The shift to Ethernet has brought many benefits, but it’s also created new challenges for those who manage industrial networks. Industrial users expect to not only have the bandwidth and ease of use they see in home and commercial applications, but to have it all live up to Google levels of reliability.
These high expectations are prompting many networking teams to reexamine their infrastructures. One of the foremost demands in industry is that networks never shut down.
“Companies like Google, Amazon and Facebook have set very high standards for availability,” says Ben Orchard, application engineer at Opto 22 (www.opto22.com). “IT people are expected to provide that level of service. Even in industrial environments, if you say the network’s down, you just get a blank stare. The tolerance for downtime has disappeared.”
Network managers are responding with a number of strategies. They’re moving to faster versions of Ethernet, altering their networking architectures to provide fault tolerance, and expanding connectivity with wireless links. All this is happening in conjunction with steps to make industrial network environments more secure.
Speed Tops the List
Leveraging Ethernet improvements, driven by commercial applications, is one of the many rationales for employing the network in industrial applications. And what is perhaps the biggest advance in the commercial Ethernet world—ever increasing speeds—is what tends to attract a great deal of industry interest. Gbit Ethernet is beginning to already see increased use in automation environments, and 10 Gbit Ethernet is starting to see some acceptance.
However, there’s still plenty of debate about where anything beyond 100 Mbit Ethernet is needed and where it’s superfluous. Most observers feel that Gbit and higher architectures have a solid place as a backbone that connects the factory floor to the front office, largely because these backbones often also link many subnetworks together.
“We see a lot of Gbit Ethernet between switches and uplinks. It’s mixed with 100 Mbit full duplex on the plant floor,” says Gregory Wilcox, business development manager for networks at Rockwell Automation (www.rockwellautomation.com). “Over time, you’ll see more and more end devices that are Gbit enabled.”
When and where those end devices need high-performance connections is open for discussion. Industrial devices often send small amounts of data, and many of them don’t send these small data packets very often. Thus, there’s little need for high-bandwidth links in these environments.
“Generally, there’s not much advantage to be gained by going to Gbit speeds, except for backbones,” says Carl Henning, deputy director at PI North America (us.profinet.com). ”We do have members with PLCs that have Gbit fiber connection, but it may not be as necessary as some people think.”
Others say that the economic downturn prompted many plant managers to closely examine their requirements when they buy new equipment. In good times, plant managers tend to adopt faster networks in many areas so they will be prepared for higher requirements that may arise in the future. But when money’s tight, they design for real-world demands.
“The need to chase speed has plateaued in industrial environments,” Orchard says. “People are finally getting their heads around the concept that 100 Mbits is adequate for 98 percent of what they do. When money was available, everyone wanted the fastest network. When the economy tanked, they looked more at their actual bandwidth requirements.”
>> The Ethernet-Security Issue: Ethernet—be it wired or wireless—is vulnerable to attacks, viruses and other maladies. Click here for more information.
However, some suppliers remain bullish on faster versions, promoting both Gbit and 10 Gbit Ethernet. One of their rationales is that as applications are added down the road, 100 Mbit Ethernet may cause bottlenecks. They also note that, as more video is used, such as with video inspection and security cameras, bandwidth requirements will soar.
“Many applications require Gbit Ethernet (1000 Mbit/s), so we recommend most customers to at least step up to Gbit speeds on the backbone of their installations,” says Tim Pitterling, product manager for industrial Ethernet infrastructure at Siemens Industry (www.usa.siemens.com/industry). “But while many people still debate the move to Gbit Ethernet, the technology has already arrived on the plant floor. Siemens Scalance X500 switches offer it. For large automation networks that incorporate a lot of voice and video applications on top of their automation, 10 Gbit is the right choice.”
Rethinking Network Architectures
One of the key elements in a high-reliability communications system is the network architecture. Today’s networks are laid out using techniques that prevent downtime caused by a single point of failure. In such layouts, problems like broken cables or switch failures won’t cause communication outages.
”We’ve seen more people move to ring topologies to reduce downtime,” Henning says. “They’re also using redundant rings, controllers and devices. As costs come down, it’s more a question of ‘why not?’ Spending a small amount of money on this can bring big benefits.”
There are many factors that help ensure that these ring architectures are cost-effective and provide both high performance and high reliability. One is that switches are no longer limited to standalone boxes. They’re embedded into many different types of equipment.
“There’s been a move to device-level topologies with switches built into devices,” Wilcox says. “You can go from a switch-level star to switches on devices on a ring topology.”
Many devices now provide more than one port, making it easy for installers to ensure that connections won’t be interrupted even if a cable is disconnected or broken. These physical enhancements are being augmented by different protocols that help reduce downtime.
“More people are using the dual Ethernet connections we put on our controllers,” Orchard adds. “Redundant networks are becoming much more common. Technologies like rapid spanning tree protocol are also seeing widespread use. Fault tolerance has become much more cost-effective for small and mid-sized businesses.”
>> Wi-Fi as an Industrial Network: Learn more about Wi-Fi as an industrial networking option by viewing the Automation World Deep Dive Video at http://bit.ly/awwi-fi.
Adopting managed switches is another technique for reducing failures. They cost a bit more than unmanaged switches, but they bring several advantages.
“On one hand, there are obvious benefits like using redundant rings. But you also get diagnostics,” Pitterling says. “This allows customers to monitor the communication and loads on the network to detect bottlenecks early and increase availability.”
>> Deploying Fiber Optic Networks: Many network managers are gaining benefits by turning to fiber optics. Click here for more information.
Though many technical issues must be considered when high-reliability networks are being installed or upgraded, managers must also consider the human side when they’re installing equipment. Installers must be trained to understand nuances that can cause problems.
“Well-installed systems simply work better than poorly designed ones,” says Helge Hornis, manager of the Intelligent Systems Group at Pepperl+Fuchs (www.pepperl-fuchs.us). “The term ‘well-installed’ may include trivial issues like making sure M12 connections are properly torqued so no water gets in or power is separated from communication cables so electromagnetic capability is dealt with properly. Installers must also understand slightly more involved issues concerning panel ventilation, or a problem caused in January may not show up until June when it gets hot.”
The Rise of Wireless
Wireless links have become an integral part of the communications infrastructure for many industrial facilities, and there aren’t any signs that its usage will subside. Cabled connections offer far higher speeds, but there are many areas where cables aren’t beneficial or practical.
“There are a lot of really sensible applications of wireless,” Henning says. “Some people use it out of necessity and others use it because of the nice human machine interface capabilities. You can take a laptop out close to a line and do your analysis.”
In recent years, tablets and smartphones have become another driving force behind wireless. Many of the early wireless networks were installed for sensors and laptops. As the computing power and availability of smartphones increased, more employees started using them in industrial areas. A growing number of companies are letting employees link their small handheld devices to the industrial network.
“Using your own device is really becoming a big deal. People aren’t having to check their iPads or smartphones at the door anymore,” Orchard says.
Proprietary networks designed specifically for industrial applications were once common for wireless industrial networks. But managers who already leverage the pricing volumes and technical support of Ethernet are adopting the commercial technology promoted by every coffee shop and hotel—Wi-Fi. Based on the IEEE 802.11 standard family, Wi-Fi is provided in every mobile device, and reliability has soared as usage has spread.
“Another benefit of wireless LANs compared to many other wireless protocols is that wireless LANs offer the highest data rates, up to 450 Mbit/s using the 802.11n standard,” Pitterling says. “Siemens even offers proprietary protocols based on wireless LAN frequencies that allow the use for wireless LAN in real-time applications, for example wireless safety.”
Wi-Fi is taking over in many areas, but it’s not the only alternative for plant managers who want to install sensors, cameras and other equipment in their facilities. Other technologies let managers add nodes without the cost and trouble of running cables. Power over Ethernet (PoE) provides a simple way for users to add equipment in areas where adding a power cable might be difficult, but stringing an Ethernet cable is not a problem.
A few years ago, the PoE standard was upgraded to provide 25 W using conventional Ethernet connections. Many companies have devised techniques that boost that to 30 W, with others pushing power capabilities up to 60 W. These upgrades have made it viable for many industrial products.
“We’re seeing a lot more interest in PoE,” Orchard says. “The cost of switches has come down, and people see how clean it is to have communication and power on one cable. We see even more usage as IPV6 (Internet Protocol Version 6) makes plenty of IP addresses available.”
Another alternative, the AS-Interface, uses power connections to carry low-bandwidth signals. It can often be employed for sensors and other equipment that don’t send a lot of data, but still give technicians a lot of information that can be useful.
“Customers sometimes ask about ‘last minute’ mounting of sensors to collect data wirelessly,” Hornis says. “Our response is that when using AS-i, the power connection for the sensor is also the data communication connection, so no additional wires are needed."
Companies in this Article
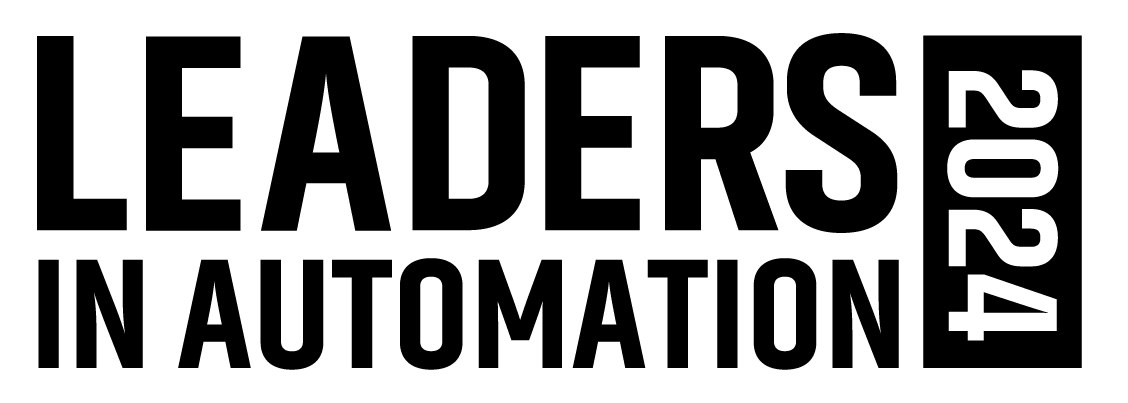
Leaders relevant to this article: