Operator Interfaces: Moving from Comfortable to Most Effective
When it comes to technology, we humans can be loath to change. We loved eight-track tapes because they let us hear the music we wanted to hear in our cars. Audiocassettes ushered in the mix tape and other useful enhancements, but required different devices and skills. Should I switch now? No, I’m comfortable. CDs came along with more benefits but more challenges, like newer devices and digital procedures. Now should I switch? Yes! No. Maybe not yet.
Then MP3 players and their many benefits arrived, but so did other reasons to hang on to our tapes or CDs. My car doesn’t have an auxiliary port.... I’ll have to buy an expensive new stereo… I’ll wait until I get a new car….
Best practices for operator interface design and alarm management can be like MP3 players for car and truck audio—you know there are benefits to the latest technology, but you’re familiar with what you have and the obstacles to switching just seem too high.
“When it comes to improving existing operator interfaces, the biggest obstacles include overcoming we-have-always-done-it-like-this thinking,” says Rob Kambach, technical product manager for HMI/SCADA at Invensys Operations Management (iom.invensys.com), Houston, Tex. Other issues: “finding funding for a re-design, and cost- justifying investments in high performance HMIs [human machine interfaces].”
From HMI software vendors and “human factors consultants” to users themselves, everyone seems to agree that a big reason operator interfaces aren’t better is because just about everyone is resistant to change. Not that we haven’t been studying the problems. The Abnormal Situation Management (ASM) Consortium (www.asmconsortium.net) is a group of end users and other experts focused on the continuous process industries. The group has developed best practices in each of seven areas based on site reviews conducted over the nearly 20 years.
Human factors
Other groups also are focusing on human factors and operator effectiveness in the process industries. The Center for Operational Performance (http://operatorperformance.org) is an alliance of petrochemical industry academic and process companies. In the pipeline industry, PHMSA 49 CFR Parts 192 and 195 require pipeline companies to comply with certain Control Room Management and Human Factors rules.
>> MORE EFFECTIVE: Click here to read how and why an oil and gas plant changed their operator interface designs.
The Engineering Equipment and Materials Users Association (EEMUA) is a European non-profit organization (www.eemua.co.uk). Based on data from the ASM Consortium, their EEMUA 191 Guidelines for Alarm Management were reportedly the first collective body of best-practice knowledge for the improvement of an alarm management system. Several institutions and societies also are producing standards related to the best practices use of alarms in industrial manufacturing systems. Among them are the ISA (ISA SP-18), API (API 1167) and NAMUR (Namur NA 102).
Alarm management has been established as a generally accepted good engineering practice. But sometimes rationalizing the alarms that have been added over time, or improving the confusing interfaces that have always been there, can seem an impossible task. Human nature being what it is, there may also be a measure of pride at having mastered a “difficult” system, which feeds a reluctance to give up that achievement.
“When an operator has been operating from a particular graphics format for ten years, he has likely learned to compensate for deficiencies in navigation, layout, etc. He is comfortable with the graphics, and selling him the idea of a different look, feel, and information presentation is difficult,” says Daniel Roessler, marketing manager for TiPS Inc. (www.tipsweb.com), Georgetown, Tex., which specializes in alarm management software and consulting.
But don’t think it’s only the operators or their management who are resistant to change. Sometimes the inertia comes from interface designers or control system vendors who are reluctant to change the views into their systems.
The typical approach to screen graphics, for example, is to pass the plant piping and instrumentation diagrams (P&IDs) to implementers to be reproduced into graphical displays, says Lisa Garrison, principle partner for Acuite (www.acuite.com), a global consultancy based in Ireland specializing in human factors engineering, control room management and design, and advanced graphics design. “This approach often led to numerous displays, deep navigation structures and a large number of graphics that are never or rarely used.” This can make it difficult for operators to find needed information when time is critical, such as when an alarm sounds.
Dave Strobhar, chief human factors engineer at Beville Engineering Inc. (www.bevile.com), Dayton, Ohio and part of the Center for Operational Performance, says there is still “a tremendous focus on the process hardware rather than the operator’s mind. Display designers cannot conceive of a single overview unless it’s on a large screen ‘because of all the equipment the operator has.’ The same focus results in what is termed ‘naive realism’—mistakenly believing that the brain is a projection screen upon which the display projects an image. This produces the need to add detail to graphics that does not improve performance and instead adds clutter to displays.”
Time to change
Some of the major DCS vendors are now paying attention to alarm management and the operator interface but, because their customers are cautious, they are cautious about getting too far away from what was done before. “There are more and more clients asking for improvements, but there still are many plants that prefer to leave things as they are,” says Garrison. “There is still the mentality that this is the way we have done it for the past 20 years and that works just fine.“
However, “the reality is that safety, operator efficiency and plant performance are not fine and certainly not where they could be,” says Garrison. “This will require a paradigm shift in the way we think about providing tools to the operations team.” These tools include the control room, consoles, user interfaces, alarm management and even the chairs, she says.
>> >> MORE EFFECTIVE: An ethanol plant upgrades its outdated HMI software. Click here for more information.
According to Andrew Ogden-Swift, engineering director for strategy and innovation with Honeywell Process Solutions (www.honeywellprocess.com), Houston “There is widespread recognition that operator effectiveness has a significant impact on both process safety and operating profitability. The ASM Consortium identified that approximately 40 percent of abnormal situations are due to human error, with an additional 40 percent due to equipment problems. The ASM Consortium [also] identified that abnormal situations lead to losses of between 3 to 8 percent of production.”
If operators don’t respond properly to abnormal situations, the problem could be related to interface design. Strobhar mentions a gas plant project he worked on in which “an operator missed a key alarm with severe economic consequences. The [proposed solution] was an alarm rationalization [program] combined with creation of higher-level graphics. The result was that the operators not only no longer requested adding monitors to the control room, but [they ultimately] operated from just two: the overview and the display from which they made changes. The union president reported [later] that they no longer had incidents in which an operator missing alarms or key information was a contributing factor.”
Best practice recommendations
Evidence like this on the benefits of improving operator interfaces is available for the organizations mentioned, and in the boxes throughout this article. So what are the most important best practices or latest technological advances being recommended?
The most frequently recommended improvement is to build situational awareness in the HMI. “Instead of just presenting data, this involves presenting information in the context of alarms and operational limits,” says Invensys’s Kambach. He cites the example of a large refinery where Invensys is involved in replacing 600 traditional HMI screens with screens built upon human factors design.
“Situational awareness is now built in,” says Kambach. “In a survey of 110 operators, 107 said they are already very satisfied with the experience. This high satisfaction rate increases our optimism that operating the plant in this new way will meet our objectives to increase productivity and reduce downtime.”
Roessler from TiPS Inc. provides an example of how graphics based on a P&ID could be changed to provide situational awareness. “A flow indication in the catalyst area might be on the catalyst graphic because that is where it is physically located, but the flow is really a part of the reaction area, because it is feeding the reactor and is essential to the feed ratios for reaction,” he explains. “Now as graphics are designed, the information is considered from the perspective of how it is used, more so than on which P&ID it resides or where it is physically located. This eliminates unnecessary navigation, and improves overall operational insight. While there is nothing inherently wrong with [the former] approach, it sometimes prevented data from being viewed in the overall context that improved its meaning,” Roessler adds.
Basic simplification of information presentation is another best practice. “In the past due to the sheer amount of information and unnecessary clutter on graphics, it has sometimes been difficult for abnormal situations to really stand out. This has been a factor in numerous incidents,” says Roessler. “Today, the entire design of graphics is intended to make these abnormal situations more easily recognizable by the operator.”
Eddie Habibi, author, founder and CEO of PAS (www.pas.com), a Houston-based Industrial Human Reliability software and services provider, says “Because the HMI is the operator’s window to the process, an effective operator interface is critical to real-time monitoring of the process. In fact, currently available High Performance HMI design best practices, when implemented, additionally help minimize operator fatigue and help improve the quality of decisions made by the operator.”
>> MORE EFFECTIVE: Read how an oil refinery achieved a 35% reduction in alarms. Click here.
Another best practice that Habibi recommends is optimization of basic process control (BPC) loop performance. “The robust performance of BPC loops ensures that unexpected process disturbances are rejected before they turn into process upsets. I like comparing basic control loops to foot soldiers defending a high value battle zone, and process disturbances to the enemy attacking the protected zone. In order to fend off the enemy, soldiers must be agile and prepared for battle. Most importantly, they must be awake in order to immediately respond to an attack. In this scenario, sluggish loops and loops in manual mode are only as good as undisciplined soldiers sleeping in the battle,” says Habib.
As mentioned, better alarm management, and an ongoing alarm management program, is another best practice. According to Roessler and Garrison, “For many facilities, the overuse of alarms is a significant issue. They have nuisance alarms, chattering alarms, related alarms, and other bad actor alarms that create unnecessary clutter on graphics, and require operators to continually acknowledge alarms. Alarm rationalization that reduces the number of unnecessary alarms and improves alarm priority distribution is critical. A strong alarm management solution that helps identify alarm issues is also key. The result is fewer alarms, which gives the operator’s a higher confidence level that when an alarm does activate, it is real and meaningful, requiring them to take action.”
Rich Chmielewski, PCS 7 marketing manager for Siemens Industry (www.siemens.com/industry), Springhouse, Penn. adds, “Even the best engineered systems require that the plant, once commissioned and running, have a manager that takes responsibility for working with the operators and equipment vendors to keep the alarms meaningful and relevant based on current production rates, plant conditions, and equipment updates.”
Chmielewski also says the following technological advances are some of the most important:
Picture in picture. This increases the area that the operator can monitor without the need for additional screens. They can control the layout/presentation of the HMI for the way they want to see and control it. These can include graphics, trends, alarming, etc. with any combination of them. Operators can also save these screen layouts for quick recall at any time on any operator station.
Priority based alarming. Using priority based alarming helps keep the focus on the most important alarms versus the ones that have just come in. The higher priority will always be placed ahead of the lower so that the operator can resolve the issues in the same manner. This usually helps to save the customer’s assets if an alarm flood condition arises.
Trending. With both integrated trending and “tag banding,” operators can be proactive versus reactive. A trend can show process direction and give advanced warning that a process is heading in the wrong direction. These trends can run embedded right into the process graphics.
For more information:
Acuite www.acuite.com
Beville Engineering Inc., www.beville.com
Honeywell Process Solutions, www.honeywellprocess.com
Invensys Operations Management, iom.invensys.com
PAS Inc. www.pas.com
TiPS Inc. www.tipsweb.com
Trident Automation, www.tridentautomation.com
Siemens Industry, www.siemens.com/industry
Companies in this Article
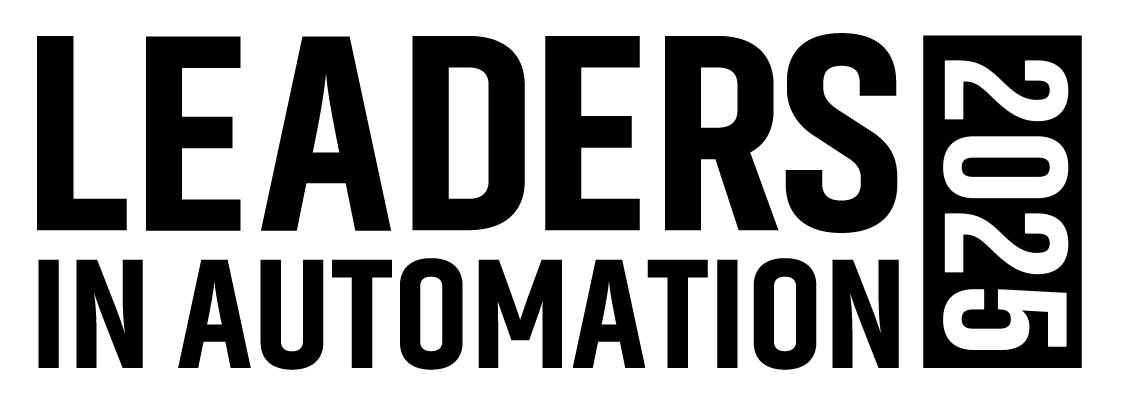
Leaders relevant to this article: