Safety in the packaging industry used to be a relatively cut and dried affair, a matter of guarding, some e-stops, warning signs and perhaps a class or two. Simply put it all in place, maintain it, and you’re covered. Today, however, safety has become a fast changing, dynamic aspect of packaging machine construction and operation, one that presents both OEMs and packaging machine users with new challenges, but also with new opportunities.
Why is the field of packaging machine safety changing rapidly? Simply put, because packaging itself is changing rapidly. Let’s start with the market. John D’Silva, safety marketing manager for Siemens Industry Sector (www.siemens.com/industry) summarizes the new facts of life: “Consumers are demanding an ever-increasing number of product choices and packaging styles. As a result, the packaging industry is requiring machines that support higher speeds, faster changeovers and reduced downtime from modular packaging systems.”
The safety systems that support and protect these machines and their operators function in a changed environment—one that challenges the old on/off, go/no go paradigm. Now, with today’s more automated packaging lines, shutting down a machine is likely to constitute a significant productivity loss rather than simply a minor inconvenience.
There are other negatives as well. “If you shut the machine down when there is product in it, before you get that machine running again you will have to clear [the product] from the machine,” points out Leo Petrokonis, packaging business development manager for Rockwell Automation (www.rockwellautomation.com). Additionally, bringing newer machines back online may in some cases be a more complex and time-consuming process than with older machines.
Clearly, there is a need to be able to perform safety related work within defined zones without bringing production to a complete halt. And there are ways to do it. “You can keep some of the machine running for instance,” says Petrokonis, “maybe slower or in a different mode of operation, so that you can keep downtime to a minimum while you keep the operator safe and get the machine back running faster.”
Significant standards
The technology exists for new, more dynamic approaches to safety like the one Petrokonis outlines, along with the standards that both facilitate and regulate its use. The two most important standards in this respect are ANSI/PMMI B155.1 2011 and EN ISO 13849-1. Other standards can come into play for specific aspects of machine or system operation, such as robotics, but these two standards are the key documents in redefining safety requirements for packaging machine builders and users.
ANSI/PMMI B155.1 2011 for Safety Requirements for Packaging Machinery and Packaging-Related Converting Machinery is comprehensive: It applies to new, modified or rebuilt industrial and commercial machinery which perform packaging functions for primary, secondary and tertiary packaging. It provides details on the risk assessment process, with due consideration for reasonably foreseeable hazards, accessing residual risk and achieving acceptable risk. It also differentiates between standalone robots used for packaging functions—which need to comply with RIA 15.06 – 2012—and the others that are incorporated into the machinery, which need to comply with B155.1.
Then there is EN ISO 13849-1. Approved just last year as a replacement for the venerable EN 954 safety standard, EN ISO 13849-1 governs safety functions in machine control systems. It is comprehensive, covering all safety-related components in all types of machines regardless of whether they are electrical, pneumatic, hydraulic or mechanical, as well as all stages of a machine’s life, from design through operation to decommissioning. It implements a consistent approach intended to eliminate the guesswork that sometimes bedeviled efforts to determine acceptable levels of risk with the old standard.
The standard, along with EN 62061 (Safety of machinery – Functional safety of electrical, electronic and programmable control systems), is a key component of the European Union’s Machinery Directive, compliance with which is mandatory for anyone wishing to sell machines in the EU. Importantly, it covers technology that wasn’t on the scene when the old standard was devised—the sort of technology that makes possible the type of productivity enhancing safety applications outlined above.
>> PMMI: PackSafe Improves Risk Assessment. Click here to read more.
Some will object to all this attention paid to standards, claiming that since the standards are not enforced there is no need to waste too much time on them. In fact, no machine standards are enforced in the U.S. except for those of the Occupational Safety and Health Administration (OSHA, www.osha.gov), whose standards (i.e., rules) have the force of law. Large multinational companies, however, are increasingly demanding compliance. Also, noncompliance effectively bars packaging machine makers from the European market. Finally, as John Kowal, director of business development for B&R Industrial Automation Corp. (www.br-automation.com/en-us) points out, the new standards are addressing and facilitating the use of new technologies that are capable of making packaging machines both safer and more productive.
Advances in zoning
Kowal provides an example: “What we are seeing is new safety technology, in particular networked safety, that uses the same Ethernet network as the machine control system,” says Kowal. “Replacing hardwired safety circuits and safety PLCs with networked safety allows packaging machines and lines to be zoned, provides additional diagnostic information, and replaces dedicated wiring.”
Zoning is the ability to safely control speeds, motion and torques in targeted sections of machines or lines for maintenance or changeover without stopping the entire line. Zoning also allows machines to cycle devices such as robot arms at controlled speeds and torques, so the system can be safely slowed rather than e-stopped and restarted.
The flexibility enabled by zoning is particularly relevant to robotics, which is playing an increasingly important role in packaging. Studies have shown that a large percentage of robot-related injuries occur not during production but during non-production activities such as maintenance and programming. To access the robot, workers must turn off some or all of the old, binary on/off safety devices, exposing themselves to risk. Newer standards and technology that permit approaches such as zoning enable workers to access robots and still be protected. The Robotics Industry Association (www.robotics.org) has recently revised its ANSI/RIA R15.06 2012 Industrial Robot Standard in accordance with the risk assessment methodology of EN ISO 13849-1 to accommodate this new reality and permit today’s advanced programmable safety devices to be utilized.
Armin Glaser, head of product management for German sensor maker Pilz GmbH & Co. (www.pilz.com), provides additional context and detail on these new approaches in his technical paper, From Static to Dynamic Safety: “For technical and economic reasons, the drive electronics—servo amplifier and frequency converter—have remained non-safety-related components within automation,” he writes. “So until today, additional safe components have taken care of safety, bringing the drive to a de-energized, safe condition in the event of a fault, or safely monitoring the movement of the connected motor. Now it is possible to integrate these additional safe components into the drive.... The result is a complete solution for the drive, control system and safety.”
Glaser provides the following details on what this newer, “dynamic” type of zoned safety application could look like. “When a safety gate is opened, the motor is braked safely with a defined ramp and then remains at standstill under active control. If the relevant authorization is present and a safe operating mode is activated for set-up mode, the motor will move in jog mode at a safely reduced speed. When this operating mode is ended and the safety gate is closed, the safety function is re-established for each machine operator. In other words: if static detection zone monitoring has been violated, production can continue at a reduced number of cycles and with safely monitored movements.”
Optoelectronics advances
Among the devices facilitating this dynamic, flexible approach to safety, Chris Brogli, business development manager for safety with Rockwell Automation cites the new breed of optoelectronics. “These are devices such as light curtains, laser scanners and safety cameras, and there have been advancements in these technologies that make them more reliable but also, when coupled with integrated controllers, provide more flexibility as well.”
Arguably the most exciting development in optoelectronics is the safety camera. They are like photoelectric cells on steroids in that instead of simply monitoring a point or a line in space, they can monitor a relatively large volume in either two or three dimensions. Because they are programmable, detection zones can be set at the controller or PC, and be easily modified when necessary. One type of modification is “muting,” which is similar to zoning and used to keep operators safe while maintaining optimum productivity.
Interestingly, since detection zone information is resident in the controller or PC, and since safety cameras can also easily monitor areas adjacent to the detection zones, it is feasible to expect that in the future the controllers will be able to anticipate probable zone intrusions and initiate an appropriate degree of protective action before a zone intrusion even occurs. Of course the idea isn’t to have the controller institute protective action every time someone merely walks by a protected zone, but there may be times and applications where this type of look-ahead capability is useful.
Mike Carslon, safety product marketing manager for Banner Engineering Corp. (www.bannerengineering.com), points out that optoelectric devices such as safety light curtains “have been decreasing in price while adding additional features” making these devices more affordable to incorporate. It seems reasonable to expect that safety cameras will follow the same path, not only transmitting and recording data, but also analyzing it as well, he says.
These and other devices are easier to incorporate into machines and systems thanks to the introduction of new safety technologies like safety controllers, says Carlson. “Advanced communications and the flexibility of the safety controller improve manufacturing efficiency by reducing machine down time,” he says. He adds that “the expandability of the safety controller allows a customer to standardize on single platform that is sized appropriately for all their machines.”
The upshot of all this? As Rockwell’s Brogli observes, “Safety can now help improve productivity. It is a key element in creating packaging machines and systems that are cheaper to operate, more flexible, and more safe.”
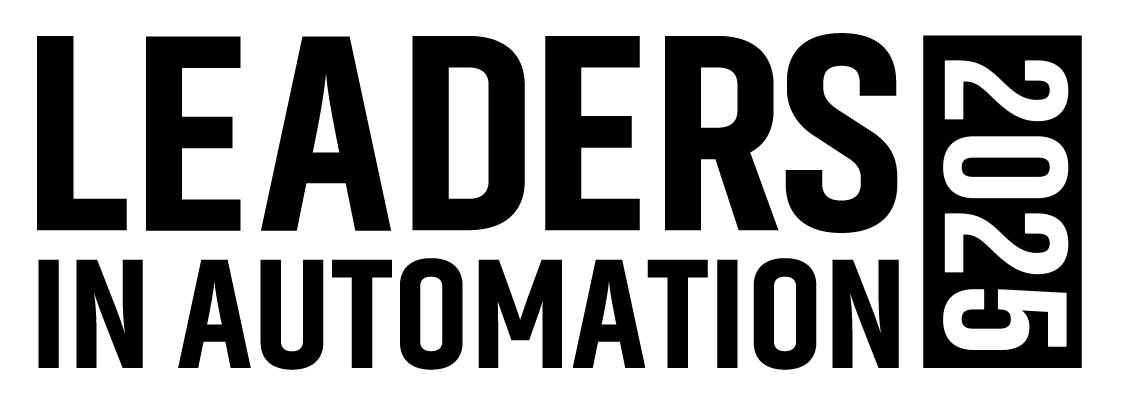
Leaders relevant to this article: