You want reassurance that everyone in your company knows how to conduct themselves in a safe manner. Everyone wants to be proud of the way their company operates.• Are your safety personnel as certified as your auto mechanic?• Do your machine operators know how their machine works?• Does your management ignore safety programs?• Have you had a safety incident in the past year?Even car mechanics have qualifications. Just look at the row of framed certifications from classes they have taken,” says Luis Duran, brand director at safety systems manufacturer Triconex, part of Invensys Process Systems, in Lake Forest, Calif. “Generally speaking, everywhere we go in life, we expect people to be competent,” adds Chuck Miller, DeltaV Safety Instrumented Systems business development manager, at process controls vendor Emerson Process Management, in Austin, Texas. “We have drivers licenses, pilots have licenses and ratings, even food service workers are certified. But there are no real competency or certification requirements for manufacturing safety people. The only other profession I can think of without certification requirements is politicians.”The topic of safety is covered by several governmental and standards organizations. Many times, they recognize the standards of each other. In the United States, the U.S. Occupational Safety and Health Administration (OSHA) is charged with overseeing workplace safety. The European standards body, the International Electrotechnical Commission (IEC) issues standards. Another standards body in the United States is the National Fire Protection Association, which promulgates NFPA 70, also known as the National Electrical Code. Still another standard is ANSI/ISA 84, developed by the Instrumentation, Systems and Automation Society (ISA) and adopted by the American National Standards Institute (ANSI).According to Miller and others, both OSHA and IEC, through its standards 61508 and 61511, state that people involved with the safety lifecycle must be competent in the area in which they deal. This is not always the case, in practice, and it may be difficult to implement. “In my experience,” states Miller, “even people we consider to be safety experts may not be expert in all areas of the lifecycle. For example, a reliability engineer may know a lot about the equipment, but may not be able to competently go into the plant and effectively calibrate and maintain that equipment.”There is another aspect to the problem of competency in safety areas in today’s workforce. Angela Summers, Ph.D., is president of SIS-Tech Solutions, a Houston-based process safety consultancy, and author of “Guidelines for Safe and Reliable Instrumented Protective Systems (IPS),” published by the Center for Chemical Process Safety (CCPS). She sees knowledge walking out the door with every staff person who retires or leaves for another job. “Only a small amount of knowledge can save many hours of work or prevent mistakes leading to process hazards,” Summers says. “Process safety competence is sustained by a foundation of written process safety information, covering the process hazards, technology and equipment. Unfortunately, many users do not see the value of this documentation, having relied so long on the tribal knowledge of their organizations.“Tribal knowledge” grows during hazard analyses conducted throughout the equipment life to identify and evaluate events caused by abnormal equipment operation, Summers says. “Each set of new eyes provides another opportunity to identify previously unseen risk in the process design basis,” she notes.Knowledge also evolves over time, as lessons learned during research and development are supplemented by those learned during equipment operation, Summers continues. “Loss of containment events identify weaknesses in the risk reduction strategy, leading to a re-examination of design and management practices. Continuous analysis and improvement of design and management practices is the best means for counteracting loss of expertise through retirements and downsizing and equipment degradation through age and obsolescence,” concludes Summers.No safety awareness
The problem of competency is not confined to the process industry. Discrete manufacturing, or machine control, has its own set of safety problems. J.B. Titus is manager of business development and safety standards at automation supplier Siemens Energy & Automation Inc., in Norcross, Ga., and a specialist in this side of manufacturing. “The two approaches have some overlap and some differences,” says Titus. “When machines really started to be driven by safety systems technology and standards around the 2002 or 2003 time frame, by and large, the market wasn’t even aware of safety systems. What we often found was that people were actually disabling safeties. In old systems, that was as simple as jumpering a relay,” Titus relates. “New systems, however, contained diagnostics so that the status of the system could be easily compared to design. We actually organized an awareness campaign with materials and complementary copies of the standards. We’d rent a conference room in a hotel and hold hands-on experience in the new safety systems.”But a simple hands-on demonstration doesn’t solve all the competency problems in safety—especially on the process side of manufacturing. Siemens E&A National Process Safety Manager Charlie Fialkowski, based in the Spring House, Pa., office, adds, “OSHA uses a term ‘competent person’ who has training and/or experience to be knowledgeable in procedures and standards. This is not the same thing as a ‘qualified’ person—someone who can put their hands on the system.”To be safety competent, a user needs to know how the overall system works, Fialkowski notes. The industry has been struggling to figure out how to define all this, he observes, adding that an independent board, the CFSE Governance Board, administers certification tests for Certified Functional Safety Expert. “You can find them on the Web at www.cfse.org,” he points out. “Achieving this certification takes the guess work out of whether an individual is a safety competent individual. The certification program requires 10 years of related engineering experience, submission of a case study, four references from other experts and achieving better than 80 percent on a two-part exam.”Bill Goble, managing partner of automation and safety products and consulting company, exida.com LLC, based in Sellersville, Pa., offers additional advice for developing a competent workforce. “A basic course that covers the entire safety lifecycle is a start for most people. An overall understanding of the process and the vocabulary is important. More in-depth training is required for those actually performing the analysis work—especially knowledge of the analysis methods they are using. Most important are the limitations of such methods and the assumptions used when the methods were developed.”Combining experience with knowledge assures further competency. “The knowledge of safety analysis methods requires constant usage,” Goble says. “A company will generally be better off contracting with experts when doing jobs that are done only once or twice a year.” An expert who does the job every week is typically much faster and more accurate, Goble observes. “Many of the safety analysis techniques are relatively new, and it is rare that current plant personnel have the knowledge to properly use these techniques.” Only about 50 percent of those who take the CFSE exam pass, and only about 600 a year attempt the exam, according to Goble.Taking a holistic view of safety involves more than a narrow knowledge of just a few safety mantras. SIS-Tech’s Summers maintains that the individual’s role in a safe operation must be closely related to competency requirements. “I don’t need a person who can repeat clauses from a standard or the gospel of some instructor. What I need is someone who is really good at his or her assigned task, whether it is a risk analysis or a proof test,” she declares.“A person needs to be competent in the skills and knowledge associated with his or her job,” Summers notes. “It is interesting how sometimes we forget the simplest things. If we go back to the fundamentals of quality assurance, W. Edwards Deming believed that 85 percent of an employees’ effectiveness is determined by the system he works within, only 15 percent by his own skill. Users must implement a management system with work processes and metrics that ensure equipment operates consistently in a safe manner, fulfills government and jurisdictional requirements, and meets recognized good engineering practices,” Summers advises. “Work processes and procedures should document minimum activities, so users achieve expected task quality, whether it is performed by the best, average or somewhat distracted employee.”Involve everyone
Emerson’s Miller reinforces this broad view of safety and training. “This idea goes to all areas of operations. All shall be evaluated for skills, process knowledge and safety training. A safety management system must also be established and this must contain an evaluation plan. It is a continuous improvement program. You want to get the right people in place who are responsible, enthusiastic and supported by management,” he says.This organization should cut across the lines of engineering, operations, maintenance and management, Miller observes. As an aside, he adds, “IEC 61511 states that when these people are not available, suitably experienced and qualified personnel should be recruited. Competency across an organization requires a leadership framework with all the right people in place to support it.”Miller recalls how manufacturers complained back in the early 1970s that OSHA rules designed to reduce workplace accidents were an unfair burden. Now, companies often prominently post a large sign on their properties proclaiming X numbers of hours worked without a lost time accident. “In the next 10 to 15 years, safety will no longer be implemented by novice employees, and training and certification will not be optional,” adds Miller. “Unambiguous authority will be given. All departments will be involved—and constantly evaluated.”Another way to increase safety awareness and knowledge is through joint professional volunteer work. Summers says, “CCPS has recently published on its Web site (www.aiche.org/ccps/metrics/index.aspx) a report on New Leading and Lagging Indicators of Process Safety Performance. There is so much interest in this CCPS guidelines book project that there are more than 50 committee members representing government, industry, education and engineering companies. Most people do not realize all of the exciting things going on at the committees right now. I feel privileged to be part of it.”Then there is still another take on achieving a safety-competent workforce—involving everyone in risk assessment activities. Mike Duta, manager of machine safety services at vendor Rockwell Automation Inc., in Milwaukee, leads the assessment services team. The team performs risk assessments at client sites, actually working with the individuals who need to be protected as part of the analysis. “Companies that have top management active support for safety invest the time to ensure that people who are responsible have the technical background and training in machine safety,” Duta says. “Many people may know all the OSHA regulations and analysis tools, and that their electrical engineers and managers are well versed in NFPA 70, robotics standards and ANSI standards. A top-down approach drives responsibility.”Dan Hornbeck, manager of safety systems business, also at Rockwell, says, “Look at the top companies who have visible safety programs, such as DuPont, General Motors, Procter & Gamble and Johnson & Johnson. They have proven the appropriate cost rewards from safety management. I assure you that Rick Wagoner, chief executive officer at GM, is very aware of the safety metrics of the company. These companies assure that safety people are technically competent. Oftentimes, when a safety manager reports through the human relations department, they don’t have that in-depth technical knowledge.”Identifying hazards and accomplishing a risk assessment process helps mitigate dangers. “We engage everyone from operations to maintenance to the cleaning crew to identify hazards. Part of the process includes defining what kind of training process they need in order to know how to work around their equipment,” says Hornbeck. “Another benefit from this engagement overcomes two trends current in manufacturing—going from an older to a younger, less experienced workforce, and using automation to enable one operator to cover more equipment. This creates a further hazard as operators switch from machine to machine.”Know your machine
Once again, the issue comes back to operators knowing their machine or process as one of the keys to safety. Says Duta, “I see a lot of operators who don’t understand their equipment. They don’t always know what happens when they push a button. They should know every control element and know what each mode of operation is. Whenever we finish a risk assessment where the operators and team thoroughly go over a machine, I always hear the comment, ‘Boy, I wish we could do this more often.’ ”While the experts, and even some companies, have a handle on safety competency, Miller, of Emerson, sums up the best. “It’s a bigger task than you might think. Most safety organizations used to be run by the seat of their pants—and some still are. They say, ‘We haven’t had an incident in 20 years. It will never happen to us. We know how to run our business.’ But if you look at reports from the United States and the United Kingdom, plus other documentation, there is always one common denominator for when problems occur—people. Someone didn’t operate, design or maintain the process right. Or they took chances when they shouldn’t have. Just as the latest report, the Baker Report on the BP Texas City explosion, stated, people were the problem.”To view the accompanying article to this story, "Six Tips to Make Safety Everyone's Business", go to www.automationworld.com/view-4147 or read "Avoiding Arc Flash Hazards" at www.automationworld.com/view-4166.
The problem of competency is not confined to the process industry. Discrete manufacturing, or machine control, has its own set of safety problems. J.B. Titus is manager of business development and safety standards at automation supplier Siemens Energy & Automation Inc., in Norcross, Ga., and a specialist in this side of manufacturing. “The two approaches have some overlap and some differences,” says Titus. “When machines really started to be driven by safety systems technology and standards around the 2002 or 2003 time frame, by and large, the market wasn’t even aware of safety systems. What we often found was that people were actually disabling safeties. In old systems, that was as simple as jumpering a relay,” Titus relates. “New systems, however, contained diagnostics so that the status of the system could be easily compared to design. We actually organized an awareness campaign with materials and complementary copies of the standards. We’d rent a conference room in a hotel and hold hands-on experience in the new safety systems.”But a simple hands-on demonstration doesn’t solve all the competency problems in safety—especially on the process side of manufacturing. Siemens E&A National Process Safety Manager Charlie Fialkowski, based in the Spring House, Pa., office, adds, “OSHA uses a term ‘competent person’ who has training and/or experience to be knowledgeable in procedures and standards. This is not the same thing as a ‘qualified’ person—someone who can put their hands on the system.”To be safety competent, a user needs to know how the overall system works, Fialkowski notes. The industry has been struggling to figure out how to define all this, he observes, adding that an independent board, the CFSE Governance Board, administers certification tests for Certified Functional Safety Expert. “You can find them on the Web at www.cfse.org,” he points out. “Achieving this certification takes the guess work out of whether an individual is a safety competent individual. The certification program requires 10 years of related engineering experience, submission of a case study, four references from other experts and achieving better than 80 percent on a two-part exam.”Bill Goble, managing partner of automation and safety products and consulting company, exida.com LLC, based in Sellersville, Pa., offers additional advice for developing a competent workforce. “A basic course that covers the entire safety lifecycle is a start for most people. An overall understanding of the process and the vocabulary is important. More in-depth training is required for those actually performing the analysis work—especially knowledge of the analysis methods they are using. Most important are the limitations of such methods and the assumptions used when the methods were developed.”Combining experience with knowledge assures further competency. “The knowledge of safety analysis methods requires constant usage,” Goble says. “A company will generally be better off contracting with experts when doing jobs that are done only once or twice a year.” An expert who does the job every week is typically much faster and more accurate, Goble observes. “Many of the safety analysis techniques are relatively new, and it is rare that current plant personnel have the knowledge to properly use these techniques.” Only about 50 percent of those who take the CFSE exam pass, and only about 600 a year attempt the exam, according to Goble.Taking a holistic view of safety involves more than a narrow knowledge of just a few safety mantras. SIS-Tech’s Summers maintains that the individual’s role in a safe operation must be closely related to competency requirements. “I don’t need a person who can repeat clauses from a standard or the gospel of some instructor. What I need is someone who is really good at his or her assigned task, whether it is a risk analysis or a proof test,” she declares.“A person needs to be competent in the skills and knowledge associated with his or her job,” Summers notes. “It is interesting how sometimes we forget the simplest things. If we go back to the fundamentals of quality assurance, W. Edwards Deming believed that 85 percent of an employees’ effectiveness is determined by the system he works within, only 15 percent by his own skill. Users must implement a management system with work processes and metrics that ensure equipment operates consistently in a safe manner, fulfills government and jurisdictional requirements, and meets recognized good engineering practices,” Summers advises. “Work processes and procedures should document minimum activities, so users achieve expected task quality, whether it is performed by the best, average or somewhat distracted employee.”Involve everyone
Emerson’s Miller reinforces this broad view of safety and training. “This idea goes to all areas of operations. All shall be evaluated for skills, process knowledge and safety training. A safety management system must also be established and this must contain an evaluation plan. It is a continuous improvement program. You want to get the right people in place who are responsible, enthusiastic and supported by management,” he says.This organization should cut across the lines of engineering, operations, maintenance and management, Miller observes. As an aside, he adds, “IEC 61511 states that when these people are not available, suitably experienced and qualified personnel should be recruited. Competency across an organization requires a leadership framework with all the right people in place to support it.”Miller recalls how manufacturers complained back in the early 1970s that OSHA rules designed to reduce workplace accidents were an unfair burden. Now, companies often prominently post a large sign on their properties proclaiming X numbers of hours worked without a lost time accident. “In the next 10 to 15 years, safety will no longer be implemented by novice employees, and training and certification will not be optional,” adds Miller. “Unambiguous authority will be given. All departments will be involved—and constantly evaluated.”Another way to increase safety awareness and knowledge is through joint professional volunteer work. Summers says, “CCPS has recently published on its Web site (www.aiche.org/ccps/metrics/index.aspx) a report on New Leading and Lagging Indicators of Process Safety Performance. There is so much interest in this CCPS guidelines book project that there are more than 50 committee members representing government, industry, education and engineering companies. Most people do not realize all of the exciting things going on at the committees right now. I feel privileged to be part of it.”Then there is still another take on achieving a safety-competent workforce—involving everyone in risk assessment activities. Mike Duta, manager of machine safety services at vendor Rockwell Automation Inc., in Milwaukee, leads the assessment services team. The team performs risk assessments at client sites, actually working with the individuals who need to be protected as part of the analysis. “Companies that have top management active support for safety invest the time to ensure that people who are responsible have the technical background and training in machine safety,” Duta says. “Many people may know all the OSHA regulations and analysis tools, and that their electrical engineers and managers are well versed in NFPA 70, robotics standards and ANSI standards. A top-down approach drives responsibility.”Dan Hornbeck, manager of safety systems business, also at Rockwell, says, “Look at the top companies who have visible safety programs, such as DuPont, General Motors, Procter & Gamble and Johnson & Johnson. They have proven the appropriate cost rewards from safety management. I assure you that Rick Wagoner, chief executive officer at GM, is very aware of the safety metrics of the company. These companies assure that safety people are technically competent. Oftentimes, when a safety manager reports through the human relations department, they don’t have that in-depth technical knowledge.”Identifying hazards and accomplishing a risk assessment process helps mitigate dangers. “We engage everyone from operations to maintenance to the cleaning crew to identify hazards. Part of the process includes defining what kind of training process they need in order to know how to work around their equipment,” says Hornbeck. “Another benefit from this engagement overcomes two trends current in manufacturing—going from an older to a younger, less experienced workforce, and using automation to enable one operator to cover more equipment. This creates a further hazard as operators switch from machine to machine.”Know your machine
Once again, the issue comes back to operators knowing their machine or process as one of the keys to safety. Says Duta, “I see a lot of operators who don’t understand their equipment. They don’t always know what happens when they push a button. They should know every control element and know what each mode of operation is. Whenever we finish a risk assessment where the operators and team thoroughly go over a machine, I always hear the comment, ‘Boy, I wish we could do this more often.’ ”While the experts, and even some companies, have a handle on safety competency, Miller, of Emerson, sums up the best. “It’s a bigger task than you might think. Most safety organizations used to be run by the seat of their pants—and some still are. They say, ‘We haven’t had an incident in 20 years. It will never happen to us. We know how to run our business.’ But if you look at reports from the United States and the United Kingdom, plus other documentation, there is always one common denominator for when problems occur—people. Someone didn’t operate, design or maintain the process right. Or they took chances when they shouldn’t have. Just as the latest report, the Baker Report on the BP Texas City explosion, stated, people were the problem.”To view the accompanying article to this story, "Six Tips to Make Safety Everyone's Business", go to www.automationworld.com/view-4147 or read "Avoiding Arc Flash Hazards" at www.automationworld.com/view-4166.
Companies in this Article
Companies in this Article
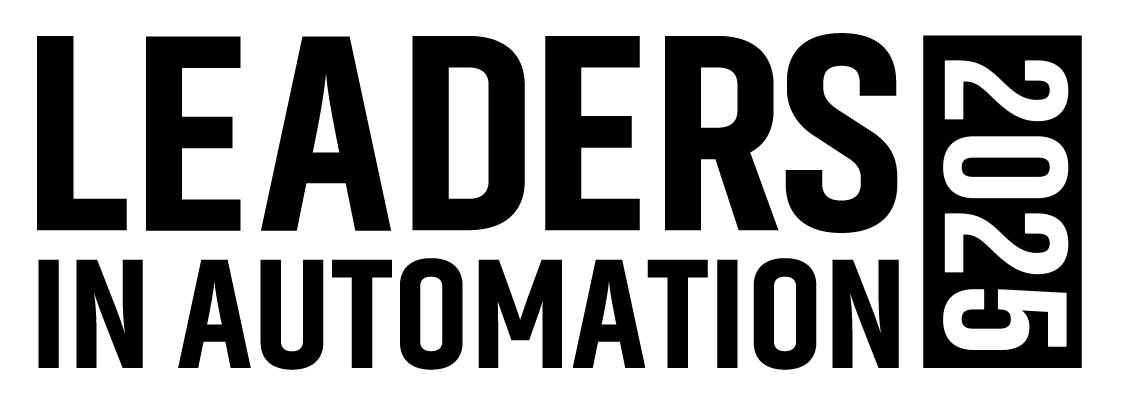
Leaders relevant to this article: