Energy expenditures typically account for anywhere from 5 percent to 15 percent of operating costs of U.S. manufacturers, making prudent energy management an important bottom-line consideration. In some cases, just a fraction of a percentage point shaved from energy costs can amount to millions of dollars in savings.
Yet, by some accounts, energy considerations sometimes get short shrift in the competition for capital at major U.S. industrial concerns. With only limited dollars to spend, top management at many manufacturers may look first toward spending those dollars on process improvements or growth, even when the payback for spending projects aimed at energy savings can be rapid. “We’ve heard reports lately of some large companies that aren’t doing energy projects, even when they can get less than a one-year payback,” laments one U.S. Department of Energy (DOE) staffer who asks not to be named.
At Rutgers University’s Center for Advanced Energy Systems, Director Michael Muller confirms that spending on projects with energy savings paybacks are not always at the top of the list for smaller manufacturers either. The Center serves as the field manager for the DOE’s Industrial Assessment Center (IAC) program, which provides free, on-site energy assessments for qualifying small to mid-sized manufacturers (See: What’s That Hissing Sound?).
“We tend to get more interest (in energy savings) during down-economic cycles,” Muller observes. “What happens in up-economic cycles is that small to medium-sized companies want to grow, so if they’ve got 50 or 100 grand to spend, they’d rather buy widget makers and not worry too much about cost cutting.”
Here’s help
As energy prices continue to rise, however, and as U.S. natural gas prices, in particular, remain at painfully high levels, the incentives for improved energy efficiency are stronger than ever. For manufacturers who are looking for opportunities to trim their energy costs, the DOE, through its Office of Industrial Technologies (OIT) “BestPractices” program, offers a breadth of assistance—ranging from informational resources and software tools, technical help, and emerging technologies access, to training in energy management practices and hands-on energy assessments.
One major BestPractices activity aimed at large manufacturers is the plant-wide energy assessments program. For a relatively low initial investment, companies that participate in assessments can expect to realize a minimum of $1 million in savings annually from energy costs, waste reduction and increased productivity—usually with a payback of 18 months, the DOE says. Further, on average, the findings from a single assessment can be replicated in at least seven other facilities with equivalent systems and energy uses.
To participate in the assessment program, companies must submit proposals in response to a plant-wide assessment solicitation, usually offered in the spring. Eight to 10 proposals are typically selected each year for awards, funded at up to $100,000 per plant, with a required industrial match of at least an equal amount by the recipient.
For each project awarded, a team of experts is assembled, which may include consultants, University faculty, retired executives and others, who perform a comprehensive energy assessment of the plant, and make recommendations based on current best practices and the adoption of best available and emerging technologies. The recommendations are detailed and specific, including cost and savings estimates for each of multiple projects and initiatives.
The DOE publishes case studies based on the results of these assessments on its Web site. And from the looks of those currently available on the site, the payoffs can indeed be substantial.
Following a plant-wide energy efficiency assessment, Alcoa Inc.’s Layfayette aluminum extrusions plant saved more than $1.5 million by reducing its use of natural gas and electricity, for example, and Alcoa has identified opportunities to save at least an additional $50 million. ExxonMobil, meanwhile, has reduced annual energy consumption by 11 percent by upgrading the control system of a recovery unit in its Baton Rouge, La., site. And at a Vulcan Chemicals plant in Geismar, La., a four-month optimization project involving two chloromethane production units required no capital investment, yet reduced process demand by 22,000 million British thermal units (MMBtu), for an annual savings of $42,000.
For a closer look at energy management activities around industry, Automation World talked to managers at some companies that have recently undergone BestPractices plant-wide energy efficiency assessments.
Ford Motor Co.
Ford’s Cleveland Casting Plant, which produces cast iron engine blocks and other components, underwent a BestPractices plant-wide assessment in 2002 that resulted in 16 specific recommendations for short-term projects. The DOE picked up $100,000 of the $300,000 cost of the assessment.
“Our Cleveland plant has always aggressively looked at energy, but with the assessment, we had an opportunity to bring in some fresh eyes to take a look,” notes Bill Ziemba, supervisor of energy leadership for Ford’s Power Train Operations, in Livonia, Mich. “And they did uncover some things that, honestly, we’d looked at in the past, but kind of lost sight of,” Ziemba allows. “So it was very beneficial.”
For an investment of about $2.3 million, the 16 projects recommended could produce annual savings at the Cleveland plant of about $3.3 million, the assessment team estimated. The recommendations addressed issues including combustion, compressed air, water, steam, motor drive and lighting system efficiency. If implemented, the projects could save 18 million kilowatt hours (kWh) and nearly 139,000 MMBtu per year, the team said, while reducing carbon dioxide emissions by about 63 million pounds per year.
Some of the biggest-payoff projects dealt with ways to more efficiently blend air into the Cleveland plant’s cupola furnaces. By reducing excess air in cupola blast preheaters, for example—a step requiring no capital expenditures—the operation could reduce natural gas usage by 64,000 MMBtu per year, producing an annual savings of $361,000. And for an expenditure of just $10,000, the plant could save an additional $465,000 yearly by using supersonic oxygen lancing to improve cupola temperature profiles.
In all, the Cleveland plant implemented 13 of the 16 recommendations, says Ziemba. “The three that didn’t get implemented fell outside of our parameters when we looked at the rate of return,” he explains. Current Ford guidelines for energy improvement projects require payback within one year.
At the corporate level, Ford measures energy improvement on the basis of energy expended per unit of production, Ziemba says. “We’ve established the year 2000 as our baseline and we’ve set some aggressive goals from 2000 forward.” The goal for 2003 was to be 8.5 percent better than 2000, he notes, and thanks in part to the DOE assessment-recommended projects, the Cleveland Casting Plant was able to exceed that goal, hitting 8.9 percent last year. The entire Power Train Operations unit, which includes Ford’s engine and transmission plants, did even better, recording an 11.7 percent gain in 2003 compared to the year 2000 baseline, says Ziemba.
“I’ve been involved in energy for a little over 10 years now,” Ziemba adds, “and Ford has always been very aggressive on energy and the environment. It’s just the way we operate.”
Rohm and Haas Co.
Rohm and Haas conducted its first BestPractices plant-wide assessment at its Knoxville, Tenn., facility in 2001, and then replicated the assessment methodology at plants in LaMirada, Calif., and Louisville, Ky.
As a specialty chemical producer with more than 100 manufacturing plants in 26 countries, the company saw the assessment as an additional step in its internal benchmarking activities aimed at energy best practices, notes Ray Baker, manager of energy and utility systems at the Rohm and Haas Engineering Technical Center, in Croydon, Pa. “Many of our plants use similar processes, so if we can make energy savings improvements at one site, we should be able to replicate that at other sites,” says Baker. “And in fact, that’s what we’ve found.”
The assessment team came up with nine recommendations covering the Knoxville plant’s steam generation and water cooling systems, among others, with total energy savings estimated at nearly 47,000 MMBtu in steam and fuel annually, and 11,000 megawatt hours (MWh) per year in electricity. Annual cost savings were estimated by the team at almost $1.5 million. When the assessment was replicated at LaMirada and Louisville, combined additional estimated cost savings totaled more than $500,000 per year. The $166,900 cost of the assessments was 50 percent DOE funded.
To date, about three quarters of the Knoxville assessment recommendations have been implemented, with additional actions taken at the LaMirada and Louisville plants, Baker says. Savings opportunities identified during the assessments have been put in place at other plants as well.
The DOE assessments and other energy savings activities at Rohm and Haas are part of an ongoing corporate program launched by the company in 1999 aimed at actively reducing energy usage and costs, Baker says. The company’s largest plant, based in Deer Park, Texas, in fact, has been aggressively focused on energy management since 1997—an attentiveness that has led to more than a 26 percent reduction in that plant’s energy intensity, Baker adds.
Among other activities, Rohm and Haas participates in the DOE’s Allied Partner program, which provides access to BestPractices information and software tools, including training modules. The Deer Park plant has hosted DOE training sessions for its own staff, and for those of nearby companies, Baker says.
As a way to more easily share energy savings best practices among all of it plants, Rohm and Haas is developing an internal Web site that is expected to go live by mid-year, says Baker. The site will include energy databases and will provide a place for plant personnel to post their energy savings ideas, including those garnered through the BestPractices plant-wide assessments. Energy savings are a “high level corporate objective” at Rohm and Haas, Baker asserts, and the company has found the DOE to be a valuable partner in that effort. “They’re an organization that is really out there to do whatever they can to encourage energy reduction and savings,” he concludes.
Submit a proposal
For companies that may be interested in submitting a proposal for a DOE plant-wide assessment during fiscal year 2005, beginning Oct. 2004, information can be found on the OIT BestPractices Web site, at www.oit.doe.
gov/bestpractices/solicitations.shtml. Solicitations for proposals are expected to be issued some time this spring with awards made during the summer. Individuals may also subscribe to the E-Bulletin—an electronic newsletter from the DOE’s Industrial Technologies Program that will contain information and links on solicitations when they are issued—by requesting a subscription via e-mail, at [email protected], or by calling the ITP office at 202-586-7547 or 202-586-9232.
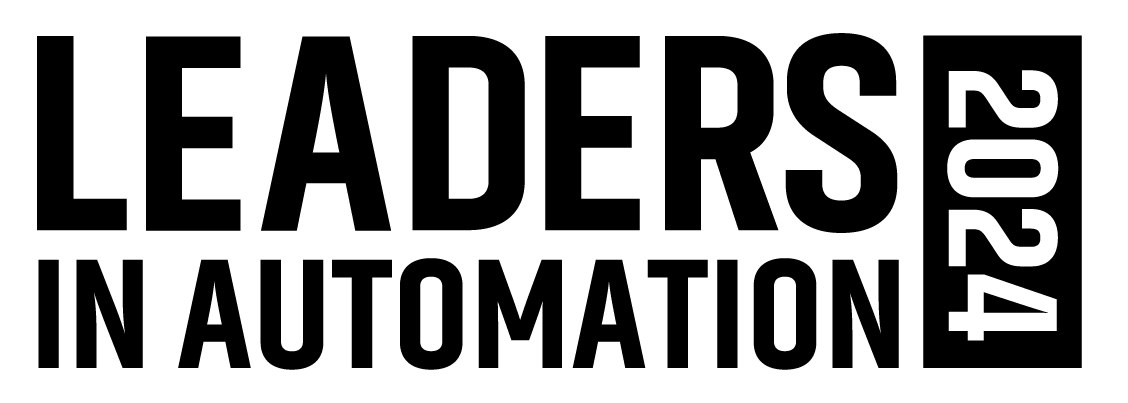
Leaders relevant to this article: