No longer the topic for science fiction or think tanks, managing a globally dispersed manufacturing enterprise is today’s reality. Nowhere does this reality affect automation more than in the design-to-manufacturing cycle of a company’s products. In order for a company to achieve a faster concept to salable product time along with fewer errors along the way, employees from many departments must work together, sharing a common set of information. Complicating the situation is the reality that these employees are often physically distributed across a variety of time zones and cultures.
Where there is a customer need, there is usually at least one supplier working to find a solution. Indeed, there are many solutions appearing that each solve a piece of the problem. Integrating the work of product design engineers, manufacturing process engineers, machine design engineers, information technology professionals, not to mention order entry, production and quality areas, is a complex issue. No one product is available that will do it all, and some ideas are still forming. This is certainly an area with exciting potential for improving manufacturing competitiveness.
Product lifecycle management (PLM) is the term that has been coined to describe the applications and functions designed for this area. Parts of PLM are quite mature, while other portions are incubating in the conceptual stage. One thing is sure; the area is rife with acronyms. This article will look at many of the technologies that help companies be more competitive today, and also some that offer help for the future.
Computer-aided design (CAD) and product definition management (PDM) are mature technologies that are widely adopted. These products help designers define the product. Computer aided manufacturing (CAM), usually linked with CAD, as in CAD/CAM, is also a mature technology that assists doing manufacturing process planning directly from mechanical design drawings. CAD/CAM helps define how to make the product and it plays out primarily in industries in which discrete products are machined.
The process of defining how to make products is expanding past CAM to manufacturing process management (MPM), championed by Portsmouth, N.H.-based software developer Tecnomatix. Also promising an automated process for defining how to make the part in a computer numeric control (CNC) environment is a standard called STEP-NC. This developing standard is championed by the Open Modular Architecture Control (OMAC) machine tool working group. Another software application to help automate the design process is design for assembly (DFA), for developing products that can be manufactured in a cost-effective manner.
Along the way, there is a technology that integrates within CAD to help manufacturing engineers design complete transfer lines by automating controls development. Finally, there’s an electronic form tool that helped one company integrate all of its departments, reducing the order to ship cycle.
Accessible information
Information is what is needed to manage a global manufacturing enterprise. The catch is that manufacturing information is filed by department and is often inaccessible to those who need it. Even if paper documents have been transferred to electronic format, different storage standards and application types still render the information useless to the vast majority of people who need it.
Dick Slansky, senior analyst at the Dedham, Mass., manufacturing analyst firm ARC Advisory Group, notes, “Huge volumes of product information must be transferred and exchanged among various facilities and their associated factory equipment, production processes and machine tools in order to do business on a local, regional and global scale.”
Manufacturers who wish to react flexibly, quickly and cost-effectively to changing market conditions, according to Slansky, must make production information available as quickly as possible across all areas of the enterprise. But just being available isn’t enough. That information must be in a form that can be processed, interpreted and executed at any level. This means that data conversions and re-processing of incomplete format translations must be avoided. He advises, “It has become essential to companies developing and manufacturing on regional and global scales to have universal and unified data formats and interfaces that span the enterprise, from the engineering design workstation to the machine tools on the factory floor.”
Slansky sees the development of ISO standard 14649, STEP-NC, as the necessary additional piece of the puzzle that fits between the CAM process and the CNC. “STEP-NC alleviates and stabilizes what has been the weak link in the CAM process: the CNC program, which represents the interface between the manufacturing planning process and the machine tool control system,” he adds.
Martin Hardwick, president of Step Tools Inc., in Troy, N.Y., explains, “The standard defines product, process and tool requirement data for machined parts. It is one of a suite of protocols being developed within the IEC (International Electrotechnical Commission) technical committee TC184/SC4 to define data for manufacturing planning, control and inspection.”
The IEC committee is expected to release a draft shortly. The new draft will include support for explicit tool path data and will use eXtensible Markup Language (XML) to enable distribution of data across the Internet. The new draft will be published as an EXPRESS model and as a set of modular XML Schemas, according to Hardwick.
The OMAC machine tool working group, a volunteer committee of users and suppliers in the industry, has released a Value Proposition document on the STEP-NC issue. It states, “STEP-NC constitutes the overall benefit of a common data exchange and interoperability environment that enables collaborative production processes between machine parts planning and programming and the machine tool.” It also makes possible a “database of machining features that can be retained and stored to facilitate as-built part configurations for future use.”
The document touts the benefits of interoperability as the single most quantifiable component of the adoption of STEP-NC. According to a recent study on interoperability costs by the National Institute of Standards and Technology (NIST), original equipment manufacturers and tier one manufacturers spend about $3.6 billion per year to solve problems associated with imperfect data exchange and interoperability. “STEP-NC will contribute significantly to reducing the cost of interoperability by providing a common open data format of machining features for the manufacturing community.”
Automating controls
One of the components of a PLM system championed by Tecnomatix is called manufacturing process management (MPM). Consulting firm Frost & Sullivan defines PLM as a computer-aided platform that supports a range of systems for the creation and management of information during the lifecycle of the product. MPM software is a component of PLM, providing information management capability specifically for the manufacturing process. It provides a link between upstream applications such as CAD and downstream enterprise resources planning (ERP).
MPM systems create hierarchical representations of final assembly manufacturing processes (eBOPs, or electronic Bills of Process). The eBOP captures process logic and flow, and defines the relationships between operations, manufacturing resources and product parts. MPM planning tools enable the design of optimal assembly sequences and facilitate the management of product variants and their changes.
According to a report from Frost & Sullivan, there are three major market drivers for MPM products: cost savings, faster time-to-market and greater integration of information.
Part of the product development cycle occurs after manufacturing engineers determine the process. Controls engineers then must determine the sequences of operations and program the automation equipment. This is a process often fraught with errors—typically due to incomplete information included in the part design and/or the process design.
A better system would be to embed basic control information in the electronic design objects at each stage of the process. A basic control program could be generated automatically from the design documents, perhaps even flowing into a program where the manufacturing line could be simulated and problems debugged even before the first steel is cut.
Such a system does, in fact, exist. Tim Reckinger, business manager for the design automation business at Rockwell Automation, in Milwaukee, says that the company’s Enterprise Controls product kicked off as a research and development project within Rockwell, Daimler Chrysler and Dassault. The idea was to be able to prove out the manufacturing system before building it. “The PLM folks have a good model for moving design to process information, but they are lacking about how to translate controls and accomplish simulation. Some can do robots, but not programmable controllers.”
Reckinger notes that this product has only recently been moved from R&D to product status.
Managing change
Sometimes the need for product lifecycle systems goes beyond the narrow definition of placing a discrete product into manufacturing. Engineering changes are an ongoing fact of life for production. Many departments within an enterprise require tracking changes. It is an essential component of quality standards and a requirement for warranty programs.
Rockwell Automation developed a strategy called DABASA, short for “design anywhere, build anywhere, support anywhere.” Under this strategy, products can be designed, manufactured, and supported where the cost is most advantageous and where intellectual and production capacity is available.
Making DABASA a reality is a huge information management challenge. “We are constantly shuffling product lines between two of our business units as well as partnering with third parties,” explains Bob Perk, IT manager for Product Lifecycle Systems, at Rockwell. “We need a system that can control all of this—an infrastructure that makes it possible to pick up a project from one place and put it into another, with everyone still having access to the correct information.”
Managers felt that it was best to have a single, open and modular system managing all product information as well as tracking critical activities such as new product releases and engineering changes in order to implement this corporate initiative.
The company initially developed a custom solution called Product Information Center based upon a product from UGS PLM Solutions, a Maryland Heights, Mo., company that is part of Plano, Texas-based EDS.
When UGS PLM’s Teamcenter product became available, Barry Umbs, Rockwell’s manager of engineering services, in Milwaukee, saw the benefit of a Web-based environment for global collaboration. But to justify the upgrade, the system had to pay for itself. Perk and Umbs, as well as Mike Faler, Rockwell manager of engineering services, in Cleveland, and Denny Connors, manager of quality process, in Mequon, Wis., realized that the Rockwell Components and Packaged Applications unit’s paper-based engineering change process offered the best chance to demonstrate a fast return-on-investment.
“Change management is not the usual place to begin a PLM implementation,” Perk says. “But we started there so we could prove to management that the system could pay for itself.” The paper-based process handled 2,000 engineering change notices (ECNs) annually, with the average ECN requiring 74 days to carry out.
Once Product Information Center was installed, its workflow functionality was tailored to the unit’s ECN process. Now, instead of having drafters running around with documents and tracking down signatures, ECNs are moved from reviewer to reviewer electronically, and automatically, via Product Information Center. Attached to each ECN are all the documents the reviewer needs to see. Perk estimates that having the ECN process managed by Product Information Center saves about $200 per ECN, for an annual savings of $400,000 in that unit.
But that is only a small aspect of the improvement. The average time to process an ECN has been cut in half—from 74 to 37 days. In addition, drafters are no longer required to physically seek out necessary signatures, so they have more time for drafting. “Not only did we reduce the backlog and cycle time of the ECNs,” says Perk, “we reduced the backlog in drafting as well.”
Automating aspects of the business process in other ways can have a substantial impact on product lifecycle management. Bruno Independent Living Aids, located Oconomowoc, Wis., is a company producing solutions for individuals who may face challenges with mobility. Products include stair lifts, power chairs, scooters, vehicle lifts and turning automotive seating.
Bob Herold, Bruno information systems director, relates that about a year ago, the sales manager called a meeting to point out that the order turnaround from initial call to production order for the company’s custom-built products was taking eight hours. If that turnaround time could be cut by half, then customer satisfaction would increase, and cash flow would be enhanced. During the kickoff planning meeting, says Herold, one person noted that if they were going to try to reduce the time to four hours, they might as well go for two. This turned out to be a prophetic statement.
Herold met the local representative for Cardiff Software, a Vista, Calif., electronic forms developer, at a conference shortly afterwards and discovered that its product called Liquid Office would fit the new process.
The existing process included 34 different product forms that were all manually completed and circulated. An internal territory manager would receive a call from a sales person or dealer placing an order. The manager would locate the appropriate form and complete all the required information. The form then went into one of two different outboxes for different routings. One routing might go through applications engineering for review, while other orders might be routed directly to production.
Because this was a manual system, forms could lie in an inbox or outbox for several hours before action or approval. What was needed was a way to automate this system and move the routing along more quickly.
The company purchased Liquid Office and put all 34 forms into its electronic format. Then the routings were put into an automatic system called a work queue. As soon as one person approved it, the action was recorded and the next person in line was notified via e-mail. Each department in line set a goal to look at all the open orders at specified intervals, usually every 15 minutes. If the order had no deviations from standard components, then it flushed through the system quickly. If extra engineering or work was to be done, even this was acted upon more quickly in the electronic system.
In the end, the order process time was cut to two hours. Not only that, but the electronic format contained features that reduced errors and forced order entry personnel to fill out forms more completely. Using radio buttons and drop-down boxes, the number of forms was reduced from 34 to six. Now, when the customer number is entered, 13 fields in the form are automatically populated.
The last remaining piece of the project is developing a way to move the completed form directly into the ERP system. Herold expects that to be accomplished in the near future.
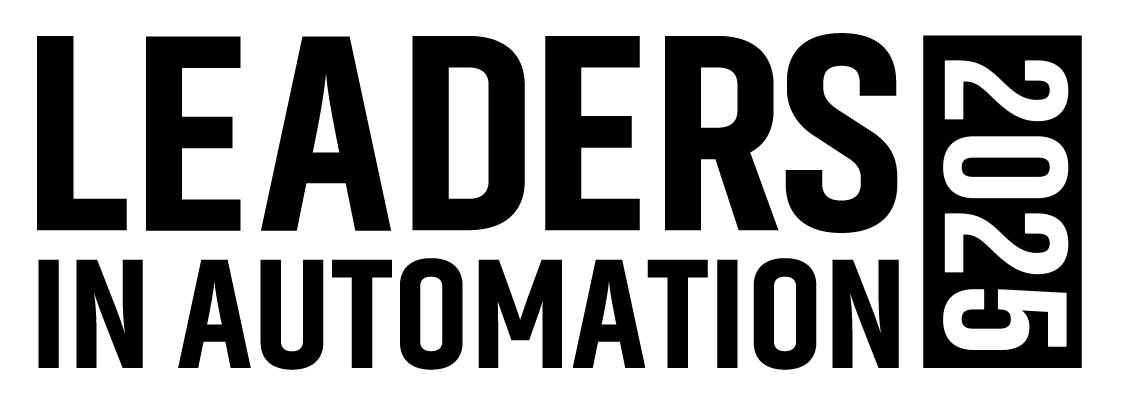
Leaders relevant to this article: