Like other manufacturers of consumer goods, the Sentry Group Inc., of Rochester , N.Y. , was not immune to the trend started by Wal-Mart Stores Inc. One of its big retail customers followed the giant retailer’s lead and required Sentry to put radio frequency identification (RFID) tags on the pallets containing the safes and other security devices that it produces. The customer was eager to reap the same efficiencies that Wal-Mart expected the technology to generate in its inventory and supply chain management. So, Sentry became another manufacturer that spent a lot of money on an expensive tracking technology just to please its customer. Other than keeping the business, there was no return on the investment. “Installing RFID and tagging product for one customer did not provide much overall benefit and did not pay for the equipment,” reports John Matrachisia, information technology director. The bar codes that Sentry had been using for years were far more cost-efficient.Make it payUnwilling to let RFID become just another cost of doing business, management assigned the engineering staff to find a way to use it elsewhere in manufacturing and logistics. “We looked at how we could leverage the technology and investment for our own operational efficiency,” explains Matrachisia. “Although we did not have to tag all our products, there was an opportunity to automate pallet transfers around the plants and to the warehouse using RFID.” The plan for capitalizing upon this opportunity involved mixing RFID with bar codes, playing off the strengths of each. “RFID is not a line-of-sight technology,” notes John DiPalo, senior vice president of product development at Acsis Inc., in Marlton , N.J. , the software vendor that integrated RFID into Sentry’s enterprise resource planning (ERP) system. “So it provides the most benefit to validate transactions without direct interaction from the user.” For example, a dock fitted with door portals could tell the fork-truck operator that he or she is loading the incorrect pallet onto a truck. “RFID also shines in its ability to read aggregations of product,” continues DiPalo. It can read all of the tags on the cases on a pallet during stretch wrapping, for example, to validate that the pallet contains the correct products and quantities. Downstream, it also can record and collect the unique serialization of items and cases in the case-to-pallet hierarchy for authenticating and tracking products through the supply chain.Bar codes don’t need user interaction for validation either, when scanners are mounted on a production line. But besides low cost and the ease of generating labels, bar coding permits users to exploit the various mobile scanning technologies that are available today. “Mobile bar-code transactions provide the added benefit of direct interaction with the user, which provides immediate validation of the product being handled,” says DiPalo.At Sentry, the solution was to apply RFID case tags to the cartons and use open-air RFID encoding during the serialization process on the packaging line. Having no bar-code printer at this point in the process maximizes efficiency. For pallets, however, the tags are both printed and encoded. Printing the pallet number on the tag provides a back-up bar code and human readable text when an RFID tag becomes unreadable or when exception handling requires a bar code or manual data entry. The mix of technologies improved the accuracy of inventory records and streamlined the movement of product through production and shipping.Finding RFID ProfitsAs Sentry and others have proven, manufacturers can profit from RFID, both inside their factories and throughout their supply chains. “By tagging cases, pallets and sometimes individual items, companies will have a more accurate accounting of their inventories,” says Mark DiSera, RFID product manager at vendor Turck Inc., in Plymouth , Minn. “This will eliminate out-of-stocks because suppliers will know exactly when quantities are running low.”Another form of inventory control that RFID can provide is the tracking of equipment and other assets, such as forklift trucks and containers. Tagging these assets gives them greater visibility, which is often the first step in getting greater utilization from them. This use of the technology is spreading quickly in the automotive industry, according to DiSera. The automakers, for example, are using RFID tags to track the locations of the expensive racks that carry frames or bodies as they travel through assembly.Despite the impact that RFID can have on controlling inventories and assets, reaping its full benefits is often not possible until enough operations in a factory or at business partners in a supply chain are using the technology. When a significant portion of the flow has no tag, workers have to go back to entering data manually, which only undercuts the economies gained from investing in the automation. “That’s why organizations like Wal-Mart and the Department of Defense are forcing their suppliers to implement RFID,” says DiSera. Another hurdle that industrial users had to jump was the past unreliability of the technology. “Many of the original RFID pilots fell short of expectations for various reasons,” says Calvin Fidler, director of solutions innovation at Peak Technologies Inc., a Columbia, Md.-based manufacturer of bar code scanners and RFID technology. His list of reasons includes the failure rates of the tags themselves, packaging issues, tag orientation and nonexistent returns on investment. The interference from electromagnetic fields, as well as metal and water commonly found in factories only complicated the problem.Indeed, configuring the readers and tag applicators was the most challenging aspect of installing RFID at Sentry Group. “We need almost 100 percent accuracy for the system to work correctly,” says Matrachisia. “There was interference from other equipment and a lot of variability in how the pallets went through the portals.” It took several weeks to configure the equipment to be accurate and to train workers to handle and store the tags correctly. Building a Better TagA better understanding of the physics behind RFID has been one of the payoffs from the mandates issued by Wal-Mart and other retailers. The resulting heightened interest in the technology has spurred suppliers of the technology to pour engineering talent into developing a wider spectrum of applications. Among the fruits has been a more stable base of firmware and the Gen 2 (second-generation electronic product code, or EPC, specification) standard.“When we started applying tags in production environments before Gen 2, the failure rate on the tags could be as high as 20 percent,” says Fidler, at Peak Technologies. “With Gen 2, we are down to less than 1 percent failure rates, a manageable number for reprocessing.” Now that the data are much more usable, users need only make the effort to look for ways to use them.The technical strides made by manufacturers of RFID technology also have improved the cost-to-performance ratio. “RFID tags are cheaper than ever—7 or 8 cents in volume, down from a dollar or more ten years ago,” says Kevin Ashton, vice president of marketing at ThingMagic LLC, a Cambridge, Mass.-based manufacturer of RFID readers. The cost of readers is down, too. Some are available for less than $1,000, and recent developments, such as the RFID reader on a chip developed by Intel and ThingMagic, promise to drive those prices even lower.Meanwhile, the performance side of the equation also continues to improve. Interference from other RFID readers, metal and water is less of a problem than it was. “In the right situations, you can read hundreds of tags per second, and at distances in excess of 30 feet,” says Ashton. He claims that a combination of the most advanced readers and tags can extend that range to as far as 60 feet when circumstances are ideal. To show the power in these improvements, he points to the experience of Avery Dennison Corp., a Fortune 500 company based in Pasadena , Calif. , that both uses and makes RFID inlays. Avery Dennison worked with ThingMagic to develop technology based on the Gen 2 standard, not only to design reliable products but also to produce them reliably. As a mass producer of a variety of tags, Avery needed a reader that could check several classes of tags at more than 100,000 units per hour.The result of the collaboration is that Avery now uses ThingMagic’s Mercury4e embedded readers to test each inlay coming off its production lines in continuous roll forms. “We can do so at least 10 times faster than the previous state of the art,” says David Puleston, head of engineering for Avery RFID. He reports a 99 percent accuracy rate. Based on the success, his next step is to move from roll-level inspection toward item-level tracking, which would track chips from their removal from wafers through delivery to customers.Better Bar CodesRFID is not the only technology capable of carrying information for managing inventories and controlling production. Over the last decade or so, vendors also have developed and perfected a two-dimensional bar code called Data Matrix. These little squares hold much more information in a smaller space than their more conventional one-dimensional counterparts that cashiers scan at the store. They can contain data such as lot numbers, production dates and features, in addition to the product code. These Data Matrixes also contain enough room for a measure of redundancy. “So they can provide better read rates because of the error correction built right into the code itself,” says Carl Gerst, senior director and business unit manager for ID products at Cognex Corp., a Natick, Mass.-based supplier of machine vision and imaging systems. He claims that this and a decade’s worth of applications engineering has made the image-based systems that read these codes more reliable than the lasers that read one-dimensional codes. Borg Warner is doing something similar for the mechanical and hydroelectric automotive components that it produces in Tulle , France . In addition to guaranteeing the quality of its fuel-pump bodies, control valves and other products, the company needs a way to trace them from cradle to grave. Human technicians also must be able to glean the information that they sometimes need during certain assembly operations and during repairs in the field.Not only must the product number, batch number, team identity and manufacturing date must be permanent, but they also must be readable by human beings as well as by automation. For this reason, the company inscribes them directly into the metal in two ways, as alphanumeric characters and as a 2-D Data Matrix bar code. As the parts come off the production line, a micropercussion device beats the information into one side of the metal part as alphanumerical characters. Then a Cognex vision system reads the characters and passes the information to an engraver, which cuts the Data Matrix into the other side of the part. A Cognex In-Sight 5110 reader verifies both the content and quality of the mark.The marked parts then undergo a series of hydraulic tests, after which a second reader records whether the piece has successfully undergone all the necessary tests. This second reading was not an easy task, according to Olivier Skalinski, project leader at Alema Automation, a Cognex partner systems integrator for southwestern France . The reason is that the pieces might arrive either dry and clean, or still containing a little oil from the testing process. So the system required some engineering to cope with the environmental differences.Another challenge for Alema was ensuring that the reader could communicate with the factory database containing the test results. It had to develop the necessary interface so that an automatic identification system would prevent bad parts from being packaged for shipping. A third bar-code reader at the entrance to the packaging area reads the identifying information, and the software checks whether the part is suitable for shipping. Only good parts are allowed to enter. The application of tracking technology could end there, or users could put the packaged parts on pallets containing RFID tags to track shipments. So it’s not just a bunch of hype; both technologies pay.
To see the accompanying sidebar to this story - "A Better Broadcast" - please visit www.automationworld.com/view-3494 For more information, search keywords “RFID” and “bar code” at www.automationworld.com.
To see the accompanying sidebar to this story - "A Better Broadcast" - please visit www.automationworld.com/view-3494 For more information, search keywords “RFID” and “bar code” at www.automationworld.com.
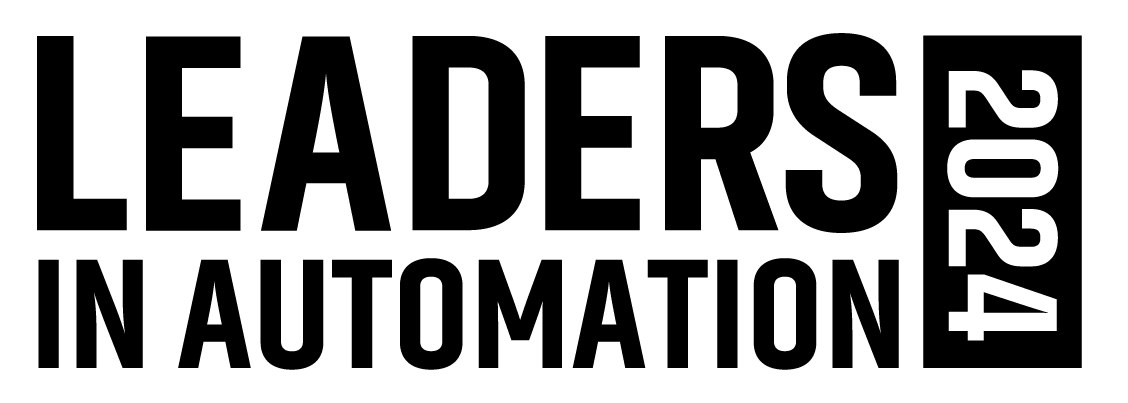
Leaders relevant to this article: