Using Mobile Wireless Technology in Manufacturing
Oct. 2, 2009
Mobile workers can use wireless connectivity, no doubt about that. But ”mobile worker” takes on dozens of meanings, from road warriors armed with Wi-Fi-enabled laptops and USB cell phone plug-ins, to back-lot roamers with pickups and two-way radios.
“There’s no such thing as a fixed shift, at least for knowledge workers,” says Cliff Whitehead, manager, strategic applications for vendor Rockwell Automation Inc., Milwaukee. “People work around the clock, responding to voice or data or e-mail coming across a variety of devices from iPhones to Blackberries to laptops to you-name-it.”
In much of the industrial world, where there are fewer knowledge workers and more hands-on personnel, there appears to be only a limited number of truly mobile workers. Functions include engineering (including controls) and maintenance, with a smattering of people involved in processes that require equipment across large areas.
That said, there are whole ranges of production work where wireless connectivity can help, whether or not people, or machines, are in motion while broadcasting on the radio. In fact, perhaps we should rephrase the whole category: not “mobile worker,” the person, but “wireless work,” the category.
Wireless in manufacturing primarily transmits and receives data or information, things as disparate as instrumented temperatures drawn from the floor every x minutes, or repair procedures sent out to a crew dealing with a sick machine. The worker might not be mobile—might not even be involved, as in instrument automation—but at any given plant, things that could benefit from instant contact are everywhere. And they can be highly dynamic, where the point of greatest use at any given second (or millisecond) can be forever moving around.
As with everything that has such broad potential, the real gains come when you focus on application planning and details. There are really two basic approaches to the application of wireless to manufacturing: task-based and systems-based.
Task-based deployment essentially replaces a clipboard or a non-wireless handheld with a radio. “The key here is to buy or make an application that services a specific work function,” says Whitehead. “For example, maintenance can use instant access to work orders, asset locations and types of tasks. And in relation to maintenance, operations can use any feedback from the operation. Things like parts installed, pulled from inventory, recycled and the like. You could call these legacy applications—taking a paper-based workflow and making it electronic.”
While it is an application type that exploits virtually any kind of radio, including cell phones, real benefits accrue when people take the right approach—see “Air-time for Operators,” below, for how a Cytec facility set about giving its operators and engineers wireless integration into workaday, manual data collection.
Theoretically, everything in the was-paper-now-electrons category is dead easy: just identify some task or set of existing tasks that go where wires cannot reach or where instant feedback would be useful, such as a quick report on a non-instrumented process. Then replace the old way, whether that be paper-and-clipboard, wired keyboards or non-wireless handhelds, with a radio.
In reality, there can be complex issues in task-based deployment, regardless of how simple it might appear on the surface. People resist change, so the benefits to the guy holding the radio have to be clear. And, as in Cytec’s case, the simple switch from paper to airwaves can quickly identify new, more effective ways of working. For Cytec, the ability to spot early trends toward equipment malfunction and fouling proved to be the big winner, and that is just one benefit among many.
The task-based approach fits (and potentially benefits) dozens of industrial scenarios, offering ways to connect immediately with maintenance personnel wherever they are; to capture and record data that otherwise might never make it to paper; and to send information directly to operators, at the time and place they need it. “Just make sure,” Rockwell’s Whitehead says, “that end-users are ready to support it. If you don’t plan and educate, you might be facing tissue rejection from the personnel who are the recipients of the ‘wonderful gift’ you’re giving them.”
For all its benefits, the task-based approach to deployment has less potential for dramatic payback than a systems-based approach. “There is more mobility than people think,” says Charles Mohrmann, vice president for sales, Wonderware mobile solutions, Lake Forest, Calif., and former vice president, strategy and business development for SAT Corp., a mobile solutions vendor acquired by manufacturing software supplier Wonderware in August, 2008.
“The image of future manufacturing that was prevalent in the 1980s and ’90s, of a few guys sitting in a computer room controlling robots and automated equipment, is a far cry from reality,” he says. “In real life, people in manufacturing are up and walking around to look at things. People are still highly hands-on and interactive in most process production.”
Mohrmann says that one of the biggest areas is what he calls “the high reliability organization. And we’ve found the best return from operator-driven reliability. Reliability fostered by maintenance is still extremely important, obviously, but operators have the most direct knowledge of the operation of the equipment they run. If you can enable them to identify and report meaningful fluctuation in operating parameters, then maintenance can get on the case before something breaks.”
He argues that mobility in communications—wired or wireless—can provide important infrastructure to the foundations of production. “You’re able to spread operational excellence across the company,” he explains. “Consistency of operation and the ability to leverage best practices has made a big difference for many users.”
Whitehead agrees. “You can’t stress enough that you must begin with a good plan,” he says. “After all, you’re making many decisions around technology selection, deployment, procurement, IT (information technology) rights and responsibilities—and that’s just a start.”
Mohrmann cites two multinational hydrocarbon producers, early adopters of IntelaTrac, SAT’s flagship offering. “They took a top-down view and determined that there was a great need to change roles,” he says. “They needed to restructure such that people could operate across traditional borders around functionalities. Once they made some fundamental changes, operators could perform minor fixes like changing a hose, or they could notify maintenance directly to make a quick repair, rather than go up a convoluted management chain.”
The key is to ensure that critical data and intelligence reaches the right people, whether from the floor up, about equipment behaviors, or from operational management down, about procedures and experience-based knowledge.
“For example, when someone, no matter how remote, can get intelligent decision trees on their hand-held, they can make the right moves at the point of an incident,” Mohrmann explains. “It’s even more critical for low-frequency incidents. You might have one that occurs once every five years and it could be catastrophic if nobody remembers the developing symptoms. But, if you’ve captured the knowledge from five years ago in a decision tree, people today can stay on top of a situation before it becomes critical.”
Mohrmann says that highly effective IntelaTrac projects show a common pattern. “People might begin by talking about paperless environments, for example,” he says, “but in and of itself, going paperless offers relatively low value. It’s really about looking at workflows, processes and especially, opportunities to change, to improve.”
Wonderware begins with a limited front-end study, then works with customers to build technical and software supports for what that study reveals as a high-payback application.
“There are three key elements,” he says. “First, you scope the project right with the front-end study. Second, you make sure there’s a commitment across the organization. Is the project team fired up? Are the super-users eager to get going? Third, you have to look long and hard at the risk factors. Are the supervisors behind the project? If not, if they don’t understand the benefits, they can undermine the whole process. Equally damaging is upper management that won’t look at the data or care about the communication opportunities.”
In the world of discrete manufacturing, there are some solid touchstones about where to begin deployment. “How do your customers take delivery on what they’ve ordered from you? What steps are involved?” asks Rodney Winger, senior director of product marking for Epicor Software Corp., Irvine, Calif. Epicor offers enterprise resource planning (ERP) systems for midmarket discrete manufacturers. “If the production floor can benefit from direct connectivity with the data around orders, then it makes sense to include production in the distribution of information. If connectivity is not an issue, or the area of the factory is fully covered for communications, they can use a browser or smart client. If it’s mobile or remote, wireless is the way.”
Epicor provides a range of modes, from a workflow-based approach for off-site service and on-site maintenance to menu-driven procedures for parts picking or shipping. “The driver is cost savings,” Winger says, “not just in labor or production figures, but cost savings in customer service turn time. Information about activities leading to the fulfillment of a given order might need to be propagated broadly—front office, production, warehousing and inventory, distribution and supply chain, you name it.”
Specific savings can even be realized in the flow of activity. “If you can reduce someone’s trips across the floor, you save,” Winger explains. “If you interleave tasks—have someone pick up materials inventory on the way back from putting away something else, for example—you are more effective in resource loading. Plus, if you think about it, there are for any order, connections all the way down to transactions in production. The key is understanding how activities connect to opportunities for sales.”
What does the future hold? Everyone agrees that the surface has barely been scratched. Winger: “ERP, that is, a top-down, comprehensive systems approach, is no longer a strange idea. The great majority of our customers—and we’re talking about midmarket here, not the sophisticated tier one mega-companies—most have been through at least one ERP system prior to adoption of Epicor. The more people know, the more they want.”
He adds: “There’s an important rider to all this. You have to remember that the labor scene is undergoing a fundamental change around technology. There’s a huge wave of people from 20 to 35 years of age whose entire lives have been in a connected world. They expect and demand instant connectivity.”
He sees not only burgeoning technologies but fundamental changes in how software is presented. “Apple is right on top of the consumer’s desire to do complicated things in simple ways. Very few manufacturing applications are truly simple to use. I see that changing dramatically in the next few years.”
Mohrmann points out that open application programming interfaces (API) are following this trend in ease of use. “New systems, the Web, SOA (service-oriented architectures), everything has gone far beyond what anyone could have imagined even a few years ago,” he says. “As more ideas are implemented, more people buy in, and as more people buy in, they demand new functionality. The user community truly energizes the supplier community.”
“We’re seeing the classic adoption curve,” Whitehead says. “It wasn’t that long ago that a cell phone was a strange new device. Now, Apple says, for iPhone applications, there have been billions of downloads. If you weed out the time-wasters and the trivial ones, you’ll find an increasing number of business applications among these. Wireless, or connectivity in general, is becoming the norm.”
He adds: “When all the fixed and mobile points can be tracked and monitored and handed off gracefully, connectivity becomes just another tool. That’s perfect—I’ll be happy to see that day in manufacturing.”Related Sidebar - Converting Manufacturing Logsheets to Wireless Pays DividendsTo read the article accompanying this story, go towww.automationworld.com/feature-6106.
Subscribe to Automation World's RSS Feeds for Feature Articles
Companies in this Article
Companies in this Article
Sponsored Recommendations
Sponsored Recommendations
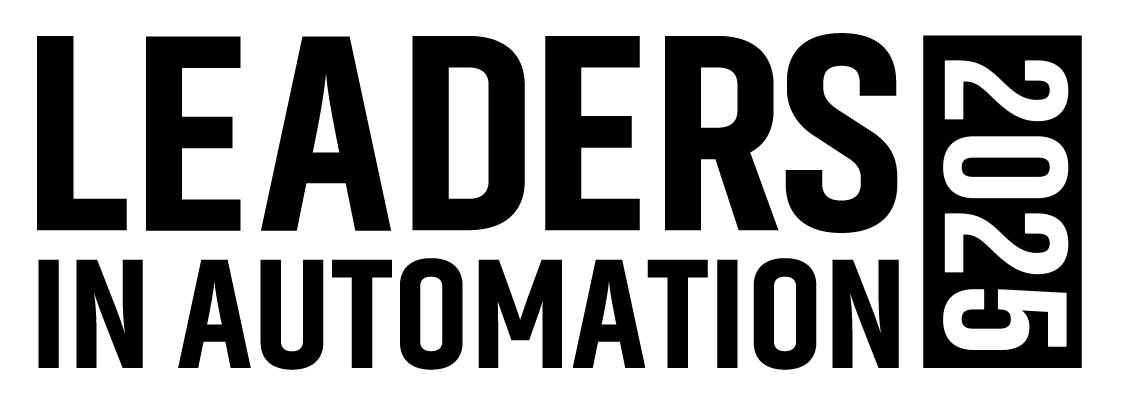
Leaders relevant to this article: