Businesses can’t let soaring energy costs kill their ability to serve customers, especially when they’re in the business of saving lives. Faced with excessively high electric bills, administrators at Lewis County General Hospital and Residential Care Facility in Lowville, N.Y., began looking for technology that would control the economic hemorrhaging caused by its antiquated heating, ventilating and air-conditioning (HVAC) system. During the summer, the HVAC system would run 24 hours a day and use discharge air dampers to direct cool air to where it was needed.
The hospital’s computerized energy-management system identified the fans delivering the cool air as a prime source of the bleeding. “We knew there were ways to improve the HVAC system’s energy efficiency, but we had to find a creative way to pay for it,” says Richard Schneider, the hospital’s maintenance supervisor. Lewis County General differs from most other county-run hospitals in that it must pay its way, living off the revenue from its services. So, it joined the ranks of enterprises investing in modern motors and variable-speed drives to generate enough savings to pay for them and the automation for running them.
At the heart of the hospital’s HVAC system was a closed-loop chiller, which included an on-site cooling tower and frequent air exchangers, as required by the Joint Commission on Accreditation for Health Care Organizations. The closed-loop system relied on three loops for pumping water through the air handlers and over coils to cool the air. Fans ran continuously to move the cool air from there to the various rooms, each of which has its own thermostat.
Because carbon dioxide sensors showed that running the system continuously for ventilation was unnecessary, the hospital administration asked Schneider to work with a Syracuse, N.Y.-based electrical distributor, CED Baldwin-Hall, to turn the supply and return fans down when they didn’t need to run at full capacity. To do the job, engineers at Baldwin-Hall recommended installing Allen-Bradley PowerFlex 400 AC drives on the fans. The manufacturer, Milwaukee-based Rockwell Automation Inc., had designed the drives to work with fans and other automated equipment typically found in buildings.
Lewis County General was able to recoup the $32,000 for buying and installing the drives on the four air handlers in the HVAC system within six months, which was much faster than it had anticipated. One reason for the rapid payback is that the savings forecast was too conservative. “We estimated it would reduce the HVAC system’s energy [usage] by about 8 percent,” says Schneider. “As it turned out, we reduced costs by 15 percent.”
Get your rebates
The payback was twice as fast as it would have been without Baldwin-Hall’s help with applying for the New York Energy Smart rebate through the New York State Energy Research and Development Authority. NYSERDA is one of a number of state agencies and public utilities offering incentives for investing in technology that reduces a facility’s energy consumption. In Lewis County General’s case, NYSERDA awarded the hospital a rebate for half the cost of the upgrade, basing the award on the project energy savings.
These incentives exist because the U.S. Department of Energy (DOE) has found that optimizing motors can reduce motor energy costs by as much as 18 percent. Installing variable-speed drives are one tactic for cutting these costs, as Lewis Country General learned. Replacing inefficient conventional motors with Premium Efficient motors is another tactic, according to Motor Decisions Matter (MDM), a national campaign organized by Boston-based Consortium for Energy Efficiency Inc. The campaign aims to educate industry about the energy savings that manufacturers can reap from motors and drives. The consortium undertook the campaign on behalf of a coalition of energy-efficiency organizations, motor manufacturers and service centers, electric utilities, trade associations and governmental agencies
The rising cost of electricity makes even small-percentage improvements in efficiency significant for facilities running tens or even hundreds of motors almost continuously. With motors that numbered between 70,000 and 90,000 at one campus alone, Eastman Kodak was able to save $200,000 by replacing inefficient motors there with more efficient models, according to NYSERDA.
Estimating payback
To encourage other companies to make similar investments, several private and public organizations offer resources for helping users estimate savings and payback. MDM, for example, has posted motor planning kits, case studies, and a variety of tools on its Web site. One tool there is an interactive chart for estimating the amount of energy that a facility can save annually by installing more efficient motors. Other places to look for resources and tips are the Environmental Protection Agency’s Energy Star program, and the DOE Office of Industrial Technologies’ Best Practices program.
The commercial sector offers tools too. Baldor Electric Co., in Fort Smith, Ark., for example, has developed a program for calculating the savings from switching to the motor manufacturer’s Super-E motors, adding variable-speed drives, or both. Called the Baldor Energy Savings Tool (BE$T), the program determines the cost of the electricity required for running a facility’s motors based on local electric rates, and the facility’s operating hours and loads.
Three factors—economics, technological advancements and governmental mandates—have influenced the development of energy-efficient motors and drives. Perhaps the biggest factor associated with economics is putting in today’s motors more of the iron and copper that motors used to have in the past. Because older motors contained more of these metals than some of the more recent models, they ran much cooler and, therefore, were more efficient.
“Manufacturers started using less iron and copper and let the motors slip a little bit more and run a lot hotter because energy efficiency wasn’t as big of a deal then as the cost of the motors,” says Chuck Hollis, manager of national systems integrator accounts for ABB Inc., of New Berlin, Wis. “Now that energy efficiency is a big deal, they are putting the some of the iron, especially higher-grade lamination steel, and copper back into their motors and are designing motors with much lower slip. Some motors have even been designed with such low slip and, as a result, with such high across-the-line starting current that they will only run with variable frequency drives.” So rather than being 80 percent to 85 percent efficient, the new Premium Efficient motors are 84 percent to 95 percent efficient.
Although restoring the metal content and changing from NEMA Design B to Design A to reduce slip probably contributed the most to recent gains in motor efficiency, Hollis also credits other factors, such as more use of better computer-aided design software capable of optimizing design. “Then there’s better manufacturing with computer numeric controlled (CNC) machines and automatic winding machines that make it possible to build motors more repeatably and with smaller air gaps and increased slot fills,” adds Hollis.
Right-sizing
Despite the contribution of technology, John Malinowski, a product manager at Baldor, argues that the biggest gains in efficiency actually come from “right-sizing” the motor for the application. “In a recent survey of motors, NYSERDA found that 55 percent of the motors installed were oversized,” he explains. “The ‘sweet spot’ for peak motor efficiency is 80 percent to 100 percent of full load.” At lower loads, both efficiency and the power factors fall.
Malinowski urges users not to think only about AC induction motors when considering efficiency. “Servo motors are also very efficient, perhaps a little better than induction motors,” he says. Plus, he notes that they allow more throughput in a given amount of time than do constant-speed motors.
Of course, motors, especially those units operating fans and pumps, usually conserve the most energy when controlled by variable-speed drives. “Savings in excess of 50 percent might be possible,” says Malinowski. For machinery, he recommends looking for even more gains by making sure that any fans, pumps, gears and other mechanical systems are the most efficient kind and size for the job.
Like motors, drives also have undergone a number of technical advancements, most tending to reduce heat losses and shrink their size. Over the last 15 years or so, designers have shrunk the size of AC drives to less than half their original size, widening their range of application. The trend shows little sign of abating. In fact, Schneider Electric, the Rueil-Malmaison, France-based automation supplier, reports that its new Telemecanique Altivar 61 drive is 15 percent smaller than its predecessor.
Many of the advancements that facilitated miniaturization also have been instru- mental in controlling heat generation. “Heat is one of the worst enemies of electronic performance and can cause failures,” says Ivan Spronk, AC drive product line manager in Schneider Electric’s Industrial Automation & Controls Group. To combat this problem, Schneider and many of its competitors have exploited a new generation of insulated-gate bipolar transistors (IGBTs) and new materials.
Thanks largely to trench technology, the new IGBTs have high switching speeds, low conduction voltage drops, and high-current capacities, which help to lower their cost and broaden their range of applications. Trench technology improves the on-site resistance of IGBTs, thereby reducing heat generation and improving thermal efficiencies. The result is lower heat losses and greater reliability. Less heat to dissipate also means that the devices need less material for the heat sinks that keep it cool, a fact that allows engineers to design them in smaller packages.
For models rated at 30 horsepower and greater, Schneider Electric’s engineers have replaced the mechanical pre-charge resistor and contactor for charging the DC bus with an input bridge controlled by a microprocessor that converts incoming AC power to DC. This combination is both smaller and a solid-state package. “By replacing mechanical components with electronic ones, once again designers were able to get a smaller, more reliable drive and eliminate heat-producing connections,” says Spronk.
Modern variable-frequency drives can do more than just reduce the electricity required for running the motors that they oversee. They also can generate huge energy savings in the process of using them, as managers at the on-campus power plant discovered at the University of Texas, in Austin. By retrofitting the fans on one of the boilers there with ABB’s ACS800 drives, the university expects to save between $500,000 and $1 million a year—by reducing its annual need for fuel and electricity by 320,000 million British thermal units (Btu) and 746,000 kilowatt-hours (kwh).
Despite their magnitude, the savings were not the catalyst for the retrofit. Rather, they were a welcome byproduct of an emissions control project initiated to comply with the stricter state regulations that will take effect next year. Since the project ended, the 150,000-pound Boiler Three emits only 21 tons of nitrogen oxides per year, a fraction of the 151.7 tons it spewed before. Plant management expects similar savings and reductions on Boiler Seven this spring, when it plans to complete the retrofit of this 500,000-pound unit.
Fan speed interpolation
The variable-frequency drives are an essential component of Compu-NOx, a system for controlling emissions of nitrogen oxide. The system controls combustion through a linear relationship between the speed of the fan and the airflow that it creates. “The system measures fuel flow and then interpolates the correct fan speed to give the desired flow,” explains Robert Benz, president of Benz Air Engineering Co., of Las Vegas, the supplier of the university’s new emissions-control system.
When dampers controlled the airflow before, the fans had to run at full speed all the time, which not only wasted energy, but also made control imprecise. “When dampers move up and down, even slightly, that generates a lot of airflow,” says Ryan Thompson, a project engineer for the university’s Utilities and Energy Management Department. “With the ABB drives, we have very precise control over the airflow, which makes all the difference in the world for fuel efficiencies and emissions.”
An unexpected consequence of the precise control over airflow is the ability to bank the auxiliary boilers—that is, to keep them in hot standby mode in case they are needed. “It allows us to keep one boiler at the ready without using any measurable amount of gas,” says Juan Ontiveros, director of the university’s Utility and Energy Management Dept. “It’s a big advantage, saving us 30,000 pounds of steam per hour.” The ability to maintain a stable and precise fan speed regardless of the load on the boiler means that Boiler Three can operate at less than 1 million Btu of input, a remarkable feat considering that its input rating is 183 million Btu.
Choosing an emissions-control system based on variable-speed drives accrued savings in other ways too, such as not having to invest $2 million in new burners for Boilers Three and Seven. “The power factor for the drive is near unity, regardless of operating speed or load,” adds Benz. “By putting on the drive, we are able to increase the capability of the transformer feeding it, so it saves the university from having to make power factor corrections.” And given reduction in energy consumption and the soaring costs of electricity and fuel, plant management expects the payback of the retrofit to be within 12 months. So a much more efficient system has stanched the bleeding in its energy budget.
For more information, search keywords “energy efficiency” at www.automationworld.com.
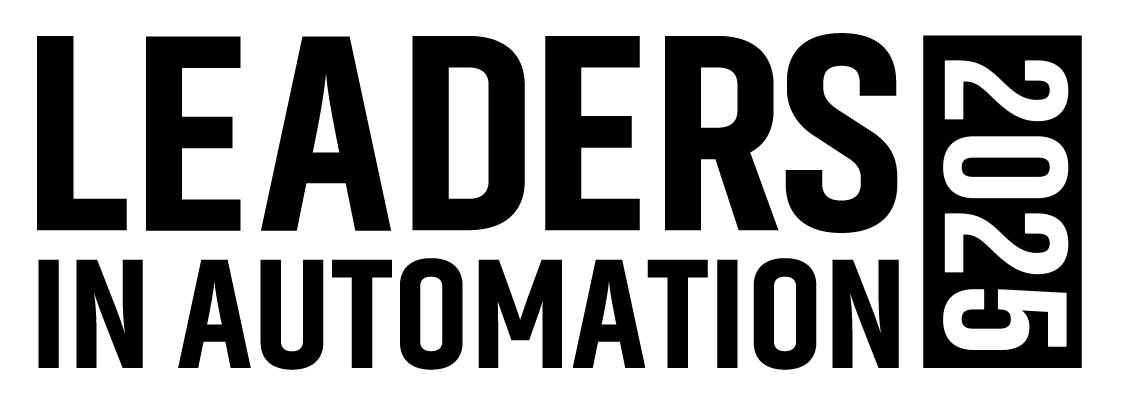
Leaders relevant to this article: