{mosimage} Things are going relatively smoothly, although the struggle to maintain manufacturing processes as efficiently as possible is a constant effort. Then the salesperson on a key account returns from a sales call and says that the customer has asked for the company’s sustainability statement. Are you prepared? Or, will this request throw the nice-to-do list right out the window as you scramble to figure out what sustainability is and what your company is doing about it?Ray Anderson, founder, chairman and retired chief executive officer of Interface Inc., in Atlanta, a manufacturer of carpet tile, faced just that request in 1996. He had no answer for the salesperson. His research for an answer, his challenge to a hastily formed team and subsequent journey into sustainable manufacturing are detailed in his latest book, “Confessions of a Radical Industrialist.” His quest to build a profitable company actually found a partner in sustainability.Often, when an either/or proposition is posed, the correct answer is “both.” As noted by Anderson, “I’m profit-minded and extremely competitive. I thought ‘going green’ would definitely enhance our standing with our customers and maybe give us some good press, too. But I also thought it just might be a way to earn bigger profits from doing what was right by the earth. No one had ever attempted that kind of transformation on such a large scale before. We aimed to turn the myth that you could do well in business or do good, but not both, on its head. Our goal was to prove—by example—that you could run a big business both profitably and in an environmentally responsible way. And we succeeded beyond my own high aspirations.”After a 12-year process, Anderson cites numbers to back up his assertions. He points to the 1997 Kyoto Protocol that was widely derided by his fellow CEOs that sought to reduce greenhouse gas (GHG) emissions by about 7 percent in the United States by 2010. Others were afraid that meeting that goal would drive them out of business. Interface’s performance by 2008 revealed a reduction of 71 percent in absolute tons of GHG emissions while sales increased by two-thirds and earnings doubled. Interface consumption of fossil fuels per square yard of carpet was down 60 percent, and waste reduction measures put a cumulative $405 million of avoided costs directly into the bottom line.“Sustainability has given my company a competitive edge in more ways than one,” Anderson continues. “It has proven to be the most powerful marketplace differentiator I have known in my long career. Our costs are down, our profits are up, and our products are the best they’ve ever been. It has rewarded us with more positive visibility and goodwill among our customers than the slickest, most expensive advertising or marketing campaign could possibly have generated. And a strong environmental ethic has no equal for attracting and motivating good people, galvanizing them around a shared higher purpose, and giving them a powerful reason to join and to stay.”Often, in business, the game goes to the company and its leaders who see a new way and have the courage to forge a new path. Games are not necessarily zero-sum, but sometimes there can be multiple wins. Anderson sums up, “Turning away from the frantic and thoughtless consumption of oil, coal and natural gas will not spell the end of the world; it’s the beginning of a new world of efficiency and clean technologies—and new fortunes.”Vision requiredDeveloping next-generation manufacturing takes far more vision, commitment and thought than just doing one kaizen event for Lean Manufacturing. Interface’s experience points to a multi-faceted approach that brings together production, product design and supply chain into an integrated whole. Tools to help managers and engineers put it all together may not yet exist, though. This is an opportunity for other suppliers to help lead the way.{mosimage} “First, you need to understand the systems,” says Terry Swack. “You have to look at the design-through-manufacturing process from a systems approach, considering the entire lifecycle perspective of the product.” She is co-founder and chief executive officer of Sustainable Minds (www.sustainableminds.com), a Cambridge, Mass., supplier of on-demand, early-stage design decision support software and information service that estimates a product’s potential lifecycle environmental and human health impacts in a collaborative, learning work space.Swack continues, “Everything ties together. Using a minimum number of parts and materials in the product reduces cost and helps make manufacturing more efficient. But there is also a direct correlation to optimizing the product’s end of life. Lots of parts make it harder to recycle. All this has to happen early on. You’ve got to think before you act. Seventy five percent to 80 percent of manufacturing costs are committed in the early stages of product design.”One problem standing in the way of development of sustainable manufacturing is understanding just what “sustainable” means. Says Swack, “One of the greatest barriers to companies is lack of definition and understanding. There are no standard sets of metrics or ways to measure sustainability. Companies are so siloed in approach that it’s hard to achieve the kind of collaboration to leapfrog the competition.”The National Council for Advanced Manufacturing has taken a stab at defining sustainable manufacturing that is as good a starting point for action as any. It says, “Sustainable or green manufacturing is creating a product in a way that considers the entire product’s lifecycle and its full impact surrounding the use and reuse of raw materials and auxiliary materials, impact on the environment and impact on the surrounding community. The goal is to be able to manufacture in a way which is so sustainable that it is able to continue far into the future.”One company had developed a product designed to help people strengthen and realign the muscles in the hand to counteract problems caused by repetitive stress. The Xtensor looks like a cut-up glove with rubber bands, but it actually exercises the hand, wrist and forearm with about five minutes of use per day. Problem was, the way the product was manufactured didn’t align with the mission of a company in business to help people.“About 18 months ago, I became increasingly dissatisfied with our contract manufacturer for the Xtensor,” says Scott Kupferman. He is the chief executive officer of Clinically Fit Inc., in Melville, N.Y., and the developer of the product. “They were focused only on the bottom line and ignored customer service. We wanted to build a company that was socially and environmentally responsible, with a product manufactured here in the United States. It’s like setting an example, if we can do it, why can’t other companies.”Cut cost, not qualityKupferman found Echo Molding, in New Jersey, a family-owned business that seemed to meet his values. Among other things, Echo in 2009 completed a project to install enough solar panels to provide about a quarter of its electricity needs—about 230,000 kilowatt hours (Kwh). So Kupferman made the decision to move his product molds to Echo. The company’s engineers worked with Kupferman’s team to evaluate materials used in the product. They pointed out that the plastic used in the Xtensor could be made from recycled material, a change that Clinically Fit adopted. “Overall, they were able to help us cut costs [of the product] without cutting quality—if anything, the quality is better,” Kupferman says. “So, companies in the United States can see that there is a way. There is a lot of technology right in our back yard. Sure, we could have shaved some cost by manufacturing in China, but the hassles and problems of shipping would outweigh the benefits. Let’s light a fire in the manufacturing world to make stuff here.”Taking a look from the supplier perspective, Chip Rennie, global director of industrial energy for automation provider Emerson Process Management, in Philadelphia, discusses sustainability efforts as a system with a long-term view. His team will do a study with a potential client before diving in. “You absolutely have to start with measurement and control,” says Rennie. “Actually, it’s a little easier these days because we’re in a digital world. You don’t have some of the drifts seen with analog measurements.”He notes, “We start from the basement up, looking holistically at valves and transmitters, then making sure there is a mechanically sound platform. We have found it easier to take people with process knowledge and teach controls than vice versa. After the base stuff, then we can go in and look at boilers and burners. The first step is to get a handle on the scope, cost and potential return on investment. If we can get the unit to automatic controls, we gain about 60 percent of the potential savings. Then we can look at optimized process control to pick up and gain an additional 15 percent to 20 percent. We never do total energy management without doing the first steps.”One problem that process plants have experienced is the slow degrading of their advanced process control systems. When engineers charged with retuning these systems are reassigned, the systems are often turned off and the gains are lost. Rennie’s answer, “If you buy the energy-optimization package from Emerson, built in is the cost of a year of continued engineering. We have built in across the project to have a consultant one week per quarter for a year. If we can show that we can keep the system in automatic for a year, they’ll keep it going.”Pet peeve“I have a personal pet peeve,” concludes Rennie. “That is people who buy or sell a solution and then 18 months later, it’s turned off.” So Emerson works with operations to gain their trust in the system, and provides support so that the gains are sustained.Facilities can be major energy wasters. This makes them attractive target markets for integrators who can put together solutions for remote monitoring and control. Saara Embedded Systems Pvt. Ltd., in Bangalore, India, is an integrated service and solution provider in embedded technologies, and an integrator partner of National Instruments Corp. (NI), the Austin, Texas, supplier of test, measurement and automation products. It assembled a system for remote monitoring and control for facility management based on NI’s Single-Board RIO—a control and input/output product—and the system-and-programming software product LabView.Siddarth Verma, an engineer with Saara, explains the problem as “effectively controlling and monitoring energy parameters and the consumption of critical infrastructure and assets of an enterprise, especially in a scenario where there are multiple facilities geographically distributed in different locations.”Verma says about the system, “Our Remote Facility Management System (RFMS) precisely monitors and controls a facility’s or an infrastructure’s total energy consumption. It provides unconstrained real-time access to parameters from diesel generators, HVAC (heating ventilation and air conditioning), signage boards, security systems, refrigeration equipment, lighting systems, uninterruptable power supplies, printers, beverage vending machines and even single-switch or valve-based devices. With the flexibility of the embedded remote terminal unit (RTU), our customers can monitor and control different points on their infrastructures, making the RFMS an ideal system for effective energy consumption and optimization.”One customer reported reduced energy consumption of 15 percent. Further, with the implementation of the RFMS, the frequency of fuel replenishments has dropped drastically because replenishments are now based on a proactive on-demand system, fuel consumption accounting is accurate, and fuel theft issues have been addressed.Paper savingsPaper mills are huge consumers of energy. Another example of a large process-control systems supplier working with a customer is the story of Myllykoski Paper, in Kuovala, Finland, and its work with Swiss-based supplier ABB. In 2007, Myllykoski Paper signed an energy efficiency contract with ABB, which started with a review of the energy efficiency of the whole manufacturing process—from inspection to implementation. A paper mill, for example, can derive savings from the process method, pumping, heating systems and energy management.Myllykoski is among the largest publication paper producers in the world. The Finland mill, located in Anjalankoski, produces more than 600,000 metric tons of high-quality uncoated and coated publication paper annually. The paper-fiber manufacturing process consumes a lot of energy, as do paper machinery and the pumps. Competing mills also invest in energy efficiency, which means that companies cannot afford to remain outside this development cycle.The program goal established in 2005 was to reduce consumption of heat by 10 percent and electricity by 3 percent by 2009. Those goals have been met, even while production has increased. ABB service, in cooperation with the customer, reviewed the entire energy-efficiency process, from inspection to implementation, with the goal to enhance the operations. The program ties into continuous improvement of energy efficiency as part of the company’s daily activities. An example savings has been a task in which the temperature of the replacement air in the hoods, was adjusted to a lower level. The payback period of this energy efficiency investment was less than a year.Ever think about how much energy a machine uses even when the production line is not running? According to a group of German automobile manufacturers, machinery left on during breaks and weekend shutdowns can still be using 60 percent of their normal usage. If they could automatically go to a sleep mode, 80 percent of that excess usage could be eliminated. Enter an application profile for Profinet called Profienergy.According to Carl Henning, associate director of the PTO (for Profibus Trade Organization)—the North American regional marketing arm of Profibus International—there are complications to shutting down for a break, but benefits as well. “Say you’re shutting down for a 15-minute break, and the line has conveyors and robots. They can go to energy save mode, but there are timing factors of shutting down and starting up. You need an orderly start-up automatically for the end of break. Profienergy, with just a little programming in the programmable logic controller, will be able to expedite this process and offer the energy savings to the manufacturer.”Achieving balanceSergio Gama, market development director for power control business at supplier Rockwell Automation Inc., in Mequon, Wis., says, “The goal is about helping customers conduct environmentally friendly and productive manufacturing enterprises. We help them achieve a balance of energy awareness, environmental conservation and labor safety in operations. These all support highly productive enterprises. We also are moving into a different area in terms of determining energy usage per unit of product manufactured—in essence allowing energy to become part of the bill of materials of the product.”Invensys Operations Management, a process systems supplier based in Plano, Texas, is a company still coming together from its components of Invensys Process Systems, Wonderware and Eurotherm. Bill Schiel, industry solution manager for IOM, reports that the company is bringing all the pieces together for customers with consulting teams to help bring in change procedures and equipment, along with the Wonderware tools for monitoring and reporting. “If you only look at the electric bill once a month, how do you know what’s actually influencing cost?” he asks. The closer we can get to real time, the better operations can influence energy reduction.Finally, Sean Robinson, industry director for food and beverage at suppler GE Intelligent Platforms, in Charlottesville, Va., sums up, “Some see these sustainability programs as part of an overall continuous improvement program. It’s really a triage for finding inefficiencies treated as a cost and opportunity that happens to have significant environmental and societal benefits.”For more, go online and listen to a podcast interview of Invensys Operations Management Vice President Peter Martin discussing energy management with Automation World Managing Editor Wes Iversen, atwww.automationworld.com/podcast-6210.Related Sidebar - Maintaining Optimum CombustionTo read the article accompanying this story, go towww.automationworld.com/feature-6672.
Subscribe to Automation World's RSS Feeds for Feature Articles
Companies in this Article
Companies in this Article
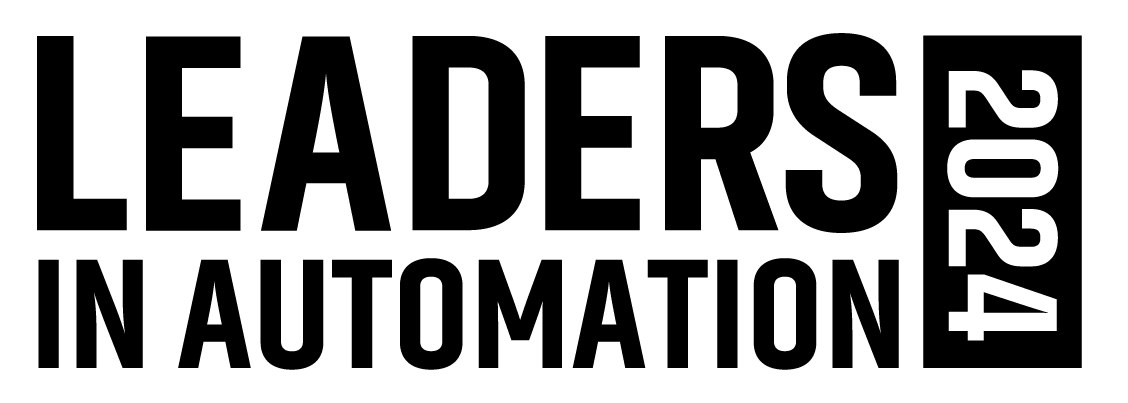
Leaders relevant to this article: