You’ve heard of “light beer” and “light cola,” but what about “automation light?” It’s a term that’s been popping up in some circles lately as global companies expand manufacturing into low-cost countries where capital budgets are severely constrained. Just as Bud Light and Miller Lite profess to offer reduced-calorie solutions for beer drinkers who don’t want to put on extra weight, so-called automation light systems aim to provide reduced automation solutions for manufacturers who can’t afford to add too much cost and complexity.
“We have about 30 customers in our global account program that have largely standardized on our products, and I would say that at least 10 out of the 30 have automation light initiatives, where they’re trying to reduce capital cost, reduce the need for IT (information technology) and reduce the need for support,” says Ken Deken, vice president, portfolio management, for Rockwell Automation Inc., the Milwaukee-based automation controls supplier.
The automation light term is one that’s familiar to Ed Thompson as well. “We’ve had customers tell us, ‘We want to do this, but we don’t want to install a great big, heavy system on top of it, so we’re trying to do automation light,’ ” observes Thompson, who is vice president, U.S. operations, for Neoris, a Miami-based information technology (IT) consulting company that is a certified integrator for SAP AG, the Walldorf, Germany-based enterprise software supplier.
Neoris has done integration work for manufacturers in low-cost countries including Brazil, Argentina and Mexico using an SAP application called Manufacturing Integration and Intelligence (MII) that supports links from plant floor devices to enterprise applications and databases. “There’s a library of integration components that MII supports that has made it very simple, very cheap and very fast to integrate for people who have smaller budgets,” says Thompson. “It’s a lightweight solution that’s been great for emerging markets—places where investments in technology are harder to justify because labor costs are lower.”
Small footprint
Not everyone has heard the “automation light” terminology. “It sounds like a bean counter term,” quips one system integrator who has had project proposals quashed by budgetary constraints.
But many agree that a need exists for small-footprint, low-cost manufacturing systems in the world’s developing regions. Low labor costs in these places may mean that manufacturers can’t justify the cost of full-blown automation and production management systems with all the features of a comprehensive manufacturing execution system (MES) software suite. What’s more, in many low cost regions, there may be limited engineering and IT talent available locally to provide complex system support.
But global companies still need to manufacture products in close proximity to their customers in developing regions of the world. And they want to maintain commonality with existing company systems elsewhere, as well as the ability to scale up small-footprint systems later as needed. Further, even with a small-footprint, “automation light” system in place, managers still need access to plant floor data for diagnostics, and to meet product quality and traceability requirements.
One company that is familiar with the challenges of going global is The Procter & Gamble Co., the Cincinnati-based consumer products giant. John Kuley, technical section head for P&G’s Household Care Business Unit, notes that his Unit has in recent years adopted a global standard for manufacturing detergents and other liquids that includes a small-footprint control system for use in low-cost countries. The system has so far been used in places including China, Malaysia, Argentina, Venezuela, Russia and Egypt.
In larger-market countries, such as the United States, P&G typically uses Allen-Bradley ControlLogix programmable automation controllers (PACs) from Rockwell Automation, Kuley says. But the small footprint system relies on a lower-horsepower Allen-Bradley CompactLogix PAC, he notes. Other components include a personal computer (PC) running InTouch factory software supplied by Wonderware, of Lake Forest, Calif., as well as SQL database capability.
Cut with care
It doesn’t pay to scrimp too much, Kuley indicates. In the past, when capital pressures were extremely high in a developing country, the P&G Unit tended to install “as simple and basic a system as possible,” he says. “But we’re finding that even with the small applications, if something goes wrong, you do need some decent diagnostic tools and historian capability to go back and figure out what happened.” Consequently, Kuley notes, the P&G Unit is working on small-footprint systems that are “more full-featured” and include “a little more MES functionality than we may have accepted in the past.”
That’s a lesson that other global companies are learning as well. When a Tier One automotive supplier was looking to set up a low-cost operation to manufacture engine components in Monterey, Mexico, it was facing major capital budget restraints.
“We integrated the line, so we did all the control systems, and we had originally proposed a SCADA (supervisory control and data acquisition) type application with a historian, but cost was an issue,” relates Alex Campagnoni, president at Sentient Controls and Engineering Inc., a Lakeshore, Ontario, Canada, system integrator. “We blew their budget with what we originally quoted for the installation, so we had to really scale it back to bring down the cost.”
Because the customer wanted to take advantage of Mexico’s low labor costs, it eliminated robotic pick-and-place on the assembly line, and substituted manual loading and unloading. The customer maintained automated systems for critical press force and torque applications on the line, which uses a Siemens S7 programmable logic controller (PLC) and Profibus networking, says Campagnoni. But “one of the areas they chucked was data management,” he notes. Instead of the full-scale automated data collection system and historian for detailed data logging that was proposed originally by Sentient, the company went with a manual approach, collecting lot-based daily average data on a range of process parameters.
It wasn’t long before problems arose. Within just five to six months, the company had discovered that its data collection approach was insufficient to deal with part rejects and quality issues on the line. The plant needed to quickly solve the problem or risk losing contracts from its automotive customers. “They came back to us after the line was running and said, ‘Look, we’ve got to do something to appease our customer and show them that we’re tracking this data,’ ” Campagnoni relates.
The company still didn’t have the budget, however—or at that point, the time—that would have been required to engineer, test and deploy a full-scale data management system. “And they really don’t have a technical workforce in the plant to be able to support the IT end of it,” Campagnoni adds. “So there was a lot of discussion back and forth about how we could make it easy for them and make it simple for the plant guys to manage and retrieve the data while still keeping the cost low.”
Connectivity solution
To meet that challenge, Sentient turned to deviseWise, a software platform from ILS Technology LLC, Boca Raton, Fla., that is designed to provide connectivity between plant floor devices and enterprise applications or databases. Using deviseWise, Campagnoni’s company created a system that runs on a standard PC and collects crucial production data such as torque values, press force values and pass-fail data from devices on the plant floor. This data is stored in a temporary local historian within the deviseWise infrastructure, and is transported on a nightly basis to another local database for archiving.
“We have an active database so the plant floor guys can very easily see the data by logging in through deviceWise at the plant operator level, so they can see their active parts. And they can also see their archived parts that they’ve already produced, so it made a real nice fit for what we needed here,” Campagnoni observes. Not only can plant floor personnel use the active and archived data for part quality tracking and production line troubleshooting, but the archived data can be electronically transported to the company’s automotive customers, if needed.
Sentient was able create the solution quickly without the need for programming, instead configuring the system using a set of transports within deviseWise that provide connectivity to a wide range of systems, databases and plant floor devices. Additional deviseWise tools allow simple logic such as transformation and filtering to be applied to the data before transport.
“We came in at the right price with the right timing, and things have worked out,” Campagnoni observes. In the future, if the Monterey plant establishes an on-site IT infrastructure with local IT personnel, deviseWise will enable easy connectivity to any kind of MES or IT level application, he notes. And because deviseWise supports bidirectional data flow, it could also be used for downloading instructions such as torque values or other parameters, either from on-site or remote enterprise applications.
Many platforms
The ILS deviceWise software can run at the plant floor level on a variety of intelligent devices or computing platforms, as well as at the enterprise level, says ILS Technology Chief Executive Officer Fred Yentz. In addition, Yentz adds, the product is also sold on an original equipment manufacturer (OEM) basis for use as an embedded connectivity solution within other vendor platforms. Mitsubishi Electric Corp., for one, uses deviceWise embedded as part of its e-Factory platform for factory automation, confirms Sloan Zupan, marketing manager for rack-based PLC platforms for Mitsubishi Electric Automation Inc., in Vernon Hills, Ill.
Zupan says the real-time, bidirectional communication capability that deviseWise provides between plant floor and enterprise level applications is an important feature for customers who are looking to localize manufacturing in low-cost locations. In geographies such as Africa, he says, manufacturers need smaller, low-cost systems to be successful. So they are looking for platforms that let them easily integrate only the enterprise components they need today, but which also provides the flexibility to scale up and connect to additional components later. Mitsubishi’s MX-MES Interface IT—which contains the embedded deviseWise application—provides that capability as part of the e-Factory suite, Zupan says.
PCs begone
Another product that uses ILS software is the xCoupler eATM (for enterprise appliance transaction module) from Online Development Inc. (OLDI), based in Knoxville, Tenn. The xCoupler module is designed to plug directly into the backplane of Rockwell Automation’s ControlLogix PACs to provide direct, bidirectional, controller-to-enterprise communication. This eliminates the need for a PC typically used to facilitate that link, says Ron Monday, OLDI president and chief executive officer. OLDI partnered with ILS to develop the software for the xCoupler module, Monday says.
Many customers are using the xCoupler eATM in locations such as China or Africa, where they don’t have access to on-site IT personnel to maintain more complex PC- or server-based applications and databases, Monday confirms. In these cases, the xCoupler can fit the bill as an easy-to-use approach to gain access to needed factory floor data, he says.
OLDI sells the xCoupler eATM as an approved third-party in Rockwell’s Encompass Partner Program. And at Rockwell, Deken concedes that in some ways, the xCoupler competes with Rockwell Software’s FactoryTalk MES suite. But he notes that “while our Rockwell Software is growing dramatically, we find that there’s a range of customer needs. And as different needs emerge, we’ll often work with partners [such as OLDI] to meet those needs. We can’t do everything ourselves.”
Besides the OLDI module, Rockwell offers other solutions for meeting low-end “automation light” style applications, Deken indicates. A Rockwell EWeb module incorporates a built-in Web server that can serve data directly from Logix family controllers, but its data serving capacity is significantly less than that of the xCoupler, he says. Another Rockwell product, the FactoryTalk Transaction Manager, can also serve as an aggregation point for data. But unlike the backplane-pluggable xCoupler eATM, the Transaction Manager runs on a PC, and so may be less desirable for some especially frugal automation light situations, Deken allows, “where maybe they don’t even have a PC in the application.”
At ARC Advisory Group Inc., a Dedham, Mass.-based analyst firm, Research Director Craig Resnick notes that the ILS and OLDI products fall into a category that ARC calls “automation appliances.” These products are used to “connect to the enterprise without having to put in a full-blown software system,” says Resnick, “and let me tell you, these things are flying off the shelves.”
The popularity of automation appliances stems from the fact that “they’re simple out of the box, they don’t get reved (revised) every six months, and they don’t require IT to support them,” Resnick relates. He is quick to note, however, that these products are not right for every application. For large-scale installations, production management software suites such as Rockwell’s FactoryTalk and others from companies including GE Fanuc, Schneider Electric and Siemens, are “all growing at double-digit rates per year,” according to Resnick.
Commonality is high on the list of objectives for manufacturers who are deploying automation systems globally, Resnick points out. “They want to create once, and deploy everywhere.” Modular systems that are scalable are a key part of that strategy. And at the low end, says Resnick, “automation appliances are probably the ultimate scalable solution for connectivity between the factory floor and the enterprise.”
Varying value
At Wonderware, a major MES player, Director of Product Marketing Steve Garbrecht agrees that scalability is key for manufacturers setting up shop in low-cost countries. “When you’re in the developing world where the price of labor is not such a big deal, the value that you get out of some of these information management applications is not quite as great as in some Western countries,” Garbrecht allows.
Wonderware addresses this need with its Compact Panel, a Windows CE-based device that provides a bundled hardware/software HMI solution that can easily be incorporated in a single machine or small process cell for price-sensitive applications, Garbrecht says. “That’s definitely very popular, and we’re seeing it going in all around the world.”
As users’ requirements and sophistication levels grow, they can scale up as needed to more fully configured Wonderware Industrial Computer or System Platform level products running the company’s InTouch software, he says. It’s Wonderware’s answer to one of the biggest challenges facing automation suppliers, Garbrecht says—developing a cost-effective solution that meets users’ low-end application needs, without cannibalizing the rest of its product offerings.
ARC’S Resnick agrees that even the largest vendors must keep low-end applications in mind. While MES software suites have a major role to play, he says, ARC advises automation suppliers to address both ends of the scale. “If you’re purely dealing with the suites, that’s great, but they might not solve the lowest-level applications,” Resnick counsels.
Sidebar - GM Targets Scalable Automation
To read the accompanying sidebar to this article, go to www.automationworld.com/feature-4434
Companies in this Article
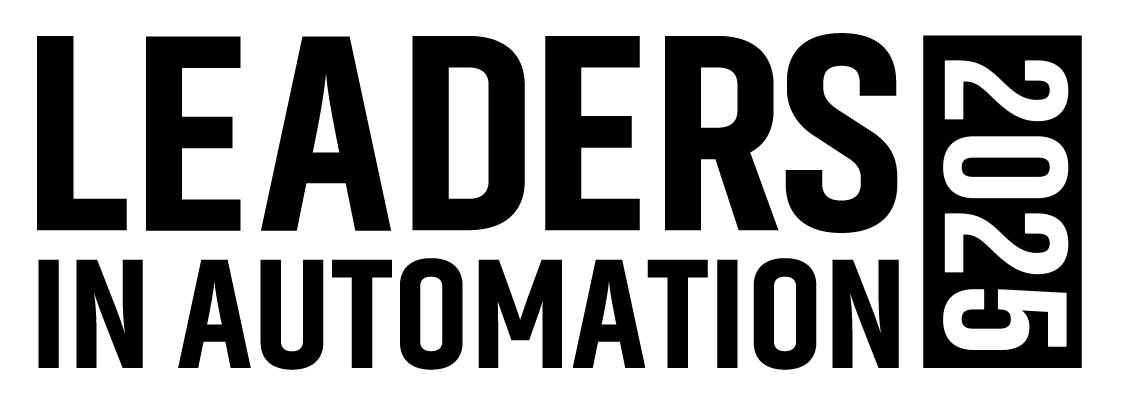
Leaders relevant to this article: