The Industrial Internet of Things (IIoT) is here and it’s improving the way manufacturers operate, produce products and provide services.
Companies have been capturing data from programmable logic controllers (PLCs) for decades, but now they’re allowing that Big Data to reach everyone who can use it to improve production. Machines, operators, supporting areas and managers can all communicate in near real time to improve production.
This is especially true in multi-model manufacturing, where multiple products are produced on a single line, requiring variations in parts and processes that don’t exist in single-model lines. That higher level of complexity can slow throughput.
One area where IIoT can have an immediate impact is in traceability. With its broadcast/subscribe model of data sharing, IIoT can facilitate a more hands-off approach to tracking varied part types through the production line, saving manufacturers and suppliers valuable time and money. Component-level traceability can give a precise birth history for each part, process and product, allowing managers to isolate faulty parts and machines, avoid adding value to faulty products, and limit the impact of product recalls.
A global tier 1 automotive supplier needed a solution to a three-part problem on their mixed-model assembly line, and they looked to an IIoT-based track-and-trace system to help. Here’s how the problem broke out:
- They were creating part lists for each car by scanning pieces of paper and sending a traveling spreadsheet through the assembly line. This created 40+ pieces of paper per product and slowed down the production process.
- PLCs weren’t connected to their corporate network, so scanned data between lines and other plants was easily lost. So if a supplier or customer called for part history, there wasn’t a way to remotely call the data. Plant employees had to walk to the PLC for that part line and search the part number for that product. This interrupted plant operations and made it hard to respond to those important queries. PLCs had been kept off the corporate network because of concerns about their data volume slowing down the network and forcing server upgrades.
- The data wasn’t consistently backed up. If a PC had a power outage and didn’t get restarted, was inadvertently turned off, or was hit by a lift truck, the missed data was gone for good.
They wanted a paperless solution that would allow PLC data to be accessed virtually anywhere by any authorized subscriber, without slowing down the corporate network. So they implemented a combination of IIoT devices, IIoT gateway software, a traceability application and cloud hosting.
Today, the in-cell PCs have been eliminated, and a simple IIoT device collects and backs up PLC data. It’s always on, and every IIoT device is controlled from a central location. IIoT gateway software manages the collection and broadcast functions. A track-and-trace app collects the scanned part data and logs it for that part. The IIoT gateway publishes the status of info to the HMI and an operator has instant access to an HMI with instructions, ending the need for paper ride-along tracking sheets. Those 40+ pieces of paper that used to travel with the product have been eliminated.
By choosing cloud hosting, PLC data is now being captured and broadcast without bogging down the corporate network. At each station, the part is assembled and a tracking app asks, “Has this part gone through all previous operations? Did it pass all previous operations? Is it configured for the right part?” Once all of those questions answer “yes,” the track-and-trace app keeps a local copy of the data and then pushes it to the cloud as a permanent record.
The PLCs are all connected and communicating so that they know where each part is in the production process. And if a PLC goes down, the data isn’t lost because it’s backed up in the cloud, with no burden on the company’s IT servers. There are no more isolated PLCs and no more PCs to maintain and manage for backup.
One of the great things about using an IIoT approach to traceability is that they’ll be able to continually add new ways to leverage their data. The same IIoT system that tracks parts through production can broadcast data to anyone who can use it to improve production:
- Shipping can use it to decide which size trucks to stage.
- Part kitting and sequencing can use it to evaluate timeliness of lineside parts.
- An app for overall equipment effectiveness (OEE) can monitor bottlenecks and starved stations, and adjust line speeds.
The possibilities are virtually endless.
So when it comes down to it, it’s all about the data—sharing and connecting it through IIoT allows manufacturers to reap the benefits of their data in ways they never could before.
Greg Giles, [email protected], is an executive director of manufacturing execution systems (MES) for RedViking, a member of the Control System Integrators Association. He leads a team of electrical and software engineers to design and implement MES, including error proofing, tracking and traceability, part kitting and sequencing, mobile factory apps, and custom app and report design. He graduated from the University of Michigan Dearborn with a B.S. in electrical engineering. Visit RedViking’s profile on the Industrial Automation Exchange.
Companies in this Article
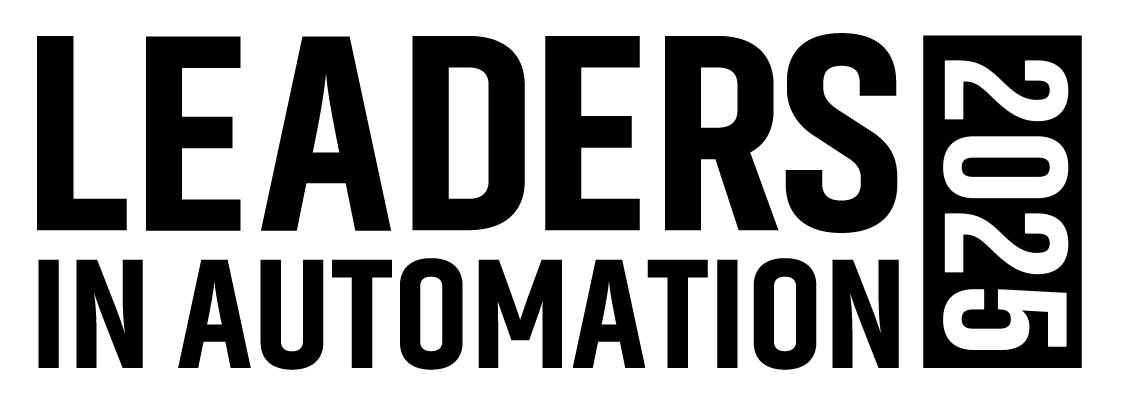
Leaders relevant to this article: