Industrial work is often dangerous work, as evidenced by the string of media headlines about chemical plant explosions and equipment rollovers in recent months. But the truth is that industrial workplaces have reported slight overall reductions in serious accidents in the past few years. That’s because industry has done a great deal to improve industrial safety methods, technology, training and system design to ensure human operators are safe during routine and aberrant activities. Human behavior, however, continues to be the wild card in any operation.
To augment our regular coverage of the new technologies and systems that keep workers safe, Automation World explored the human side of safety through our latest reader survey and compared results to a similar 2015 poll. Responses reflect how readers’ ideas and behaviors around safety have changed, and what experts say is impacting safety system engineering today—namely, collaborative applications that require humans and robots to work closely together, the recognition that some critical components of safety fluctuate in real time, and insights from the field of behavioral economics.
First, a look at that wild card in the manufacturing plant: humans. Newer employees raised on remote control cars and cellphones might look at an automated guided vehicle (AGV) and be complacent about safety. “That’s someone who believes they’re safe and takes safety for granted,” says George Schuster, industry safety specialist for Rockwell Automation. “They think, ‘It’s just a robot. I had one as a kid. What could possibly go wrong?’”
Other workers might anthropomorphize their machine, naming it like people name ships or cars because it has a perceived personality. “This can be both good and bad,” Schuster says. “It’s good when people can view machines as coworkers who are really able to help them. It’s bad because there have been documented cases where people in a factory have thrown themselves between a hazard and their coworker robot to protect the robot.”
Traditionally, when a machine and a person needed to be in the same place at the same time, safety engineers would manage that shared space with mechanisms like hard guarding or alarms to keep people and machines separate. Because of this, safety was seen as an obstacle to productive operations.
This is one reason why workers might be less than diligent about following the safety guidelines set forth. Asked if they’ve seen coworkers do something unsafe in an industrial environment, the majority of respondents to our latest safety psychology study (67 percent) answered, “Yes, but not very often.” Unsafe actions occur all the time, according to 14 percent of respondent, while slightly more (19 percent) said that their coworkers always follow safety guidelines. These results are similar to those from the 2015 survey.
In a white paper titled “Human Factors and Their Impact on Plant Safety,” ABB noted that some 70 percent of reported incidents in the oil and gas industry worldwide can be attributed to human error. “Industrial plants are designed with the highest degree of accuracy in mind, often with several separate safety loops checking the integrity of process systems,” says Luis M. Duran, global product manager for safety systems at ABB and co-author of the report. “However, this approach can’t check for human intervention, and a small human error could cause an enormous catastrophe.”
The industrial sector has been mainly focused on the physical component and automation process of the working environment rather than on the human as a part of both physical and psycho-social elements, Duran says. “The human was ignored, regardless of the fact that it is the human that makes most critical decisions when abnormal situations occur,” he adds.
Safety culture and standards
The concept of a safety culture has developed and grown over time. “Ten years ago, when the topic of machine safety was brought up with industrial users, [we] saw a big gap in terms of users understanding the requirements of machine safety and its implications,” says John D’Silva, safety technology manager for Siemens.
That gap was addressed by automation vendors and others with training materials and awareness programs about developing a safety culture, as well as with further development of safety standards. There have been a lot of lessons learned from industry accidents and incidents, and these have been captured in the writing of International Functional Safety Standards (IEC 61508 and IEC61511), and previously ISA 84.
These lessons learned impact product design, project implementation, operations and maintenance activities, and affect multiple areas of the plant lifecycle. “Nowadays, when interacting with industrial users, they are very knowledgeable and know the benefits of machine safety, not only from a compliance standpoint, but also how it protects operators and contributes towards an increase in productivity and operator morale,” D’Silva says.
A strong safety culture recognizes the impact of safety behaviors and actions on the integrity of the production asset. Asked whether they believe their companies have established a strong safety culture, the proportion of our survey respondents saying “yes” jumped from 63 percent in 2015 to 79 percent this year.
Factors that readers deem essential to developing a strong safety culture include training (93 percent), defining safety responsibilities (74 percent), leadership buy-in (73 percent) and enforcing accountability (71 percent). All four factors were seen as more important by 2019 respondents than they were by 2015 respondents.
“Nowadays, many times the discussions with industrial users move straight ahead to functional safety for their applications,” D’Silva says. That shows that safety standards, which provide methodologies like risk reduction and risk assessment, are clearly defined and accepted.
Duran agrees. “Today, functional safety standards have matured,” he says. “And with that maturity, their application and importance has also become the norm.”
Functional safety standards introduced the concept of the safety lifecycle, describing the phases that should take place from concept to design to implementation and operation of a safety instrumented system (SIS). “The safety lifecycle is a step in the direction of reducing the impact of human factors by establishing the proper design best practices, documentation reviews and validation, and verification steps in the execution of a safety project,” Duran explains.
Additionally, the standards introduce two important elements: competence of personnel and the functional safety management system (FSMS). “Recent changes to International Functional Safety Standard IEC 61508 have turned these requirements into normative clauses of mandatory compliance instead of a recommendation, as in the previous versions,” Duran says.
Safety technology advances
Just as standards evolved to address issues of human competence and behavior, technology has evolved as well. Going beyond long-established safety technology such as presence sensing, e-stops and safety relays, safety automation products continue to develop. These devices include safety drives, advanced sensors, safety programmable logic controllers (PLCs), safe motion/motor control, and networks that better integrate control, motion and safety. When surveyed, 72 percent of readers said their companies have bought or are planning to buy such new technologies.
Siemens has observed that the number of lockouts/tagouts have decreased, and the number of machine shutdowns due to process, safety and/or operator errors is minimal, according to D’Silva. “The defeat of safeguards is practically non-existent due to the continuous monitoring done by the safety controller and at the same time autonomously by the related safety I/O, which can be centrally located or distributed throughout the machine or plant, based on the application requirement,” he says.
“Technology continues to improve,” Duran adds. “What started in the late 1970s with safety logic solvers had spread to other areas of product design. New technologies allow users to design safety instrumented functions (SIFs) following functional safety standards such as IEC 61511/ISA84, he says, and make it available in digital format.
“More importantly,” Duran says, “the functions could be correlated with real-time information and used during operations and maintenance. This subtle change allows operators to see the impact of common actions (e.g., bypassing an instrument or switching a control application to manual) on the actual performance degradation, or impact on that SIF, or if a specific maintenance action could compromise the safety of the production asset or even to what extent.”
Machine safety was always about continuous monitoring, but now there is a lot of momentum toward the Industrial Internet of Things (IIoT), Big Data analytics and other integrated technologies. With many automation solutions, it is very easy to collect—not only the safety performance data and any reporting as required by plant management, but also to cross-check the safety integrity of the application and the hardware and software associated with it.
To ensure proper use of the safety systems, D’Silva says, one of the big automotive manufacturers has integrated cross-checking the safety signature at the beginning of every shift. Following manual data entry through the human-machine interface (HMI), the system cross-checks values with the safety signature stored in the safety controller to ensure no one has tampered with the safety on the machine.
Process industries are similarly combining IIoT devices with modern supervisory control and data acquisition (SCADA) systems to improve data-driven decision support. Yesco, a Korea-based natural gas supplier, implemented Aveva Monitoring and Control software, part of Aveva’s Industrial Software Platform, to be more proactive with maintenance and safety management programs and to drive operational excellence. After a five-month deployment and nine months of use, rich data analysis improved safety management at Yesco through better visibility.
In another example, the AMS Inspection Rounds application for Emerson’s AMS Trex Device Communicator makes it easier for operations teams to capture, report and respond to abnormal plant conditions that pose safety risks. Operators making inspection rounds can electronically record any abnormal or hazardous conditions in real time and deliver condition data to other plant systems via a wired or secure Wi-Fi connection.
“Route-based inspections are a key line of defense for identifying abnormal and unsafe conditions that may reduce efficiency or put personnel in danger,” says Mani Janardhanan, vice president of product management, Plantweb and reliability solutions for Emerson Automation Solutions. “AMS Inspection Rounds helps ensure that issues impacting safety and reliability are detected, reported and resolved earlier.”
Corvex Safety has introduced its own smart personal protection equipment (PPE), which is a combination of geolocation technology, the capture and transmission of unstructured data like photos, and social media engagement/gamification ideas all provided on a locked-down rugged device. The system enables two-way communication among machine technicians and supervisors and collects real-time data at the worker level. The goal is to empower the frontline worker to “make observations in real time, mitigate those observations, learn what happened and how they solved those things,” says Corvex CEO Ted Smith.
Using data to influence behavior
Analysis of more and different types of data provides opportunities to improve processes, performance and safety—both automatically and by influencing or guiding human behavior. Recording of real-time behavior allows the data to be mined for insight and use of behavioral science techniques can allow the data to be baked into useful analytic algorithms.
For example, real-time data gathering can empower front-line employees to provide feedback and “engage,” to use a term made popular by social media. It also allows safety-related activities to be viewed as performance-enhancing rather than as an obstacle or hindrance. Using behavioral science learnings from video games to appeal to the human desire to “win” can encourage safe and effective human actions.
Corvex Safety is leveraging the skills of BEworks, a behavioral economics consulting firm, to develop its smart PPE devices. Behavioral economics studies the effects of psychological, cognitive, emotional, cultural and social factors on the economic decisions of individuals and institutions. It’s a type of behavioral science that’s used to understand how people consciously or unconsciously evaluate risks and rewards of all types when deciding to take an action.
“Understanding the psychological and behavioral forces behind people’s decisions provides a rich opportunity to make changes to the work environment (e.g., how we present safety information) to help people make safer decisions,” notes a BEworks whitepaper. The science is being applied to understand things like why people ignore actions that will protect them, or what incentive for good behavior is enough to overcome bad behavior.
Schneider Electric’s Peter Martin has talked extensively about how real-time data analytics can enable “profitable safety” in this way. “It is now understood that the safety of the operation can have a direct positive impact on the operational profitability of the plant,” he says. “EH&S [environmental health and safety] can now be viewed not just as a cost center, but as a profit center.”
Schneider Electric’s approach to modeling the measurements of variables from process sensor data in real time enables this change, Martin says. “Once the variables are measured in the necessary timeframe, the resulting information can be provided to the operator, who impacts the business variable through a scorecard or dashboard,” he explains. “Empowering profit-impacting operational personnel in this manner enables them to make better decisions that drive profitability. Experience has shown that, over time, even front-line operators with moderate education levels learn to drive significant profitability improvement.”
Similarly, Rockwell’s Schuster describes how real-time data can provide insight into how machinery is being used, or misused, on the factory floor. “It could be as simple as a machine access point designed to be used two times per shift,” he says. “If that access point is being used 10 times per shift, that is an out-of-compliance frequency that is a red flag.”
That real-time data could be indicating the need for one of two things. “Either the operator is not trained and he or she is using an access point inappropriately, or maybe he found a better and faster way to do his job and we need to incorporate that into the standard operating procedures,” Schuster says. “So we have to take the data as both an opportunity to improve compliance and an opportunity to create a continuous improvement program to make these machines better and faster.”
Need for system thinking
Regarding safety data specifically, Schuster points to beneficial technologies such as laser scanners, lidar and safety mats. “But we haven’t really done a good job yet with a system that can combine and aggregate those technologies and weight them to create a more comprehensive view,” he says.
New sensors are coming that deliver ever more specific data, but even existing sensors can be used in new ways, according to Schuster. “The system that can aggregate data from multiple overlapping sensors is a very important consideration,” he says. “It’s a system way of thinking.” Sensor systems and data aggregation systems can “change the kinds of tools we have, so we can do some very precise coordination between people and machinery to ensure high efficiency and safety.”
Schuster has been working on more advanced sensor networks that can detect, track and predict the motion of people and machines together in a shared space—that can rank and evaluate potential future interactions. “One of the things that is really important about that, from a recording or a compliance perspective, is that it would almost be like a snapshot or frames in a motion picture—an image of the people and the machinery moving together in a shared workspace,” he says.
That way, if there were an accident or injury or even a near miss, this kind of a system could record and evaluate the complex motions between the two.
Companies in this Article
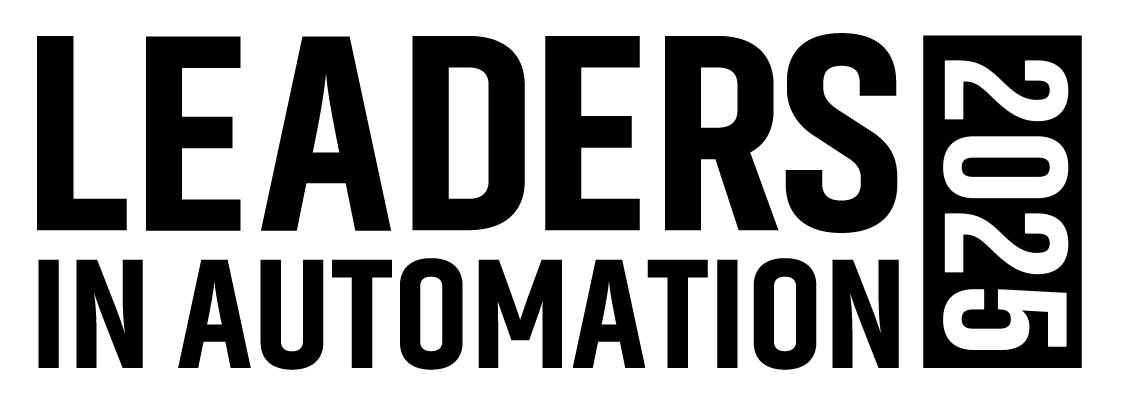
Leaders relevant to this article: