The future control room is here. Sounds like an automotive branding campaign for the latest, high-end sedan. However, with the process industries, there’s nothing to be convinced of—it’s here. Technology advances in the last eight to ten years, such as stronger computing power and mobility tools, have produced more efficient staffs in the physical control room, and provided more strategies on how to control their processes outside of it.
With recent capital projects and control network migrations, a more thoughtful control room design is starting to emerge as well, as older plants reduce their control room footprints. “Human factors” are part of the control room design objective as complexity grows within process plants. ARC Advisory Group, an analyst firm in Dedham, Mass., noted in 2010 that operators, on average, are responsible for 300 to 400 control loops.
Various automation vendors, academics, government organizations and end users have thrown their collective weight behind human factors and ergonomics research. Ergonomic factors include building layout, lighting, coloring, sound, graphics, operator console design and large screens. Organizations include the Center for Operator Performance (COP, www.operatorperformance.org), the Abnormal Situation Management Consortium (ASMC, www.asmconsortium.net) and International Standards Organization (ISO, www.iso.org), along with the American Institute of Chemical Engineers’ (AIChE, www.aiche.org) recommended practices for safe havens in the process industries. The ISO’s 11064 user-centered design document provides a guideline for best practices in developing “Ergonomic Design for Control Centers.”
While executive management might not see the need for more user-centered design in the control room, they should. “Research indicates that nearly 80 percent of production downtime is preventable, and half of this is due to undetected events or poor situation awareness by operators, according to Ian Nimmo, president of New River, Ariz.-based User Centered Design Services, Inc., and founder of the Abnormal Situation Management Consortium. The cost of this failure in the petrochemicals industry alone is estimated at $20 billion per year,” Nimmo adds.
“We are starting to see a large interest from process customers who are looking to really understand the presentation of information to their operators, says Cindy Scott, DeltaV product manager, Emerson Process Management, Austin, Texas. “Regarding new control room redesigns, I see a concerted effort by companies not to duplicate previous designs. There’s an increasing awareness and interest about the capabilities of a human being. What visually draws our attention, how many displays we should have and what we can remember, and what should go on a big screen.”
Ergonomic requirements depend on the country or size of company, according to Yasunori Kobayashi, general manager of Vigilant Plant Services for Tokyo-based automation supplier Yokogawa Electric Corp. Kobayshi says, “North American customers generally give importance to ergonomic design to improve visibility, but West European or Japanese customers give importance to knowledge-based design to support operators’ decisions.”
>> Click here to read sidebar, “Beyond the Control Room, the Workforce Adapts.”
U.K-based CCD Designs & Ergonomics Ltd provides consulting services on control room design best practices for multiple manufacturing segments, including utilities, aviation, industrial facilities and more. Recently, CCD Designs advised on a project for a pipeline operator in the North Sea that was introducing a SCADA system to control additional infrastructure.
The graphic interface of the new SCADA system was not the same as other SCADA systems adjacent to it on the workstation. For example, there were differences in the use of colors and icons for pump operations and in the terminology used for alarms, according to CCD Designs (www.ccd-designs.co.uk). Getting consistency between the systems required a detailed analysis to be undertaken. Had this work not been done, there would have been risks of human error in operation.
>> Control Room Design: Find out how to incorporate human factors and user-centered design into your next control in this white paper. Visit http://bit.ly/awwp044
With older plant infrastructure a reality, many capital projects are underway in the mining, oil and gas, pulp and paper, and water/wastewater industries. These large, modernization projects also include control room consolidation. “I can say that we’ve been approached by a number of companies in the past year looking to upgrade their control rooms, says Tom Williams, senior technical manager, Honeywell Process Solutions (www.honeywellprocess.com). “Companies are asking about best practices and proper locations for control rooms, including how to incorporate human factors into existing or new control rooms.”
For control room design, Honeywell offers its Operator Role Complexity Analysis software. The software does a comparison of the company’s operation against the database of other Honeywell customers and makes recommendations that are based on the Abnormal Situation Management Consortium’s (www.asmconsortium.net) user-centered best practices. Honeywell is a founding member of ASMC.
Control room consolidation is an issue most process plants execute during modernizing projects, such as a control system migration. Moscow’s JSC Gazprom Neft approached Yokogawa (www.yokogawa.com) to address this issue and provide recommendations on how to reduce 40 operating control rooms. Due to the high number of control rooms, the control operators were not able to share real-time information, coordinate operations or execute changes quickly. Yokogawa suggested a more consolidated approach and a savings of $4 million US per year.
The study suggested multiple consolidation scenarios, with one option including a main production management center where board control operators and a production planning staff would be located away from the process applications. Three satellite centers near the process would include field operators and maintenance. Yokogawa’s consolidation advisements pointed to a dramatic decrease in the number of physical control rooms, a reduction of approximately, 70 percent.
Modernized infrastructure
In St. Paul, Minn., the Metropolitan Council Environmental Services (MCES) is implementing plant upgrades to its seven existing water/wastewater plants. The modernization project for the main wastewater plant, called the Metropolitan Wastewater Treatment Plant, includes the replacement of older, non-maintainable PLCs with Schneider Electric’s (www.schneider-electric.com) Modicon Quantums controllers—36 cabinets in all. The Metropolitan plant is the largest plant in the system, where 200 million gallons per day of wastewater are treated in the treatment plant and eventually discharged into the Mississippi river.
“The PLC replacement allows us to standardize all seven plants with one control architecture setup, including operator interfaces, says Roger Knuteson, process computer manager, Metropolitan Council Environmental Services (MCES). “We really wanted to do this because our operators rotate through all seven plants within the seven county area. The staffing is different for each of these plants and, in fact, some of them are not staffed 24/7.
The Metropolitan plant moved away from one central control room in its latest redesign, mainly due to the size of the plant and functions. “We separated the Metropolitan plant into two business units. One control room is dedicated to liquids and other to solids in those parts of the plant. So you have a set of control operators solely focused on incineration—dewatering—and another liquids primary, secondary and disinfection treatment.” The metro plant handles incineration for the majority of the district. The seven wastewater plants receive wastewater via hundreds of miles of interceptor pipes. The new design at the plant includes meeting areas near the control rooms for discussions about work orders, planned maintenance for equipment, changing processes or the regular Monday morning coordination meeting, adds Knuteson.
Currently, the Metropolitan plant control rooms use Invensys Operations Management’s (iom.invensys.com) Lake Forest, Calif., Wonderware InTouch 10.0 operator workstations and an InSQL 9.0 server. Looking ahead, the plant would like to move to InTouch 10.5 and Historian 2012 R2 and, eventually, consider a move to a system platform, terminal server, thin client and tiered historians.
Control room expansion
At the Metropolitan plant, operators are able to control the processes from either the field or the control room, expanding the definition of the traditional control room in the wastewater industry. “We have the central control (computer) room and there are a limited number of workstations in there for people to look at. But, we also have workstations out in the process area itself so that people don’t need to run back to the computer room to do something,” says Knuteson.
Metropolitan control operators—control and field operators are one in the same—use PanelView 1500M fixed monitors from Rockwell Automation (www.rockwellautomation.com), Milwaukee, Wis. These single-purpose devices control multiple PLCs and are placed in strategic locations within the plant. According to Knuteson, MCES is looking at a wireless application strategy and would like to replace the fixed panel monitors with tablet PCs that deliver the same functionality but add the desired flexibility.
“We’ve started looking at how to implement a mobile strategy for the wastewater treatment plants and conducted a prototype in the summer of 2012 at one plant,” Knuteson adds. “The plant prototype tested network communication and redundancy; we need to have the ability to talk to that PLC and that piece of equipment if the network is down.” The tablet PC used in the pilot project was a Motion F5-Series rugged tablet PC, supplied by White Bear Lake, Minn.-based Lowry Computer Product (www.lowrycomputer.com). The plant’s cost justification plan is to run the fixed PanelViews to failure, and reduce the number of HMI licenses needed with the addition of docking stations in the control rooms.
Knuteson says the pilot program was a success, but control operators wanted more than process information via their tablet PCs; they wanted access to the enterprise information. “Operator feedback was great on the process functionality. However, the operators said it would be nice if [they could] find work orders and maintenance data on [their] tablets,” he explains. “So our challenge, now, is the integration of disparate data networks. We need to integrate lab, enterprise and maintenance databases and applications.”
Knuteson says that in the current control rooms, operator workstations can access business (enterprise) information, work orders from the business centers, purchase orders, time cards, “and whatever else that’s needed to run a business versus run a process.” So, “if an operator leaves the control room to go out into the field,” he says, “they, in essence, need take the control room with them.”
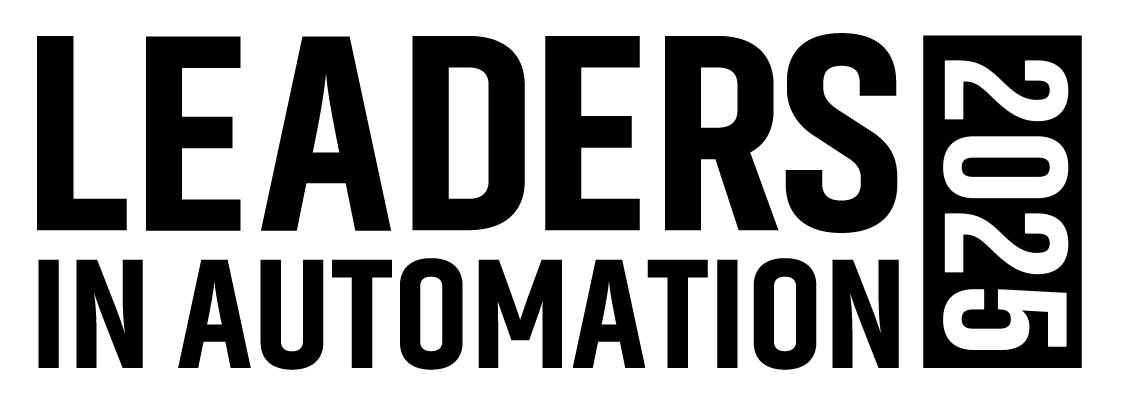
Leaders relevant to this article: