Building Sustainable Businesses: Turning Lip Service into Reality
When Automation World examined the rise of sustainable energy sources in March 2009, the potential economic benefits were readily apparent.
Basically, energy costs money, so saving on energy by using sustainable energy sources such as wind, solar, biomass and the like will save money. However, what was also clear was that automation vendors still had a lot of catch-up work to do to provide the infrastructure required to make the most of renewable energy sources.
Consider Biometrics LLC, a Framingham, Mass.-based-company that provides process-engineering, architectural-design and validation services to the biopharmaceutical and biomass conversion industries. Steve Fitzpatrick, Ph.D., Biometrics president and chief executive officer, points out that most of the control systems his company relies on in the biopharmaceutical and biomass conversion markets were actually designed for the oil industry. Describing his company’s circumstances as a “best fit” situation, Fitzpatrick says that the systems he was using, while good for managing liquids, weren’t flexible enough to accommodate solids and slurries—materials that are seeing more and more use as biomass technology matures.
Now a year on, progress is being made. While many of the automation systems aimed at supporting sustainable energy systems are still little more than a selection of systems cobbled together from other offerings and repackaged with a green label, many vendors are catching up with Fitzpatrick’s needs and releasing solutions tailored to meeting the requirements of the sustainable business.
Enterprise resource planning (ERP) vendor SAP AG, of Waldorf, Germany, is a case in point. At the SAP Influencer Summit in December 2009, SAP executives including Peter Graf, who fills the recently created position of chief sustainability officer, laid out the company’s strategic direction as they transform the organization and try to stake out a leadership position in the sustainable software marketplace. With their sustainability initiatives, SAP executives are looking to position the company favorably as the economy recovers from the trials of the last couple of years and migrates to a more sustainable and resource-optimized model.
Stephen Stokes, vice president of business and climate change for AMR Research Inc., in Boston, attended the conference and wrote, “Unlike so many information and communication technology (ICT) companies, SAP has cut to the chase in building a framework to embrace sustainability.”
This framework includes a couple of key factors, starting with the way the company has been able to clearly articulate its sustainable business case to customers. Rather than getting bogged down in things like “philanthropy and triple bottom lines, [SAP] sees sustainability as the corporate imperative of increasing short- and long-term profitability by holistically managing risks and opportunities. Away from the bright media lights of Copenhagen and other public platforms, the message emerging from economic analysis of climate change and resource overexploitation is that it’s both a market failure and a potent market opportunity.”
Additionally, and most importantly, SAP has managed to define a long-term, strategic view of the corporate sustainable product space, defined the sustainability challenges organizations face and segmented a series of product domains that link together to create the company’s overall sustainable product line.
SAP is far from alone in embracing this strategic direction. IBM has its Smarter Planet initiative, and GE is continuing to pursue ecomagination, to name just two other major information technology (IT) vendors that have targeted sustainability as a business and product transformational event.
Ahead of the curve
What’s more, the traditional automation vendors are moving in the same direction, working feverishly to put together the operational systems required to actually make things work on the shop floor in a sustainable way. This is clearly different from the SAP approach, which has a different purpose: helping companies function in more efficient and sustainable ways. Automation has been geared toward doing that all along. Indeed, with real-time optimization based on information gathering and two-way communication and control, efficiency and sustainability is the whole idea behind automation, and always has been. One might even say that the SAPs and IBMs of the IT world are just catching up.
Moreover, with governments around the world, and especially in the United States, handing out billions of dollars in tax breaks aimed at incentivizing companies to become more sustainable, there will be a significant impact on the number of request for proposals (RFPs) that automation companies can expect.
“We are expecting a very strong 2010,” says Brian Micciche, president and managing director of the Crystalline Business for York, Pa.-based Komax Solar, adding that the company has already seen a ramp-up in bookings since the turn of the year. Komax provides turnkey automation systems to solar-panel producers around the world. Basically, it can provide all the standard and customized equipment and processes required to run a solar-panel factory.
“In around 2003, the whole automation market took a nose dive,” says Micciche. “So we sat back and said we had to make a change. We saw a change happening in Germany and decided to focus entirely on the solar industry. We released our first product in 2005 and tripled our revenue the following year.”
However, solar-panel production is a pretty straightforward production-line setting. There will be customization required based on regionalization and layout, but it is essentially a simple production line with robotics and material-handling systems. But solar is just one of many sustainable energy options being developed, and some are far more complex, putting more demands on the automation systems.
“We’re seeing as the technology has matured that it is becoming more like our traditional stuff,” says Al Novak, director of Alternative Fuels, in Pittsburgh, for automation supplier Emerson Process Management. “Biomass is a good example. For a long time, biomass meant corn-based ethanol. The challenge was that it wasn’t compatible with the existing energy infrastructure in the United States. It required all kinds of special equipment, cars couldn’t run on it and so forth. So now there is a shift. Biomass companies are making a different product and more complex molecule that is compatible with the existing infrastructure. That requires more complex processing on the front end, which requires more automation to make those molecules. And as the complexity has increased, we see more of a demand on the control systems.”
Complex vs. simple
The irony in making things more complicated is that it actually simplifies things for the automation engineer, says Novak, adding that the processes used for converting biomass have become very much like the production process you would see in any chemical plant, rather than what you might expect to see in a laboratory. “The more you can make the newer forms of energy compatible with older infrastructures, the simpler it gets.”
For example, Broomfield, Colo.-based Range Fuels Inc. called in Emerson to help get its commercial cellulosic biofuels plant up and running. The new plant, located in Soperton, Ga., and scheduled to start production this year, will use non-edible biomass including timber and wood waste to produce more than 100 million gallons of ethanol and methanol each year. The thermo-chemical process was proven and perfected at a pilot plant in Denver, where the company was able to successfully demonstrate the commercial viability of the technology to government partners and financial backers, and secure an $80 million loan guarantee from the U.S. Department of Agriculture.
According to Bill Schafer, senior vice president, business development for Range Fuels, the company is looking to Emerson to help shorten project cycles and ramp up to production target levels safely and efficiently, and then to eventually repeat the process with other plants near other feedstock sources around the country. As with any other automation project, Emerson is tasked with defining protocols, engineering and automation standards that will enable Range Fuels to lower risks, reduce downtime, and run reliably and efficiently to meet its production goals.
With the way vendors are descending on the alternative energy industry like a cloud of locusts, this is but one of many similar examples.
Dalton, Ga.-based Shaw Industries Inc., the world’s largest broadloom carpet manufacturer, hired Siemens Industry Inc. in Alpharetta, Ga., to help develop a process for converting excess carpet and wood waste into steam energy, which is then used to drive manufacturing operations and thus reduce the company’s reliance on coal and fuel oil.
The plant provided by Siemens, which has been a major player in the alternative fuels industry since its inception in Europe decades ago, consists of fuel-preparation equipment, a gasification unit and a waste-heat steam production unit. It can convert six tons of waste wood into 50,000 pounds of high-quality process steam per hour. The effect on the bottom line would have fit well in our March 2009 story: $2.5 million per year worth of energy savings.
Meanwhile, the Region of Peel—a regional municipality in the Greater Toronto area that owns the Mississauga, Ontario, Canada, underground landfill—contracted to Integrated Gas Recovery Services (IGRS) the rights to collect, control and, ultimately, generate electricity from the large amounts of landfill gases, including methane, carbon dioxide and other greenhouse gases. In turn, IGRS contracted system integrator H.S. Electric, in Norwich, Ontario, Canada, to design, build and install a fully automated control system using solutions from Rockwell Automation Inc., the Milwaukee-based supplier.
According to Matt Dugan, the plant engineering manager on the project, IGRS was looking for an automated system that would help collect the gases on the landfill—which is located under a golf course—for odor control, as well as to generate electricity in a sustainable way. Today, the IGRS facility produces approximately 5,000 kilowatts of power per hour, enough to power an average of 5,000 homes in the Mississauga area.
Global automation giant ABB is also stepping forward. Many customers are using the company’s automation products to embrace alternative, sustainable energy sources. For example, St1 Biofuels Oy, in Finland, is relying on ABB solutions to help make biofuel—specifically bioethanol—from food waste at several fully automated plants.
The biofuel is 85 parts ethanol blended with 15 parts gasoline components and additives, and is sold in Finland as Refuel (or RE85) as an alternative vehicle fuel. Drivers must have a vehicle engineered to use it, a so-called “flex-fuel” vehicle—but RE85 costs about 42 cents U.S. less per liter than regular 95 octane unleaded gasoline.
Subscribe to Automation World's RSS Feeds for Feature Articles
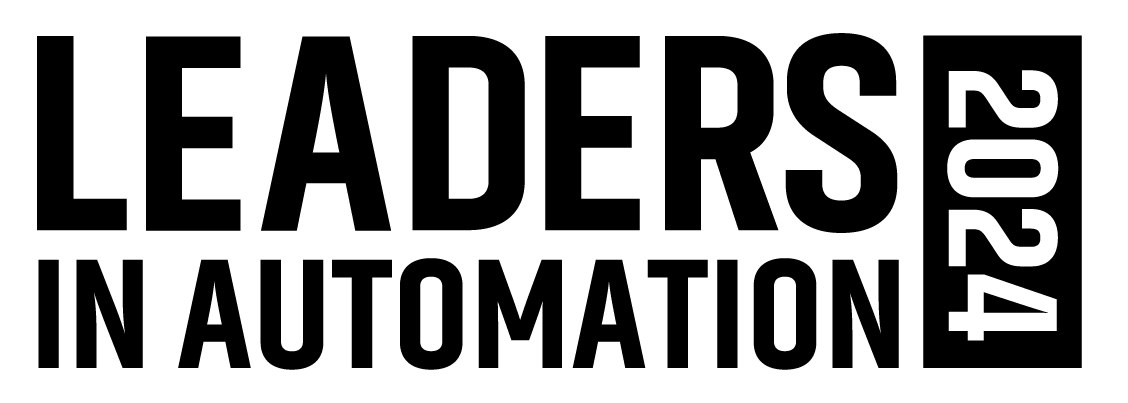
Leaders relevant to this article: