Fialkowski, a safety expert at Alpharetta, Ga.-based supplier Siemens Industry Inc., has seen a significant push throughout the process industry to improve the general level of competency with regard to safety. “The standards tell you that decisions should be made by ‘competent’ individuals, but that term is used loosely. So education programs have come up to help qualify people to do the work.”Fialkowski refers to the CFSE (certified functional safety expert) program—a non-profit organization that is geared to certifying people, the FSE (functional safety expert/engineer) program, and the ISA itself, for which, like Gruhn, Fialkowski is a trainer. “I also know some of the safety programmable logic controller (PLC) manufacturers out there offer free workshops on how to apply best practices techniques on applying the standards. So there is a lot of education available. When I got my CFSE five years ago, there were a few dozen of us. Now, there are more than 500, so you can see the trend.”“Our major customers all have dedicated safety engineers. They all know the standards and know what they are looking for. The others, many of them, especially the smaller businesses, have less knowledge and therefore, it’s very difficult for them to pick a system that meets their needs,” says Erik de Groot, global marketing manager for Safety Management at Phoenix-based supplier Honeywell Process Solutions.Safety coursesThus, Honeywell uses numerous means, ranging from detailed surveys and questionnaires to in-depth, vendor-neutral safety courses covering topics such as standards, to try to work with customers on safety issues.Adds de Groot, “Customers are often wading through the confusion about what these standards mean, and that can hold them back. It’s about making sure the customer is educated. This is the cost of doing business. It’s the job of companies like Honeywell to help customers understand what they need.”After training comes the systems themselves. Almost all of the process automation vendors offer some kind of SIS. These systems are universally standards-compliant, and when combined with “competent” staff, can help a manufacturer meet safety requirements. The latest research and development (R&D) advances apply an evolution that has been gradually permeating the automation industry as a whole: the continued introduction of intelligence to all levels of the operation, and then the use of that intelligence for greater control and more informed decision-making. Siemens calls this Totally Integrated Automation, but Siemens isn’t alone. For example: Emerson has PlantWeb and other vendors are doing the same thing. In keeping with this approach, Emerson’s DeltaV SIS is an extension of PlantWeb, covering the safety system, the field devices and control valves, plus integrating with the process automation system, plant asset management system and other elements of plant automation.Whatever system you install, Art Pietrzyk, segment manager for critical control and process safety for vendor Rockwell Automation Inc., Milwaukee, stresses that this is just the first step. “Technology alone can not make things safe. In fact, it gives us a false sense of safety.” Pietrzyk gives the example of a car’s emergency brake. You don’t know how the emergency brake is going to work until you use it, unless you test it on a regular basis. Safety integrated systems are the same. “It’s not enough to merely have a system. In the process world, the safety system is a low demand system. You can go for years without that systems being activated. You have to go back periodically and do a proof test, make sure the system works, the sensors are sensing and valves are working.”This is where intelligence comes into play. “Newer technologies provide more than a mere connection to the device but include intelligence in the device itself. This makes it an instrument rather than merely a device, and allows us to do things like predictive maintenance.”This intelligence is an important building block in the safety process lifecycle. “People are starting to realize that when the standard calls for a safety lifecycle, there’s more to compliance than just using a certified safety system,” says Luis Duran, business development manager for safety systems, Americas, for supplier ABB Inc., in Houston.Critical stepsDuran identifies four critical steps in the life of a safety process: 1. Analysis. What are the risks and how can they be mitigated?2. Safety System/Process Design. With the assessment complete, you can design the best system for you and ascertain how it will be used and maintained, and what other risk mitigation processes that may be required. Says Duran, “This is where people are realizing that it is more than just buying and installing a system. How often does the system need to be maintained? How will you proof test it?”3. How do we actually run the system? There is a lot more emphasis on the operational maintenance today than in the past. 4. End of life and replacement. Adds Duran, “Some of the incidents that have happened in the process industry are a result of failures to properly proof test and maintain the system. For example, if you look at Texas City, you can’t point to one failure. Numerous things went wrong.” In the intervening years, BP has accepted that human error was a factor in the explosion. Additionally, several level indicators failed, leading to overfilling of a knock-out drum, and light hydrocarbons concentrated at ground level throughout the area which were, in turn, ignited by a truck that was left running nearby. But will lessons learned at the cost of lives lead to improvements? The systems are better, the standard of related education has improved and manufacturers are spending money on the issue, so one has to be positive. However, some managers persist in the belief that increased safety systems will slow down production and cost money—a position that Gruhn of ICS Triplex says is patently ridiculous. Production efficiency actually improves when you do safety properly because you have more control and intelligence about how your operation is set up and running, says Gruhn. By way of example, he points to the Occupational Safety and Health Administration’s (OSHA) introduction of the PSM Process Safety Management of Highly Hazardous Chemicals standard (29 CFR 1910.119) regulation. In the years since, reports indicate that the number of accidents has gone down by more than 20 percent, and companies are reporting that their productivity has gone up.And that’s before the cost of an incident is factored into the equation. Texas City has cost BP more than $2 billion so far. When all is said and done, the 2005 Buncefield Depot explosion in Hertfordshire, United Kingdom, will cost operating companies Total UK Limited and Hertfordshire Oil Storage Ltd around £700 million. The first impact of the most recent Tesoro incident was felt as quickly as the following trading day, as Tesoro’s stock price fell 6 percent. Says Bresland, “When will we know whether the tragedy of 2005 has resulted in greater safety at BP and other companies’ refineries? Only when we can look back over a significant number of years without major accidents, deaths or injuries.”For additional safety organizations and links, go to www.automationworld.com/feature-6994.
Subscribe to Automation World's RSS Feeds for Feature Articles
Companies in this Article
Companies in this Article
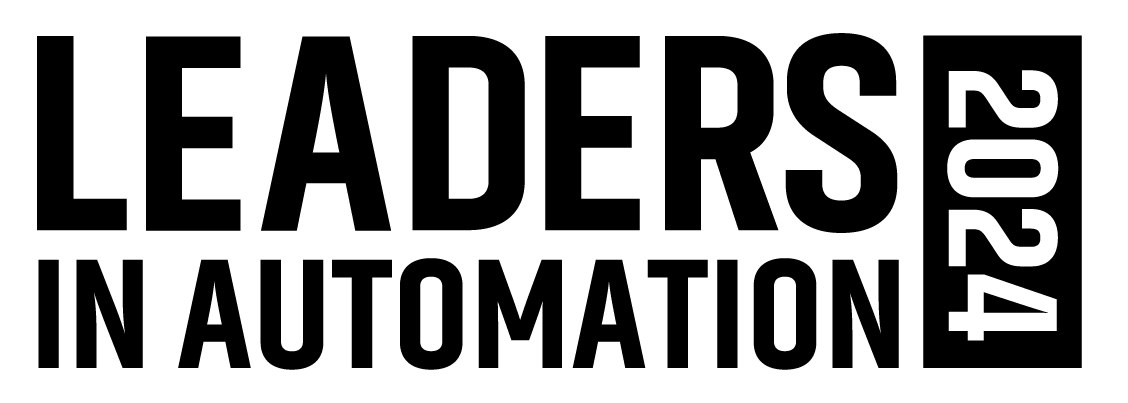
Leaders relevant to this article: